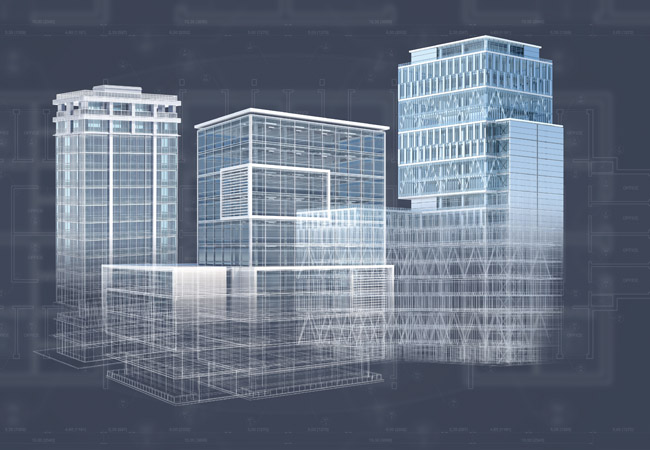
Three industry experts shared their views on the benefits and limitations of modelling at a recent event organised by the CIBSE HVAC Systems and Building Simulation groups.
Ant Wilson, formerly of Aecom, argued that modelling has limitations because human behaviour is inherently unpredictable, while Verco technical director Robert Cohen said clients can reap the benefit of modelling if buildings are simulated at every stage of construction and performance data is fed back to designers so they can improve subsequent simulations.
Built Physics director Darren Coppins’ concern was that there was little consideration of how plant responds to the building load in models.
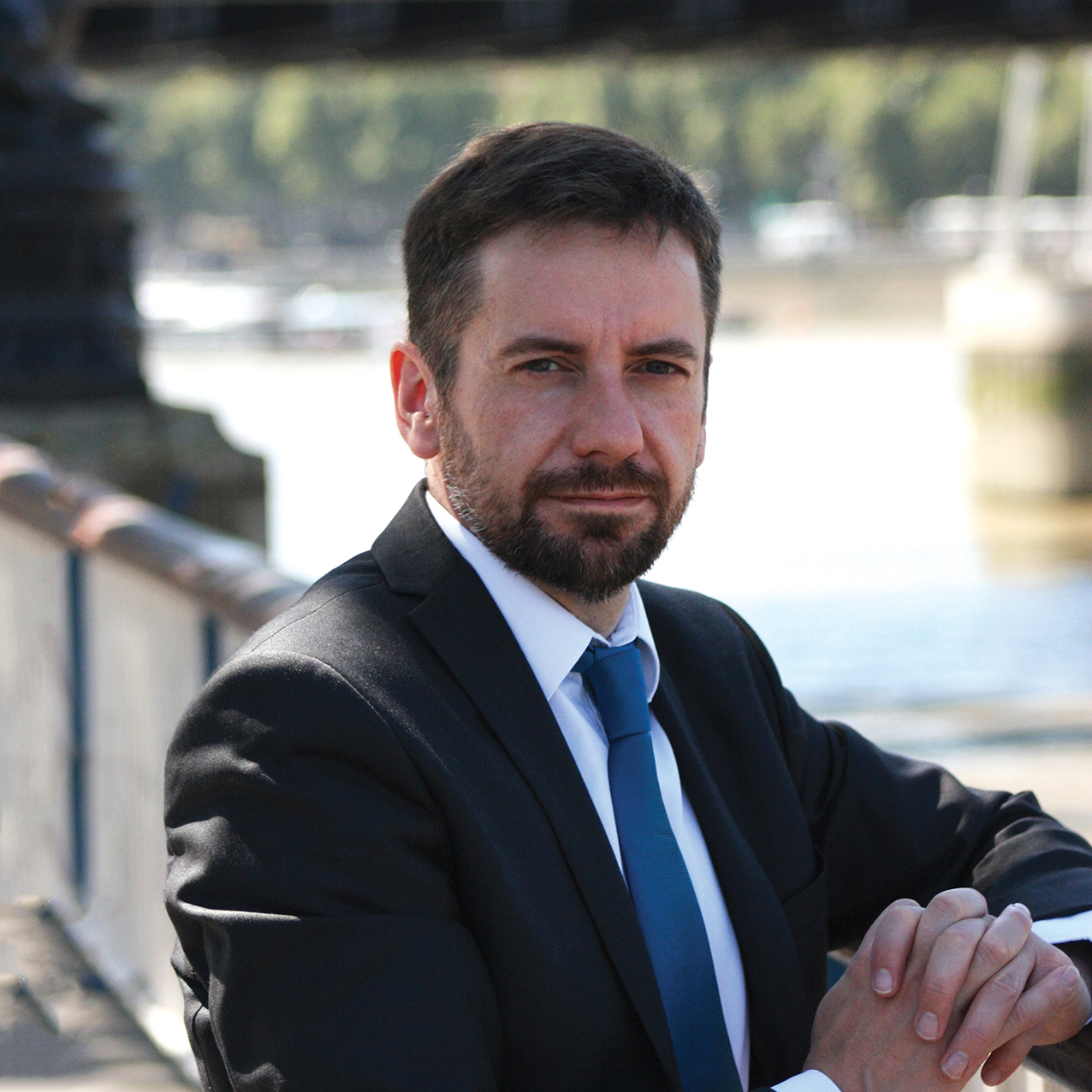
Ant Wilson was first to the podium and started by asking the audience: ‘Why do we model?’ There are a number of reasons, and Wilson highlighted the following: informing the design, ensuring compliance, creating thermal comfort, and predicting energy and carbon performance.
He said, within the building industry, we have been modelling since the 1960s, when solar simulation was used to produce an array of results, one of which might be right, but the rest of which were likely to be wrong.
Moving towards nearly-zero energy building, building performance modelling has become an inseparable part of building and plant design, but Wilson questioned the quality of the models we create.
He suggested that accuracy of results had more to do with the competency of the modeller than the software used. He added that the more accurate the data you put in, the more accurate the result you will get out.
He looked at the ideal scenario – a perfect model, created by a competent modeller, with accurate data. So why do our buildings still not perform as predicted?
Wilson likened the problem to car emissions, and why the amount of fuel used by different makes and models was so different from the manufacturers’ official figures.
