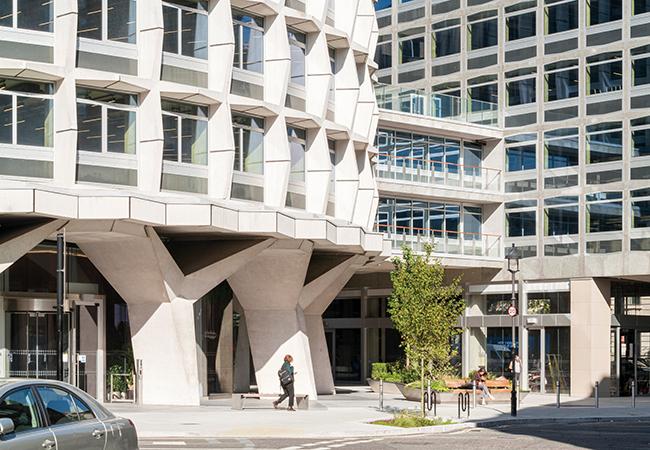
The regeneration of Space House – a 1960s, Grade II-listed, Brutalist architectural icon in London’s Covent Garden – as an office for the 21st century has pushed the boundaries of what is possible in an energy-efficient refurbishment of a historic building.
Completed in 1968, Space House was designed by architect Richard Seifert & Partners for developer Harry Hyams, the same team responsible for the 34-storey Centre Point tower, a few streets further west. The buildings’ shared heritage is evident in the geometric grid of their precast concrete structural façades.
While Centre Point has since been transformed into a residential block, Space House has been completely updated to turn it into a high-spec, energy-efficient, contemporary workspace, one of the first Breeam Outstanding listed buildings in the UK.
Its refurbishment has been quite a challenge, says Younha Rhee, technical director at building services engineers Atelier Ten. ‘The buildings’ listed façades meant we had to work within the existing envelope, which created spacial constraints in almost every area: the floor-to-ceiling heights on the office floors; the basement; the roof; and even the risers,’ she explains.
Project team
Developer: Seaforth Land
Investor: QuadReal
Main contractor: Bam Construction
Architect and principal designer: Squire & Partners
Breeam, sustainability, MEP: Atelier Ten
Structural engineer: Pell Frischmann
Project manager and cost consultant: Gardiner & Theobald
Atelier Ten’s involvement with the scheme started in 2019, when the project was at RIBA Stage 3 and architect Squire & Partners was already on board. Space House is actually two buildings: a distinctive, 17-storey round Tower and an adjacent, more conventional-looking, eight-storey rectangular Block. The two offices are linked by a common basement and by a two-level, enclosed walkway on levels 1 and 2. At the time the engineer was appointed, developer Seaforth Land had set a target of Breeam Excellent for its refurbishment.
Rhee says Atelier Ten was ‘confident’ it could push the mechanical, electrical and plumbing (MEP) design to achieve Breeam Outstanding within the confines of the buildings’ listed envelopes by exploiting the inherent qualities of the original design. ‘We developed our design to use what was already there, and to minimise any interventions, so as to retain the original architect’s intention in terms of how the building operates,’ she explains.
Both offices had a good base on which Atelier Ten could build: they had narrow floor plates, openable windows, and good levels of daylight. Their innovative hybrid structure of precast and in-situ concrete meant they also had high levels of thermal mass to help minimise peak cooling loads. This was exposed by removing the suspended ceilings installed by a previous tenant to reveal the concrete soffits on the office floors.
Removal of the suspended ceiling also helped the design team overcome the office’s very low floor-to-ceiling heights, which Rhee says was one of the most challenging aspects of the legacy scheme. Even with the soffits exposed, the floors’ lack of height precluded the use of fan coil units (FCUs) because there was insufficient depth beneath the structural beams to accommodate these. Undaunted, Atelier Ten developed a servicing solution that employed active chilled beams to provide heating, cooling and ventilation to the office floors, using ‘as fitted’ drawings retrieved from the archives.
The benefits of using chilled beams, says Rhee, are that they are more energy efficient than FCUs, ‘because the beams have a radiant component’, they provide better thermal comfort, and they are quieter. In addition, because they have fewer moving parts than an FCU they have a longer lifespan, which means they have ‘lower whole life embodied carbon’, adds Rhee.
Despite the two buildings’ different forms and heights, Atelier Ten has applied the same servicing strategy to both. This includes the ability to subdivide each office floor plate to enable two tenants to be accommodated per floor.
