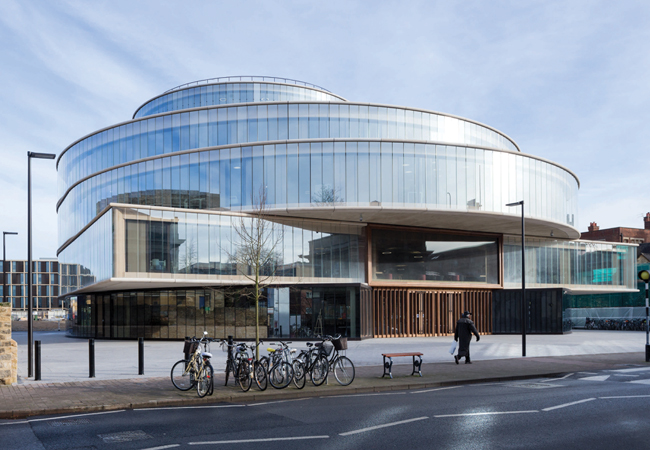
Credit: Iwan Baan
The Blavatnik School of Government is a visually striking building, situated in a prominent corner of the historic Radcliffe Observatory Quarter in central Oxford. The new £55m building, designed by Tate Modern architect Herzog & De Meuron, uses a naturally ventilated double-skin façade, mixed-mode ventilation and a ground source energy system, with on-site electricity generation by photovoltaic arrays. The mechanical, electrical and public health (MEP) engineers, Hoare Lea, have a hot-desk in the building, from where they now provide an aftercare service to help occupants and facilities management staff make the most of its sustainability features.
Project team
- Client: University of Oxford
- Architect: Herzog & De Meuron
- MEP engineer/acoustics/ daylighting/lighting/ sustainability and performance optimisation: Hoare Lea
- Structural engineer: Pell Frischmann
The building ensures a permanent home for the school, which was established in 2010 to improve, inform and support better public policy and government around the world . The architectural concept uses floor-to-ceiling glass as a metaphor for transparency in public life, and an open forum space with sweeping staircases to promote communication. The engineering solution needed to integrate with the high-quality finish and enable the architect’s vision for full-height glazing, while meeting the client’s brief for natural ventilation, an Energy Performance Certificate A rating and a comfortable internal environment through a range of current and predicted climate scenarios.
To make things even more challenging, a planning condition prevented heat-rejection plant from being installed on the roof, because of its prominence in the historical cityscape.
Thermal comfort strategy
The central forum, complete with glazed roof, extends from the basement to the fifth floor, and promotes a ‘stack effect’ for natural ventilation while admitting daylight into the centre of the building.
At the very top of the stack, buoyant exhaust air accumulates at ceiling level. The building management system (BMS) controls consider the internal and external air temperatures to determine the optimum exhaust-air strategy. In winter, this warm exhaust air is extracted by the air handling units (AHUs) for heat recovery, while, in summer, it is exhausted through motorised dampers, which double up as the airflow path for smoke extract fans.
The thermal comfort strategy employs night cooling, using the thermal mass of extensive, fair-faced concrete soffits and walls. However, the absence of ceiling voids and the high-quality finish resulted in very limited routes for high-level extract ductwork. So, working with the architect and contractor, Hoare Lea’s designers and acousticians developed exhaust-air paths consisting of bespoke, acoustically attenuated slot details. These allow airflow from individual rooms into circulation spaces, while maintaining acoustic privacy between rooms and corridors.
