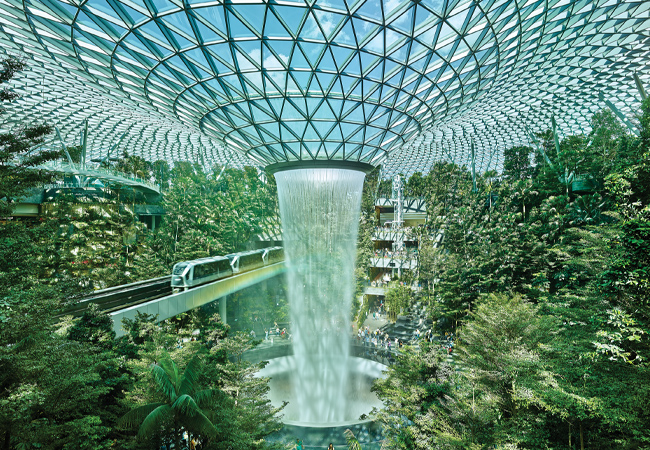
Jewel Changi Airport, where up to 23m3 of water falls per minute in the world’s tallest indoor waterfall
The world’s tallest indoor waterfall is the centrepiece of Jewel, at Singapore’s Changi Airport. In an otherworldly space, water showers down from an oculus in the centre of the building’s 200 metre-diameter, toroidal glass roof.
The waterfall plunges 40m into a valley blanketed by an indoor forest of 1,400 trees; the valley’s sides rise up five storeys in a series of terraced gardens. Trails twist up through the terraces, a canopy of activity nets is strung above the tree tops, and a sky bridge provides visitors with a vertical perspective down onto the vegetation.
Beneath this 20,000m2 forest garden are five floors of 280 shops, restaurants and a hotel. Designed by Safdie Architects, and located between the airport’s existing terminals, the Jewel building is open to the airport and the city. Trains carrying passengers to the airport’s terminals pass through this lush space on an elevated track.
Modelling daylight
Modelling was the key to resolving the competing demands of light and heat for the gardens. Plants need high levels of daylight to thrive, but with high levels of daylight come high levels of solar heat, which could make the space uncomfortable for visitors.
Using a combination of bespoke ray-tracing and illuminance prediction software linked to the architect’s 3D BIM model, Atelier Ten modelled the light coming through each triangular glass cell of the grid shell roof (designed by Buro Happold) for each hour of the day over a year, to evaluate different glazing materials and surface coatings in terms of energy demand and use.
The modelling resulted in a glass coating being selected that admits 62% of the sun’s energy as visible light while admitting only 33% of that energy as heat. In addition, a frit-pattern was applied to the glass in different densities, to further reduce the solar gains in areas where daylight levels were less critical. The ability to limit solar gain was vital in reducing cooling demand to keep the public spaces comfortable.
Mapping the daylight also gave PWP Landscape Architecture a thorough understanding of the quantity of light available when it came to determining the planting for a particular area to create the lushly landscaped forest valley for a climate-controlled indoor forest. Atelier Ten worked with PWP to adjust the surface properties of the glass to shine more light into areas where plant species required higher light levels.
The biggest challenge of Jewel Changi Airport was the potential impact of the waterfall on occupant comfort. The main concern was the air movement generated by 23m3 of water falling every minute. There was no precedent for an indoor waterfall of this scale, so environmental engineering consultant Atelier Ten used computer modelling and the application of fundamental building physics to recreate the environmental impact on the indoor environment.
If modelling the deluge wasn’t challenging enough, the design team also had to measure the impact of trains running through the space. Complex software was used to find a way for trains to simultaneously enter and leave without conditioned air escaping the building.
The dependency on modelling for the success of the project meant building physics was at the core of the workflow, says Atelier Ten director Meredith Davey. ‘We used it to inform the design development rather than for simply validating our finished design,’ he adds.
