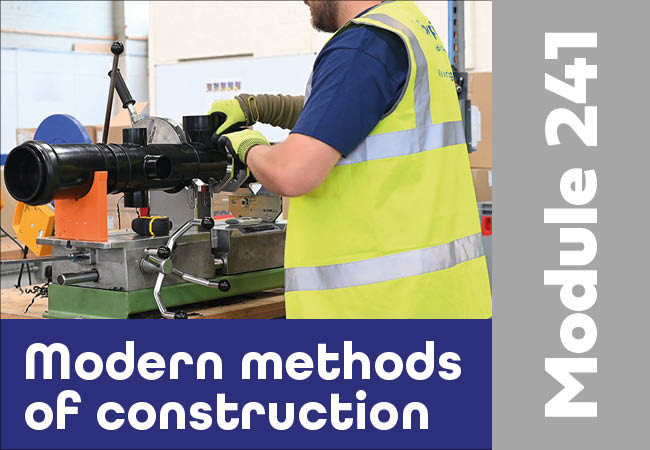
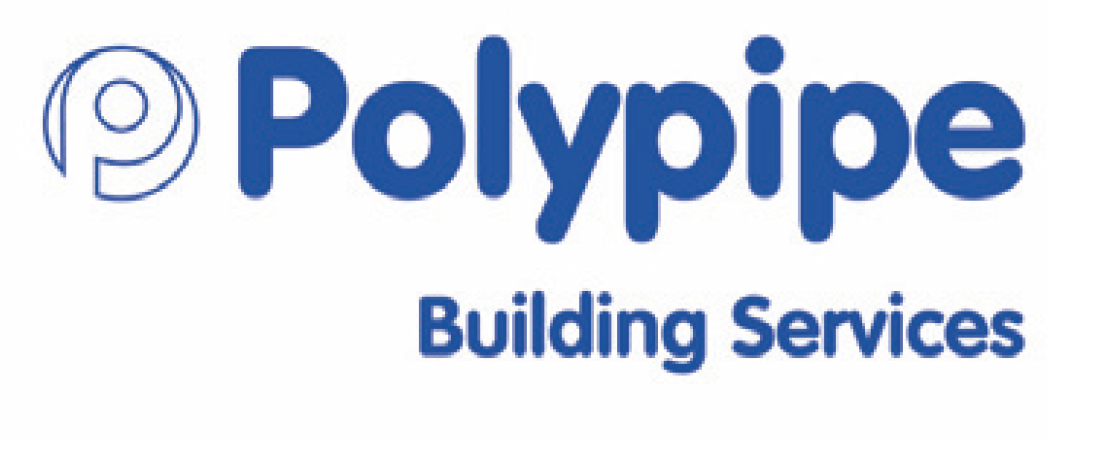
Design for manufacture and assembly (DfMA) has been applied across various sectors, including automotive, aerospace, and consumer products. More recently, disciplines associated with the built environment have embraced this approach to add value to their offerings.
DfMA can have – and, for some, is already having – a transformative impact on building services engineering by focusing on efficiency, quality and collaboration in the design, fabrication and installation of mechanical, electrical and plumbing (MEP) systems. This CPD article will explore aspects that underpin the concept of DfMA, and consider the benefits and challenges of increased application of modern methods of construction.
DfMA can be considered1 as involving a four-stage process to optimise product design for efficient manufacture and assembly:
- Functional analysis: ensures the design fulfills its purpose by examining components and identifying areas for simplification.
- Manufacturing analysis: evaluates design feasibility for manufacturing, considering factors such as materials, processes and complexity.
- Handling analysis: assesses ergonomic considerations for handling components during manufacturing and assembly.
- Assembly analysis: examines the assembly process, identifying redundant steps, intricate manipulations and potential bottlenecks.
This systematic approach optimises products for both function and manufacturability. This includes an array of applications, such as modular units delivering pre-assembled risers, waste systems, service pods, pumping and heating stations, and plantrooms. Such modules would typically incorporate ductwork, piping, wiring (power and control), and other systems, which are integrated into standardised frameworks.
These are designed to be manufactured, often offsite, in a controlled factory environment, and later installed as complete units. Components and systems would normally be designed with simplicity and optimisation in mind, to streamline both the process of offsite manufacturing (OSM) and the assembly on site. This can also encourage the use of standardised, readily available components to reduce complexity and manufacturing costs, such as with the prefabrication of the drainage stack illustrated in Figure 1.