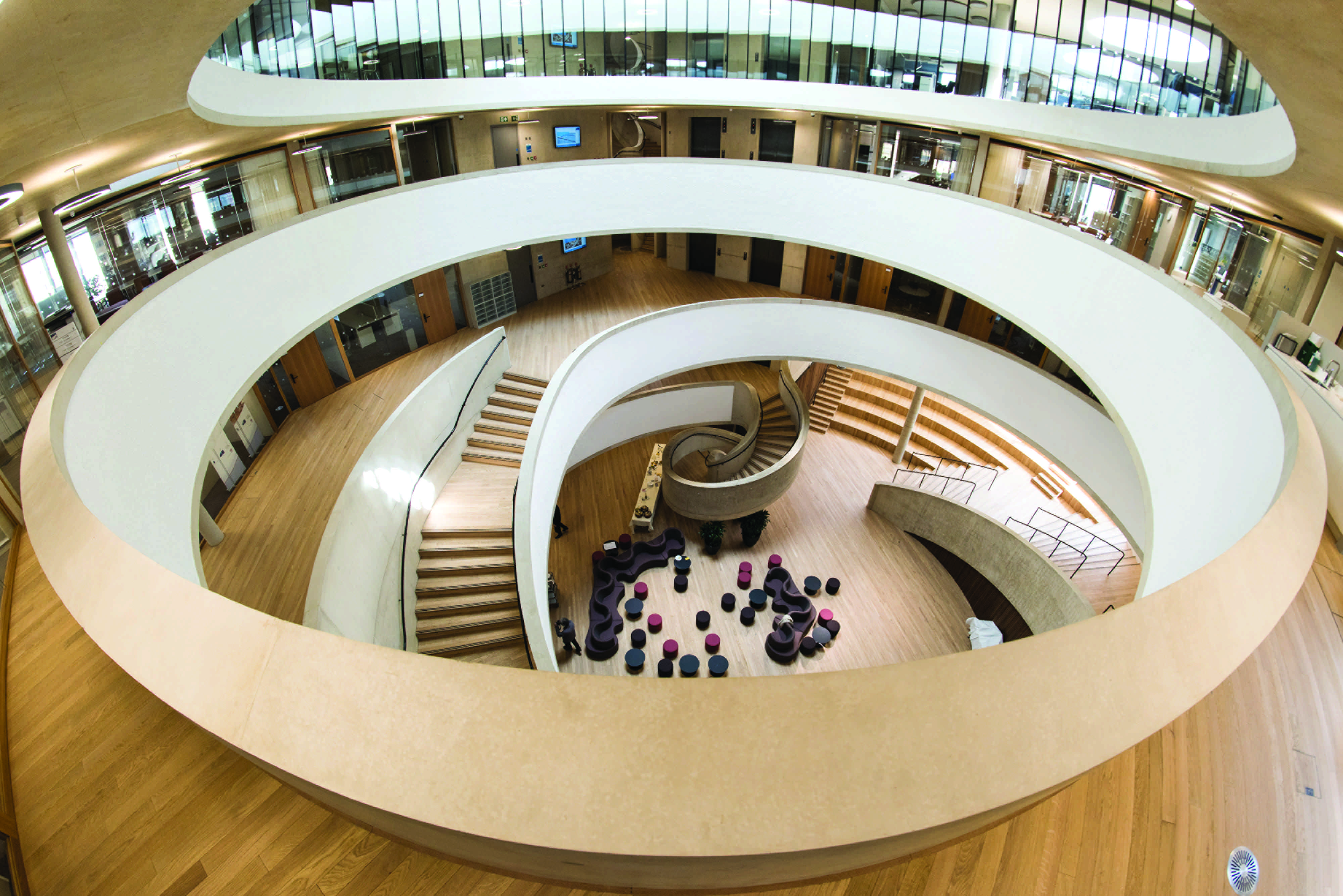
Atrium for stack ventilation. Credit: Will Yeong
The building envelope consists of a glazed double-skin façade with integral motorised blinds and natural ventilation panels. This façade harvests solar energy in winter by heating the air in the void, reducing the energy required to heat the building.
Overheating is mitigated by glazing coatings and external solar control blinds. These automatically deploy on a zone-by-zone basis, when the solar gain into a particular area of façade exceeds a set threshold.
