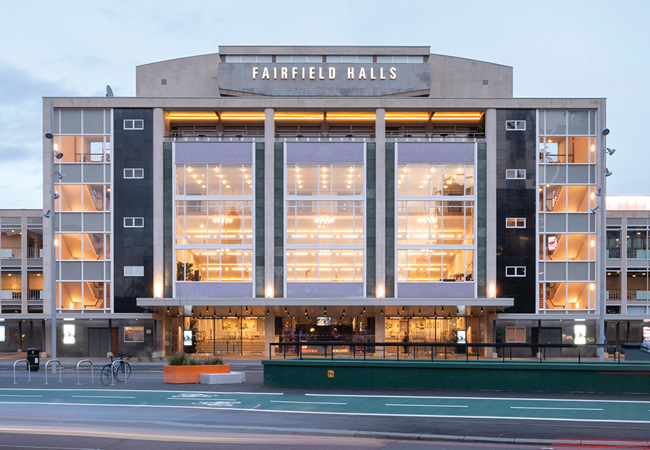
The 1960s performance venue is a striking part of the Croydon landscape
After a £42m refurbishment by MICA Architects, Croydon’s Fairfield Halls performance venue has been returned to its original 1960s design intent.
The foyer has been decluttered and the two main auditoria, the Phoenix Concert Hall and the Ashcroft Theatre, have been brought up to date. An underused gallery space to the south has also been converted into two multipurpose creative spaces to expand the types of events the Halls can host.
Trying to bring a 1960s public building up to current comfort standards has been quite a challenge. From a building services perspective, this means delivering the modern levels of comfort and ventilation expected of a 21st century venue, but with the same ducts, risers and plantrooms that served the original scheme.
‘One of the really tricky things with working on existing buildings is the constraints they impose on the MEP,’ says Edmund Chan, principal engineer at Max Fordham, the project’s MEP, lighting and acoustic engineers.
The giant 1,600-seat Concert Hall (1,800 seats including the choir stalls) is at the heart of the building. Its rows of reconditioned, deep-red, material-covered seats are set against panels of Japanese oak that line the auditorium’s lower walls.
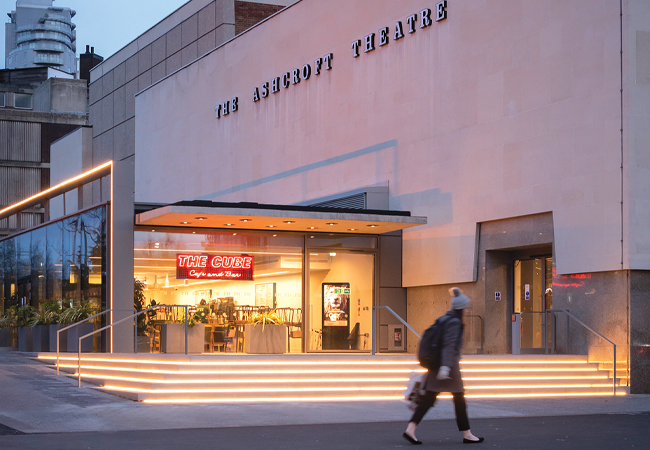
MEP engineers had to work within the constraints of the original building’s scheme
Rising up from the joinery is the hall’s supporting concrete frame, complete with double-skinned brick infill panels, its form clearly visible in the white of the upper walls. At the junction of these two finishes is a dark-coloured band, which contains two rows of jet nozzles for supply air ventilation. Perimeter ventilation supply was a legacy of the original system that Chan has had to adapt to work for the hall’s new ventilation scheme.
At this point, it should be mentioned that the outstanding acoustics of the original Concert Hall meant that it had a reputation as one of the best venues for orchestral music in Europe. So good was its reputation, that it was used by the BBC to record classical music performances, mostly without the audience present.
In the original 1960s installation, ductwork transported tempered fresh air from the Concert Hall’s plantroom, located above the stage, and through the auditorium ceiling void, from where it dropped down the walls through voids between the brick infill panels to supply air to perimeter grilles.
