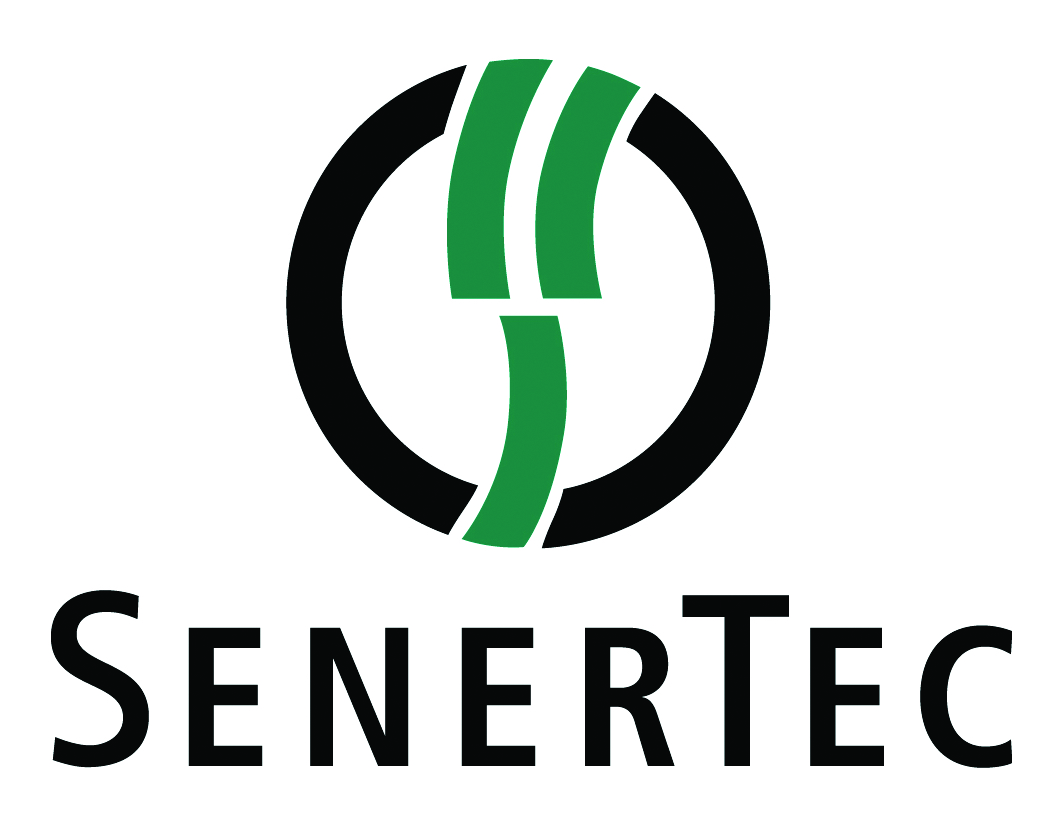
Much in this CPD will draw directly from a key reference for this area – CIBSE AM121 – to determine the requirements for a proper feasibility study for a modular CHP implementation. The focus will be on systems that are less than 50kWe output, typically known as ‘mini’ or ‘small-scale’ CHP.1
CHP compared with traditional systems
The benefit of applying local CHP is that it uses energy that would otherwise be wasted in centralised power stations (by rejecting heat to the atmosphere). CHP also avoids transmission and distribution losses that – for mature networks – will lose 7-8% of the power.2 Considering the primary fuels employed in centralised power generation, in the UK over the past year grid electricity was predominantly produced3 from gas (31% with a rising trend); nuclear (18%); coal (16% with a falling trend); and wind and solar (13% with a rising trend).