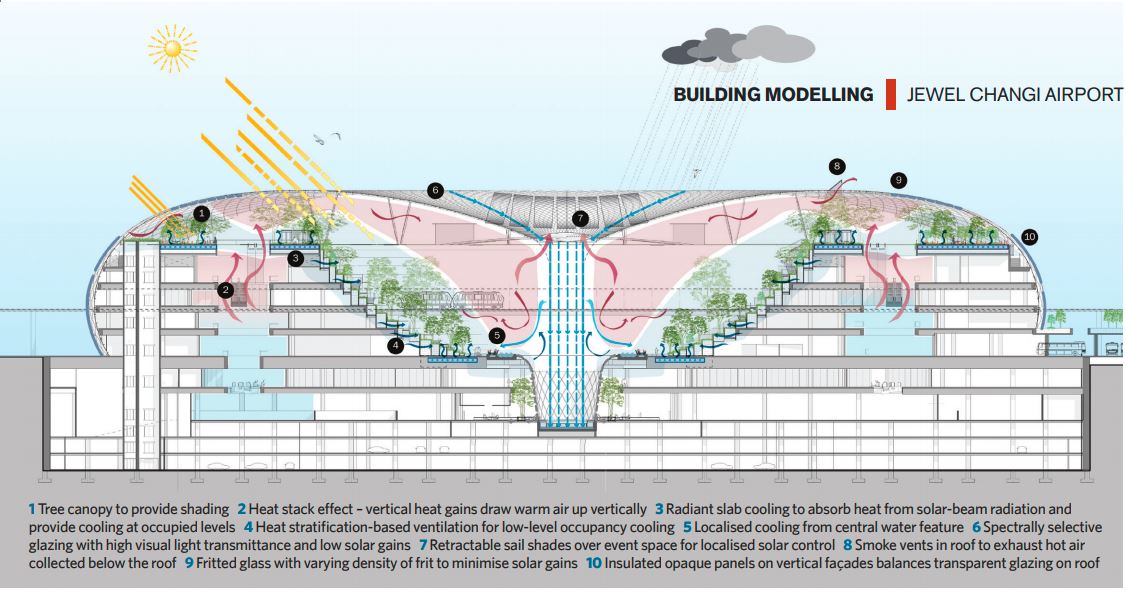
The concrete slabs with embedded cooling act as a giant thermal buffer to absorb the solar heat before it can be radiated into the air
The Jewel opened last year and, thanks to the extensive modelling, the waterfall and trains have had no adverse affect on plants or visitors. In November, its success was recognised by Atelier Ten winning a CIBSE Building Simulation Award.
A shopping mall like no other
The scheme has similarities with the series of giant air conditioned greenhouses of Singapore’s Gardens by the Bay attraction, for which Atelier Ten was also the environmental engineering consultant. At Jewel, the consultant provided strategic environmental design, analytical consultancy and conceptual services engineering.
As with Gardens by the Bay, the challenge was to achieve the delicate balance of providing natural light for the plants and thermal comfort for visitors, while minimising the building’s energy demands in Singapore’s tropical climate.
Conditioning the volume under the glass roof would have used enormous amounts of energy, so only the occupied zones are conditioned. These are maintained at a temperature of approximately 24°C using a combination of integrated displacement ventilation and hard paved areas with embedded chilled water pipework. ‘It worked well at Gardens by the Bay, so we thought it was a good idea to do it again,’ says Davey.
Dealing with the solar gains was one issue, but by far the biggest challenge was the potential impact of the waterfall on occupant comfort. ‘For Gardens by the Bay, we did some modelling of the impact of a waterfall on the internal conditions, which, although crude, was broadly right,’ says Davey. ‘[In Jewel] the scale of the waterfall and its central location in the space was so integral to occupant comfort that we had to go way beyond making simple assumptions.’
Designed by WET, the waterfall – or rain vortex as it is termed – is an impressive piece of engineering. Rain falling on the inner slope of the toroidal roof flows down to a slot opening forming the perimeter of the oculus.
