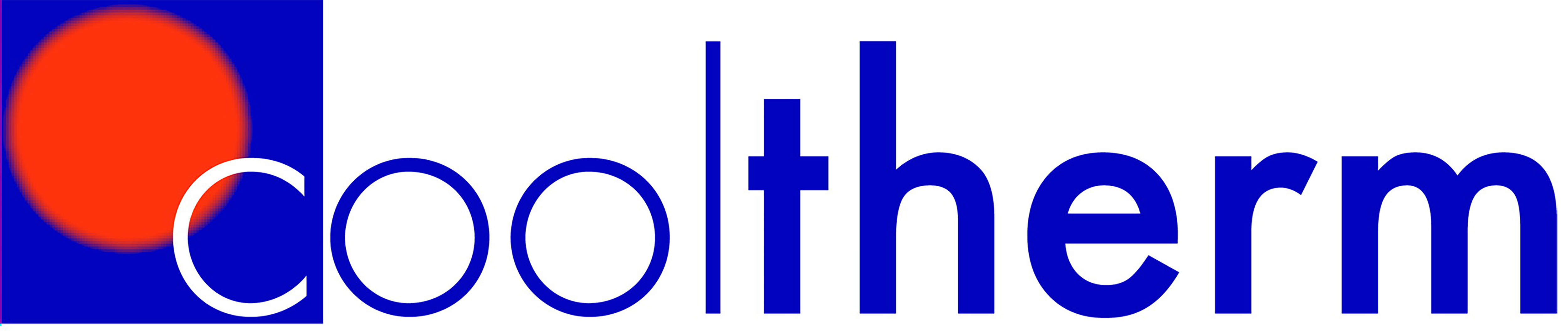
This article will consider the use of propane for air conditioning applications.
Propane (R290) as a refrigerant
Propane is a naturally occurring substance and is produced as a by-product of natural gas production and oil refining. Common general uses are as a fuel for engines; brazing and welding; portable stoves; and residential heating boilers. It is also used as a fuel for hot air balloons.
Propane is already widely used in domestic fridges and freezers. However, propane’s operating pressures and temperatures are well suited for use in air conditioning equipment, including chillers. Propane’s performance characteristics are similar to those of the now-outlawed R22 – which was phased out because of its high ozone depletion potential. Propane has good compatibility with materials commonly used in the construction of refrigeration and air conditioning equipment, and is commercially available and relatively inexpensive. It can be stored and transported in steel cylinders in much the same way as other common refrigerants. However, being flammable, there are some additional health and safety rules to observe.
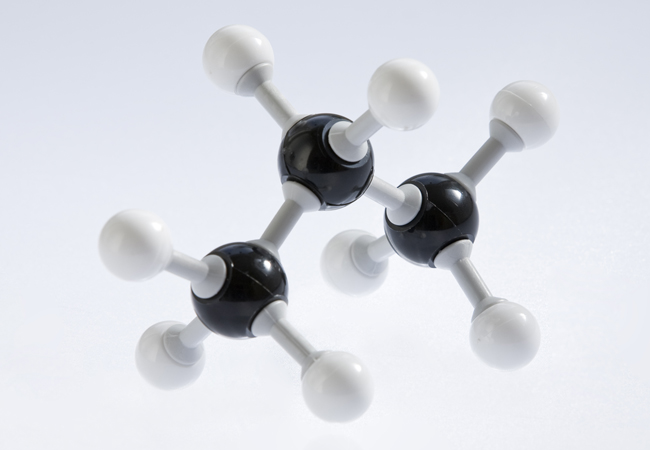
Propane molecule
When compared with hydrochlorofluorocarbons (HCFCs) and hydrofluorocarbons (HFCs), propane will have a lower system pressure drop and a higher heat transfer performance. Since its thermodynamic properties are well suited to the temperatures typically encountered in building services engineering, the refrigeration cycle coefficient of performance (COP) is comparatively good.1 As a result, the refrigeration charge for propane can be 40-60% less than other common refrigerants. Propane is non-toxic, and has an ozone depletion potential (ODP) of 0 and a global warming potential (GWP) of 3, as shown in Table 1. Its potential environmental impact is, therefore, far lower than many other commonly used refrigerants.
