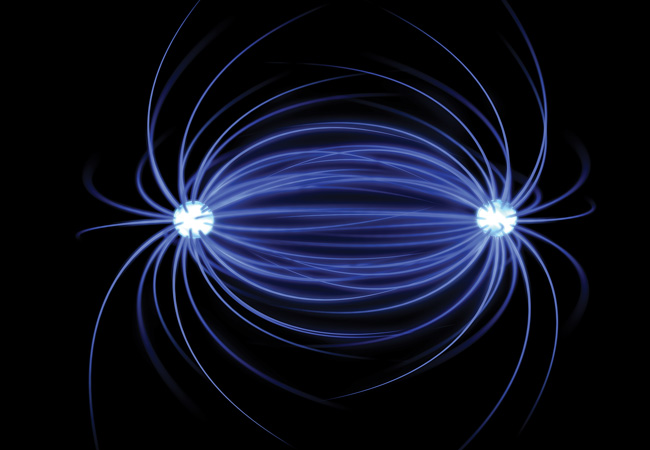
Credit: iStock.com – Enot-poloskun
Refrigeration, air conditioning and heat pumps account for 19% of UK electricity demand and around 10% of total greenhouse gas (GHG) emissions.
In 2015, the EU agreed to intensify reductions in carbon emissions between 2020 and 2030. This will include a further 40% reduction in GHGs, through much greater use of renewable technologies and a massive increase in energy efficiency.
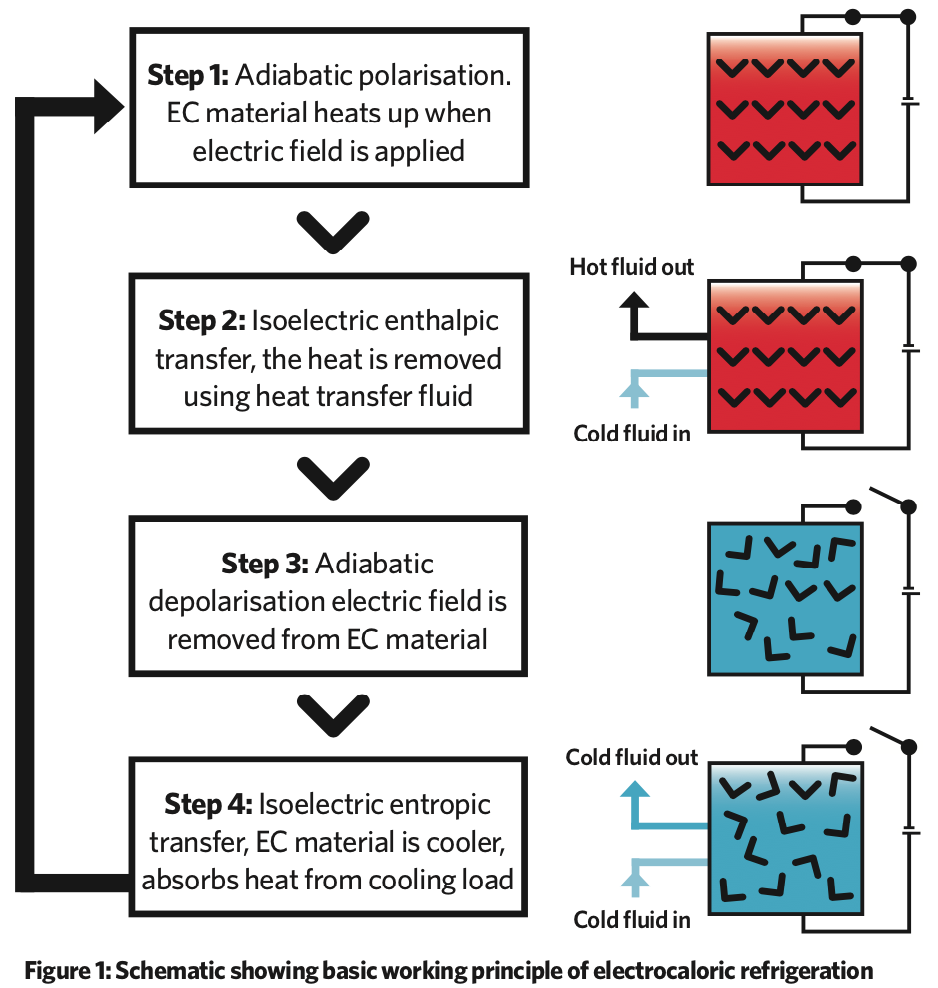
Several promising alternative, innovative heating and cooling technologies are under development, including elastocaloric, magnetocaloric, thermoelectric, barocaloric and electrocaloric. While the magnetocaloric effect has been studied extensively since its discovery by Emil Warburg in 1881 (see ‘Magnetic attraction’, CIBSE Journal, February 2016, ), electrocaloric cooling (EC) – discussed in this article – has had much less interest. It is, however, an emerging, innovative and potential low carbon technology.
