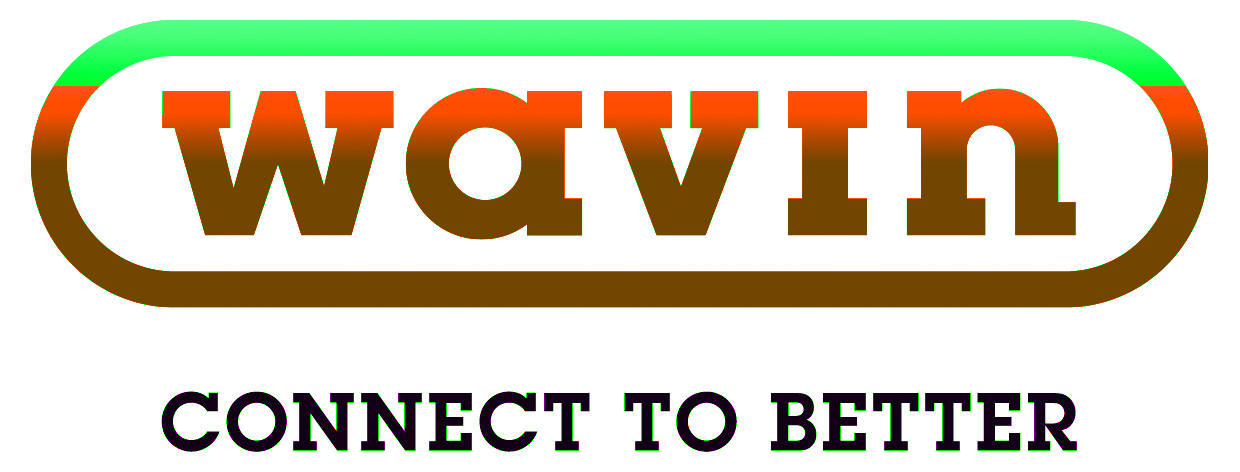
This CPD will consider some of the ways that BIM has been shown to deliver real benefits, and some opinion as to why it has not reached further into the industry. In addition, it will describe an example of how detailed manufacturers’ data can be readily used – together with ‘off the shelf’ BIM software tools – to provide design solutions for waste-water systems swiftly.
The integrated building information model can be exploited and developed by the whole construction team, and enable contractors and building operators to get earlier involvement in the process.
BIM is still seen by some as a simple ‘add-on’ to a 3D design, but – for its greater success – it requires timely contributions of information from all participating parties, throughout all the stages of the project delivery.
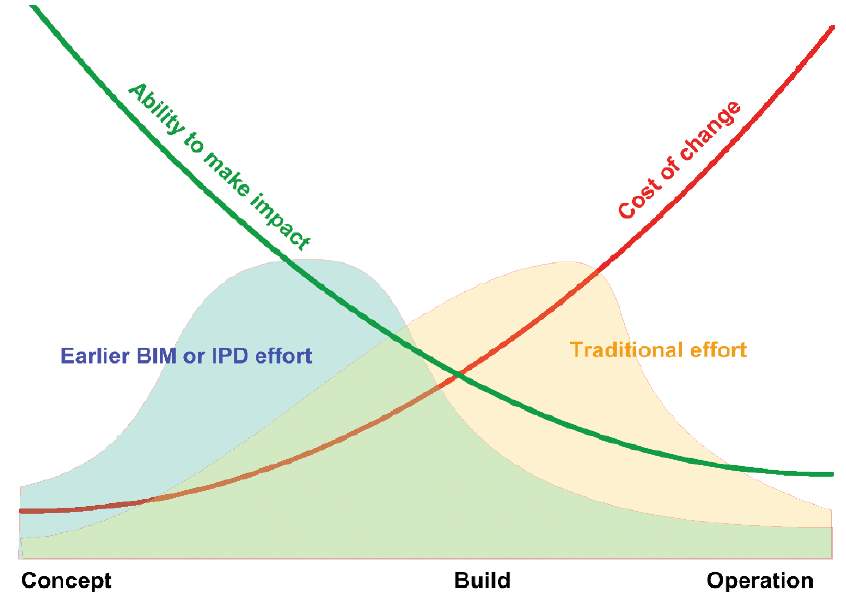
Figure 1: The classic curves indicate that earlier intervention – as would be likely in integrated BIM – makes greater impact at lower overall cost (after work by MacLeamy/Paulson)
BIM is, however, much more than software. It is a catalyst for integrated working in a collaborative design and supply chain, between all the stakeholders in a construction project. In an ideal scenario, BIM underlies a scheme from conception, through design, manufacture and construction, to life-long operation and eventual decommissioning, demolition and recycling – connecting all the phases with a continuous and maintainable data set that lives with the building. In practical terms, the application of properly managed BIM processes removes the need for the construction chain repeatedly to re-enter data into disparate pieces of software, or to produce multiple independent versions of drawings and schedules. By doing so, it eliminates not only this task, but also the inevitable errors of ‘translation’.