Because of its flammability, great care is required in the manufacture, installation and servicing of chillers that contain propane. Propane is denser than air, so if a leak occurs it will displace air and drop to the lowest point. This means it could collect into enclosed areas where there is a risk of explosion if the leaked gas comes into contact with a flame, spark or other ignition source.
Propane that is supplied for general use – such as in barbeques and patio heaters – is not suitable for use in refrigeration systems. This can contain high levels of contaminants, with purity ranging from as low as 65% to 95%, featuring high levels of moisture and unsaturated hydrocarbons. Only propane produced specifically for use in refrigeration systems – with a purity of not less than 98.5% and moisture content below 10ppm (by weight) – should be used.
System requirements to use propane
Most of the principal components – including condensers and evaporators; filter driers; sight-glasses; check valves; safety valves; shut off valves; solenoid valves; pressure switches; and thermistors – are no different from those fitted in an HFC or HCFC refrigerant chiller. Expansion valves specifically designed for use with the operating conditions of the propane refrigerant should be fitted to chillers.
The typical approach taken by manufacturers is that the chiller is: always considered to be operating in a normal situation; is gas-tight and sealed; will not be working in an explosive atmosphere; and will be commissioned by someone having the relevant experience, training and qualifications. Under these conditions, there is considered to be minimal risk. However, if a leak occurs, a risk exists of an explosion from, for example, a spark produced by an electrical device.
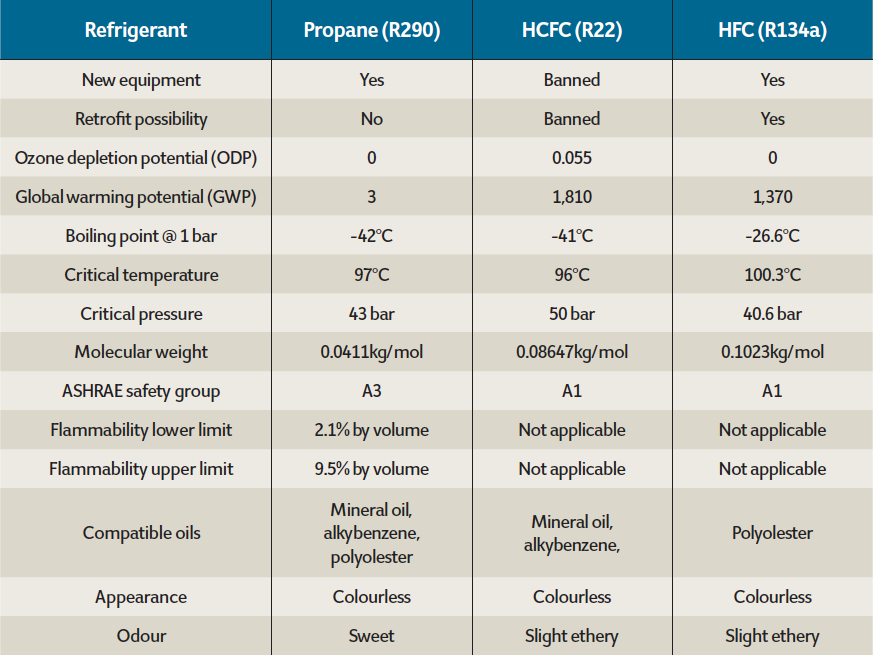
Table 1: Principal properties of propane, compared with a pair of alternative refrigerants historically used in chillers
Chillers are produced to minimise both leakage of propane and the propane charge for the given application. BS EN378 Part 12 contains strict limitations on the size of charge of hydrocarbon refrigerant that can be used in equipment, dependent on: room type; location and size; occupancy category; and whether the system is sealed, indirect and located in the open air. Propane is designated an A3 safety classification – refrigerants are designated a toxicity/flammability category in ISO8173 that is applied in BS EN378. ‘A’ indicates low toxicity (‘B’ is high toxicity), and the scale of 1 to 3 is used to designate the degree of flammability: no flame propagation (1); lower flammability (2L); flammable (2); and higher flammability (3). No mandatory limit is placed on how much propane refrigerant can be used in a packaged chiller installed in the open air. However, some manufacturers have adopted 25kg as the upper limit for the amount of propane per circuit.
