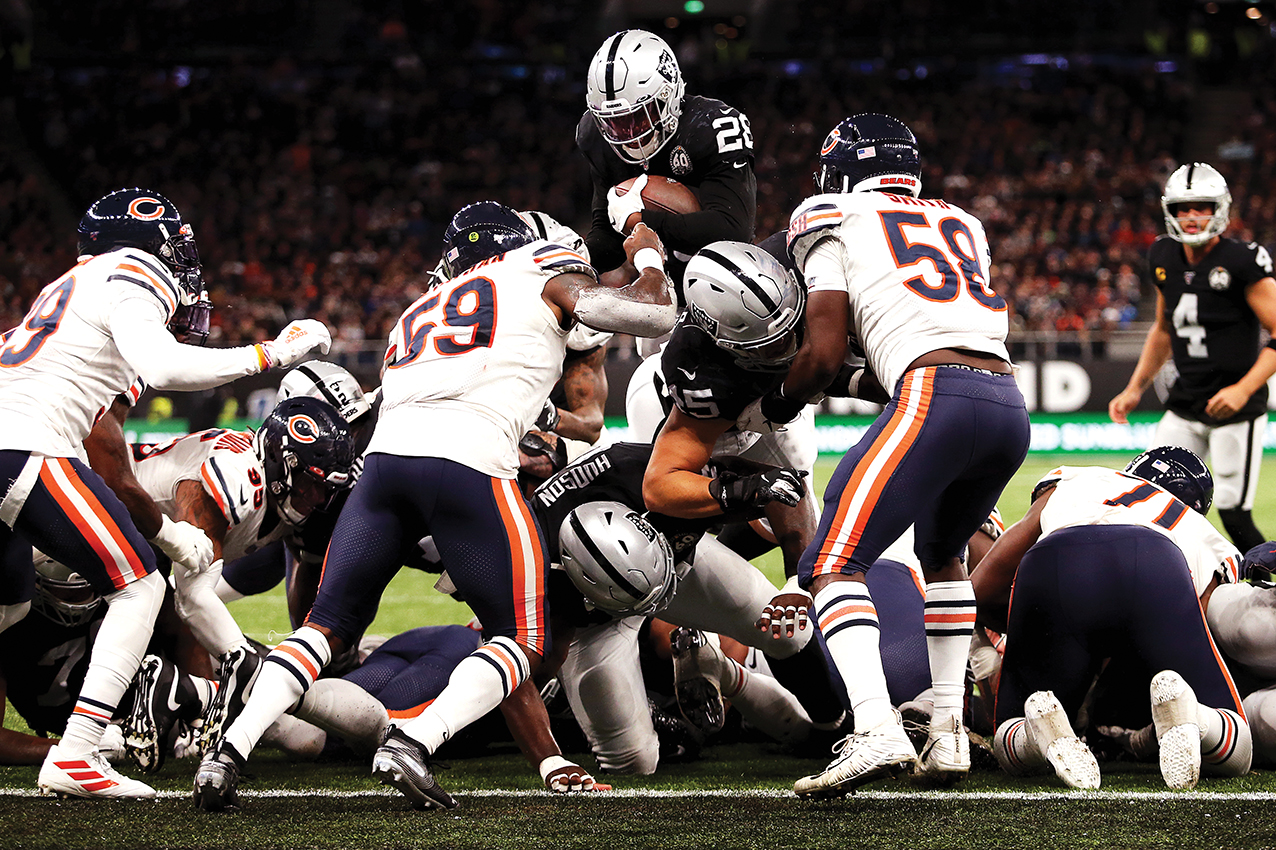
Tottenham Hotspur FC’s new 62,062-seater stadium in north London is unlike any other in the world. It features a natural turf pitch that can be retracted to reveal an artificial playing surface to enable American football (NFL) games to be played, and concerts and other events to be hosted at the venue.
The first Premier League football match at the stadium took place on 3 April 2019, when Tottenham beat Crystal Palace 2-0. The first NFL game to showcase the stadium’s unique ability to host the USA’s most popular sport was played last month, when the Chicago Bears lost to the Oakland Raiders.
The stadium bowl’s most distinctive feature is its 17,500-capacity South Stand – the largest single-tier stand in the UK – which the stadium’s architect, Populous, says will enable the home fans to create a ‘wall of sound’. It is supported on two giant, tree-like columns, beneath which is a food and drinks hall containing what is claimed to be Europe’s longest bar, at 65m.
This is enclosed by the stadium’s glazed façade to create a place for fans to congregate before and after matches. The stand is also home to a micro-brewery, operated by Beavertown Brewery (there are ‘Tap Inn’ bars all over the site). The brewery, along with a cafe, is one of many features designed to draw people to the building on non-match days.

