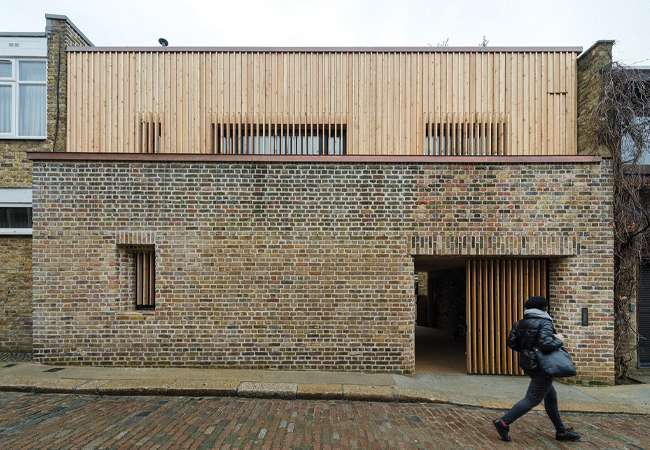
Credit: Tim Crocker
Max Fordham’s House will leave a lasting legacy. Not only because it was built to the Passivhaus standard, but also because the scheme features innovative insulated shutters, which Fordham hopes will become an energy efficiency solution for future retrofit and low-cost housing projects.
Designed and built in collaboration with Max Fordham LLP (the practice he founded), bere:architects, Price & Myers and Bow Tie Construction, the three-bedroom home, set in a tight, urban infill site in Camden – previously Fordham’s garden – was completed in February 2019 and is undergoing Passivhaus certification.
The building’s thermal envelope, its ventilation system and windows are all designed so that the heat loss on an overcast, cold winter’s day is no more than the heat generated by people living in the house.
Envelope
The building frame is concrete with insulated timber walls, with incorporated airtightness and moisture-tightness layers, eliminating thermal bridges and uncontrolled air exchange.
As well as allowing daylight into the home, removing the need for electrical lighting during the day, the windows allow solar radiation to warm the inside air. They feature automated insulated shutters that have been developed to reduce night-time heat losses and to achieve an energy balance between gains and losses on a winter’s night.
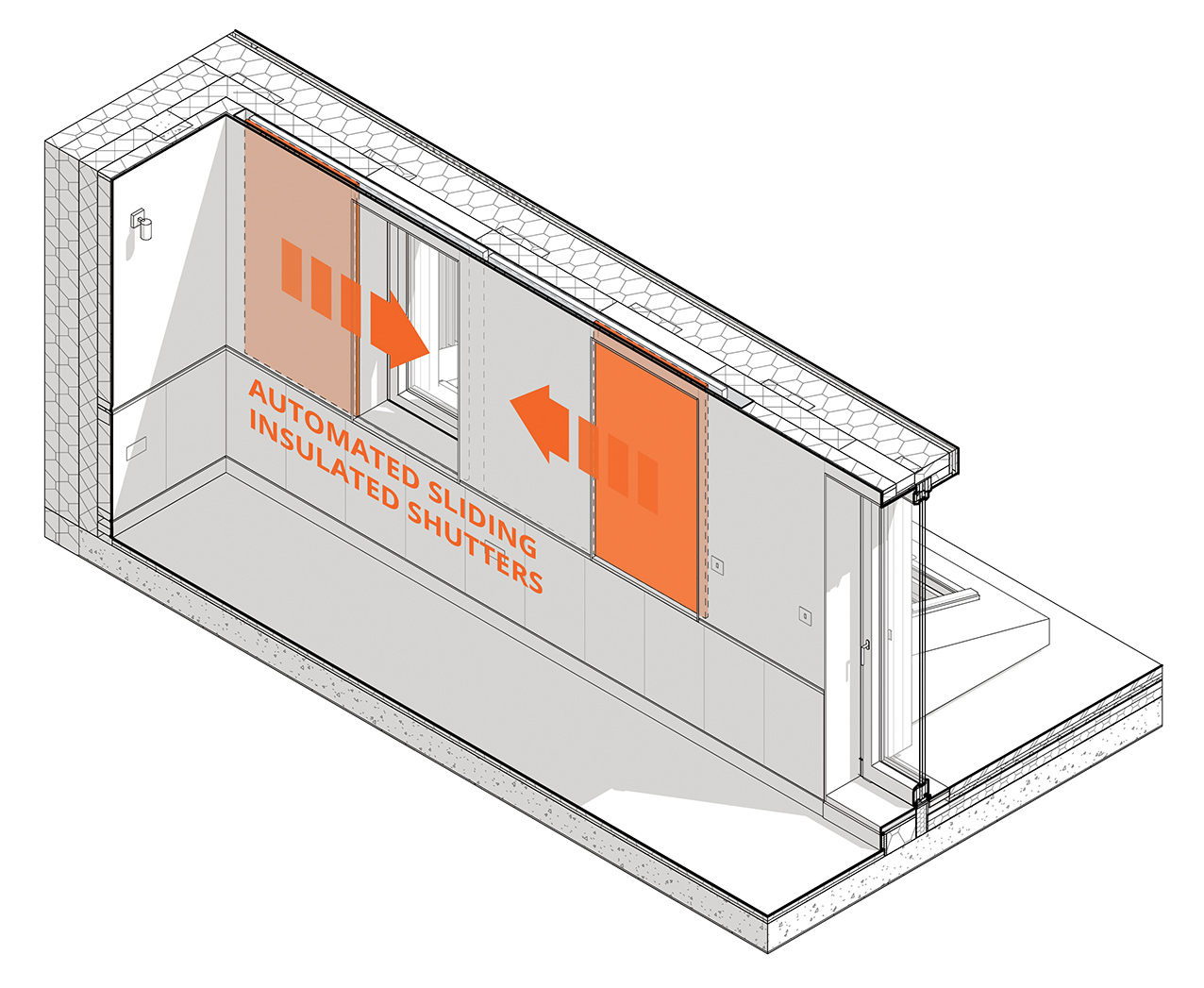
Usually, on cold, grey days, more heat is lost through a window at night than gained during the day. ‘We have altered the behaviour of the windows so they are net contributors to the building’s heat balance, even on a freezing, overcast day,’ says Ali Shaw, senior engineer at Max Fordham.
He says the horizontally sliding thermal shutters – constructed from polyurethane rigid foam (PUR) panels and integrated into the internal fabric of the building – are intended to maintain a constant comfortable internal temperature, and to defend against extremes of both external cold and heat.
The shutters allow the windows to become much more insulating at night so the windows are thermally a net benefit every day. It is hoped that this technical concept, when proven, can be replicated in low-cost housing projects as retrofit items.
