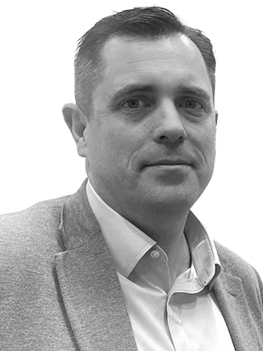
To reduce reliance on fossil fuels, the government plans to turn to hydrogen. This offers a good alternative to natural gas because it can be added to the current gas network and sent to our homes in the same way.
However, we do not currently have adequate infrastructure to accommodate hydrogen in the UK.
The extraction of hydrogen is a highly expensive process, making it difficult to sustain a national infrastructure. Additionally, the physical properties of hydrogen make it hard to store and transport. It is also highly volatile, which complicates its usage.
Moreover, there are two methods used to extract hydrogen: electrolysis (green hydrogen) or steam-methane reforming (blue hydrogen). Blue hydrogen is not made from renewable resources and, therefore, causes pollution. This is a huge issue because the majority of the global hydrogen supply is blue. So, while research and development is done to find more sustainable methods of harnessing green hydrogen, it is imperative to look to alternative sources of energy, such as air source heat pumps (ASHPs) in the interim.
Whitecode is at the forefront of integration of ASHPs after the effective ban on natural gas boilers in the Greater London Authority (GLA) region. Nevertheless, their integration is not straightforward. One client told me: ‘After 15 years, we have just got used to combined heat power, district heating and heat interface units, and now this. I can see it being a disaster.’
First, boiler rooms tend to be in basements, at ground level or in areas not suited to any other use. If you are lucky, the plantroom might have an external wall. Conversely, ASHPs must be located externally, on a roof or at the back of a building. However, this causes immediate conflict between building services engineers, architects and planners. We are now regularly seeing plantrooms on roofs, necessitating staircases and lifts to go up to these levels as well. Moreover, schemes have often grown in height as new applications or amended applications are introduced. In some cases, the plant on the roof is more than a storey high when acoustic attenuation is added.
The next problem is temperature. Heat pumps have a high flowrate and operate at low flow and return temperatures. This is particularly relevant to the application of heat pumps in residential buildings, where the hot-water demand means a second heat source is needed to raise the primary flow temperature so that instantaneous heat interface units can generate hot water at 50°C. Typically, this is achieved using a higher-temperature water-to-water heat pump, or electric boiler.
ASHPs must be located externally, on a roof or at the back of a building. However, this causes conflict
The biggest challenge we have faced is working within the confines of the building footprint. For example, a 10x10m plantroom could easily house 6mMW of gas boiler plant. For the equivalent output using an ASHP, you would probably require a space six times greater to fit the ASHP on a roof. We often find on larger schemes that the client expects the team to find space at ground level or lower levels, as the weight of ASHPs has structural implications, increasing the cost of implementation.
The lack of roof space and structural capacity often leads to solutions using ambient loops, much smaller external ASHPs and water-to-water heat pumps in the apartments. This solves the external planning problem, although the GLA did not approve of them initially.
Whitecode has found that the majority of its client base does not like these solutions because of their cost and size, as they fill the apartment service cupboard.
The second-biggest issue we have encountered with heat pumps is noise. Extracting heat from air generates a high level of noise, which creates a significant problem. In addition to the overheating requirements set out in Approved Document L, some councils have stated that the exterior plant must be 10dB below ambient noise. So, minimising noise is a priority.
Attempting to reduce noise output can lead to large amounts of attenuation and, in some cases, we have had no option but to move the plant because we cannot provide enough attenuation to reduce the noise adequately.
We have noticed that this is not as much of a problem in office buildings, as most sites already have a large rooftop louvre area for the cooling plant. This generally means we are able to increase existing plant areas rather than introduce new ones.
As a result, we often have roof plantrooms instead of conventional basement plantrooms. In addition, we are now supplying these sites with reversible chillers or chillers that can produce hot and cold water simultaneously, to minimise the pressures on space.
Electrical capacity is the biggest challenge relative to costs. The use of heat pumps shifts the demand from the gas network to the electrical network. The power consumption is minimised because of the ratio of the heat output to energy input of the heat pumps, but we still run into the problem of the extra load placing a strain on the network.
For example, a residential development with gas boilers would use around 1.5kWe per unit as a diversified load; with heat pumps, this could now be as high as 3-4kWe – and, with car charging, the peak load could exceed this.
The same applies to commercial developments. The 1MW of energy produced by a boiler could be replaced by a reversible chiller, but while the electrical demand for the site when being served by gas heating could be minimal, at least 350kW of additional electrical demand would be needed just for supplying pumps and ancillaries, which often requires network reinforcements.
One of our sites in West London has been advised that the electrical network will only be able to supply them with 1MW per year. The project has a total load of around 10MW, meaning their site now has a minimum 10-year build programme unless we find a solution. We are beginning to talk about battery banks to support the network, or generating our own power using generators until the Grid catches up. This raises more questions about sustainability and what fuel source would be used – oil or gas? These are real conversations we are having with our clients.
I wish that the price of ground source heat pumps was more accessible. At this point, the capital cost is a barrier unless the client is prepared to accept that the ground source solution will provide a long-term return.
With all the material cost increases, everyone is looking for the cheapest solution, but we should all consider heat pumps as the most efficient solution, even if they cost more to run.