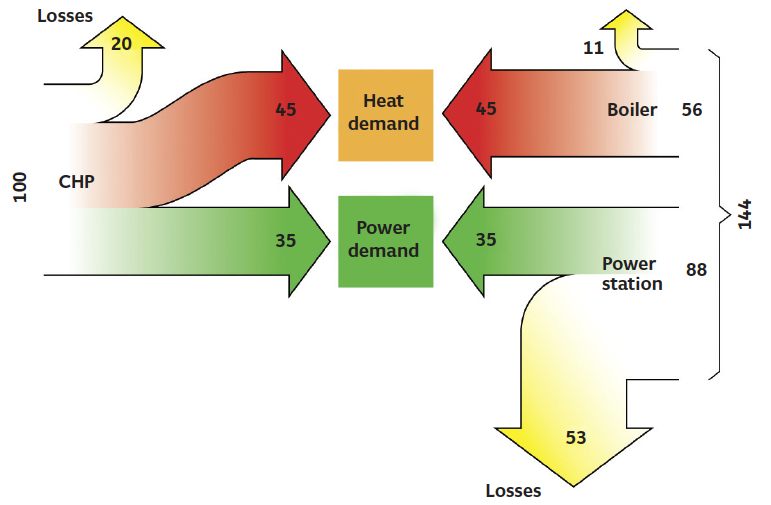
Figure 1: The basic case for CHP (Source: CIBSE AM12)
The efficiencies of centralised generating plants will also vary, but tend to be around 35% (other than solar/wind). With appropriate design of complementary electricity generation and heat recovery, overall efficiency in CHP plants can be in excess of 80%, and the generalised comparison, as shown in Figure 1, would be indicative of systems in the UK and Ireland. This CHP process can be applied to renewables, such as biomass and biogas, and to fossil fuels, including natural gas and LPG. CHP can use either turbines or engines, and each has specific applications, but spark-ignition gas engines are the predominant technology used for CHP in buildings.
Determining the feasibility of mini-CHP
A feasibility study will normally be required to determine whether it is worth investing in a CHP project, as capital costs will be significantly higher than for conventional systems. CHP schemes can be considered as a retrofit measure in an existing building or as part of a new construction. In both cases, the arguments for and against a CHP scheme will be compared with those for ‘conventional’ plant alternatives, such as condensing gas or biomass boilers, together with grid-supplied electricity.
Data gathering
A basic understanding of site energy demands is required to make any assessment of the viability of the CHP scheme. Some data will be readily available – typically, as quarterly or monthly fuel bills – whereas other data, such as daily or weekly energy profiles, may have to be developed or synthesised. When designing conventional power and heating systems, the capacity of the plant is determined largely by maximum demands, so the plant will operate at part load most of the time. High plant utilisation is required for CHP to be viable, so when selecting a CHP scheme, the minimum energy demands in the running period are as important as – and often more important than – the maximum demands. There are usually significant differences between winter and summer demands, and an understanding of these differences will be important in determining the capacity and expected running hours for the potential CHP system.
In an ideal case, data that identifies heat and power energy demands at hourly intervals throughout the year will be obtained from monitoring of electricity, heat or gas meters. Where this is the case, the route to CHP selection will be somewhat clearer. Using monthly data to assess loads available for a CHP scheme can be misleading and over-optimistic where there is significant variation in demand over a 24-hour period (for example, between day and night). Using monthly average profiles will tend to overestimate the potential operating hours from CHP during the ‘shoulder’ months (in the spring and autumn).
If there is insufficient discrimination or detail in the available data, specific energy surveys, temporary metering and audits may be required. If time is available, sample monitoring of meters on representative days (weekday and weekend, heat and power demand data) in each month would be beneficial; otherwise, days in late spring or early autumn should be selected. When converting from fuel use to heat demand, a pessimistic boiler efficiency level should be assumed.