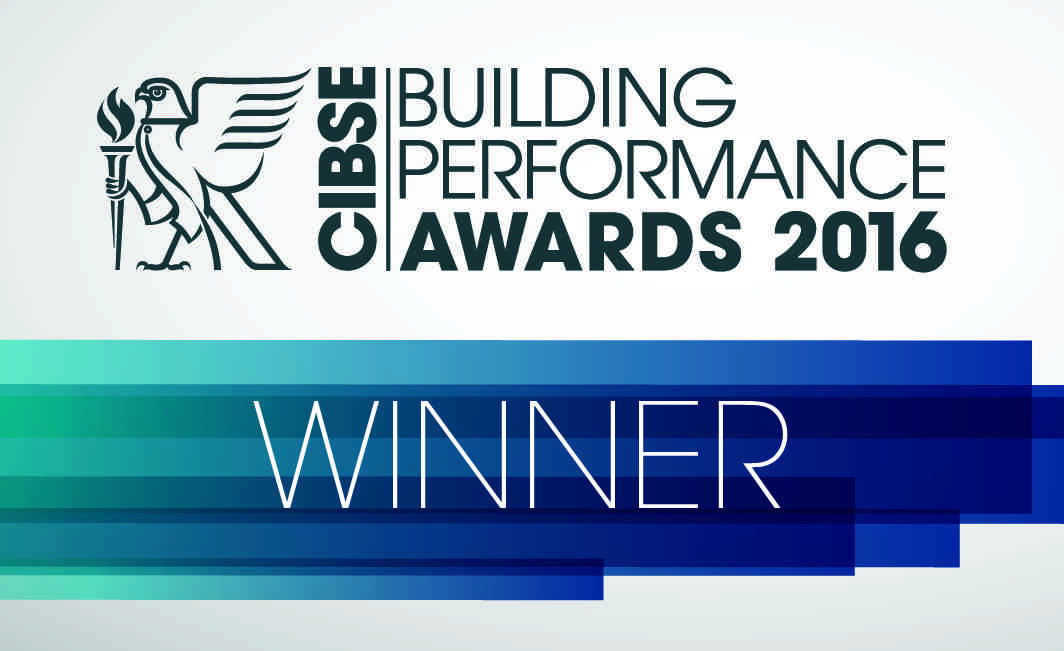
A ‘mixed mode’ ventilation strategy keeps the building cool in summer and prevents simultaneous heating and cooling. The bespoke natural-ventilation panels in the façade open outwards, like casement windows, into the annulus of the double-skin façade to provide a full-height opening. They were carefully designed, with acoustically absorbent internal insulation and a perforated inside face, to attenuate cross-talk between adjoining naturally ventilated rooms.
The mixed-mode strategy closes the natural ventilation panels and uses mechanical underfloor displacement ventilation for summer cooling, and for heat recovery during low outside air temperatures. The displacement ventilation is provided by a central variable air volume (VAV) system, supplied by four parallel AHUs in the basement, which connect into common header ducts.
The parallel AHUs are sequenced by the BMS to spread the load across as many units as possible, to reduce the internal pressure drop through the AHUs at part loads and reduce fan power consumption. To make further energy savings, the AHU fan inverter speeds are controlled on a variable volume, variable pressure strategy. This uses feedback from the VAV terminal unit actuator positions and determines when the air pressure set points in the supply and extract ducts can be reduced, and when they need to be increased to meet the VAV demands.
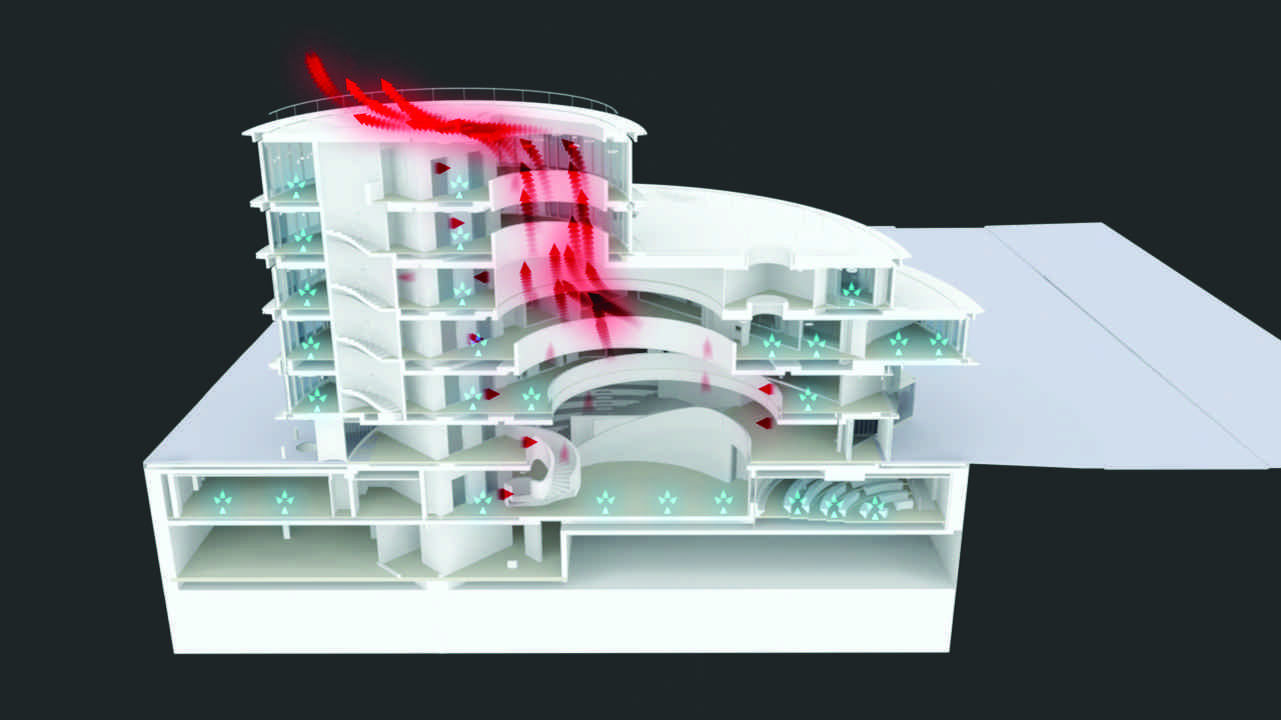
Warm stale air rises through natural buoyancy and is released through the atrium smoke vent
The post-handover monitoring to date has shown this variable pressure strategy typically halving the AHU pressures in relation to their maximum design pressures, resulting in a halving of AHU fan power.
In addition to the measures to reduce the mechanical heating and cooling loads, energy-in-use predictions were used in the design of a ground source energy system, which provides all of the building’s mechanical cooling and a significant proportion of its heating.
During early conversations with the client, it was agreed that the building should be resilient to future climactic variations, including a predicted Oxford 2040 design summer year.