The food and drinks hall claims to have Europe’s longest bar, at 65m
In contrast to the single-tier South Stand, the North, East and West stands incorporate a higher and lower tier of seating, plus a huge variety of private and corporate suites and bars spread over nine levels (see panel, ‘Two-tier stands’).
‘Mechanically, it’s a fairly simple scheme,’ says Mark Owen, associate director at BuroHappold Engineering, the project’s building services engineers. ‘The bulk of the mechanical air handling plant, along with eight chillers and 10 boilers, are located in the main mechanical plant spaces on levels six and seven; services drop down risers located in the six main access cores, to feed the various levels.’
The access cores are spaced around the stadium; there are two serving each of the East, North and West stands. As well as the mechanical risers, the cores contain electrical risers, lifts and the main access stairs.
The hospitality spaces are kept comfortable using an all-air system, with heated and cooled air supplied from the air handing units located in the level six plant space. Fan coil units (FCUs) provide localised peak-lopping – for example, above bar areas where crowds are expected to gather. FCUs also provide heating and cooling to the individual hospitality boxes, enabling the boxes to be used at times other than on match days.
The sheer number of hospitality floors and spaces means 57 kitchens and catering facilities, spread over the stadium’s nine floors are required. To ensure domestic hot water is available to all of these, hot water calorifiers are ‘dotted all over the place’, says Owen.
To cope with the huge variations in domestic hot water demand leading up to, and during, a match, the calorifiers are heated by low temperature hot water (LTHW) with electric backup. Owen quotes a domestic water demand figure of 4L.s-1 at three hours before kick-off, rising to 11L.s-1 20 minutes before kick-off. This pales into insignificance, however, when compared with the 55L.s-1 to satisfy the half-time rush.
In contrast to the hospitality floors, main concourses on level one and level five are classed as outside spaces, because they incorporate openings to the spectator seating pitch side and feature perforated sections of the façade on the exterior. As a result, piped services in these areas incorporate trace heating.
The area beneath the South Stand is also classed as an external space, although Owen says the large area of glazing means ‘it will remain comfortable, even in winter’.
Pitch perfect
The South Stand accommodates the ‘pitch pocket’ – a basement recess into which the grass pitch can be retracted in three sections, each weighing more than 3,000 tonnes, by 68 electric motors in 25 minutes. Being able to roll the pitch into a purpose-designed repository is fundamental to maximising the building’s functionality. As well as allowing American football to be played there, it enables the stadium bowl to be easily converted into a venue for concerts and other events.
Environmental conditions are critical to ensure the grass on the pitch is maintained in perfect health while it is stored. Lighting that mimics sunlight and irrigation systems keep it green and watered. ‘The grass has to be kept healthy, but they don’t want it to grow too much, because it cannot be cut when stored in the pocket,’ says Owen.
The key is to keep the temperature in the pitch pocket cool while blowing air to agitate the grass. ‘In agitation mode, we ramp up the fan speed to blast air out of nozzles so that it ruffles the grass,’ adds Owen.
The pitch pocket has two bespoke environmental systems: one humidifies and dehumidifies the space; the other provides heat and cooling. Owen says the cooling load is ‘massive’, and when the pitch is in storage, energy is diverted from stadium systems to serve the pitch-pocket environmental plant.
‘It’s a trade-off,’ he explains. ‘Pre-event, while the stadium is still in setback mode, chilled water and heating are supplied to the pitch-pocket plant; then, hours before the event is due to start, the stadium switches to normal operating mode and the pitch-pocket systems switch to setback mode. There is enough inertia in the pitch pocket for the pitch to sit for a day without any treatment.’
The stadium stands, level by level
Starting at the basement, the levels in the North, East and West stands are:
- Basement: car park
- Level 0: pitch level, where the changing rooms and match-day facilities are located
- Level 1: main concourse, where the public enters, It is also where many of the bars and food outlets are located
- Levels 2, 3 and 4: hospitality floors
- Level 5: high-level concourse
- Levels 6 and 7: mechanical plant spaces
- Levels 8 and 9: additional hospitality, including the level nine Sky Lounges on top of the East and West stands, joined by a glass bridge incorporated into the roof structure to give spectators panoramic views of the pitch.
The show will go on
The electrical system has been designed to allow the stadium to continue to host a football game even if the incoming supply fails during a match. Inside the stadium, an 11kV, medium-voltage, three-core supply cable rings the basement to feed four 2.5MVA transformers.
Each transformer feeds a main low-voltage (LV) electrical panel, which in turn feeds sub-distribution panels on the upper floors. Unlike the mechanical services, which drop down risers from the Level 6 plantroom, the electrical services are generally distributed at basement level and feed up the risers.