From this opening, a vortex of water plunges down eight storeys, the final three of which are contained within a giant, transparent, acrylic tube as it passes through basement retail. At the foot of the fall, water is collected and pumped back up to the roof, to ensure a constant flow of 4.5m3 per minute. The spectacle is enhanced for 20 minutes in every hour, when pumps ramp up to deliver water at up to 23m3 per minute.
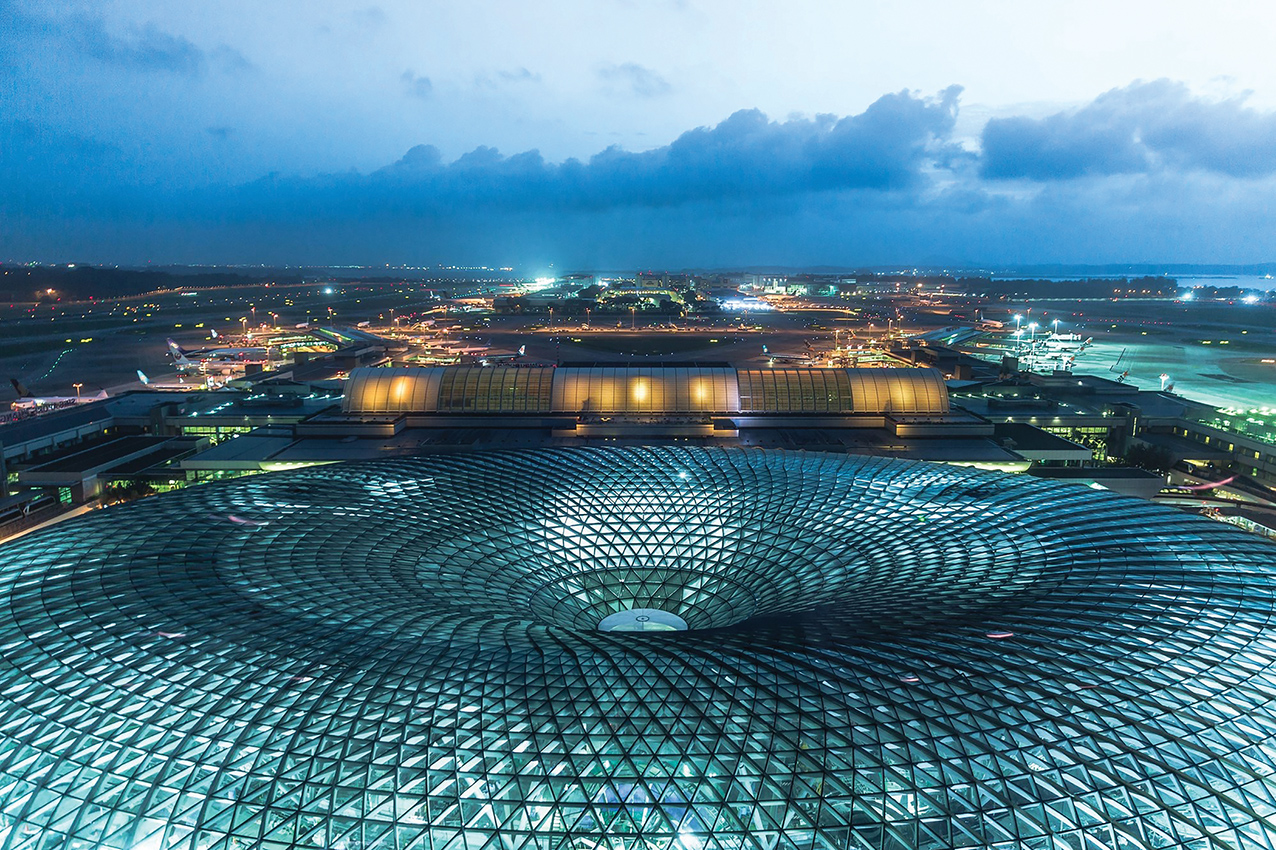
The toroidal roof of the Jewel makes an impressive addition to Singapore
The intent was to model, in detail, the impact of the waterfall on the space. While the cascading water will naturally cool the air through adiabatic evaporation, its impact on the huge volume was, Davey says, ‘relatively minor’. Of much more concern was the air movement generated by the huge volume of falling water.