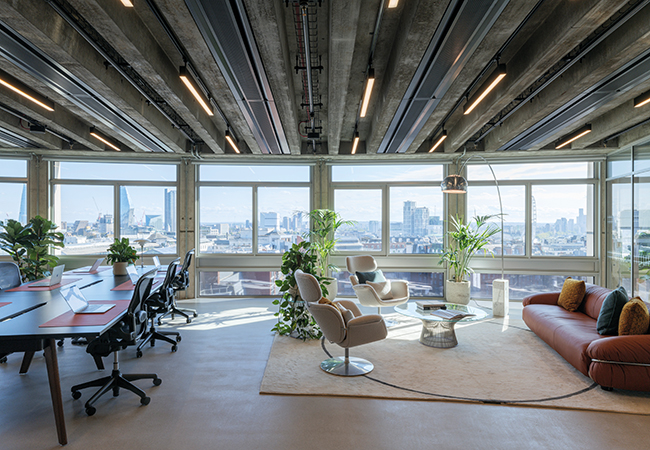
Bespoke trapezoidal-shaped chilled beams have been fitted within the recess formed by the structural beams
For the Block, which faces predominantly east-west, Atelier Ten was able to insert conventional rectangular chilled beams between its orthogonal structural grid to maintain floor-to-ceiling heights on the 960m2 floor plates.
For the circular Tower, however, bespoke trapezoidal-shaped chilled beams had to be manufactured. This was to ensure they would fit within the tapering recess formed by the structural beams that radiate – like spokes on a bicycle wheel – from the building’s concrete core to the cruciform precast concrete façade elements on each of the 960m2 circular floor plates.
The spokes help order the exposed building services on the column-free floor plates, with the chilled beams alternating every third recess with the track-mounted lighting and sprinklers, and containment.
The offices were originally heated by oil-fired boilers located in the basement plantroom. Under this all-electric scheme, the fossil-fuel boiler has gone, and in its place are four roof-mounted air source heat pumps (ASHPs) that provide heating and cooling to the chilled beams via pipework routed through the central core of the tower. ‘Removal of fossil fuels from site to make this an all-electric scheme was key to making our design sustainable,’ says Rhee.
The four ASHPs provide a total of 1,640kW of heating and 2,040kW of cooling. The chilled water is supplied at a temperature of 14°C flow, 17°C return, and heating is supplied at a temperature of45°C flow, 38°C return. ‘Because it is a concrete building and we could not introduce additional insulation to the listed façades, the heating demand is higher than it would be in a new building,’ explains Rhee.
Air handling units (AHUs) on the roof and in the basement supply fresh air to the chilled beams. The offices are designed for a relatively dense occupancy of one person per 8m2, which, Rhee says, was based on the British Council for Offices guide that was current at the time. She adds that, because this is a speculative office – and the tenants’ requirements were unknown – there is ‘some flexibility in the design in case we need to accommodate a trading floor’.
Extraction is from grilles in the building’s core. The supply air is dehumidified at the AHUs to prevent condensation on the chilled beams in the summer. There is also a dew-point sensor on the floor plate, which will close off the valves if condensation is detected.
The original intention was to control the volume of fresh air to the chilled beams to each floor zone using a variable air volume (VAV) box, to help minimise energy usage. However, there was insufficient space to install VAV boxes because of the limited floor-to-ceiling height, so fresh air is supplied to the chilled beams at a constant volume.
‘We can regulate the volume of air to each floor based on CO2, but there is no zonal control – so, unfortunately, the fresh air supply is at a constant air volume,’ Rhee explains. However, the impact of this decision is mitigated to a certain extent because the services to the chilled beams are intended to be turned off for around 30% of the year, to enable the floor plates to be naturally ventilated as part of a mixed-mode approach.
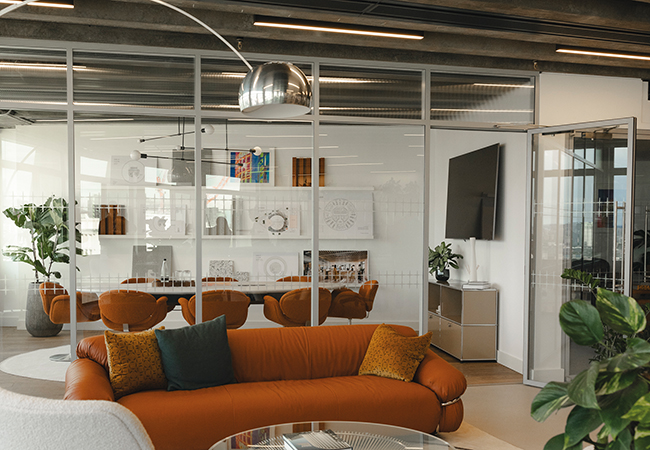
More than 90% of the existing structure of Space House was retained
The engineers were fortunate that the two blocks were originally designed to be naturally ventilated. The 39.5m-diameter Tower was built with opening windows on the perimeter of the floor plates. It also has a small lightwell in the central core, which acted as a chimney, drawing air from the perimeter and discharging it at roof level. Under the refurbishment, the lightwell has been infilled to accommodate additional toilets. Nevertheless, Rhee says the Tower’s circular shape will facilitate natural ventilation because ‘it doesn’t matter from which direction the wind is blowing’.
