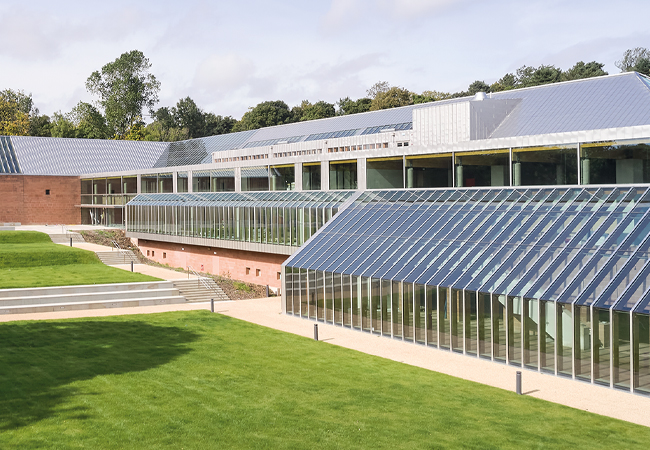
Credit: Hufton + Crow More than 3,120m2 of double glazing was removed and recycled during the refurbishment of the Burrell Collection
‘The greenest building is… one that is already built.’ This phrase, attributed to Carl Elefante, former president of the American Institute of Architects, may well be true for the newly refurbished Burrell Collection building, in Glasgow’s Pollok Country Park. Green, however, was not an epithet that could have been levelled at the Grade A-listed art gallery before its refurbishment.
Originally opened in 1983, as the new home for the art collection donated to Glasgow by shipping magnate Sir William Burrell, the building was suffering from a myriad of issues, the most significant of which was its failing envelope. Its faults were consistent with a building of its time: low levels of insulation; a leaking roof; poor airtightness; and high solar gains, from expanses of south-facing glass, putting a heavy strain on cooling systems. The faults were so bad, that the museum was no longer able to provide a suitable home for the art collection.
In 2016, Glasgow City Council appointed building services consultant Atelier Ten, architect John McAslan and Partners, and Arup Façades as part of £68.25m project to refurbish and improve the Burrell. ‘It was a fairly unsustainable museum to operate, in terms of cost and so on, and the building services were pretty much shot,’ says David Cameron, director at Atelier Ten. ‘Our brief was to revive the building to make it more sustainable from an economic, social and environmental perspective.’
Improving the envelope of the building was key to the success of the refurbishment. ‘We started by writing a brief for Alba, who went to site and did a thermographic survey, as well as general resistance tests, to determine the current fabric performance,’ says Cameron, who describes the findings as ‘disappointing’.
After we found out that the building couldn’t hold pressure, we got really paranoid and re-engineered the heating and cooling batteries to cope with a leakage figure of 15m–³·m–²
Tackling the problem was far from straightforward, however. The building’s listed status meant many fabric elements, such as the stone walls, could not be touched, so improvements had to be focused on the flat roof and the glazed façades. ‘We targeted significant improvements on these 1980s elements, to bring them up to current standards and a bit beyond,’ explains Cameron.
As part of the initial design development, the team did an airtightness test on the building – but it leaked air so badly that it was unable to hold sufficient pressure to provide the testers with a reading. The estimate was that the building’s leakage rate was ‘in excess of 20m-3·m-2·h-1@50Pa’, says Cameron. Pressure testing was applied to Class A as per DW 143, which is 500Pa positive pressurisation.
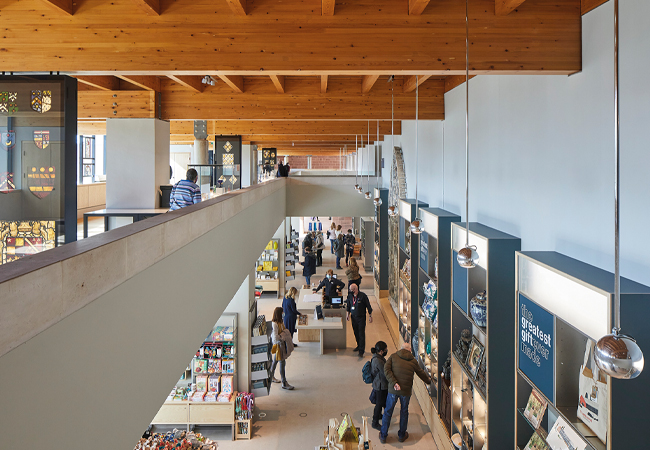
Improvements have reduced the building's peak heat load by about 50% and its cooling demand by at least 20%
This underscored the challenge facing Atelier Ten. Design conditions were 6°C, 100% relative humidity (RH) in winter, rising to 24°C, 100% RH in summer. ‘After we found out that the building couldn’t hold pressure, we got really paranoid and re-engineered the heating and cooling batteries to cope with a leakage figure of 15m-3·m-2·h-1@50Pa’ explains Cameron.