When it came to modelling this, the engineer found very little information. Davey says the modellers spoke to an academic who had modelled airflow in a shower to find out why the shower curtain is drawn into the cubical when the shower is in use. ‘That was the nearest approximation we could find to modelling air movement around a waterfall,’ he says. The design team corresponded with him to outline its proposed methodology, which he endorsed as appearing to be ‘on the right track’.
The reason it was so difficult to model the impact of the waterfall on the surrounding air is because it is a series of interacting elements. As each drop of water falls through the air it creates a comet’s tail of drag behind it that accelerates the surrounding air. Then the team modelled what happens when two water droplets next to each other fall through the air: ‘There is some drag, but there is also interference, so it is not a perfect teardrop,’ Davey explains.
The more droplets modelled, the more complex the model. For example, they wanted to know what the impact would be of a droplet falling in the middle of 30 million droplets. In this case, the air around the droplet will already have been accelerated, but the droplet will still be accelerating because of gravity, Davey says. ‘In very fast air, the droplet will be pulled apart to become smaller droplets, so the model very rapidly goes from what sounded like a simple challenge to a hugely complex task to define what is actually going on.’
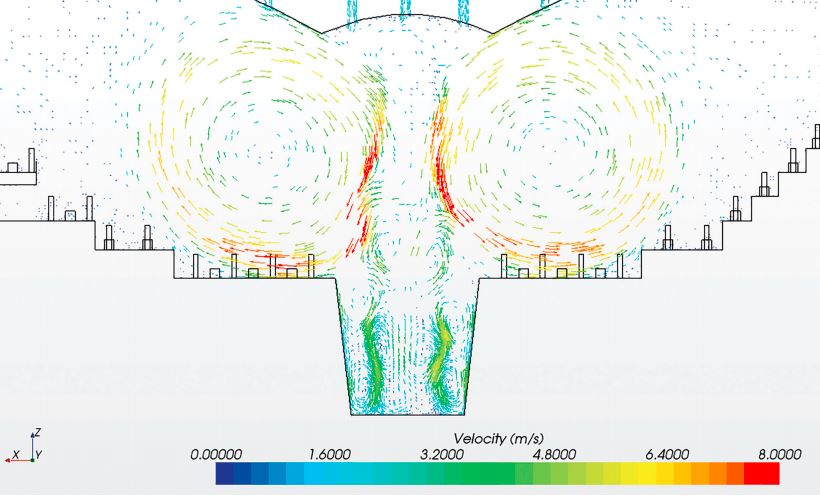
Computer model showing water fall dragging hot air downwards before being pushed horizontally by air being forced back up the cylinder at the waterfall base
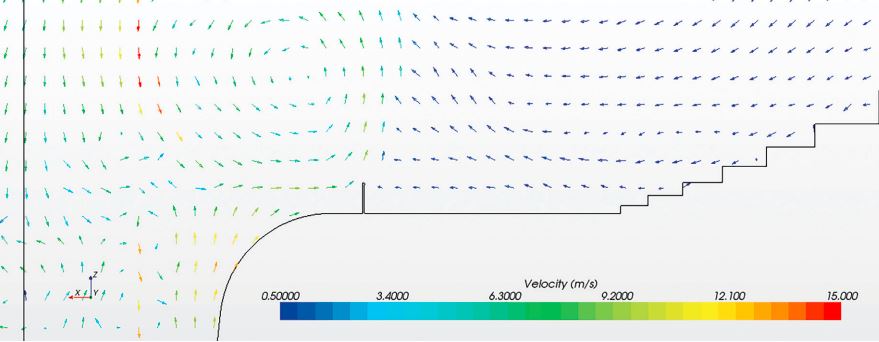
A balustrade deflects the air being pushed up from the cylinder from a horizontal pattern to a vertical pattern. This creates an air curtain-like effect stopping the air flow from the waterfall from moving laterally, and enables comfort to be maintained inside the wider volume
Their solution was to approach the modelling from both a macro- and micro-scale. ‘We were doing macro modelling analytically from first principles, using engineering and fluid dynamic equations, to establish what this mass of water might do to the surrounding air; then we were doing stochastic modelling around droplet size and distribution,’ Davey says.