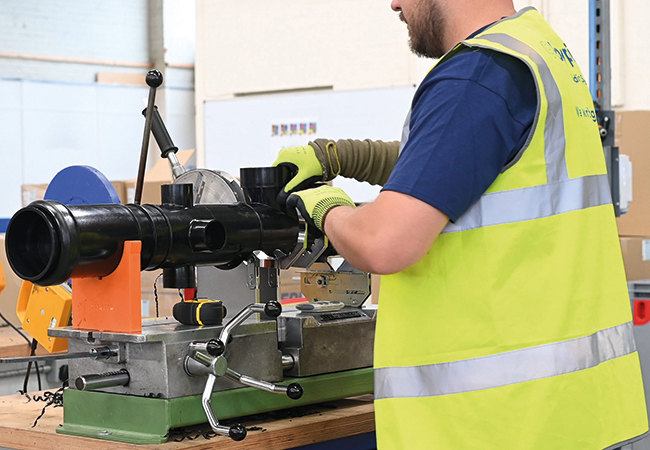
Figure 1: Offsite prefabrication of drainage systems in factory conditions allows for faster and more confident installation on site. Specialist fabricators and factory-controlled quality assurance systems (including pressure testing) ensure quality and reliability (Source: Polypipe Building Services)
Successful implementation of DfMA requires early involvement of contractors, subcontractors and suppliers in the design process, to ensure that the manufacturing and assembly of the components are feasible and deliverable. It can benefit from digital technologies, including building information modelling/models (BIM), and digital twins to facilitate design coordination and information sharing among project stakeholders.
Successful building services design requires close coordination between multiple teams, including mechanical, electrical, plumbing, structural and architectural specialists, who have knowledge and understanding of fabrication, installation and operation. DfMA fosters collaboration early in the design phase by encouraging interdisciplinary consideration of assembly constraints and factory fabrication methods.
This encourages smoother communication, more effective coordination and proactive problem-solving from the project’s inception.2 It also supports building systems designers to work more closely with manufacturers, to ensure components fit the overall design and construction plan. As DfMA focuses on simplifying assembly, systems are likely to be easier and quicker to install by reducing the number of individual components needed to be assembled on site.
DfMA is a key component of modern methods of construction (MMC), providing the design philosophy and methodology to facilitate the successful implementation of many MMC approaches. While MMC encompasses a range of innovative construction techniques, DfMA provides the framework for the efficient and effective realisation of MMC.
These principles and approach are particularly supportive of the MMC activity related to pre-manufacturing. The use of software systems (such as BIM) for design coordination, clash detection and logistics planning aligns with the principles of process-led site improvements.
BIM can be employed to enable more insightful planning of prefabrication and installation, ensuring that systems are optimised for offsite manufacturing and allowing potential issues to be addressed before construction begins. Essentially, DfMA provides the design foundation for a more efficient, streamlined and integrated construction process, which makes it a key aspect of the broader shift towards MMC.
This approach is particularly useful in projects with tight schedules, such as hospitals and data centres, where timely completion and compliance with design specifications are critical. The implementation of DfMA often leads to the creation of modular systems that have been proven to simplify fabrication, transportation, installation and maintenance,2 and reduces the opportunity for errors and defects, producing faster and more predictable project timelines.
MMC promotes standardisation and repeatability, allowing the development of standard systems and sub-systems for use across multiple projects. This is particularly useful in sectors such as housing or healthcare, where repeated designs are common.
One of the most compelling advantages of MMC is the ability to shift a large portion of the work off site, to controlled factory environments. This transition to offsite prefabrication allows for greater control over the quality of components and assemblies, as they are manufactured in a standardised manner, often using automated processes.3,4
Standardised designs can be prefabricated more efficiently, potentially reducing design time for individual projects. MMC reduces the need for multiple teams of specialists working on site, as much of the work is completed in a factory setting, which helps mitigate common issues such as weather delays, inefficient waste management, and unsafe working conditions.
The precision of factory-based manufacturing delivers a significant reduction in defects4 and reduces material waste, ultimately leading to a higher-quality final product. Through the more extensive planning process there is potential to integrate renewable energy sources, smart controls and other sustainable technologies into the systems.