The architect’s philosophy of being true to the original means that alterations to the walls, ceiling or wood panelling were not an option, so Max Fordham had to use the existing duct routes to the hall’s perimeter to ventilate the refurbished venue. ‘For a newly constructed concert hall, you would build in low-velocity supply grilles under the audience seating, but our only option was to supply air into the hall through from the side walls. We had to carefully design the system so that ventilation, audience comfort and noise criteria are all achieved,’ explains Chan.
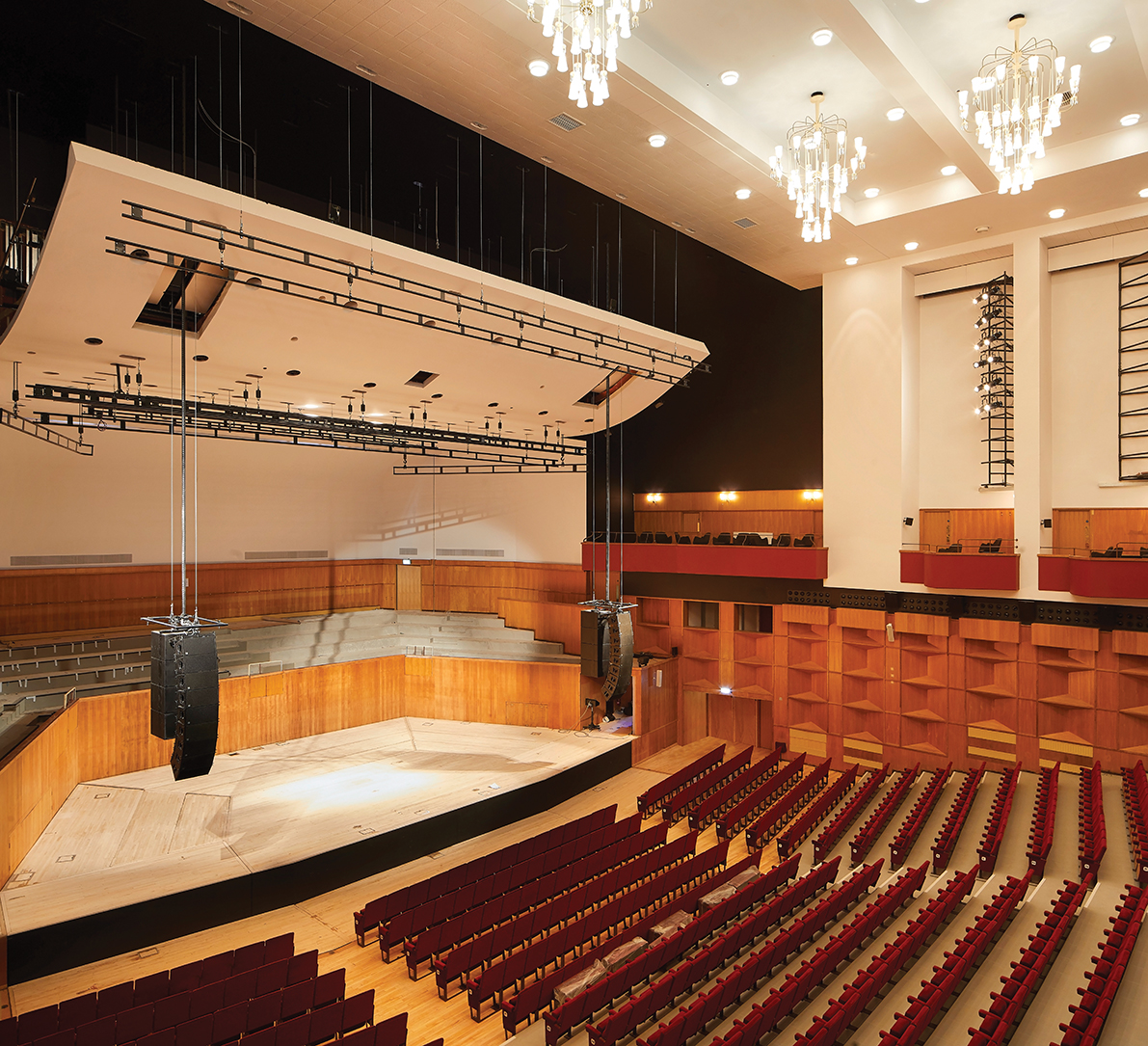
The Concert Hall’s acoustics are among the best in Europe for orchestral music
The original system was designed to push 100% conditioned air in from side-wall nozzles, with stale air extracted from grilles set into the auditorium ceiling, with no form of heat recovery or recirculation. ‘Air turnover was massive, but using perimeter grilles meant air would never reach the audience seats in the centre of the hall,’ says Chan.