Hoare Lea did extensive energy in-use thermal modelling, and ground source energy specialist GI Energy came in to carry out the ground loop design modelling. It became clear that the building cooling load over a hot summer would exceed the heat-rejection capacity of the ground under the building. The site boundary and foundations precluded a larger footprint for the borehole array, and the presence of the Oolite aquifer underneath Oxford limited the depth of the boreholes. Planning constraints on rooftop plant also precluded the use of external chillers. These factors left the designers highly constrained.
Cooling the ground loop
Their first concept used ducted chillers to supplement the ground source cooling during high fresh-air cooling loads, with the chillers rejecting heat into the exhaust air header duct of the main ventilation system. However, analysis of the predicted cooling load profile showed that this solution was unable to provide the full balance of cooling capacity in future climate scenarios. This was exacerbated by the use of variable air volume control on the main ventilation system, as the airflow would also have needed to be controlled to the dictates of the chiller condenser fans and the minimum run time on chiller compressors.
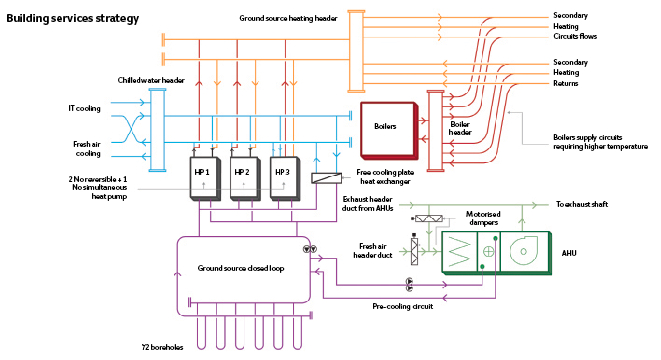
After exploring several options, the designers arrived upon a novel solution. A simple AHU was employed as a dry air cooler, to cool the ground loop. This solution ‘decoupled’ the supplementary heat rejection from the operation of the main ventilation system, so that they are not required to run at the same time. This extended the availability of heat rejection to 24 hours per day, and removed the need for a constant airflow to serve heat rejection. By allowing the ground loop to absorb heat during the day – when the main ventilation system requires cooling – then reject that heat into relatively cool air at night, the cooling capacity and energy efficiency were improved drastically.
The AHU has ducted connections into the mechanical ventilation exhaust and fresh air ducts, controlled by motorised shut-off dampers. An algorithm in the ground source supervisory controller calculates a comparative measure of heat-rejection capacity in the fresh air and exhaust header ducts, using sophisticated thermal dispersion airflow-rate and duct-temperature sensors. The algorithm then determines whether to open the AHU dry air cooler to the fresh air intake or exhaust air duct.