To ensure a healthy indoor environment, ventilation is controlled mechanically, with heat recovery efficiency in excess of 90%.
Overheating risk is mainly mitigated by windows that open fully, says Shaw. The top-floor rooms, which have the most solar exposure, are dual aspect, and rooms with daytime occupation are thermally massive.
The horizontally sliding thermal shutters are intended to maintain a constant comfortable internal temperature, and to defend against extremes of both external cold and heat.
The MVHR system provides a modest amount of night cooling, while the window/shutter design offers more night cooling through partially open window and shutter combinations.
‘We did an admittance calculation in line with CIBSE Guide A during the design stage. This is a fairly simple calculation that only looks at 24 hours, and we felt it showed the house would be reasonably comfortable during prolonged very hot weather,’ says Shaw. ‘This calculation was based around a very hot day in a 2050s London climate. We would expect a more sophisticated calculation that looked at a whole year to show cooler indoor air temperatures, and we would expect cooler indoor air temperatures in reality.’
The building performed well during the recent summer heatwave, adds Shaw, maintaining internal temperatures between 25-28oC through a diurnal cycle when London was between 24-34oC.
Figure 1 shows the external air temperature for 25 July 2019 – during the recent heatwave – which is similar to the day against which the house was modelled, the modelled internal temperature, and the measured internal air temperature. ‘The building performs well in hot weather, and as expected,’ says Shaw.
He says during warm nights with little wind, buoyant forces created by temperature differences would drive some natural ventilation. ‘There is also some night cooling with the mechanical system as well,’ he adds.
The risk of overheating is managed, partly, by the shutters, which can be closed during hot summer days to limit solar gains, and can be opened wide at night to purge excessive heat. North-facing windows have inbuilt timber slats to maintain privacy, and south-facing windows are partially shaded by a deciduous apple tree in the summer months. The windows can also be slightly open with the glossy and reflective shutters closed.