Factory testing and quality control before systems are installed on site can further improve system performance and reduce the risk of defects. Processes can link the construction programme to BIM, enabling detailed cost measurement and analysis, and the creation of a library of construction materials relevant to MMC.5
By moving more of the work to a factory environment, engineers can design systems that can be assembled by fewer, highly trained workers. This reduces the demand for onsite labour teams and minimises the need for potentially dangerous activities associated with working in difficult site conditions, such as high-level installations or work in confined spaces.
It also reduces congestion and the number of trades working simultaneously on site, so improving overall site efficiency and safety. The opportunity to closely control material waste and reduce onsite emissions aligns with environmentally-conscious construction practices. By enabling parallel construction activities, MMC reduces the overall construction time.
While modules are being fabricated off site, other onsite tasks can proceed simultaneously, resulting in a faster project completion.2 Supply chain management becomes crucial in MMC, as prefabricated components need to be delivered on time and integrated smoothly into the overall construction schedule.
Digital technologies, particularly BIM, play a crucial role in amplifying the benefits of MMC in MEP. BIM facilitates the creation of comprehensive 3D models that aid in clash detection, optimise MEP routing, and generate highly accurate fabrication drawings. The seamless transfer of this digital information to the manufacturing facility further enhances the overall accuracy and efficiency of the construction process.
An MMC framework6 developed by the UK government’s former Department for Levelling Up, Housing and Communities (DLUHC; now the Ministry of Housing, Communities and Local Government) outlines seven distinct categories of MMC:
- 3D primary structural system: This category focuses on volumetric construction, where three-dimensional units, often entire rooms or modules, are manufactured off site and then assembled on site. This approach is particularly well suited to projects with repetitive layouts, such as hotels, student housing, and some residential buildings.
- 2D primary structural systems: This category involves the offsite manufacture of two-dimensional elements, such as walls, floors and roof panels, which are then assembled on site to form the building’s structure. This category encompasses various materials and systems, including timber frame, light-gauge steel and precast concrete panels.
- Non-systemised structural components: This category focuses on individual load-bearing elements that are pre-manufactured off site and then incorporated into the building’s structure on site.
- Additive manufacturing: Although not yet widely used in construction, this category includes innovative techniques such as 3D printing, where building components or even entire structures are created layer by layer on site.
- Non-structural assemblies and sub-assemblies: This category encompasses pre-manufactured elements that are not part of the building’s primary structure, but contribute to its overall functionality. Examples include prefabricated bathroom pods, kitchen units, utility cupboards and pre-assembled MEP modules.
- Product-led site improvements: This category focuses on using traditional building materials in innovative ways to improve onsite productivity. This can include using pre-sized or pre-cut materials or employing components designed for faster and easier installation.
- Process-led site improvements: This category encompasses innovations in onsite processes and technologies that enhance construction efficiency, productivity and safety. Examples include the use of BIM for site logistics and coordination, digital site verification tools, robotics, drones, and worker augmentation technologies.
While the seven categories provide a valuable framework for understanding MMC, a recent collaborative research report7 introduces an additional category, referred to as category ‘0’: Precondition: design, standardisation, and digitisation. This category emphasises the crucial role of design thinking, standardisation of components, and digital tools in enabling the successful implementation of MMC.
It highlights that MMC is not merely about offsite manufacturing, but also about a holistic approach that integrates design, manufacturing and onsite assembly processes. However, this proposed category could blur the division between the scopes of DfMA and MMC.
The DLUHC framework is primarily geared towards residential construction. However, the principles and benefits of MMC are applicable across various sectors, including healthcare, education, commercial, and even infrastructure.7 There has been a ‘significant increase’ in completed modular housing projects around London that may reflect the framework’s success.4
Developers and contractors are recognising the benefits of these techniques and are increasingly incorporating them into their projects. There has been greater collaboration between industry stakeholders, which is essential for the successful implementation of MMC, which has led to the formation of new partnerships and alliances.7 Increased investment in MMC-related technologies and businesses indicates a growing confidence in the potential of MMC to transform the construction sector.4
It is important to note, however, that the adoption of OSM is still in its early stages and there are challenges to overcome. The perceived barriers largely stem from concerns around cost, logistics and industry readiness. High initial investments in technology, manufacturing facilities and specialised equipment can deter companies, despite the long-term cost savings.