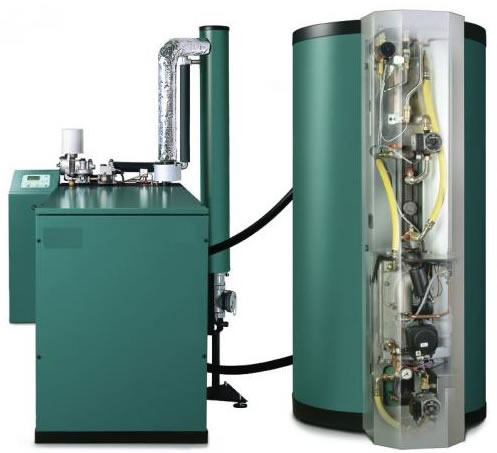
Figure 2: CHP unit with close-coupled thermal store (Source: SenerTec)
As well as taking into account existing energy consumption, consideration should also be given to future changes in consumption. These might be affected by the implementation of energy efficiency measures, the addition of new facilities, discontinuing old processes, or simply changes in operation, organisation or occupancy patterns. These aspects may be evaluated by undertaking sensitivity analyses of any calculations.
For new buildings, the heat and power demand profiles must be estimated. Such estimates may be based on: a combination of building design data; dynamic thermal simulation of the building; projected occupancy patterns; benchmark data from similar buildings; and empirical data from energy models or consumption codes for different buildings by type of use, floor area and volume. The confidence level attached to the demand profiles derived must be recognised when selecting a suitable CHP plant rating.
The CHP system assessment requires intelligence on how the energy is ultimately integrated into the building operation. For electricity, this could include: the supply and building system voltages; the system fault levels; switchgear arrangements; distribution layouts; and possible connection points.
The heat from the CHP is most effectively absorbed in systems with a near-constant demand throughout the year and with an operating temperature of 80°C or below. So it is important to ascertain the type of heating systems and loads (for example, heating or hot water) that are in use, together with their operating temperatures, the users, peak loads and load profiles, and the existing plant performance, age and condition.
Typically, modular CHP units would be self-monitored by their own stand-alone controls, which could be used with remote monitoring, and would be able to integrate into the building energy management system. Fuel options for most CHP plant are natural gas, LPG, gas oil, biogas and liquid biofuels. For the majority of mini-CHP installations, natural gas will be the fuel, as it can be supplied virtually on demand and requires no on-site storage facility. It will be necessary to establish the available capacity, metering and supply agreement details of any existing gas supply. However, if the gas is not immediately available, then the cost of providing a supply must be determined (which might be influenced by other potential systems that would also benefit from a gas supply). Where the supply condition is not adequate, a gas pressure booster may be required, and this will impact upon energy consumption, space and cost.
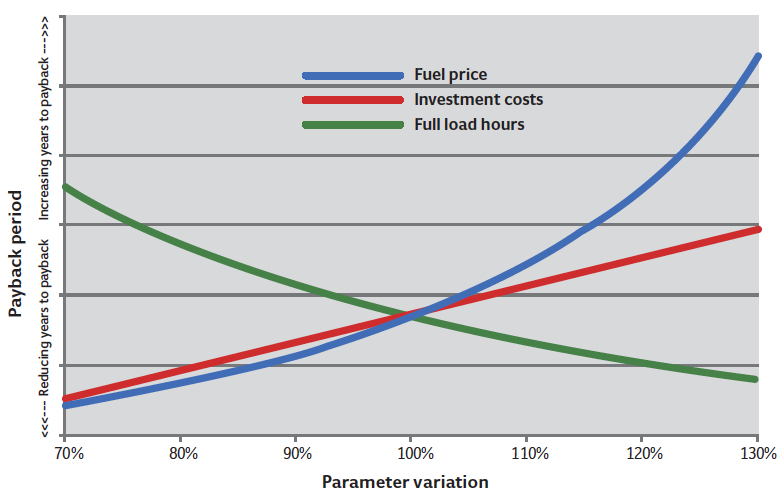
Figure 3: Examining the sensitivity of payback to other example parameters
As it is not possible to match heat and power demands continuously, the planned operating strategy will often require additional heat from conventional boilers or heat rejection, power importing or exporting, and modulation of CHP output. Different operating strategies will need to be considered for such part-load considerations, such as: the benefits of exporting power; heat rejection to atmosphere to maintain power production; the requirement for night operation; and the necessity for a thermal store. The potential benefit of a thermal store is that it smooths peaks in building heating demand, so allowing heat to be supplied without the CHP being operated. Stored heat may be used to satisfy night-time heat demands, as generating night-time electricity may not be economic. At times of low heat demand (typically in summer), the CHP can be operated for fewer hours but at higher output. (Without a store, the demand may be below the CHP unit’s acceptable turndown limit.)
