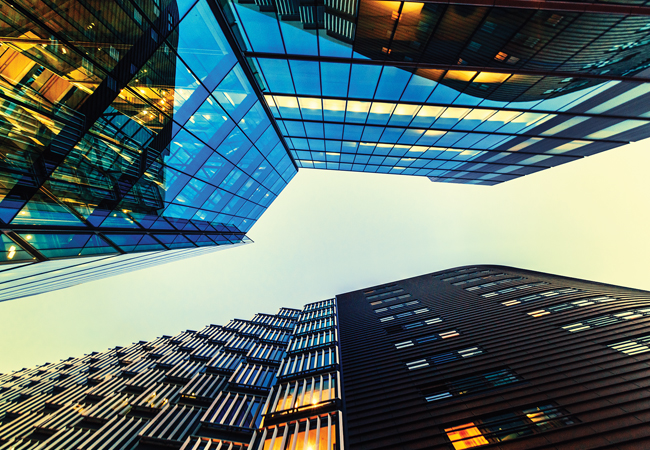
In May this year, the Committee on Climate Change (CCC) recommended that the UK government immediately set legally binding targets to cut greenhouse gas emissions to zero by 2050.
It made it clear that this will not be easy to achieve, and stabilising global warming will require action from every sector. Construction is no exception, and is especially important because 50% of the world’s raw-material consumption is through the development and use of buildings.
As well as galvanising government support, it is up to us – as an industry – to develop new methods of working that allow us to achieve this goal. This may seem daunting, but better environmental practices can also be beneficial for the bottom line.
Ramboll recently conducted analysis of the operational energy performance of more than 100 commercial properties within our clients’ UK portfolios. We found that heating, cooling and electrical systems in buildings across the UK are regularly designed with more capacity than they will ever need – bad for the planet and the bottom line. So why is this happening and what can we do to solve it?
Playing it safe
We found that, in its efforts to achieve technical compliance, the industry is over-designing and, consequently, installing too much capacity in building systems. Our analysis showed that, in the UK, designing to codes and guidance – as well as pressurised consultants commoditising and reusing ‘safe’ designs, often with only minor adaptations from previous projects – is leading to massive inefficiency. The reality is that there are smarter ways to achieve and exceed compliance standards without increasing capital expenditure.
We studied the operational energy performance of 100 commercial properties within our clients’ UK portfolios, using real data. Often, we discovered, 50% of the electrical supply capacity will never be used, and 30% of the cooling and heating plant capacity will never run. Of course, the space required for this unnecessary plant will exist for the lifetime of the building and will never be monetised.
We need to break free from out-of-date delivery models and conventional thinking
Normally, designers will turn to codes, occupancy levels and the extremes in environmental conditions to inform design – but this is causing significant waste and inefficiency in plant operation.
Our findings show there is a huge gap between predicted performance and reality. The key is to understand how a building will perform by simulating its operation early in the design development, so more informed decisions are made to deliver more efficient buildings. We have also taken lessons from our work in extreme environments and applied it back into the UK, to deliver leaner systems.
While building owners and developers might make some savings on initial design fees, and take comfort in having a building ‘designed to the codes’, the outcome for them, the tenants, the building users and the environment, can be greatly improved. We need to break free from out-of-date delivery models and conventional thinking.
Data and hybrid energy solutions
Within our commercial portfolio, we estimate achievable savings to be in the region of £60/m2 in capital expenditure (capex), and up to 50% in energy savings and carbon emissions. Scale this up to the 1.1 million m2 of offices currently under construction in London, and you see the scale of opportunity in the capital city alone – approximately £70m in construction savings and 23,000 tonnes of CO2 per year. So, sustainable solutions do pay.
The first priority is to establish accurate building demands. We have looked at occupancy profiles over a 12-hour working day, five days a week, and modelled the operation for 365 days, to derive highly accurate daily, weekly and monthly heating and cooling profiles. This enables the systems to be designed to maximise operational efficiency at any time of the year.
We can then take a hybrid energy approach, where heating and cooling systems are optimised for operational building requirements, rather than adapting systems traditionally based on design for peak winter and summer extremes.
The plant comprises a combination of boilers, heat pumps and chillers, selected to operate specifically to maximise efficiency from realistic internal occupancy demands. Essentially, we can design in reduced-size boilers and chillers, and use them only for the extreme short peaks in temperatures when they are highly efficient, but then rely on the heat pumps for the majority of the year, when temperatures are more stable.
A key feature is to use reverse-cycle heat pumps to take full benefit from simultaneous heating and cooling loads available for much of the year.