Max Fordham’s ventilation system for the hall uses three air handling units (AHUs), each with heating and cooling coils, a heat-recovery wheel and an air-recirculation capability. ‘You do the hall’s temperature control through air recirculation as much as possible, and then you introduce fresh air based on CO2 levels,’ says Chan.
The three-AHU solution adds operational flexibility. One AHU serves the stage area, one the stalls and one the balcony; individual units can be turned off – for example, if the balcony is not in use. ‘We’ve segregated the systems so you have stage vent separated from stalls vent, separated from balcony vent, so you can turn the fresh air down accordingly,’ Chan says.
Rolls of sound-absorbing material hidden in banner boxes at high level on the walls can be unfurled to adapt the reverberation time of the Concert Hall
The system is designed to supply fresh air at a rate if 8L.s-1 per person. ‘We’re limited by the number of nozzles in the auditorium; if we’d wanted to supply more fresh air, we’d have put in more nozzles, but there was nowhere to put them,’ Chan says.
To deliver fresh air to where it is needed, and to limit the air velocity through the jet nozzles, Max Fordham used extensive computational fluid dynamics modelling. The jet nozzles are angled between five and 15 degrees from horizontal, depending on their location in the auditorium to ensure good air movement across the audience seating. Noise is minimised using attenuators, lined plenums and by controlling regenerated noise.
‘The ventilation system has pre-sets, calibrated to suit different situations,’ says Chan. For example, during recording sessions, the facilities team can select a mode that achieves the lowest noise levels and provides sufficient fresh air for an orchestra without an audience.
The foyer has been ‘decluttered’ as part of the Hall’s refurbishment
Where new finishes have been applied to the hall, these have been selected to match the acoustic performance to the original finish they replaced. The one significant addition to the hall is what Chan terms ‘acoustic banners’. These are rolls of sound-absorbing material hidden in banner boxes at high level on the walls. For the majority of events, the banners will remain furled, but they can be unfurled to adapt the reverberation time of the hall – for speech-based events, for example.
Max Fordham tested the hall’s acoustics as part of the commissioning process. ‘Acoustic testing was done during the night to minimise the influence from other noise sources,’ says Chan. The acousticians have also used the Covid-19 lockdown as an opportunity to make additional measurements to validate the Concert Hall acoustics and quantify the effect of the acoustic banners.
Ventilating the Ashcroft Theatre
The ventilation system for the 800-seat Ashcroft Theatre is very similar to that of the Concert Hall, with fresh air delivered via wall-mounted jet nozzles and extracted through ceiling grilles; Chan describes it as ‘Concert Hall lite’.
Two AHUs serve the theatre; one supplies fresh air to the stage and the front of the auditorium, and the other the rear. ‘As with the Concert Hall, we have front and rear AHUs, which can be turned on or off individually depending on occupation levels,’ Chan explains. These AHUs have heating coils, heat-reclaim wheels and a recirculation facility, with the ability to add cooling in the future.
The AHUs are located in a plantroom above the stage. Ducts transport the tempered air from the units and through the ceiling void above the auditorium, to supply branches that drop down in the walls of the auditorium to feed the jet nozzles.