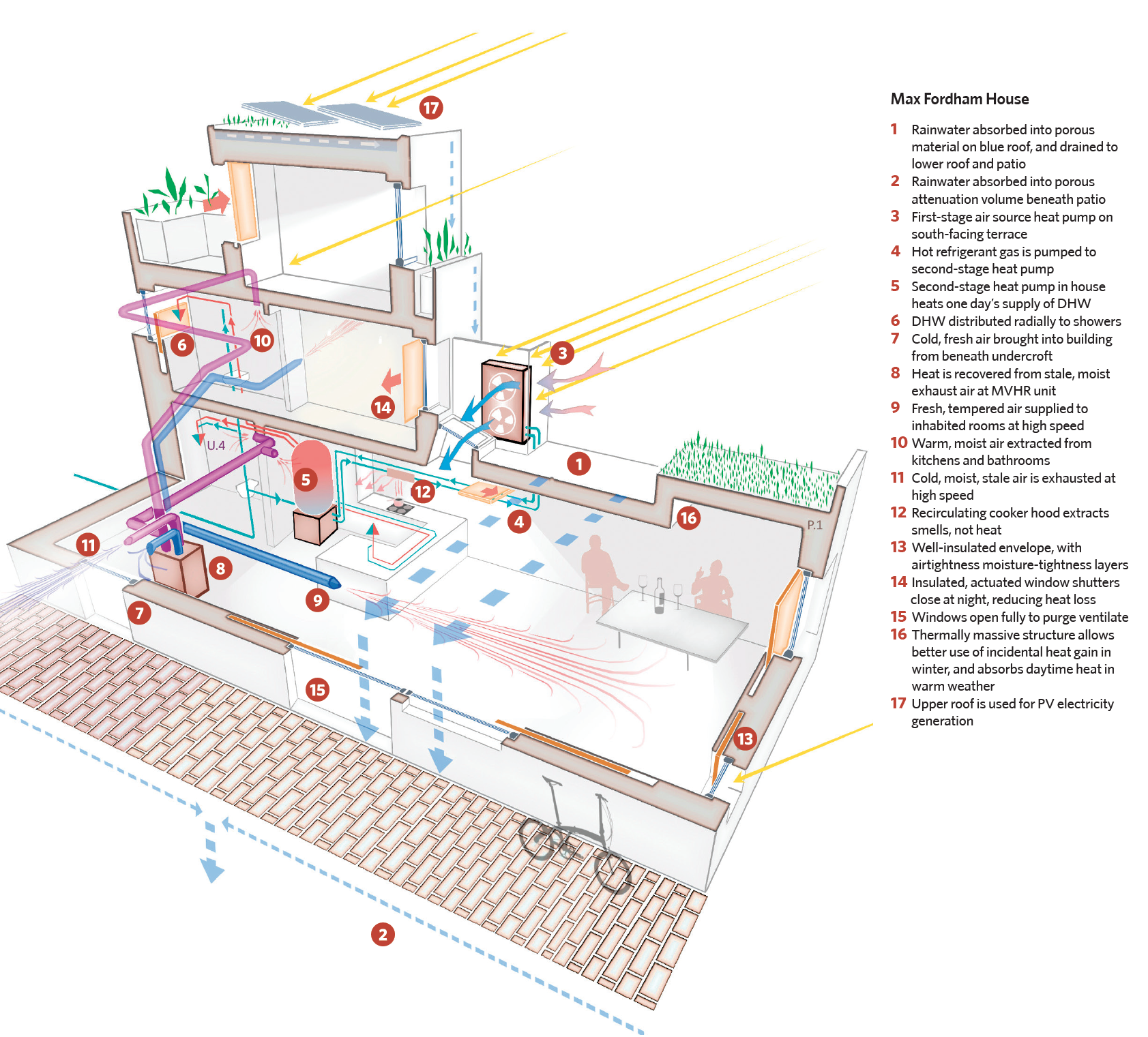
Water supply
Domestic hot water (DHW) is the largest energy demand in the house. Although solar thermal technology was considered, heat pump technology aligns well with the continuing decarbonisation of the national electricity Grid.
A two-stage air source heat pump with an integrated DHW tank supplies the high-grade heat needed, and uses naturally renewed air as its heat source.
While some summertime efficiency may be sacrificed in the second compressor, this is compensated by the high wintertime efficiency, and the lack of immersion heating needed. The heat pump works in tandem with the MVHR system that is fitted throughout.
The heat pump’s air-side heat exchanger is located within a suntrap on a south-facing terrace, and operates for an hour each afternoon, when air temperature is warmest and the heat pump is most efficient. This is also when the roof PV array is likely to be at its most productive.
Hot refrigerant gas is pumped indoors to the second-stage heat pump, which heats one day’s supply of domestic hot water, distributed radially to showers. The second circuit takes heat at about 45oC and boosts it to 65oC.
Shaw says radial DHW distribution is used to avoid recirculating domestic hot water. The cylinder is located very close to the showers and the kitchen sink, and the pipe sizes are kept small, so draw-off times are quick.
‘The nature of the house means we’d expect high turnover through all the branches. Meanwhile, DHW is generally stored at 60oC – rather than 50oC with weekly pasteurisation – which drove the selection of a two-stage heat pump that produces 65oC DHW fairly efficiently,’ says Shaw.
