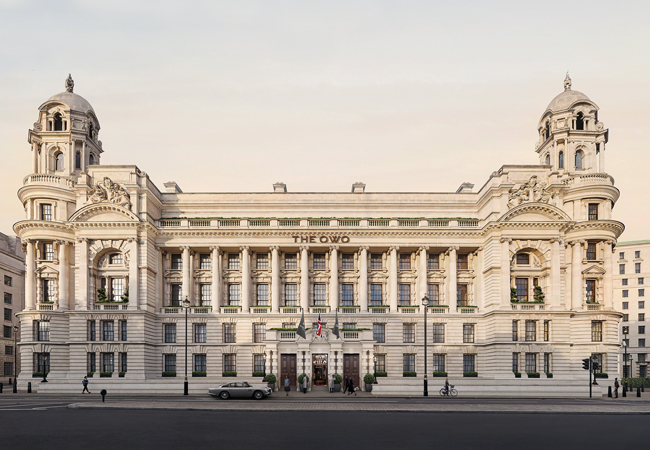
From seat of power to one of London’s most luxurious destinations, the Old War Office building in Whitehall, London, has undergone a monumental six-year transformation. The Grade II* architectural landmark, the corridors of which were once walked by Winston Churchill, will open its doors to the public this autumn, transformed into a flagship Raffles hotel. Known simply as The OWO, the hotel has 120 rooms and suites (known as keys in the hotel industry) and includes nine restaurants, three bars, and 85 Raffles-branded private residences.
Built in 1906, the listed building’s metamorphosis from government office to leisure destination has resulted in the already colossal, 1,000-room structure being extended by 31% with the addition of a three-storey rooftop extension. There are also four additional basement levels carved out below the Baroque-style edifice to house a spa, swimming pool, ballroom and kitchens.
It is the scale of the project, its location within the Whitehall conservation area, and the need to sensitively restore and preserve many of the building’s historic interiors that have made servicing the new hotel a herculean task. ‘It is all about coordination and trying to get services around the building without disturbing all of its beautiful features,’ says Anthony Hume, technical director and The OWO project manager for building services engineer Aecom.
The [BIM] model is ‘an absolute monster’, with more than one million elements, 400,000 of which are related to the mechanical and electrical services
Hume has been involved with the project since 2017, when Aecom was asked to look at the services in the former office building with a view to it being turned into a luxury hotel. ‘That was the easy bit; the scale of the project is so big it meant nothing could be reused, so the whole lot needed to be stripped out to enable us to start from scratch while respecting the listing,’ he says.
Aecom’s approach has been to service the building as a whole, with dedicated systems for each building – the hotel and high-end residences – where possible

Services had to be installed without disturbing the building’s beautiful features, such as this marble staircase
The hotel has the larger footprint. Its 120 guest rooms occupy Levels 1 to 6, while amenity spaces, restaurants and bars make up the ground floor, and the subterranean ballroom and its associated kitchen are at Basement Level 2.
In developing its servicing solution, Aecom was able to use a survey model created from digital scans of the building. The model was supplemented by digital general arrangement (GA) drawings with embedded photographs.
‘The entire building was catalogued in pictures, so you could click on a GA to reveal a photo of a particular element, which was really useful,’ Hume says.
Surprisingly, given the size of the building, finding enough space for all the plant needed to service a luxury hotel was a major challenge. ‘We knew what the hotel operator needed, so we had to work with EPR Architects to make sure there was enough space for us to deliver that,’ explains Hume.
Ultimately, the quest for sufficient space meant the planned new basement extension had to be dug deeper still to accommodate the building services.
‘There are six levels of basement; some were added purely to accommodate plant,’ Hume adds. Even with an enlarged basement, there was limited space for the air handling units (AHUs). ‘We have over 35 air handling units on this job, simply because we did not have the space to accommodate fewer, larger units,’ he says.
To aid cooperative working and coordination on this complex conversion, the entire project team worked in Autodesk Revit 3D building information modelling (BIM) software. Hume describes the BIM model as ‘an absolute monster’, with more than one million elements, 400,000 of which are related to the mechanical and electrical services.
‘What was fantastic was having this digital design tool combined with a building that already largely existed – so, if we were struggling to route a service digitally, we could get up and walk to the actual space, which was particularly useful when explaining to those new to the project.’
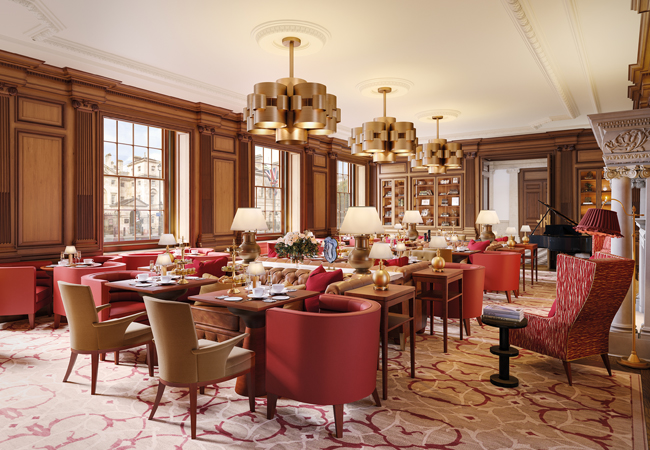
The OWO hotel includes nine restaurants and three bars
Even with digital scans, the engineer was still presented with some surprises. For example, when part of the ceiling was removed the team exposed a series of beams that had been added in World War II to provide enhanced protection to a particular area. The services had to be routed around the reinforcement.