To test the effectiveness of the computer model, various full-height, part-width, mock-ups were built. As a result of modelling, they were able to illustrate that the waterfall would entrain a significant quantity of the surrounding air. The model showed that this mass of moving air would drag down hot air from high within the space, which would then be pushed out across the valley floor, making conditions uncomfortable for visitors.
It also showed the problem occurred at the point where falling water passes through the opening in the valley floor. Air, entrained by the falling vortex of water, was being dragged down into the acrylic cylinder at the waterfall base and colliding with the air being forced back out from the cylinder. As a consequence, the mass of entrained air was being driven horizontally across the main pedestrian plaza. ‘We found that the shape of the funnel was causing the air to come down and bounce back out again, to be forced out laterally at the top of the funnel,’ says Davey.
At the point where the waterfall passes through the valley floor, the architect has placed a disc-shaped reflection pool, intended to act as a barrier to prevent visitors from walking too close to the opening. The modelling showed that the addition of a simple glass balustrade around the perimeter of the reflecting pool was sufficient to prevent the lateral flow of air and keep the space comfortable. ‘Adding a glass balustrade meant the lateral flow of air was forced upwards,’ Davey says [see models above].
The inside track
In addition to the waterfall, another major challenge were the openings that allow trains to pass through the valley on an existing line to link terminals 1 and 3. There are two trains on the elevated track. They travel in opposite directions, but pass each other at speed at the mid-point of the forest valley, where there is a crossing loop.
Initially the plan was to encase the track in a glass tunnel. However, this approach was abandoned because of concerns that the tunnel would be impossible to keep clean. ‘The challenge we then had to overcome was how to keep the building operational with the tunnel removed,’ says Davey.
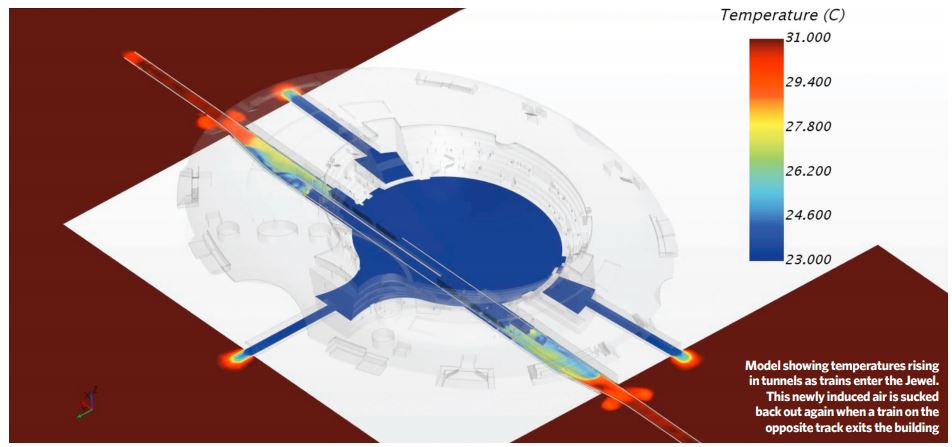
The challenge was to resolve how to seal the train entrance and exit portals to prevent conditioned air from inside the positively pressurised glazed torus escaping outside. One solution was what Davey describes as ‘a system of meaty air curtains’. This involved installing two air curtains at the entrance and exit portals. One air curtain would operate continuously under normal conditions and, when the wind speeds increased, a second high-powered air curtain – which Davey describes as like ‘an electric-powered jet engine’ – would kick into action. ‘They weren’t quiet is all I’ll say,’ laughs Davey.
