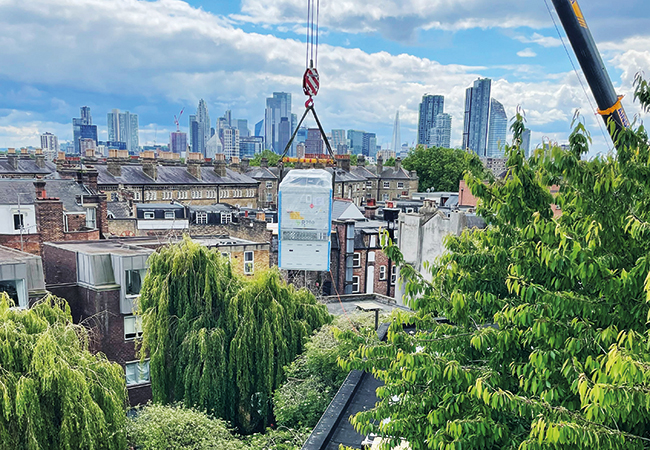
A large, louvred rectangular box is the latest addition to the garden of Greenpeace UK’s London HQ. Within the grey enclosure is the organisation’s smart new air source heat pump, which, despite its utilitarian appearance, is the key to the environmental non-governmental organisation’s latest initiative to end its reliance on gas to heat its offices and domestic hot water.
The heat pump is one in a series of steps taken by Greenpeace UK to cut the energy used servicing the 1920s former printworks that it calls home.
Its decarbonisation journey started in 2010, with a commitment to reduce the office’s CO2 emissions by 42% in 10 years. This undertaking resulted in the installation of photovoltaic panels on the roof of the office building and on Greenpeace’s adjacent warehouse and upgrades to the lighting systems, along with presence detection to improve control. The organisation also migrated its IT systems to the cloud to benefit from its improved efficiency.
In addition, the organisation undertook thermal imaging surveys of the building envelope. This led to the installation of additional draught-proofing, replacement of the external doors, and the renewal of some of the building’s glazing. A new building management system (BMS) was also installed to optimise operation of the building’s gas-fired heating and hot-water systems.
Despite the Covid pandemic, the organisation succeeded in meeting its initial 42% carbon-reduction target, albeit nine months later than planned. ‘The interventions did make a big dent in our carbon emissions,’ says Andrew Hatton, Greenpeace UK’s resource and technology director.
It was evident that the number one thing we could do from a CO2 reduction perspective was to come off gas
Having succeeded in stage one of its plan, which Hatton describes as tackling ‘the low-hanging fruit’, Greenpeace UK set about determining the next step in its carbon-reduction journey. ‘It was evident from crunching the numbers that the number one thing we could do, by quite a large margin from a CO2 reduction perspective, was to come off gas,’ Hatton says.
The organisation duly set about modelling the building to see if ditching its gas boilers was feasible. It worked with a third party and its own in-house energy analyst to model the building to understand its energy demands. Alongside the digital model, data from the BMS, installed a few years earlier, proved invaluable in showing the rate at which the brick-built building heats up and cools down.
Occupancy numbers were also factored into the modelling. This proved to be a tricky exercise in the midst of the pandemic. ‘Before Covid, we might have 180 to 200 people in the building, 30 of whom would be cyclists using the showers, but post-Covid – with hybrid working – we were not sure what the new working pattern would be,’ Hatton explains.