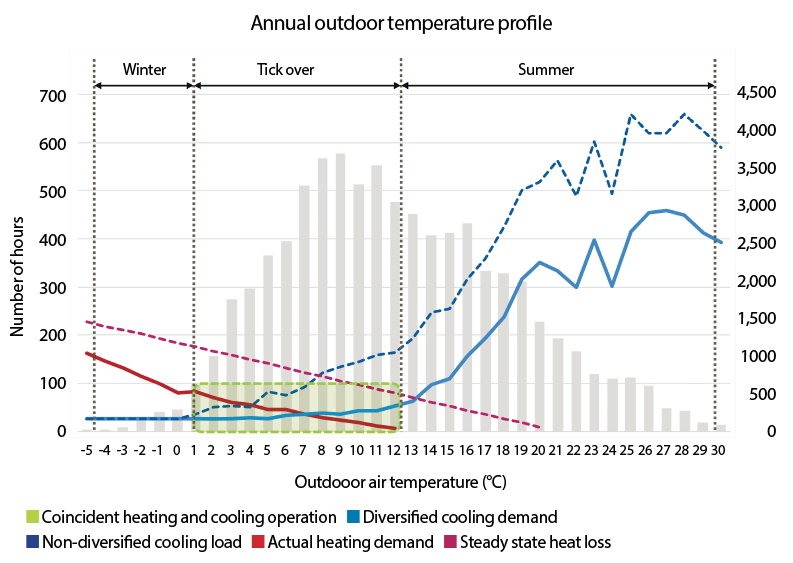
Annual heating and cooling profile of loads for a large London office development
Learning from extreme environments
We have taken lessons from the practice of engineering in extreme environments, where – by virtue of location – the energy solutions demand extremely lean designs. These approaches can be brought back to the UK, and help show how we can adopt ‘extreme for lean’ engineering principles driven by sound data analytics.
With the British Antarctic Survey (BAS), the extreme environment makes designing differently a key necessity. Working together for the first phase of the Rothera Research Station Modernisation Project, Ramboll and BAS have developed a design that targets a reduction in energy consumption by up to 35%. A whole host of measures were taken, including: rationalising smaller buildings; recovering waste heat; using thermal storage; improved insulation and demand controls; snow deflectors; and photovoltaic generation.
Devising the right solution for a site-wide masterplan that included some existing buildings, as well as new ones, required the assessment of the heating and electrical loads of all these buildings – with numerous variables – simultaneously.
With five million possible energy scenarios, finding the optimum solution would be like finding a needle in a haystack when using conventional iterative approaches. So, instead, we incorporated a method into a parametric modelling tool called the Evolutionary Energy Solver. This mimics nature to identify and rank the combination of inputs that will give the best performing, or ‘fittest’, solutions. This reduced the time needed to identify these solutions by 88%, enabling Ramboll and BAS to interrogate quickly the options most suited to the needs of their organisation.
Coupled with more efficient buildings and energy re-use, the end result offers a solution that will reduce energy consumption significantly in the first phase of the modernisation project.
Overdesigning building structures
The challenge of overdesign holds true for the structure, too. Ramboll is involved in an initiative, led by the University of Cambridge, that seeks to improve material efficiency across the construction industry. Research carried out as part of this work has demonstrated that we are using design loading in offices that may be more than double the loading the building will ever experience in its lifetime.
If you look at the current office space being constructed in London, we estimate that – by challenging just the design loading alone – 10,000-15,000 tonnes of embodied CO2 could be saved.

Lean design is essential on British Antartic Survey buildings
In addition, around £15m-£20m could be saved on construction costs through reduced slab thicknesses, column sizes and foundations. Add to this the time and workforce benefits, and we can see the huge potential of improved building structures.
This is where data and digital tools can help transform the industry. Ramboll is inventing its own digital tools, which we are piloting with a number of developers.
One such tool is SiteSolve, which enables our clients to vary the development brief rapidly and review the impact of their assumptions. With the power to look at hundreds of options in the time it would take to look at just one traditionally, the tool uses engineering insight to bring data to the forefront of the design process. This allows us to evaluate and refine solutions while balancing many complex technical criteria.
By embracing data-driven design, the construction industry can reduce capital expenditure, save carbon, reduce energy consumption, and deliver more healthy and sustainable buildings.
The sector is facing pressure from climate change, resource efficiency, digitalisation, economic difficulty and industry productivity – but we have the tools, the know-how and, more importantly, the data to meet this challenge.
We can turn design on its head and enjoy the fruits of more economical, sustainable, safe, comfortable and compliant buildings. So why wait to change?
■ Andrew Henderson is executive director, UK buildings, at Ramboll