Routing the ductwork through the ceiling void was much more of a challenge for the theatre. Unlike the Concert Hall, which is supported on a concrete frame, the roof of the theatre is supported by a series of dense steel trusses, which Chan describes as the bane of his life.
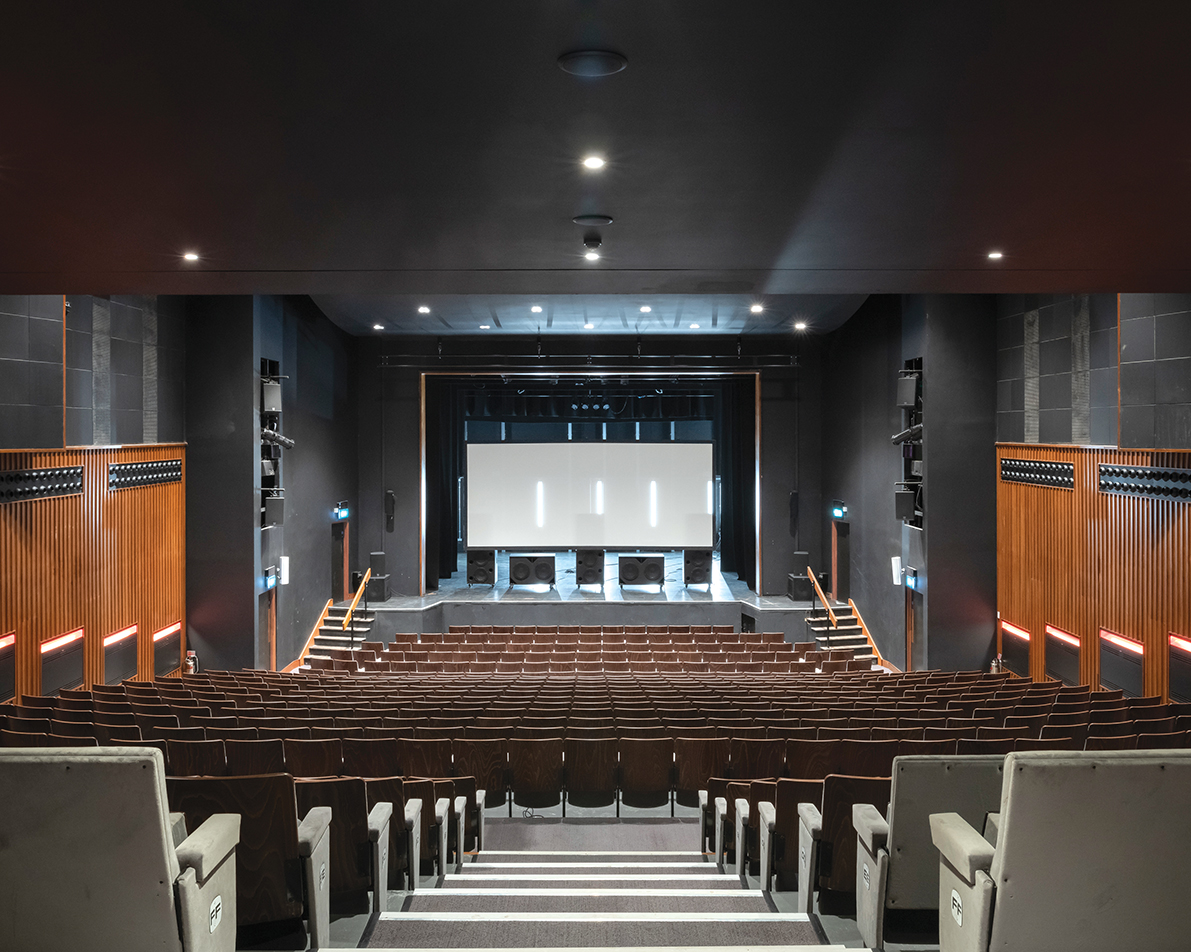
Chan describes the theatre’s new ventilation system as ‘Concert Hall lite
He says the original ventilation system must have been designed alongside the steelwork very accurately to ensure the ducts could be threaded through the forest of angled steel.