A leak detection and control system must be fitted that, when activated, will pump down the propane charge into a liquid receiver and then shut off the electrical supply to the chiller. Where a compressor is enclosed, a ventilation fan (that meets appropriate requirements of the EU ATEX – Atmosphères Explosibles directive) must be installed to remove any gas that might leak from the compressor into the enclosure – this being activated by the leak detection system.
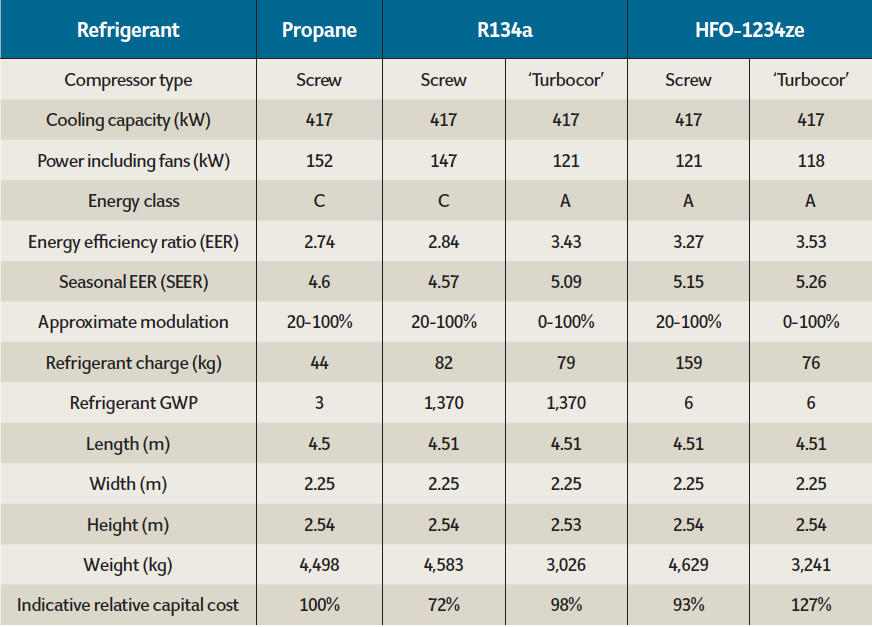
Table 2: Example packaged air-cooled chiller selections, based on chilled water temperatures of 6°C flow, 12°C return, and external temperature of 35°C. Data supplied by Geoclima srl/Cool-Therm
Compressors for propane chiller applications are usually based on a reciprocating or screw design. Electrical components fitted directly onto the compressor – such as the terminal connection box, start capacitor or crank case heater – should be manufactured to at least IP54 standard (so being protected from limited dust ingress and from water splashes) or a higher rating, and meet the requirements for an A2 zone. Motor winding thermistors should be housed and wired separately from other electrical components. The compressor will be clearly labelled ‘Attention Fire Hazard’.
The electrical components must be inherently safe, and the risk of static electricity build-up limited by the manufacturer through the fitting of adequate earth bonds.
Abnormal operation of the chiller, exposure to heat (fire), and various other faults may cause high-pressure refrigerant conditions. On sensing abnormally high pressure, gas should be relieved into the low pressure side of the refrigeration system, rather than released to atmosphere. If the pressure continues to rise, then the gas is released through a pressure relief valve – each chiller refrigeration circuit must be fitted with a correctly selected relief valve to release excess pressure. The valve should be mounted as close as possible, and above high-pressure liquid receivers. In the case of air-cooled condensers, valves should be fitted at the highest point of each condenser bank circuit, and should be easily accessible and clearly visible from a safe distance – so readily alerting operators of the potential release of a flammable gas. Wherever possible, the discharge port on the valve must be directed to a safe place, away from any source of ignition – preferably in an upward direction, to prevent pooling of propane at low level.