The first experimental measurement of the EC effect was reported in the early 1930s, but the scale was very small. This changed with the recent discovery of the ‘giant EC effect’. Since then, the practical application of EC heating and cooling has been subject to a lot of research, and commercial applications are now on the radar.
Basic working principles
The principle of EC cooling is based on the ‘EC effect’ – the ability of a material to change temperature when an electric field is applied. An EC device has two thin materials separated by a vacuum layer. Application of an electric field causes the most energetic electrons on the negative side to jump across to the positive side. As they leave the negative side, it gets colder. Figure 1 helps to demonstrate how to use this effect. Two types of materials are normally used for EC – ceramics and polymers. Ceramics have more advantages because of their high breakdown field, higher electrocaloric efficiency, and larger cooling capacity.2
Challenges
To improve and implement new manufacturing and processing methods for materials and regenerators
Lead-containing ferroelectric ceramics show great potential for EC refrigeration technologies, but they are not acceptable environmentally. With this in mind, more research on lead-free materials is required
Advances in materials that support the absorption of large amounts of heat from a cold reservoir have been established as a priority. As such, good progress has been noted over the past five to 10 years, with the improvement of EC temperature change from 2.5K (in ceramics) to 40K (in thin films)1
Use the EC principles to generate electric energy.
The main limitation of the EC system shown in Figure 1 is the relatively small temperature difference that can be achieved between the cold and hot source. A number of techniques have been used to increase this exchange, such as active caloric regenerative process. The principle of this cycle uses a heat-transfer fluid in contact with the EC materials flowing from the cold side to the hot side when the material is heated, and from the hot side to the cold side when the material is cooled down. This progressively increases the temperature difference between the cold and hot source to about 40K1, making the system potentially suitable for a range of commercial applications.
One of the obstacles to achieving a sufficient EC effect is related to the exposure of the material to very high electric fields.
Benefits
EC cooling does not use refrigerant gas but, instead, a cooling fluid, which could be water-based. As a result, there are no direct CO2 emissions and EC heat pumps comply fully with all regulations, such as F-Gas in Europe and EPA regulations in the US.
Its advantage over magnetocaloric cooling is that the high electric fields required for refrigeration are easier and less expensive to generate than the high magnetic fields required for magnetocaloric refrigeration. There is no dependence on rare-earth materials and the pumps are the only moving parts.
Compared with existing refrigeration and heat pump technologies, EC refrigerators or heat pumps are predicted to have efficiencies of 60-70%.3 The coefficient of performance of existing refrigeration and heat pump technologies is in the range of 3-5. Major research is required to get EC refrigeration to the development stage, and there remain some challenges (see panel). Fundamental and technical features have yet to be resolved – but watch this space.
Potential applications
There are various potential applications for this technology1, including: Replacement of vapour compression in small refrigerators Small heat pumps
Thermal management of power electronics in integrated circuits
Air conditioning of hybrid and electric vehicles.
About the authors
Metkel Yebiyo is a lecturer in Sustainable Energy Systems and Building Services Engineering at London South Bank University at London South Bank University
Professor Andy Ford is acting director of research and enterprise and professor of building systems engineering at LSBU
References:
1 Kitanovski, A, Plaznik, U, Tomc, U, Poredoš, A, Present and future caloric refrigeration and heat-pump technologies, International Journal of Refrigeration, 2015
2 Ožbolt, M, Kitanovski, A, Tušek, J, Poredoš, A, Electrocaloric v magnetocaloric energy conversion, International Journal of Refrigeration, 2014
3 Analysis of potential of novel refrigeration technologies suitable for selected industries for application and improvement of food quality, energy consumption and environmental impact, FRISBEE project, 2011