‘I’d be lying if I said everything went in as we’d designed it, without hitting a single beam,’ Chan says, laughing. ‘Some of the voids and risers could only be accessed from scaffolding; when we started to open them up, we discovered things such as downstand beams that were not on historic drawings.
As with the Concert Hall, the challenge with the theatre was to provide modern levels of comfort and ventilation within the constraints imposed by the existing structure while keeping noise to a minimum. ‘We managed to drive the ventilation rates up by pushing more air to the rear of the auditorium,’ says Chan.‘Space constraints meant we had to build attenuators into the wall voids, which was a less efficient solution than having one big attenuator upstream.’
Ready to return
The lighting control system for the theatre is also similar to the one used for the Concert Hall. All of the original fittings have been refurbished or rebuilt and fitted with LEDs (see panel, ‘Making light work of Fairfield Halls’). All the fittings are tuneable, dimmable and linked to the house-lights system.
The revamped and revitalised Fairfield Halls opened in September 2019 to critical acclaim. Seasonal commissioning of the building services was part of the contractor’s remit. The systems’ operation was optimised for winter conditions.
However, when it came to commissioning for spring and summer, the country was in Covid-19 lockdown and all performances had been suspended, so commissioning was put on hold until the venue reopens.
Hopefully, it will not be long before audiences can return to appreciate the iconic architecture, comfortable environment and outstanding acoustics.
Making light work of Fairfield Halls
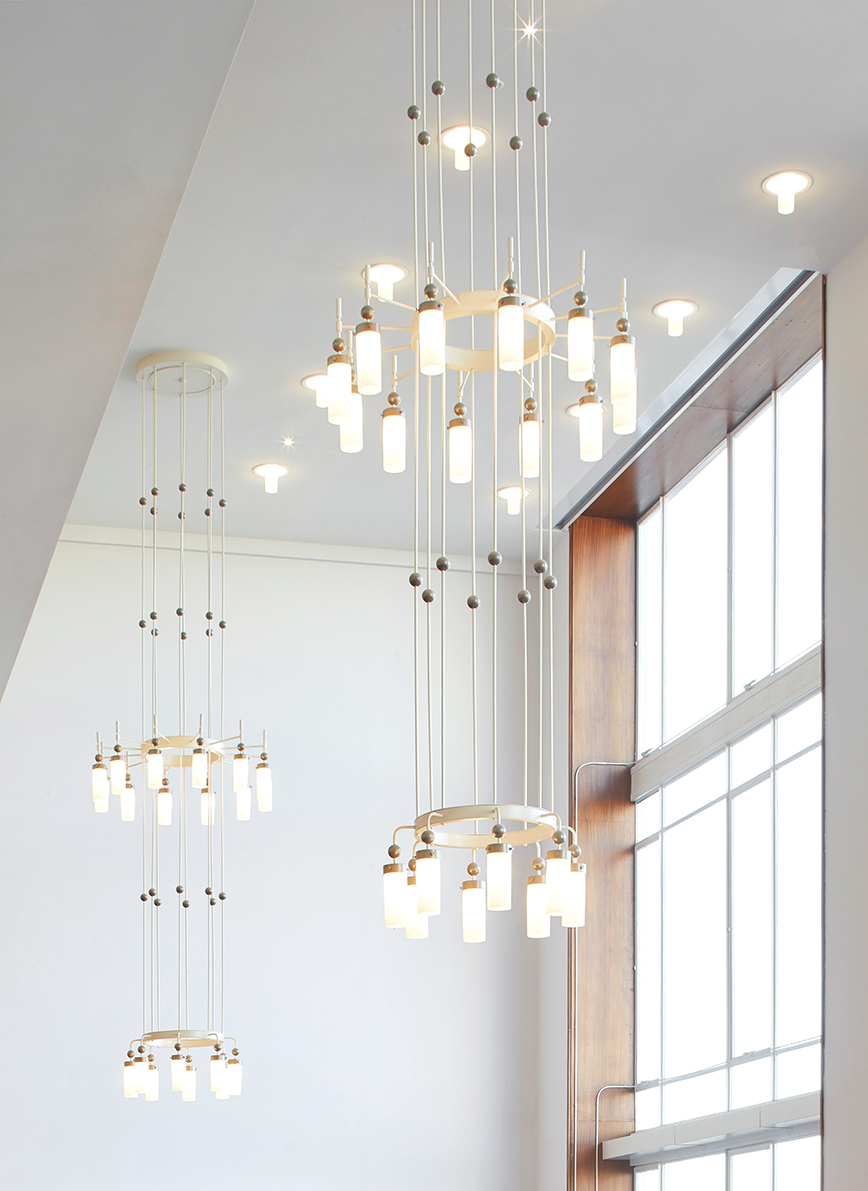
Our overarching ambition in re lighting Fairfield Halls, says Chan, was to restore the original character of the venue while using the latest technologies to minimise energy costs and bring a higher level of flexibility and control.