Each of the four main electrical panels is divided into four sections based on the criticality of the loads; these are life-safety, essential, match continuation and non-essential. Two generators, each rated at 2.5MVA, provide a total of 5MVA of back-up power. The generators have 24 hours of fuel storage and each has an additional three-hour day tank in case there is a problem with the main fuel-storage tank.
To add further resilience to the scheme, output from one generator’s electrical panel feeds two main LV panels, while output from the second generator’s panel feeds the other two main LV panels.
An interconnector links the two generator panels so that any main LV panel can be supplied from either generator. The scheme has been designed to cope with various power-loss situations (see panel, ‘Emergency power doomsday strategy’).
‘If a transformer explodes, we’d be able to run its LV panel from either of the two generators,’ explains Ryan Carr, electrical engineer at BuroHappold. ‘If we lost all power, we could run the life-safety, essential and match continuation sections of the panels on both generators; if one generator failed, we’d still be able to run life-safety systems for the entire building from the one generator.
‘We’ve completed a significant amount of doomsday testing for Building Control to get the stadium’s safety certificate.’
The stadium has been designed to be safe and to operate under various power-loss situations. There are four categories of electrical loads, depending on their importance: Category 0: Life safety These loads are the most important and typically comprise smoke control, fire fighting lifts, and emergency lighting. Category 1: Essential The next most important, they include primary IT, security systems, and UPS equipment. Generally, if either generator is unavailable, or one fails, only life-safety and essential loads will be maintained and the stadium will be evacuated. Category 2: Match continuation These loads, along with categories 0 and 1, are required to enable match play to continue in the event of a utility power failure. They include: field-of-play lighting; media lighting and power; hospitality lighting and power (excluding kitchens); and ventilation. When both generators are available the system can support Categories 0, 1 and 2. Category 3: Non-essential These loads are the least important and not generally generator-supported. They include façade lighting, escalators, catering chillers, kitchens, and food and beverage areas. The South Stand’s glazing will keep it comfortable, even in winterEmergency power doomsday strategy
Some of the big electrical loads the design has to be able to deal with include lighting and IT. Pitch lighting is based on 324 LED fittings in a 450kW scheme. The scheme also includes façade lighting, while the roof features what Carr describes as a ‘halo’ of light integrated into the roof eaves, to project colour onto the top of the roof.
There are also RGB LED uplighters mounted within the roof structure, to enable the club to project a variety of colours onto the roof’s underside.
The stadium incorporates a huge amount of IT, including everything from security to pitch lighting. It also has wireless connectivity across the venue to enable fans inside the stadium to connect with and share their live-event experiences with others around the world.
The IT systems are backed up by two, 600kVA uninterruptible power supply (UPS) systems, which will ensure continuity of operation until the standby generators kick into action.

The stadium incorporates a huge amount of IT, from security to pitch lighting
The stadium’s 57 kitchens are classed as non-essential under the criticality classification. The main kitchen, which prepares food for all of the stadium’s smaller processing kitchens, has a mighty 1,000-amp supply. ‘If there is a power failure during a game, the match can continue, the TV broadcast can continue, but hot food will no longer be available,’ Carr says.
Surprisingly, the micro-brewery located beneath the South Stand is classed as non-essential, too. It includes an electric steam boiler fed from two supplies of 520A and 250A. The brewery also has a distribution board to serve pumps, among other things, and this has a 250A supply.
‘To keep the loads manageable, the brewery does not brew beer on the same day as a match is scheduled,’ explains Carr.
The stadium opened to critical acclaim for the quality of its design, if not for the quality of football played on the night. Now that this major landmark is complete, the second phase of the site’s development is set to begin and will include a 180-bedroom hotel, an extreme sports building with the UK’s tallest climbing wall, a community health centre, and 222 new affordable homes. Game on.
BuroHappold Engineering, which designed the building services for Tottenham Hotspur’s new home stadium, was the winner of the Building Performance Consultancy (Over 1,000 Employees) category at this year’s CIBSE Building Performance Awards. The focus of the consultancy is on delivering high-performing buildings and cities via six core areas: delivering building performance; health, wellbeing and productivity; BIM for efficient delivery; smart buildings; digital design for the built environment; and design for prefabrication. The award judges were particularly impressed with the work by the building performance group to create an interactive database for all modelled and measured data across BuroHappold Engineering’s global portfolio of projects. This will enable project teams to understand how their buildings are performing in use and on a year-on-year basis. It is good to see what BuroHappold is doing to address building performance and to get that understanding reflected in what is delivered on site, said the judges.In a (CIBSE) league of their own