The physical integration of the CHP must be considered, as they are far heavier than traditional condensing boilers. Adequate space must be available to allow proper access for servicing.
Renewable technologies to supply heat and power may need to be considered, especially for new-build projects, and the interaction with the CHP system should be quantified to ensure that two technologies are not competing to supply the same demand.
Typical capital and maintenance costs and efficiencies for gas-engine CHP will generally be evaluated in terms of £/kWe. These can be provided by the manufacturer or through tables such as those in AM12.
The modular mini-CHP units are typically designed to run practically unattended (with facilities for remote monitoring) and are likely to require servicing annually. It is typical for maintenance contracts to be written in terms of a fixed cost per hour of operation, so operating at part load will effectively incur additional maintenance costs per unit of energy produced. Generally, specific maintenance costs reduce with the CHP capacity.
Financial viability
A spreadsheet model can be set up, from which operating costs and savings can be evaluated. This needs to be subjected to sensitivity analysis on energy prices and also on variations in site energy demands. The accuracy of the final result will depend upon the reliability of input information. However, by setting up a spreadsheet model, it is a straightforward process to test the sensitivity of the result to fluctuations in input parameters, such as gas or electricity prices.
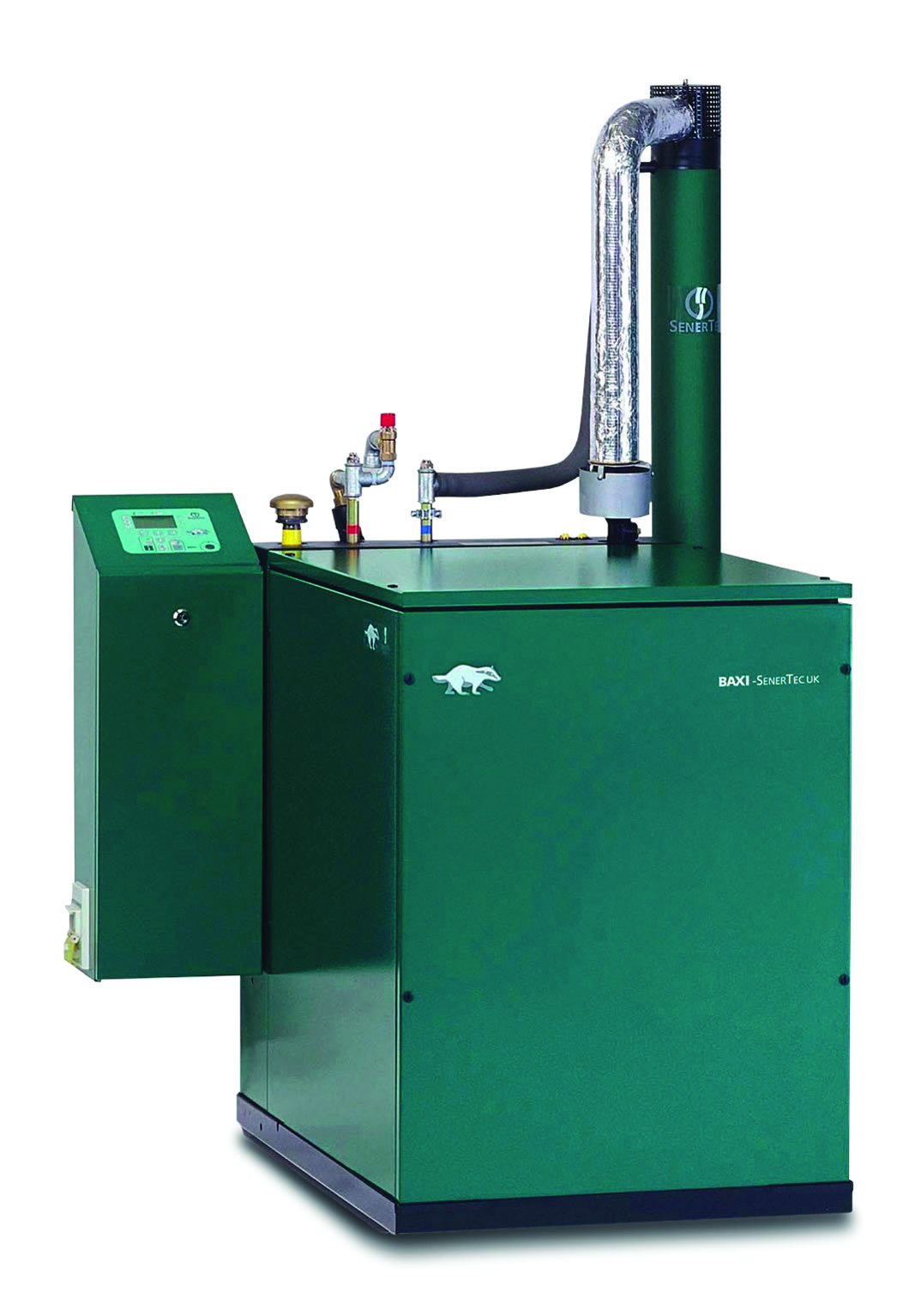
Figure 4: A 5.5kWe/12.5kWth – 15.5kWth with condenser – CHP unit (Source: SenerTec)
Using a simple payback approach assumes constant operational savings and ignores the project benefits beyond the payback period – which may be higher if energy prices rise. Where multiple investment options are being compared, a simple payback period is also of limited value, as the capital investments may vary significantly. For a project that could generate variable revenues over a period in excess of 10 years – or where there are many options to evaluate – a discounted cash-flow analysis would be more appropriate.