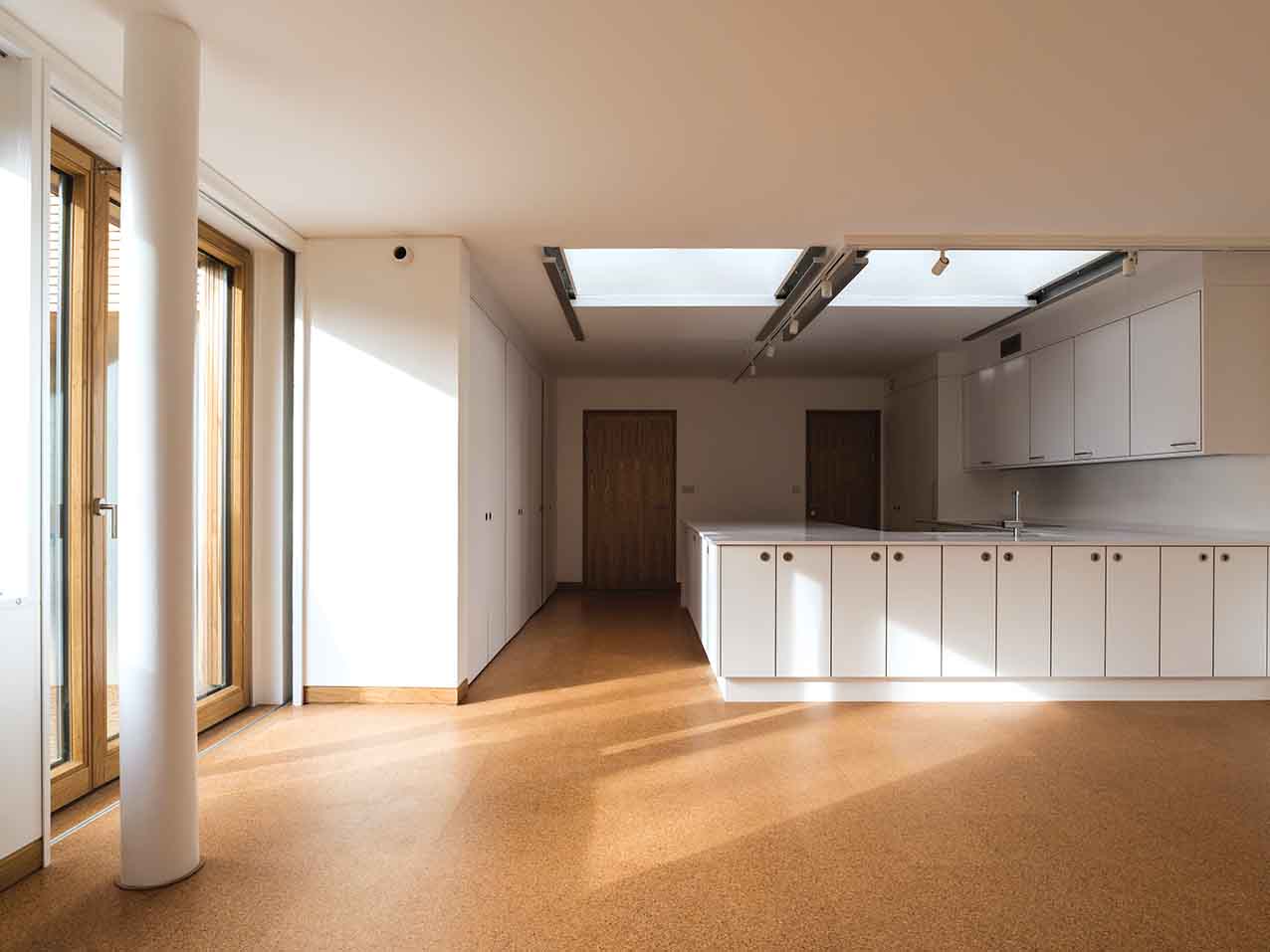
HVAC
Cold fresh air is brought into the building from beneath the car undercroft. Heat is recovered from stale, moist exhaust air at the MVHR unit, and fresh, tempered air is supplied silently to inhabited rooms at high speed through 3D-printed jet nozzles.
Warm, moist air is extracted from kitchens and bathrooms, and cold stale air is exhausted at high speed.
Roof engineering
Planning was awarded for the home to be slightly higher than its neighbours, which maximises the effectiveness of the 5kW roof-mounted solar panel array, generating around 4,000kWh annually, almost all the energy needed for the house.
Rainwater is attenuated in the green roof and planters, absorbed into porous material, and drained to the lower roof and patio at a controlled rate. It is then absorbed into an attenuation volume below the patio, before being slowly drained away. A rooftop copse of hazel plants on the first floor also contributes to the biodiversity.
Max Fordham House won the RIBA London Sustainability Award 2019, a RIBA London Award and is shortlisted for the RIBA House of the Year 2019. And, this winter, it will undergo its biggest test – keeping its occupants warm without heating.
Project team
Client: Max Fordham
Architect: bere:architects
Passivhaus consultant: Max Fordham in consultation with Passive House Institute
Energy rating assessment: Max Fordham
M&E engineer: Max Fordham
Structural engineer: Price & Myers
Main contractor: Bow Tie Construction