For transport to site, the framework of propane chillers should completely enclose all the refrigeration system pipework and components that contain propane. This is to avoid accidental damage and the release of the flammable gas during transportation and handling.
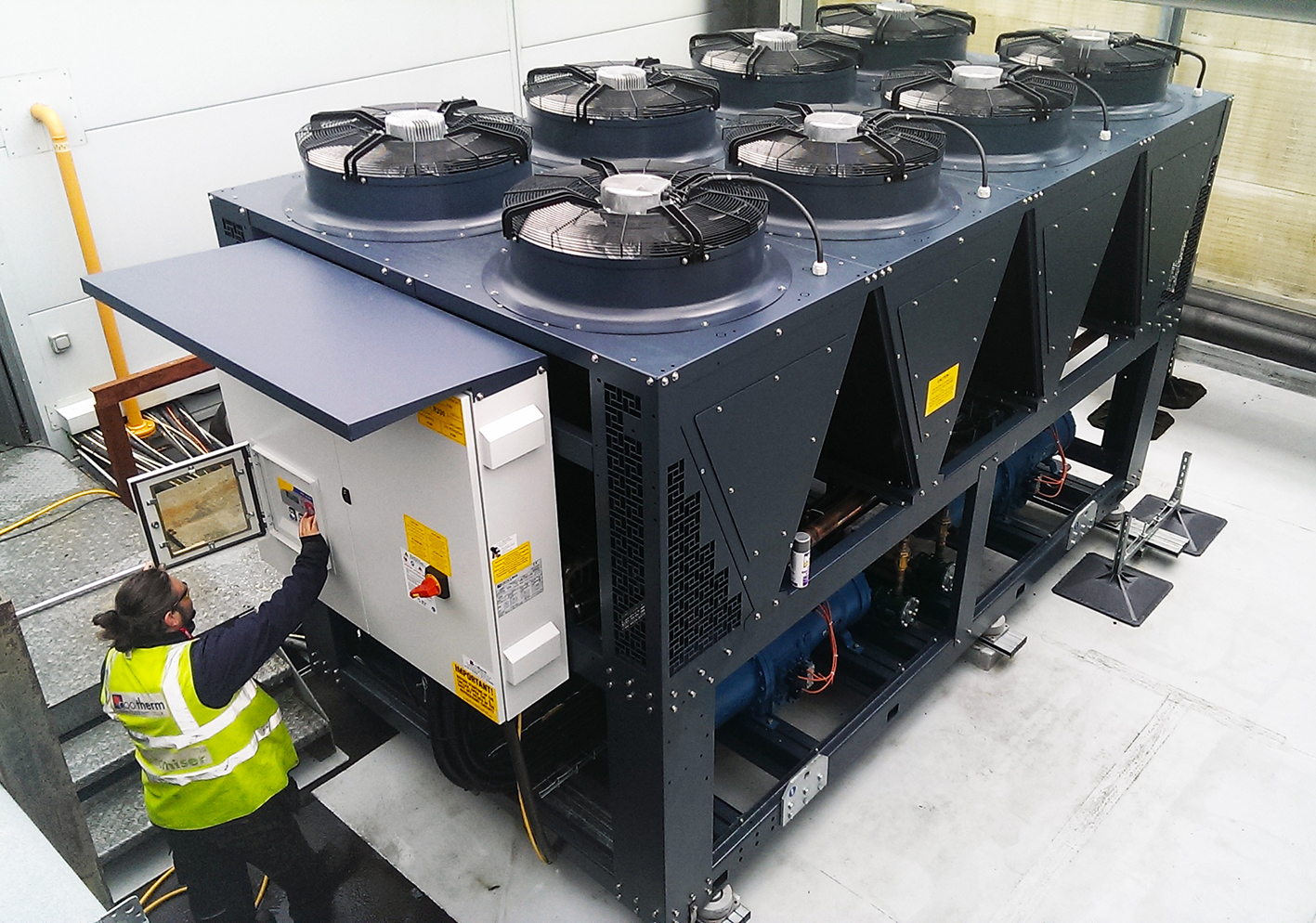
Figure 1: A 500kW air-cooled propane chiller (Source: Cool-Therm)
The European ATEX legislation on pressure equipment has been aligned recently to the New Legislative Framework to simplify and improve its implementation, and the new directive 2014/68/EU4 came into force on 20 July 2016. Propane chillers supplied in Europe must be certified and tested to comply with this newly aligned and recast directive.