Design flexibility is often seen as limited with OSM, especially for complex projects, which can make it less appealing. Additionally, logistical challenges – such as transporting large, prefabricated components to urban or remote sites – can add to the complexity.
A skills gap within the workforce is another hurdle, as OSM requires proficiency in digital tools, manufacturing processes and system integration – areas in which many construction professionals lack experience. Regulatory and planning processes are often not well suited to offsite methods, causing delays and uncertainty in compliance. The construction industry’s fragmented supply chain can further impact the efficiency of OSM projects, with issues around coordination and reliability.
Culturally, the industry has been slow to embrace OSM because of its conservative nature, and there are concerns over the quality and long-term performance of prefabricated solutions. This resistance is compounded by a perception of risk, as OSM depends heavily on precise coordination, and any disruption can lead to costly delays. Finally, securing finance can be challenging, as lenders are often cautious about its viability compared with traditional methods.
Nonetheless, DfMA, MMC and OSM can deliver significant benefits to building services engineering. A recent report by the UK parliament’s Science and Technology Committee calls for greater adoption of OSM in the construction sector.
It highlights the benefits that are encompassed by DfMA, including improved quality, faster construction times and reduced waste – as, for example, delivered by the drainage stacks in Figure 2. However, the report also confirms the barriers to wider adoption, such as skills gaps, lack of collaboration, and financing challenges.
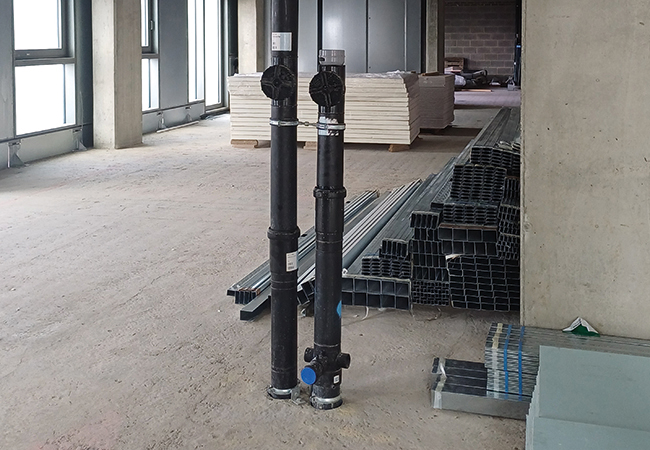
Figure 2: Scheduled deliveries of standardised prefabricated components reduces the need for onsite storage, while also reducing the time and cost of installation for these drainage stacks. Waste on site is virtually eliminated. Such systems are designed for easy adaptation to most domestic drainage applications in high-rise developments (Source: Polypipe Building Services)
To address these challenges, the report recommends that the government support skills development, promote best practices, and create a favourable funding environment for OSM. It also highlights that collaboration among industry stakeholders is crucial, as is the use of digital tools such as BIM.
By implementing these recommendations, the government can create an increasingly supportive environment for MMC, leading to a more efficient, sustainable and resilient construction industry. This could result in improved quality, faster construction times, reduced waste, and greater value for developers and consumers. Government support can readily reach beyond financial initiatives such as grants, tax incentives or subsidies, to mitigate the upfront costs associated with MMC.
By mandating the appropriate use of MMC for public projects – including schools, hospitals and social housing – the government could help ensure consistent demand for MMC, lessening concerns about the long-term stability of the sector, which is often hindered by irregular workloads and funding streams.
© Tim Dwyer 2024.
References:
- Design for manufacture and assembly (DfMA) Guideline: Version 1, Construction Innovation Hub, UKRI, 2022.
- Reference Materials – Adopting DfMA for MEP works, Aecom Asia Company Limited for HK CIC, 2021.
- Bao, Z et al, ‘Design for manufacture and assembly (DfMA) enablers for offsite interior design and construction’, Building Research and Information, 2021, bit.ly/CJNov24CPD31.
- Bayliss, S and Bergin, R, Modular housing handbook, RIBA Publishing, 2020.
- Jansen van Vuuren, T and Middleton, C, Methodology for quantifying the benefits of offsite construction, CIRIA 2020.
- Introducing the MMC definition framework, MHCLG Joint Industry Working Group on MMC, 2019, bit.ly/CJNov24CPD32 – accessed 30 September 2024.
- Ahmad Alrifai, A et al, Offsite construction – concept design and delivery, Buildoffsite/CIRIA 2023.