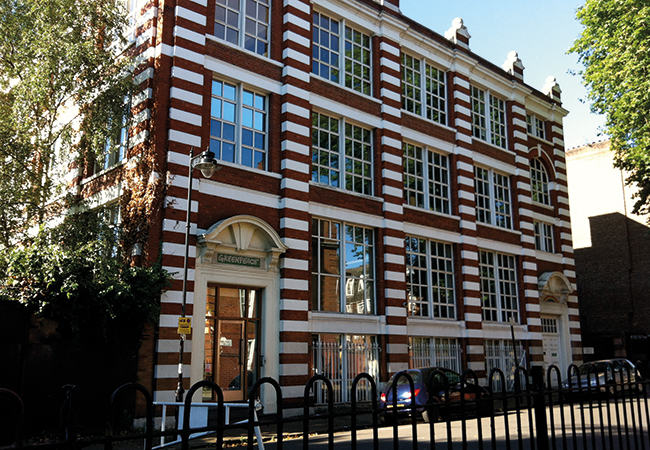
Greenpeace UK’s headquarters in London was the site of an old printworks
A ‘new normal’ of 60% occupancy was assumed to be a realistic scenario – a guesstimate that has subsequently been shown to be fairly realistic, with actual occupancy numbers fluctuating around this figure.
The modelling did prove that it was feasible to replace the building’s two commercial gas boilers with one or more electric heat pumps. ‘We needed a total heating capacity of about 80kW, so we set about exploring heat pump options and looking at where we could locate the unit, given the constraints of our site,’ says Hatton, who adds that he realises this particular solution was not the only way of doing things.
‘We could have spent hundreds of thousands of pounds on greater thermal insulation for the envelope so we could put in a lower-output heat pump, but the solution we opted for was the most appropriate and sensible at the time.’
Although keen to replace its ageing gas boilers, the NGO was equally keen to avoid a major retrofit of its existing low pressure hot water radiator heating system, given the additional costs and disruption this would cause.
Most radiators on the system were low-level, double-panel units, which, Hatton says, had been ‘performing well’ with the gas boiler system, which operated with a flow temperature of around 80oC. Knowing that a heat pump would run more efficiently at a lower flow temperature, Greenpeace UK experimented with running the existing gas boilers at a lower system temperature during the winter, to understand the impact on the office spaces and to garner occupant feedback. ‘Thermal comfort of staff was our top priority, because we didn’t want them saying “great, you’ve reduced emissions from the building but now my office is too cold for me to work”.’
The exercise proved that the existing radiator system could be used, albeit with a slightly reduced flow temperature of 65oC, which Hatton says is still high, compared to most ASHP systems’.
Greenpeace UK was also concerned about the choice of refrigerant for the heat pump. Its policy team had been involved in campaigns to raise awareness of the global warming potential of refrigerants, so the organisation was keen to be seen to walk the talk.
‘It was a steep learning curve,’ recalls Hatton. ‘We started to look seriously at R290 [propane], which is a natural non F-gas refrigerant and has a low global warming potential [GWP 3] compared with fluorocarbon-based refrigerants.’
The challenge of using propane as a refrigerant
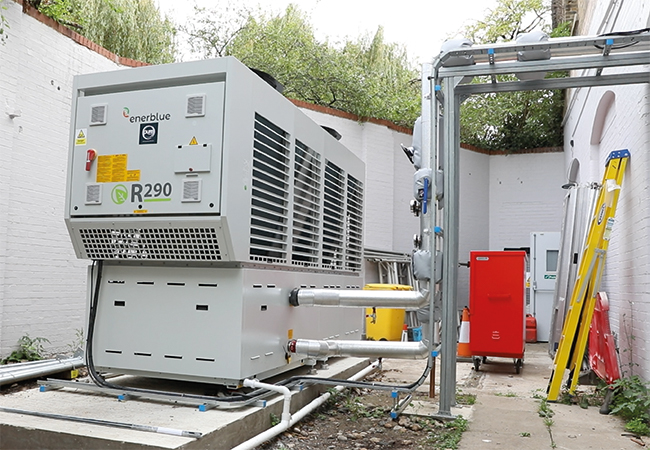
Greenpeace UK’s headquarters in London was the site of an old printworks
The heat pump contains 9.6kg of R290, which is about 50% more propane than is contained in the gas cylinder used by most domestic gas barbecues and patio heaters.
The heat pump installation has to comply with the Dangerous Substances and Explosive Atmospheres Regulations (DSEAR), the rules that apply to all refrigerant installations, albeit with a higher level of diligence because of this being an A3-class refrigerant.