Natural ventilation of the rectangular Block was facilitated by its narrow, 16m-wide floor plates, which ensure adequate cross-ventilation.
Both buildings’ Grade II-listed status restricted fabric energy efficiency improvements to the replacement of the single-glazed, floor-to-ceiling windows with double-glazed units.
‘We wanted to improve the fabric performance as much as we could, but because of the listed nature of the building, and the risk of interstitial condensation, we could not add any insulation to the solid walls,’ explains Rhee, who adds that – as the glazing is approximately 80% of the wall area –replacing the single-glazed windows with energy efficient double-glazed units has made ‘a big improvement’.
The listed façades also prohibited the addition of external solar shading, although Rhee says the precast concrete façades provide ‘some shading’. Installation of internal blinds is at each tenant’s discretion, which means the glazing is designed to control both solar gains and heat losses. Atelier Ten provided the architect with the required g-value and u-values for the glazing specification.
To ensure the upgraded window units were a perfect fit, every opening was 3D-scanned to determine its dimensions. Every third window is fitted with an actuator, which will open and close the window under the control of the building management system (BMS), to optimise the buildings’ performance and use of natural ventilation.
The mixed-mode ventilation will run predominantly in spring and autumn. ‘There is a very sophisticated control strategy to optimise the building performance and thermal comfort criteria,’ explains Rhee, who says there was some concern about controlling the levels of humidity in the offices to prevent condensation on the chilled beams – ‘which is one of the reasons we had to automate the opening of the windows’.
The windows will also open automatically at night, under the control of the BMS, to enable night purge of the structure’s thermal mass to remove heat accumulated during the day, recharging it ready for the following day.
The basement of the Tower has been repurposed, as has the ground floor, which now features a restaurant. Two additional floors have been added to the Tower and one to the Block to create more space.
Obsolete space put to new use
At the base of the Tower, outmoded basement space has been put to new uses. Designed in an era when the car reigned supreme, the scheme originally incorporated two levels of car parking – and even its own mini petrol station.
All of this has now gone, with the original 200-space basement car park transformed into a versatile, double-height, 1,500m2 event space, shared by the two buildings.
The subterranean transformation includes the addition of 600 cycle spaces (accessed by one of the original car park ramps) and 62 showers.
Domestic hot water for the showers and toilets is provided by two water source heat pumps to step up the temperature of the heating hot water from 45°C to 60°C. The heated water is stored in calorifiers in the basement.
A similar transformation has taken place on the Tower’s ground floor, where a new public restaurant has been created above the spot in the basement where the petrol station was located. Appropriately called The Filling Station, it is connected to the main plant through heat interface units and cooling interface units for heating and cooling, and capped boosted cold water service and drainage.
The existing UPKN 33kVA sub-station was retained in its current position, but the vertical ventilation to the roof was removed. Atelier Ten added a new ventilation system, which now discharges at ground level.
The listed buildings have also been extended upwards, with two storeys added to the Tower and one to the Block. These are set back from the building’s listed façade; they were allowed by the planners ostensibly to conceal the rooftop plant while, at the same time, helping to maintain the building’s intended silhouette.
Atelier Ten’s initial proposals included photovoltaic (PV) arrays on the roofs of both buildings. As the design evolved, however, space for the array disappeared, much to the annoyance of the planners. ‘The air source heat pumps occupy most of the available roof area on the Tower, which prevented us from introducing PVs,’ explains Rhee. ‘We had to demonstrate to the planners why PVs could not be accommodated.’
On the lower-height Block, it was not space, but adjacent buildings that prevented the use of PVs, because ‘the roof was too heavily overshadowed to deliver the output that would make the installation economical’, says Rhee.
In operation, the building will be powered by 100% renewable energy from the Grid.
The building services design means operational carbon will be reduced by 46% in the new extensions, says Rhee, and by 70% across the existing elements of the scheme, compared with a notional Building Regulation-compliant building. It is an impressive achievement that shows it is possible to breathe new life into a 60-year-old Grade II-listed building.
Equally impressive is that remodelling the Brutalist icon has retained more than 90% of the existing structure, which has saved 10,700 tonnes of CO2 as embodied carbon – which, as Rhee points out is ‘comfortably below the LETI and RIBA 2030 targets’.