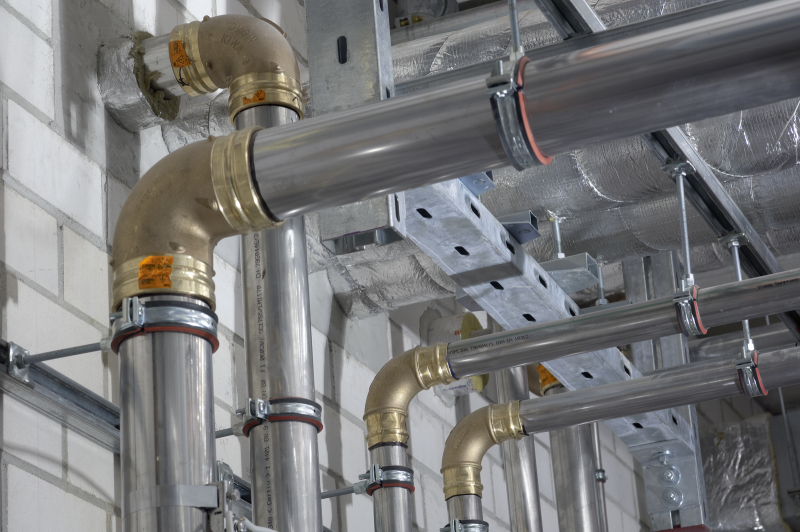
One of the most common causes of issues with heating systems, hot and cold water and potable water pipework is poor maintenance. While the system may be designed, installed and commissioned according to best practice, if it is not maintained correctly it can leave the system vulnerable to corrosion and contamination.
Corrosion is a key concern for all water pipework due to the level of dissolved oxygen present in most systems. While it is possible to deoxygenate water, for most applications it is impractical and prohibitively expensive. However, there are steps that can be taken to extend the lifespan of the pipework.
Firstly, once the system is filled it is recommended that draining the system is avoided wherever possible as this inevitably exposes the pipework to much higher levels of oxygen. As soon as oxygen comes into contact with water on the surface of the metal, corrosion will begin to occur. If it becomes necessary to drain the system, the work should be planned to limit the amount of time it is left before being refilled.
Furthermore, establishing a programme of regular maintenance is crucial as this will help to identify and address any issues before they begin to affect the health of the system. For example, when commissioning heating systems it is best practice to dose the system with a high-quality chemical inhibitor that prevents the accumulation of sludge and protects the metal in the system from corrosion and limescale build up.
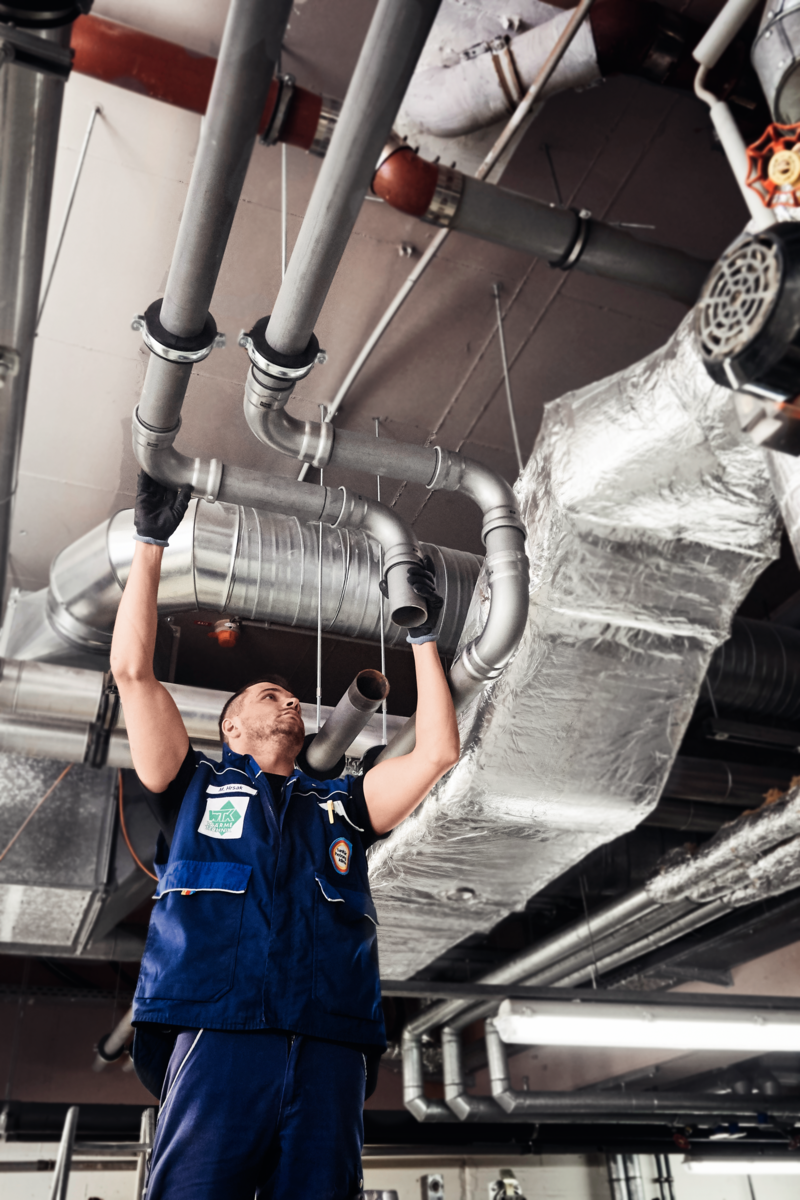
However, the concentration of these chemicals in the water can deplete over time so this must be checked as part of the maintenance cycle. Ensuring the levels of inhibitor in the system will not only protect the pipework from corrosion but will also protect the boilers, pumps and other equipment from the damaging effects of sludge.