Broadbent says the Palladium unit doesn’t present an ATEX (explosive atmospheres) risk during operation because it has built-in leak detection, automatic shut-off and, importantly, forced airflow. In addition, before the unit is enabled to start, integrated fans draw air through it to ensure a high-volume flow through the compressor housing, to effectively purge the unit.
The unit will only operate once it senses an air-pressure differential. In addition to meeting DSEAR demands, a 1.5m Zone 2 area is required around the heat pump, to prevent any uncontrolled access and remove any flammability risk.
DSEAR is, effectively, a risk-assessment process. In the case of A3 refrigerants, it is particularly important in ensuring that issues of non-compliance do not emerge at the end of the job. Broadbent says it is good advice to have a DSEAR review carried out at the start of the design stages, to pick up on any obvious issues before the unit position is finalised.
At the same time as it was researching refrigerants, the organisation was talking to the London Borough of Islington’s planning department, to discuss potential placement of the heat pump. ‘It became clear that noise from the unit was something we were going to have to consider seriously, given our location in a moderately built-up residential neighbourhood,’ Hatton explains.
‘We ended up in a situation where we knew we needed a low-noise unit; we knew we needed a natural refrigerant with a low GWP; and we knew we needed an air source heat pump, or heat pumps, that would deliver 80kW.’
It was at this point that Greenpeace UK approached Pure Thermal.
‘We’d just launched our Palladium range of air source heat pumps, which were a nailed on fit for the site because they are R290 units with ultra-low noise operation,’ recalls Garry Broadbent, Pure Thermal’s operations director. ‘It’s not always practical to use R290, because it has a maximum output temperature of 70oC, but it was perfectly suited to this application, which runs at a maximum of 65oC.’
Peace garden
The heat pump was to be located externally, in a courtyard area of the garden behind the office building. A Palladium 120.4 model, optimised for R290, was selected. Manufactured by Italian propane specialists Enerblue, it has a seasonal coefficient of performance of 3.58 and is capable of delivering up to 80kW of heat at an outside air temperature of -5oC.
The unit is also ultra-quiet, with a sound power level of 73dBA. This is the standard specification, without any secondary acoustic measures, which is very relevant where a challenging location such as this is considered.
The unit features twin refrigeration circuits, with each circuit served by two scroll-compressors to provide operational resilience. Having four compressors also ensures efficient load management, by enabling the unit to progressively bring each compressor online only when load demands. Importantly, its twin circuit configuration enables one refrigeration circuit to remain in operation while the other is operating in defrost mode, removing ice from the unit’s coils. This means that the flow temperature remains neutral through the defrost cycle without reducing in temperature, as would be the case without this unique Enerblue defrost feature. In a further eco-friendly touch, the defrost melt-water is collected and used to irrigate the Greenpeace garden, rather than being dumped down the drain.
To maximise its operational efficiency, the heat pump is load compensated. This ensures it operates at the lowest system temperature possible to deliver the required space heating for the building.
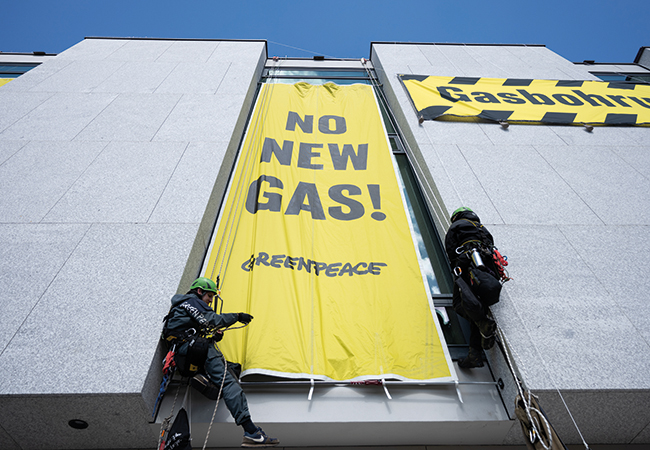
The system will run at 65oC when it is -5oC outside, but it will decrease to 50oC when the outside temperature is, say, 8oC. The BMS dictates the system temperature that the heat pump needs to deliver; if space temperature is not being maintained, the BMS will signal to increase or lower the system temperature.