Perhaps the biggest challenge was in getting the building services from the basement plant spaces to the hotel’s upper levels avoiding many of its listed rooms located on the ground floor. ‘This floor is full of double-height spaces with minimal ceiling voids and some major structural elements, so we made the decision at the outset to avoid using this space,’ says Hume.
Fortunately, Aecom was able to make use of what Hume calls ‘the moat’ – an existing subterranean corridor located at lower ground level that encircles the entire building, following the line of the façade. ‘Using the moat gave us the opportunity to circumvent the entire building to distribute the services,’ he explains.
Aecom used ‘the moat’ – an existing subterranean corridor at lower ground level that encircles the entire building, following the line of the façade
From the plantrooms on basement levels, services rise up to lower ground level, from where they are routed to the moat. From here, the various services follow the building’s perimeter until they reach the point on the plan closest to where they are required. From the moat, the services are routed up, through the ground floor, to Level 1, where a deep ceiling void provides the space for them to transfer from the building’s perimeter to the foot of a series of internal risers, concealed within the walls, that deliver the services to the upper floors.
For the guest rooms, services from the risers connect to fan coil units (FCUs) to provide heating and cooling. The building’s windows are designed to remain closed. This is partly because of noise, and partly for security reasons in rooms overlooking the royal procession route along Whitehall. Tempered fresh air is supplied to the FCUs from dedicated AHUs located on Level 1. This arrangement was more challenging in the largest guest suites that now occupy the former war rooms, which had listed wood-panelled walls. The panelling had to be carefully removed to enable the services to be installed. FCUs have been hidden behind the panelling, set into recesses carved into the walls. The only clue to their existence are period-style grilles subtly added to the panelling. ‘All you can see now is the grille, but the work to install these units was extensive,’ says Hume.
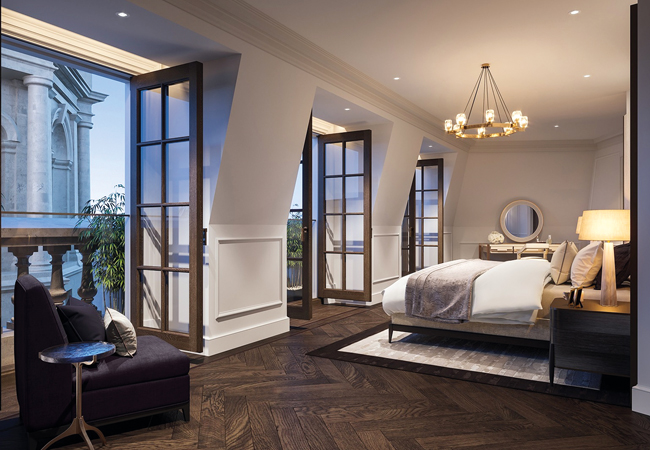
Windows in the guest rooms are designed to remain closed, partly because of security reasons
The chilled water circuit serving the FCUs circuit is pumped from multiple modules amounting to 3MW of cooling located on Level 6. ‘The condensers are the only plant allowed on the roof and they are in a sunken plant area to keep them hidden below parapet level,’ Hume explains.
Heating is provided by 4MWs of modular gas-fired boilers located at Basement Level 5. The boilers also supply heat to the hotel’s domestic hot water calorifiers, which are located on the same basement level. The boiler flues, however, terminate 11 floors up, when they reach roof level. ‘The flues are the only service in the entire building to have a completely straight riser,
from top to bottom,’ adds Hume.
The residential apartments have a similar servicing strategy to the hotel guest rooms. These are located in a separate wing of the building, surrounding a small courtyard, with a dedicated entrance and basement car parking. Engineers also had to design apartments for intermittent occupancy, as many residents were expected to be absent for large parts of the year.
Designing for absence
The challenge in servicing the apartments at The OWO is that they needed to be designed for intermittent occupancy, with many residents expected to be absent for large parts of the year. As such, each apartment has a dedicated mechanical ventilation unit with heat recovery to provide it with fresh air.
Even though the units generally draw in air from the apartment courtyard, all the intakes are fitted with a NOx filter to minimise nitrogen dioxide and particulates in the air supply.
As with the hotel guest rooms, heating and cooling to the apartments is via FCUs. However, the apartments have a dedicated heat interface unit to separate them from the landlord’s heating and cooling pipework.
This unit’s heat exchanger also provides instantaneous hot water to the apartment to avoid the need for water storage. Even so, both hot and cold water systems are connected to what Hume terms a ‘hygiene flushing box’. ‘This automatically flushes the systems if it detects that they have not been run for a set period, ensuring they are always safe and to prevent stagnation,’ he explains.
The project is finally nearing practical completion. Over its six-year duration, legislation changes and enhancements to the hotel operator’s brand standards have necessitated design changes and amendments. For example, Aecom added electric vehicle charging to the residents’ parking areas. ‘The rapid change in car charging requirements over the course of the project meant we needed to add chargers in midway through,’ says Hume.
When The OWO is open to guests and residents later this year, Aecom will still be involved: ‘We’re doing seasonal commissioning post-handover, so that we can adapt the systems as they are being used,’ says Hume. ‘We’ve done the theoretical design, but this allows us to work with the operator to tweak elements to reflect the way that the operator is actually using the building.’ Only then will Aecom be able to say the monumental building’s transformation is complete.