Correct care and maintenance practices are also crucial to protect the quality of the potable water supply. Stagnation of water in the system is one of the most common causes of contamination as it provides an environment in which the bacteria can grow.
The design of the system can help prevent this by avoiding the creation of dead-legs in the pipework and ensuring that the pipe is sized correctly to help maintain pressure and flow. However, the usage patterns of the building have to be considered as interruptions in the usage will also cause stagnation.
For example, a school, college or university building will be used intensely during term time but will typically be left empty for weeks during holidays. Similarly, seasonal hotels and office buildings may have rooms, areas or even floors that are left unoccupied for extended periods.
To prevent stagnation and the build-up of bacteria during this time, a plan must be put in place to flush the system. Automatic and manually activated flushing systems are available that simplify the process in buildings that will regularly be unoccupied. Alternatively, pipework can be manually flushed by opening each outlet to refresh the water.
Furthermore, it is important that the temperatures of the water in the pipework are not allowed to rise or fall excessively. Legionella bacteria breed most effectively between 25°C and 45°C and so it is recommended that water is stored above 50°C. However, while this guidance may be followed, the temperature of the water can decrease as it travels through the building.
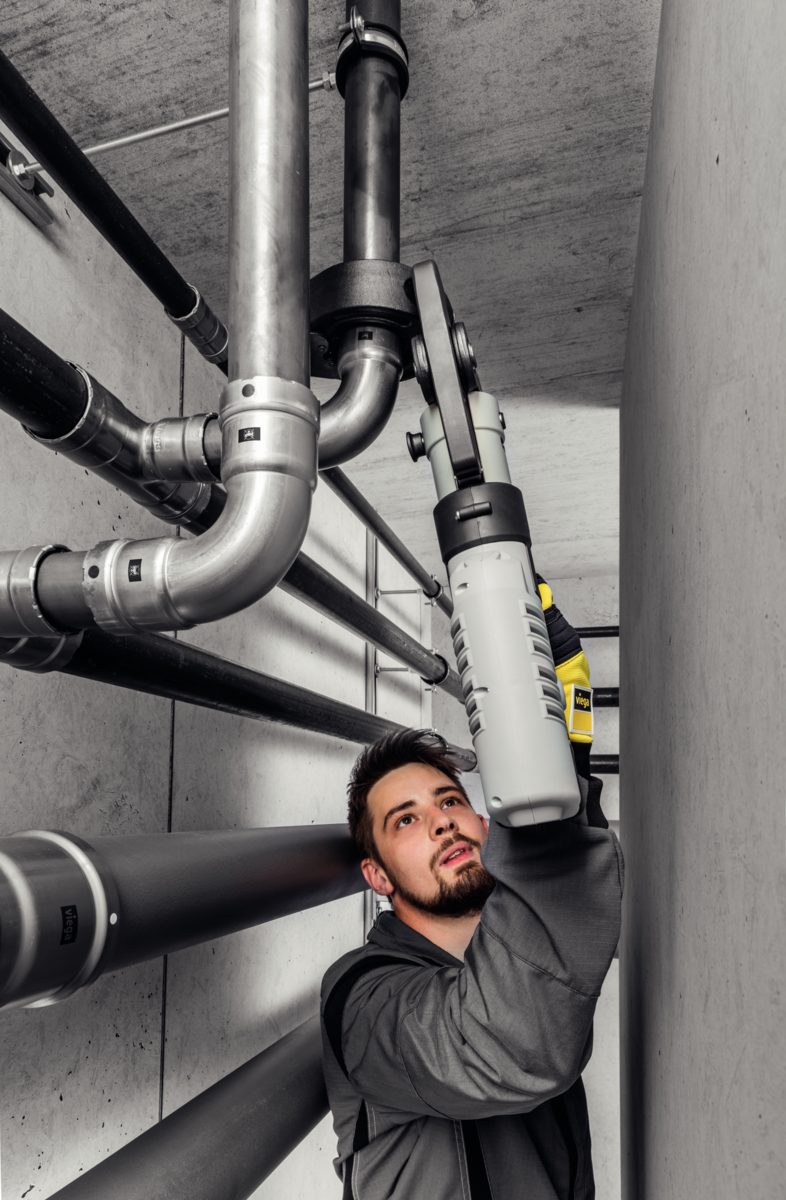
Similarly, the temperature of cold water supplies can rise, especially if routed close to sources of heat and can cause the temperature to enter the range where bacteria can grow rapidly. Therefore, ensuring the correct level of insulation is installed and maintained is vital – not only to maximise energy efficiency but to protect the quality of the water.
Finally, the choice of products for repairs or additions to the system must be considered carefully as this is a potential source of contamination. Bacteria can be introduced during the manufacture of components and equipment. For example, any water left in the product after wet leakage tests in the factory will encourage the growth of bacteria during storage.
As such, products that have been dry tested are recommended. Often, once bacteria are established in the system it can be difficult to remove and there have been cases where the system has had to be disinfected repeatedly over a number of years to treat the contamination.
Following best practice for ongoing maintenance and repairs is just as important as ensuring the correct design, installation and commissioning of the system. Manufacturers of pipework components can provide guidance on the right approach to care and maintenance.
Viega has developed a CIBSE accredited CPD on potable water systems that covers everything from planning and design to installation and maintenance. To find out more visit: viega.co.uk/en/service/CPD