However, having built a contingency into the capacity of the heating and cooling plant to allow for excessive air ingress, the target air-leakage figure given to the main contractor, Kier Construction Scotland, was 5m-3·m-2·h-1@50Pa. ‘The figure they actually achieved was 5.3m-3·m-2·h-1@50Pa, which was a very impressive improvement,’ adds Cameron.
One reason for the dramatic improvement in airtightness was the specification and careful detailing of the new glazing, its aluminium frame and gasket system, developed by Arup. More than 3,120m2 of double glazing was removed from the site and recycled (see panel, ‘Arup implementing circular principles with glass recycling’).
ARUP implementing principles with glass recycling
Arup, the project’s façade consultant, found that elements of the original glazing due to be replaced could be reused for architectural glass production. As a result, more than 16 tonnes of glass was recovered for processing into new architectural glass, saving CO2 by eliminating the need to extract new material. Body-tinted, laminated and large-scale glass units that could not be recycled were ‘processed into other building products’ under a new glass industry network of manufacturers, research institutions and end-of-life/recycling facilities. Arup claims that no glass material removed from the building was sent to landfill.
More than 4.5km of glazing frames were also reused through what Arup describes as a ‘painstaking process’ of detailed inspection, structural calculation, cleaning, repair and strengthening of fixings to support the new high-performance glazing units. The frames’ refurbishment involved the addition of new thermal breaks and the use of a bespoke gasket system. The frames’ re-use reportedly saved 8.5 tonnes of aluminium.
The original glazing system was typical of its time, with a monolithic outer glass pane and a clear laminate internal pane, which, Cameron says, had an average U-value of about 3W·m-2·K-1. This was replaced with glazing with a U-value of 1.6W·m-2·K-1, which included the heat loss through the refurbished aluminium frames.
The flat roof was the other major fabric element targeted for improvement. Resistance tests showed its average U-value to be around 2.2-2.3W·m-2·K-1.
The old roof was removed, and replaced with a new, highly insulated construction, originally specified with PIR insulation, which gave a U-value of 0.18W·m-2·K-1. After the fire at Grenfell Tower, however, the PIR was ditched in favour of non-combustible mineral wool at the client’s request. This increased the roof’s U-value slightly, to 0.25W·m-2·K-1, which, Cameron points out, still delivers ‘an 80-odd per cent improvement’.
The new roof also supports 384 photovoltaic (PV) panels generating up to 140kW electricity. To make the most of these panels, a 250kWh battery is being installed so that electricity generated by the PVs can be stored when the building doesn’t need the energy. Electricity can also be taken from the Grid when tariffs are low and stored for use in charging the park’s electric buses.
The services solution
An all-air system, based on eight main air handling units (AHUs), is housed in a sub-basement in the middle of the building. This provides the bulk of the heating and cooling to the galleries and other spaces. Internal conditions in the galleries must be maintained between 20°C and 23°C and 40-60% RH to comply with the insurance requirements for the exhibits.
In total, the AHUs move between 60,000 and 80,000 litres of air a second. While they provide fresh air for the occupants, about 90% of the air is recirculated via an integral mixing box. At night, when the museum is unoccupied, the system is designed to operate on full recirculation.
‘Covid hit just when we had started to design the air handling system, which called into question the fact that we are recirculating air,’ says Cameron. ‘But if you don’t recirculate air, you might as well shut down the museum because its energy bills will be through the roof.’
Fresh air quantities are controlled by CO2 sensors. Because the building is relatively open plan, the AHUs mix fresh air into the recirculated air supply to all zones served by the unit.
A thermal wheel transfers heat and coolth from the exhaust air stream to temper the incoming fresh air. When cooling is required this is then cooled and dehumidified using chilled water supplied by two 300kW high-performance heat pump chillers, which recover heat from the cooling cycle. The outdoor air is then mixed with the recirculated air in the AHU and reheated as necessary by the primary heating coil. Primary coils run at a temperature of 60-40°C using the chiller-recovered heat. These figures are the flow and return temperatures, so the heating coils are sized to operate at 60°C flow and 40°C return generating a mean temp of 50°C. This means they are commensurate with future Heat Pump technology fit-out throughout.
‘If we need to boost the temperature further, the boilers can kick in; they can also boost to 80°C/60°C increasing the mean temp of the coils to 70°C. So far, that high temperature demand has never materialised,’ says Cameron. With all coils and heat emitters sized for 60-40°C, the infrastructure has been developed to allow for full heat pump changeover in the future.