The ground source energy system also features a plate heat exchanger for passive cooling of the chilled water system when the ground loop is cool. This is anticipated to occur in winter, when the balance of energy flow is heat dominated, when there is a net flow of heat out of the ground, to produce a cooling effect on the ground loop water.
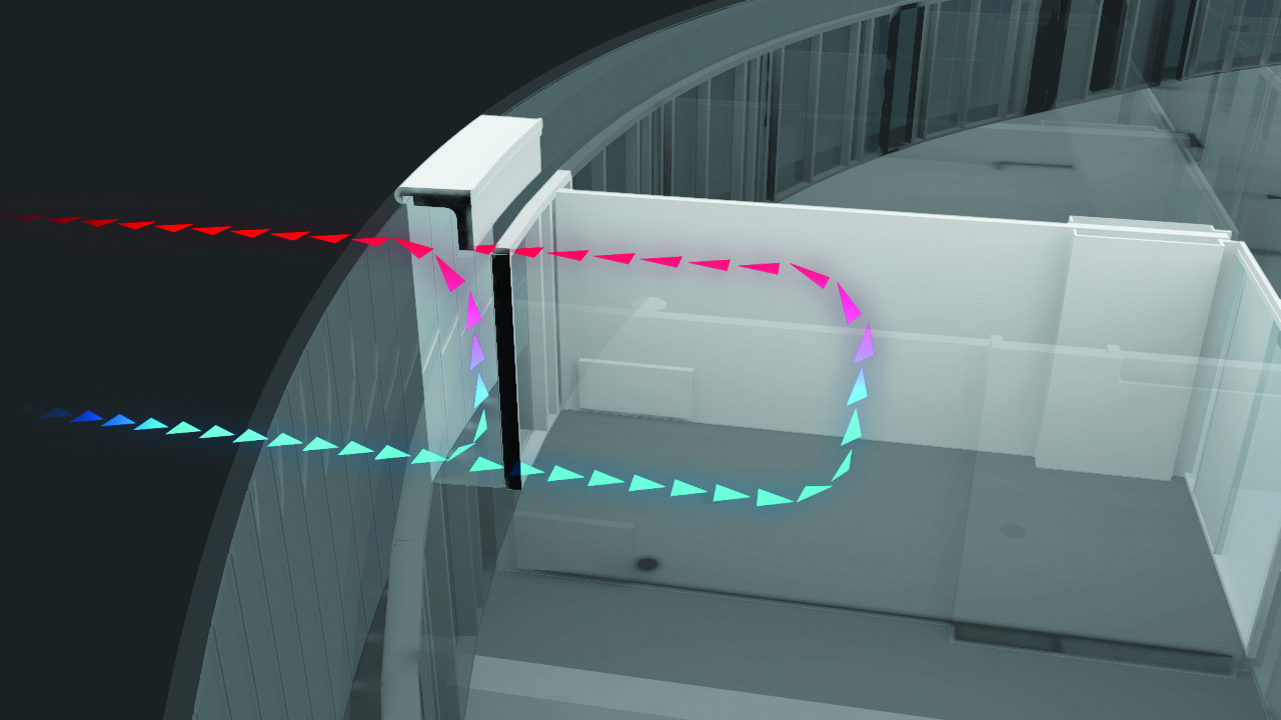
Mid-season :Perimeter rooms are naturally ventilated through automated slots in the double-skin façade
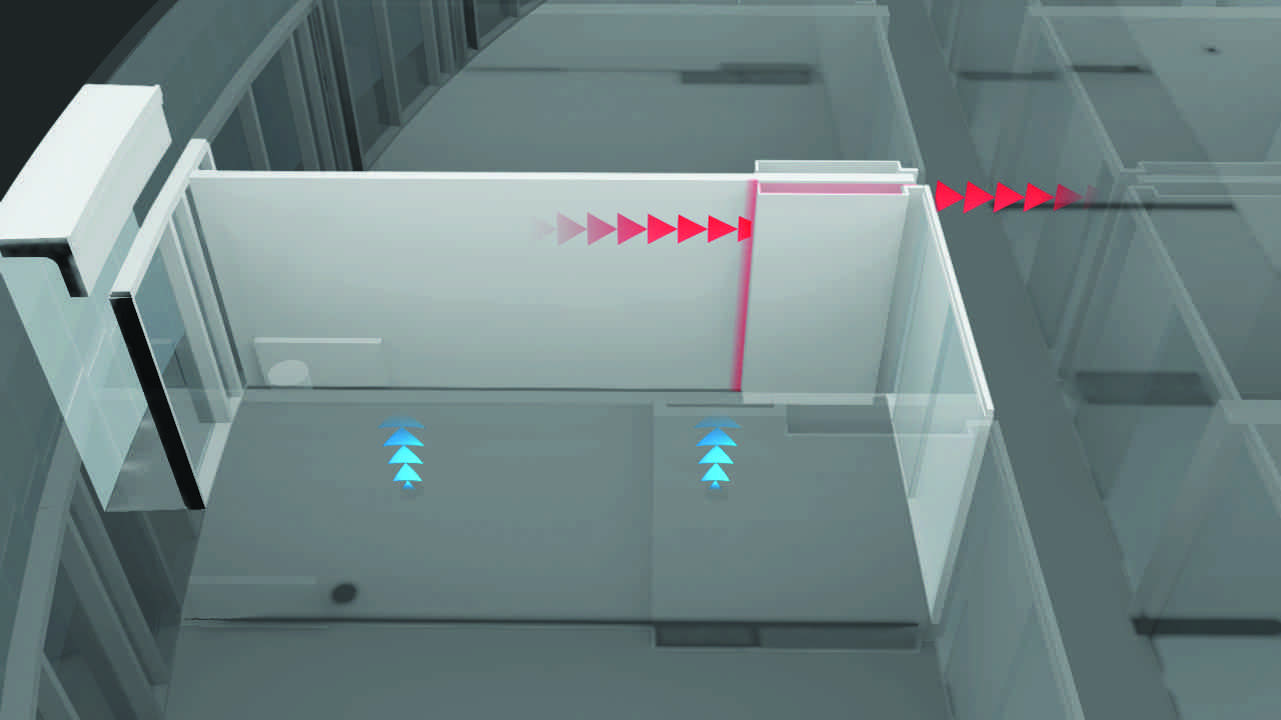
Winter/summer: Fresh air is supplied through the floor via displacement ventilation
A small simultaneous heat pump is sized to the year-round IT cooling base load – while rejecting heat into the heating system – to increase the global heating/cooling energy efficiency of the ground source system.
The building’s space heating is supplied by radiators on a compensated circuit, with underfloor heating in the forum, while fresh air heating and domestic hot water (DHW) pre-heat is provided by a constant temperature circuit with 45°C/35°C flow and return temperatures. Each secondary heating circuit is connected to both the boiler and ground source heating headers, with 3-port switch-over valves to select the appropriate heat source.
During mild weather, the compensated radiator circuit calculates a lower flow temperature demand and switches onto the ground source, and the boilers become a ‘backup’ heat source to each circuit. During cold outside conditions, the compensated radiator circuit calculates a higher flow temperature requirement and switches onto the boiler header. The constant temperature circuits remain connected to the ground source header and only use the boilers for backup, or for a short-term temperature boost on AHU start-up or DHW pasteurisation.
The ground source energy system can connect into a future site-wide ground source structure, which will allow different buildings to share capacity and recover heat.
Soft landings
The project is the culmination of the University of Oxford’s long-term commitment to delivering soft landings. Hoare Lea has paid particular attention to the commissioning and handover process, with user-engagement presentations, an interactive, electronic building user guide – based on CGI animations – staff training, and extensive testing of the building systems. The project is now regarded by the university’s Estates Services as the benchmark for all future building handovers.