This meant creating bespoke lighting fixtures, sometimes by refurbishing and adapting what was already on site and sometimes by designing new lights based on old photographs and archive evidence of the original installation.
Fortunately for Max Fordham, bespoke lighting manufacturer and renovation specialist Dernier & Hamlyn was based locally.
Perhaps the most challenging of all the lighting projects was the restoration of the eight Concert Hall chandeliers, to bring them up to current electrical standards and enable them to accommodate LED lamps.
The chandeliers’ size meant they had to be dismantled carefully on site so they could be transported to Dernier & Hamlyn’s workshop.
Here, they were stripped back to their original metal fi nish before being given a new powder-coated finish in a period colour. Replacement glass shades had to be handmade to fit.
To complete the restoration, hundreds of crystal elements were sourced and fitted to the conical cowls above the shades; these had been in the original fittings, but had disappeared over time.
Some of the lighting was too far gone to be repaired. Originally, Dernier & Hamlyn was asked to renovate 139 recessed lights. When these were removed, however, it became evident that they were beyond reasonable repair, so Dernier & Hamlyn recreated the original fittings, which it adapted to incorporate LED lamps.
Dernier & Hamlyn also manufactured 44 semi-recessed down lights for the Concert Hall’s house lights to replicate the original fittings, using black-and-white photographs from the 1960s for reference.
Similarly, for Fairfield Hall’s foyer, three two-tier chandeliers, each 5.4m long, had to be recreated using black-and-white photography from the venue’s early days as inspiration. Each chandelier has 20 conical, opal glass shades, supported on 24 metal rods and balls finished in shades of silver and cream. Above each
chandelier is a metal ceiling plate that houses control gear for the dimming system.
Max Fordham used ETC ArcSystem lamps in the Concert Hall and theatre, with tone-adjusting dimming for a warm ambience and fittings controlled by a wireless DMX system. Low-energy decorative fittings by Lucifero and Lightnet were chosen to add interest to the circulation spaces
Covid-secure theatres
Many of Max Fordham’s clients are asking how building design and operation can help mitigate the transmission of coronavirus. ‘The key area on which we can have an impact is the ventilation – reducing the concentration of aerosol through good ventilation in terms of volume, distribution and filtration of air,’ says Mark Palmer, senior partner at Max Fordham.
Good ventilation design is about delivering adequate volumes of fresh air to all occupied parts of the auditorium through good design and system controls, says Palmer.
‘Displacement ventilation, with air supplied under each seat, is the best way to get good quality air to every person, because they are sitting in the freshest air in the room, with potentially contaminated air extracted at high level,’ he adds.
During the pandemic, theatre operators should also adjust ventilation controls to increase ventilation rates, prevent recirculation of contaminated air, and extend the run-on period.
‘In the past, some theatres have not taken air quality seriously enough, but if the public is to return, theatres need to be able to show that they have taken appropriate measures and that things are being done right,’ Palmer says.
One positive he hopes will come about as a result of coronavirus is an increased awareness of the importance of good ventilation, which, Palmer says, ‘will be no bad thing for general health and wellbeing’