Of course, the big challenge in retrofitting an electric heat pump to a system previously served by gas boilers is in raising the output temperature to a point where it is able to heat the building’s domestic hot water (DHW). Broadbent notes that heat pumps should provide hot water on an ‘accumulated, rather than instantaneous’ basis, to minimise the specified heat pump capacity.
To accumulate hot water, the Greenpeace UK system incorporates two insulated 2,000-litre hot-water storage vessels, which the heat pump maintains at a temperature of between 55oC and 60oC. ‘The rationale for this application is for the hot-water tanks to recharge after the cyclists have had their morning showers and demand drops significantly,’ Broadbent explains.
When the hot-water tanks need heat, valves switch to divert the system flow and the heat pump will switch from the load-compensated space heating temperature to DHW heating mode, and increase the system temperature to 65oC so that the hot-water tanks can then accumulate heat.
Having four compressors enables the unit to progressively bring each one online only when load demands
As soon as the thermal stores are up to temperature, the heat pump will return to heating mode and drop the system temperature again. ‘To increase system operational efficiency, the system is load compensated with prioritised hot-water production,’ says Broadbent. ‘For 95% of the time, it has the ability to run at a lower temperature than is required to heat the hot water, which means that the temperature of the double-panel rads will be well below 65oC a lot of the time.’
The hot-water tanks were installed, along with the heat pump, by contractor VWG Mechanical. The retrofit took approximately six months to complete, including the heat pump lead time, with the heat pump commissioned in August 2024.
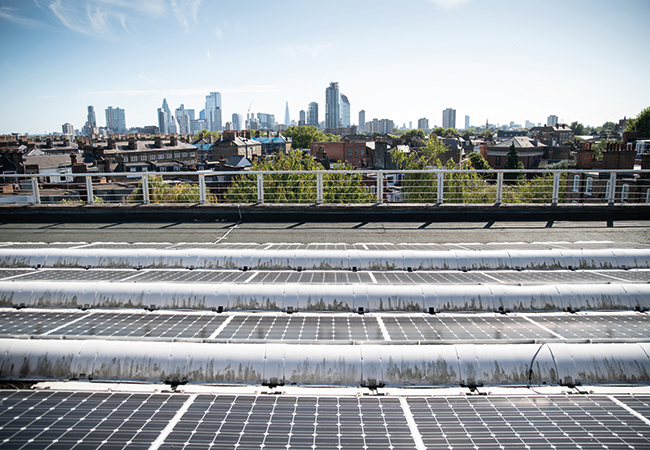
Photovoltaic panels have been fitted to the roof of Greenpeace UK’s headquarters and an adjacent warehouse
Hatton says that, now the system is operational, Greenpeace UK is monitoring and managing it carefully to ensure the system runs as optimally as possible, but it is still ‘too new’ to report any carbon savings. ‘We did some initial modelling based on desktop research, which showed that the carbon savings should be substantial,’ he adds.
While the carbon savings are potentially significant, will the switch from gas to electric heat come at a cost premium? ‘Unfortunately, at the moment, the answer to that question is yes,’ Hatton says, although he expects that to change in the years ahead when gas and electricity costs become more balanced.
‘The heat pump will cost broadly about the same to run – maybe a tiny bit more – than the gas boilers; we’re not saving money at the moment, but I would expect that to change over the next five years.’
As Greenpeace UK becomes familiar with its new heat pump, Hatton says it might focus operation of the unit to those times when the Grid has the lowest carbon intensity. ‘At the moment, we are not doing anything around that because we’re not experienced – and because of the tariffs we are on currently.’
Now that the unit is up and running in the Greenpeace UK garden, it is much quieter than Hatton had expected. Perhaps more unexpectedly, he describes the grey box ‘as having a certain charm’ and says that his colleagues want it to be seen. ‘It’s doing such a noble job, we are going to leave it on display for all to see.’