A solution based on spring-loaded doors that would flip open the second the train bumped into them was also investigated, but this was abandoned after the train operator’s liability insurers refused to allow anything to touch the train. In the end, a system of fast-acting roller-doors, of the type used to allow forklift trucks to enter industrial refrigerated warehouses, was selected. To enter and exit the forest valley, the tracks pass through concrete tunnels. A roller door is located close to where the train enters and exits each tunnel, forming a rudimentary airlock.
The problem with this vestibule arrangement was that the roller-door mechanism did not work fast enough to cope with the speed of the train. ‘Basically, the inside door would begin to open before the outside one had fully closed,’ says Davey. The Building Construction Authority of Singapore – Singapore’s building control – was concerned about this arrangement, so the design team had to evaluate the volume of infiltration air, to prove it was relatively insignificant. ‘We were worried that, as the train drives into the building, you’d get a piston of air pushed ahead of the train and a vortex trailing behind it,’ says Davey.
Atelier Ten developed a means of modelling the air movement, but had to work with its CFD software suppliers, Siemens CD-adapco, to use its supercomputers, because the CFD model was so complex that their inhouse computers ‘did not have enough horsepower’, says Davey.
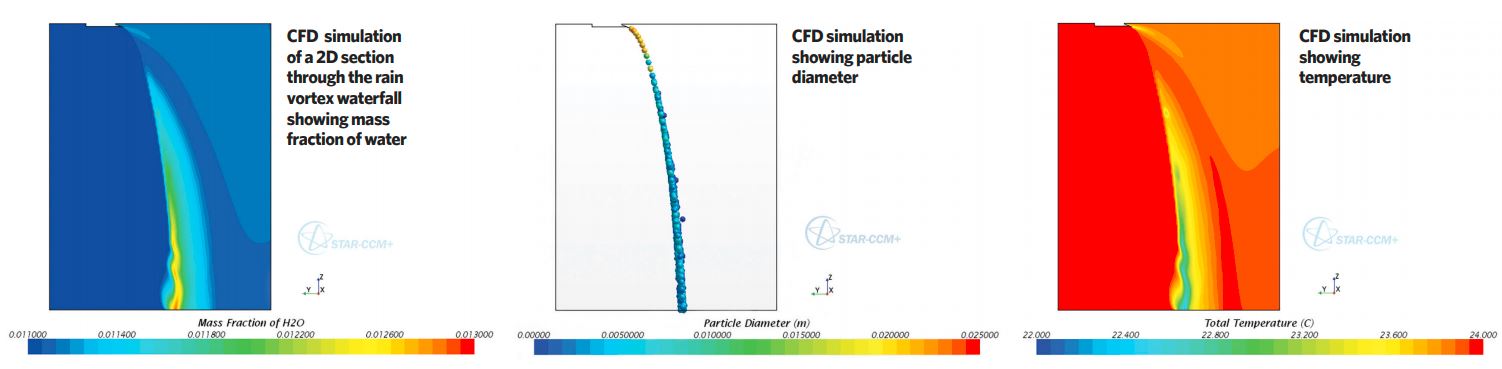
As a result of this complex modelling, they were able to show that having the trains pass each other inside the dome was advantageous. ‘What we found was that, as a train entered, we were getting some air bleeding into the space, mainly because of the vortex wake,’ explains Davey. Fortunately, as the second train left through the same set of doors, the model showed that it sucked most of the newly induced air back out again.
‘Because the trains pass each other in the building, each train acts to counter the airflow of the other,’ Davey says. The net result was a small amount of infiltration, which was easily dealt with by the displacement ventilation system.
The system modelling has clearly been effective. ‘A key objective was that people had to be comfortable inside this space for it to be successful,’ says Davey. The building has now been open for six months and has had more than 50 million visitors, which was the total number of visitors expected for an entire year. ‘It has been much more successful than had been anticipated,’ says Davey.