He suggested that it was, in fact, the driver – and the way they drove the car – who had control of the car’s emissions. Wilson then questioned whether we operate buildings in the predicted way they have been modelled. Perhaps not, he said, and this might be because the models are unable to predict human behaviour.
Measure to improve
Cohen felt passionately that we might learn ‘a thing or two’ from Australia. Could this be the answer to how to close the performance gap between model and building?
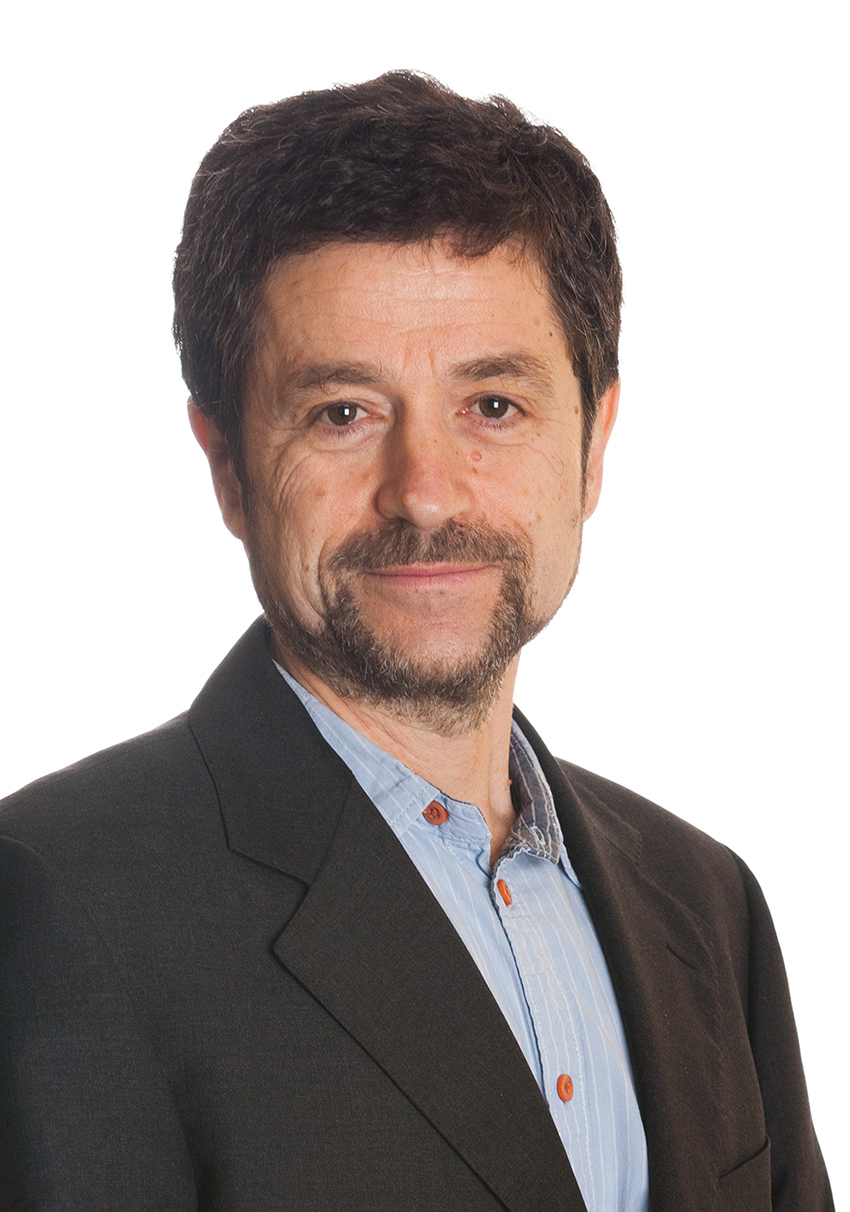
By following the process in a Nabers Commitment Agreement, Australian teams can now routinely achieve in-use operational energy performance ratings in line with the predictions of the design stage models, he said.
He demonstrated how, since 2002, by delineating, measuring and disclosing base building operational energy performance, new Australian office buildings were reducing their annual energy use year on year.
The least efficient new office building now has half the energy intensity of its peer in 2002, while the most efficient is five times less energy intensive. It is striking that equivalent data for the UK is not available but, in 2012, a BBP study suggested London’s average energy intensity for office buildings was similar to Melbourne’s average in 2002.
But what are the factors behind this market transformation? Cohen highlighted two: the market – including occupiers, investors, developers and supply chain – asks for, and values, performance; and the use of commitment agreements to design for performance by setting targets, undertaking advanced simulation modelling, fine-tuning, verifying and then disclosing achieved performance, leading to lessons learned.