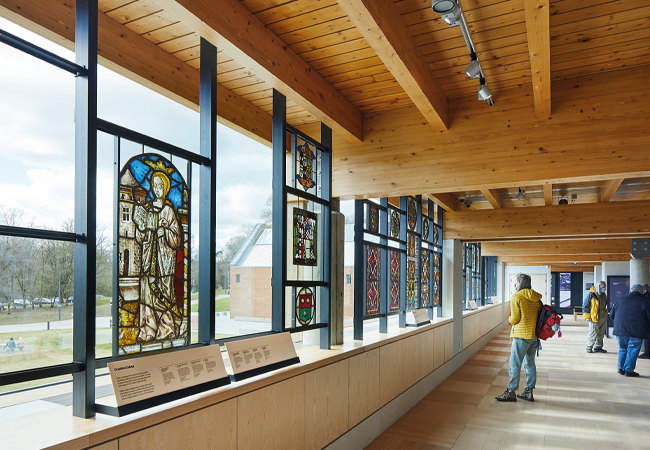
Atelier Ten will evaluate the museum's performance over the next three years
Unusually for a museum, the Burrell has a significant amount of south- and east-facing glass, plus an equally significant area of north-facing glazing. ‘I know this is in Scotland, but the southern and eastern glass gets bombarded with solar gain, while the northern element is constantly losing heat because it is not exposed to the sun,‘ explains Cameron. Atelier Ten’s solution is to use the heat-recovery chiller to move the passive solar heat from the southern galleries to provide heat for the colder northern galleries.
The building’s listing meant the engineers had to use the original distribution ductwork. Incredibly, 430 ducts leave the basement plantroom through the soffit, and are all concealed in the walls of the floor above.
‘We had no option but to reuse these ducts because we couldn’t demolish the entire internals of a listed building,’ says Cameron.
Atelier Ten’s concern was that the original ductwork would no longer be airtight. These concerns were realised when the ducts were pressure tested; most were found to leak, some by as much as 60%. ‘The reality is that, if we pump air into the duct, 60% of it would end up in the cavity, which was a real concern,‘ adds Cameron.
The solution was to use Hasman’s Aeroseal duct sealing system. This uses a fan to pressurise the ductwork, and an aerosolised sealant is then blown through it. The sealant particles attach to the edges of any hole, quickly and effectively closing it from inside the ductwork.
The heat-recovery chiller is used to move the passive solar heat from the southern galleries to provide heat for the colder northern galleries
The manufacturers claim gaps up to 25mm can be sealed and that the repair will withstand a pressure of up to 2,000Pa.
The system worked. According to Cameron, Reduced leakage to less than 5%. ‘It’s quite an expensive process, but it is guaranteed for 30-odd years, so, in effect, we’ve just given those ducts an extra 30 years’ life – and we’ve saved 30 tonnes of embodied carbon,‘ he says. The ducts are sealed into stone walls, replacing would require deconstruction of almost all interior walls. When compared to the cost of destroying the full interior and rebuilding, it was cheap.
The refurbished building reopened to the public in March 2022. It is estimated that the improvements have reduced the peak heat load by 50% and its cooling demand by at least 20%. Post-occupancy evaluation and optimisation of the building is being undertaken by Atelier Ten, working with Glasgow-based digital modelling and building physics specialist IES, over the next three years. The work involves the use of an IES-created digital twin, which is calibrated using actual data from more than 80 energy meters, all of which are linked to the digital building management system.
Initially, the building is being run with the gallery temperatures at a constant 21°C. ‘We’ve proved the system works well in winter and the conservation guys have given us a big thumbs-up for summer,’ says Cameron.
The next phase in the museum’s optimisation will involve letting temperatures freewheel slightly, to save energy. ‘We’ve got a meeting with the conservation and energy teams to look at the data and agree where they might let conditions flex a wee bit,’ Cameron adds.
Currently, two 750kW gas boilers provide full back-up and top-up heat for the AHU heater batteries and domestic hot water. Over time, Glasgow City Council hopes to provide the park and its buildings with some degree of energy independence by generating power and heat locally.
Working with IES, the wider Pollok Park Estate project has been commissioned by the council as part of its commitment to become net zero carbon by 2030. This includes options of turning the park’s historic water mill into a water turbine power station. If the council can pull this off, the Burrell Collection building really will be one of the greenest already built.
PROJECT TEAM
- Client: Glasgow Life
- Architect: John McAslan and Partners
- Building services, fire, environmental engineer and Breeam: Atelier Ten
- Civil and structural engineer: David Narro Associates
- Main contractor: Kier
- MEP contractor: FESx