The labelling on the plant must include refrigerant type and group classification, along with an indication of flammability risk. To be sold in Europe, the equipment requires an EU declaration of conformity that confirms it is in accordance with relevant regulations and standards.
Operational responsibilities
It is recommended that the local fire authority be advised of the location of a propane chiller installation, including the size of the refrigerant charge and any other relevant health and safety information.
As with all chillers, planned maintenance is essential to keep plant working safely, efficiently and reliably. Only experienced refrigeration technicians, who have undertaken appropriately certified training, are permitted to service and maintain propane-based chillers. As its popularity grows in the refrigeration and air conditioning industry, increasing numbers are being trained to work with propane equipment. With a propane refrigerant chiller, regular leak checks are particularly important. As a general rule, four quarterly inspections each year are considered sufficient, and record-keeping in line with the F-Gas regulations5 must be undertaken.
The potential future for propane chillers
Under the revised F-Gas regulation – which came into force in January 2015 – from 2022, a ban will come into effect on new centralised refrigeration systems for commercial use with a capacity of 40kW or more, using refrigerant with a GWP of more than 150. This will rule out many of the refrigerants commonly used in chillers today, notably R134a. Meanwhile, the race continues to develop new low-GWP refrigerants, as well as evolve systems to utilise the more environmentally benign extant refrigerants that are both safe and affordable, and can operate economically at the conditions required for building services systems.
Packaged propane air-cooled refrigerant chillers (such as that shown in Figure 1) can be a serious contender when considering low GWP cooling plant for commercial buildings. Apart from flammability considerations, propane chillers are not too dissimilar from those that have been used for many years in the building services industry. They have similar designs, dimensions, weight and efficiency, and can be equipped with inverter-controlled capacity to operate effectively across varying loads. A propane plant is around 39% more expensive than a basic screw compressor chiller operating on R134a. However, when other low-GWP, high-efficiency chillers are compared (as in Table 2), the cost difference is minimal – just 7.5% higher than a screw compressor chiller working with HFO-1234ze refrigerant, and 27% less than a ‘Turbocor’ compressor working with HFO-1234ze.6
The installation and commissioning process is much the same as for any other chiller installation, although it is particularly important that a proper risk assessment is undertaken on the intended position of the chillers. Reportedly, propane chillers have proven to be very reliable, possibly because the operating characteristics are very similar to the once commonly used refrigerant R22. Service and maintenance are likely to be slightly more expensive, compared with a standard screw compressor chiller but, in time, this differential is likely to reduce, as greater numbers of service technicians become experienced and qualified in handling propane chillers.
© Ken Strong and Tim Dwyer, 2016.
Further reading:
- Guidelines for the use of hydrocarbon refrigerants in static refrigeration and air conditioning systems, ACRIB.
- Guide to flammable refrigerants, BRA.
- Safety code of practice for refrigerating systems utilising A2 & A3 refrigerants, Institute of Refrigeration.
- Flammable refrigerants safety guide, The Australian Institute of Refrigeration and Air Conditioning Equipment.
References:
- Pandavly, P. et al, Ecofriendly Refrigerants, Applied Mechanics and Materials Vol. 612 (2014), pp 181-185.
- BS EN 378-1:2008, Refrigerating systems and heat pumps – Safety and environmental requirements. Basic requirements, definitions, classification and selection criteria (+A2:2012) (incorporating corrigendum December 2008).
- ISO 817:2014, Refrigerants – Designation and safety classification.
- Directive 2014/68/EU on the harmonisation of the laws of the member states relating to the making available on the market of pressure equipment, May 2014.
- See F-Gas in refrigeration air conditioning and fire protection systems for detailed information.
- Data supplied by Cool-Therm.