If the building is simulated at every stage of the project, from concept through to user occupation, the energy performance can be more accurately checked. Cohen concluded that performance feedback to the original designers was imperative to ensure improvement in their next design. He said to improve performance, we must measure performance.
Accuracy of results has more to do with the competency of the modeller than the software used
Coppins rounded off the presentations by examining HVAC system modelling, asking what it is and why it is important.
Most larger commercial buildings in the UK have some form of energy intensive HVAC system, he said. Currently, the majority of modelling only uses simple formulae for plant efficiency; however, the actual performance can be significantly more complex.
One of his concerns was that we model thermal loads in detail with little consideration for how plant responds to the building load.
By simulating HVAC systems, we gain a greater understanding of energy consumption. For example, if the controls philosophy and plant items are specifically modelled, then outputted data can be used to understand the suitability of the plant, and can offer more realistic building loads, helping to reduce plant sizes and systems.
Coppins said there might be an answer to the performance gap, but conceded there are still many factors impacting our ability to predict energy use. He showed examples of building services that had just ‘gone wrong’ in construction, illustrating that human error is a major factor in the discrepancy between prediction and performance.
All three speakers felt that modelling gives a valuable insight into the behaviour of a building, but the results are highly dependent on the competencies and commitments from all those entwined in the building process to understand, learn, implement and take responsibility.
- The next HVAC Systems event, Low carbon heating – how to meet the challenge, will be held on 23 October. For details, visit cibse.org/Groups/HVAC-Systems