To compare a range of options – such as several sizes of CHP and other low carbon heat source investments – net present value (NPV) or internal rate of return (IRR) are used. The NPV is the total value of the project (both capital and operating costs over a period of years) expressed at today’s value, equivalent to a capital cost. A positive NPV means that a project is viable. The IRR value for a project identifies the return that money invested elsewhere would have to earn to give a better return than the chosen project. Many companies and organisations will set a ‘hurdle’ rate of return that must be achieved for a project to receive funding. Both methods are considered in more detail in AM12.
Sensitivity of results
For any appraisal technique, care must be taken about the reliability of input data and the sensitivity of results to changes. The aim is to give confidence about a project’s viability under variations in key project parameters, including heat and power demands, gas and electricity prices, and capital expenditure. Computer-based spreadsheets allow many scenarios to be compared swiftly, potentially producing output as in the example in Figure 3.
A likely uncertainty that can be built into the model is the availability of grants and incentive schemes.
Applications for mini-CHP
There are particular applications that are likely to fare well in the foregoing feasibility study, such as small care homes, police and ambulance stations, and social community housing. Mini-CHP can be suitable for small hotels and leisure centres – applications with significant year-round hot water requirement (and so heating load) and demand for power. Remote, potentially off-grid locations that have the opportunity to produce biogas may also present a good opportunity for CHP, such as the unit shown in Figure 4.
CPDs on CHP
The April 2016 CPD Applying CHP to reduce CO2 emissions and operating costs for the supply of domestic hot water provided an account of the application of CHP associated with producing domestic hot water. That article provides complementary information to this one on CHP technology.
CHP can only provide benefit if it is sized, installed and operated correctly. Manufacturers’ experience suggests that including the supplier, contractor and operator at the early stages of the feasibility and design leads to more effective implementations that are both carried out appropriately and operated effectively. This can provide systems that are environmentally and economically sound, even with the reducing carbon factor for grid electricity.
© Tim Dwyer, 2016.
References:
- CIBSE AM12, Combined heat and power for buildings, CIBSE 2013.
- http://data.worldbank.org/indicator/EG.ELC.LOSS.ZS – accessed 6 July 2016.
- Energy Trends: June 2016, DECC, UK.