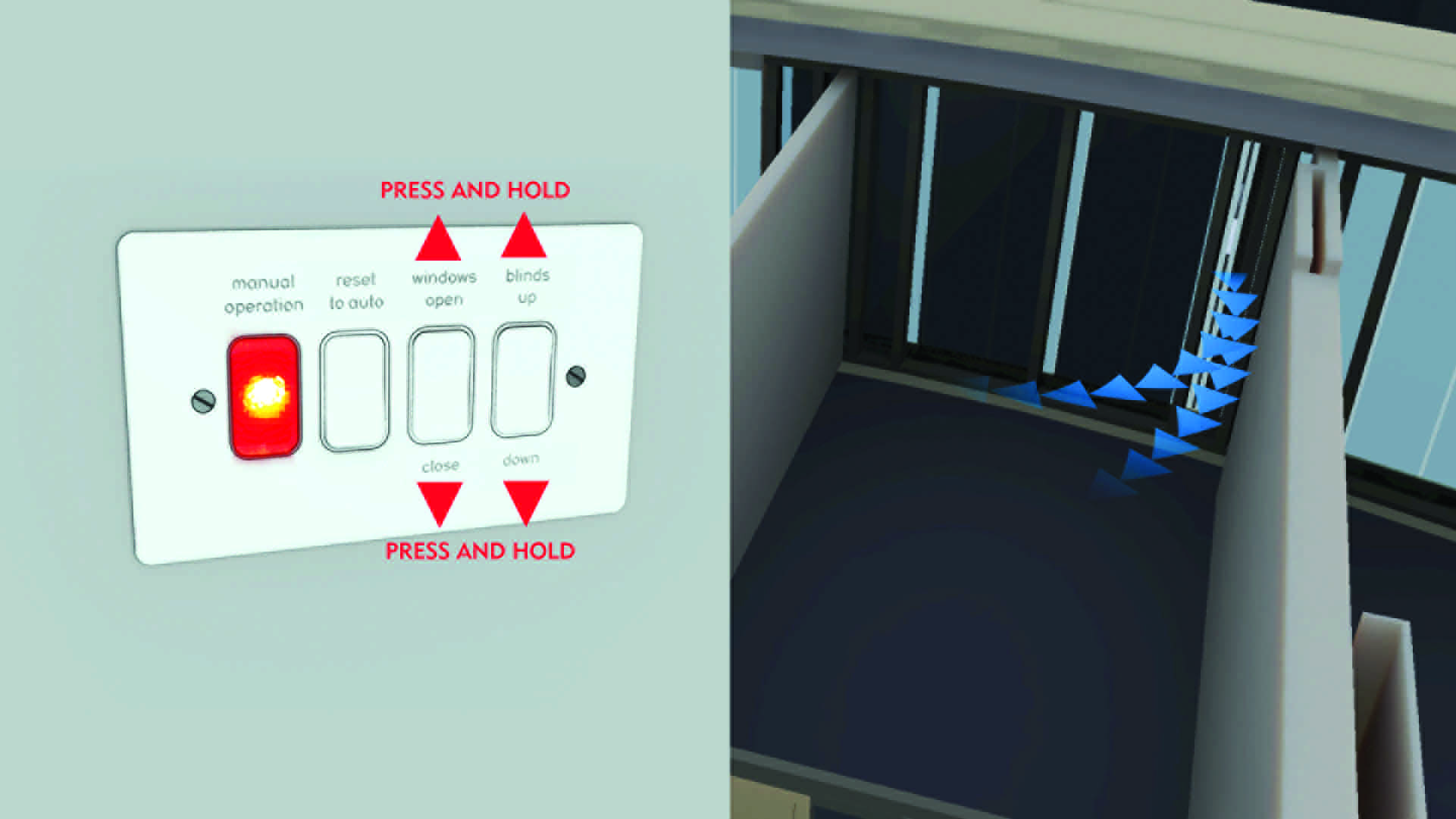
Using manual controls will disable automatic control, indicated on the control panel by the red light
From its hot desk in the business school, Hoare Lea experiences the building from a user’s perspective. This arrangement is anticipated to yield deeper insights into how occupants feel about their environment, and how this relates to the design and commissioning of the building systems. Hoare Lea will also hold ‘refresher’ sessions with the users to recap on building operation through different seasons.
Hoare Lea’s MEP, building performance and engineering visualisations teams have collaborated with the occupants and facilities managers to create an interactive building user guide hosted on the client’s FM intranet. This allows users to navigate a 3D virtual model of the building, and click on points of interest. Animated 3D videos help users become familiar with the control systems.
The team is currently undertaking an 18-month performance optimisation service after full occupation of the business school. This will help users make the most of the building’s environmental control systems and optimise energy efficiency in use.
During this period, Hoare Lea will recover data from the building management system and from the electric, heat, gas and water meters. It will then analyse this and compare it with the Energy In Use model that was developed for the building.
Hoare Lea will use this data analysis to identify opportunities for further energy savings, and then quantify the impact after the implementation of any changes. The learnings will be fed back into the design of future buildings.