In his paper1 presented at the CIBSE Technical Symposium earlier this year, engineer and BIM specialist Barry Wormald provided some convincing real-world examples of how the active incorporation of BIM methodologies was providing robust return on investment. He cited several case studies that illustrated the practical benefit of the early influence of integrated product delivery (IPD) in the design and construction process – as shown by the curves in Figure 1.
Wormald writes of practical examples of how BIM has been used to improve a project across its whole life, including:
- Modelling at early stage to assess loads accurately, and compare options for the most efficient life-cycle cost solutions for building form and system type
- Optimisation of plant space requirements
- Reduction in the requirement for the production of drawings
- Ability to generate an accurate bill of quantities to allow option appraisal and accurate costings
- Information provided sufficiently early for prefabrication of services for optimisation of material and labour requirements, plus improvement in quality
- ‘Virtual commissioning’ of systems using BIM to optimise system design, and then to reduce onsite commissioning
- Applying BIM to inform the facilities management model, potentially to increase the value and life of the asset, and reduce life-cycle costs.
However, there is a dilemma that may be preventing building services engineers from fully embracing the adoption of integrated BIM tools, particularly early in the project. In a recent article2, Ed Paul, a US-based BIM manager, notes that: ‘Architectural models are detailed and dimensioned to a high level of accuracy, and it is expected that [building services] models will match that accuracy… This sets the precedence in architectural and structural models, which are required to provide dimensional control for the contractor as an element of design. [Building services] design work rarely, if ever, has the same level of detailing. However, as [building services] modelling software became mature enough to be used on major projects, expectations were already set for similarly detailed [building services] models.’
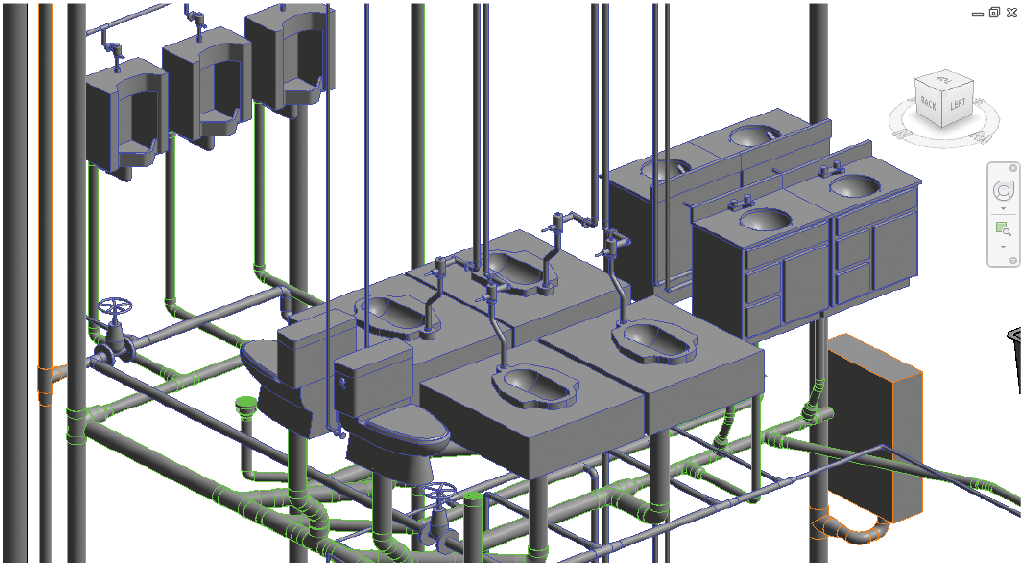
Figure 2: A layout of generic waste pipework generated semi-automatically by a BIM software tool (Source: Autodesk)
Whether or not the traditional working practices of building services engineers are lacking positional resolution, the 2015 industry survey carried out by CIBSE and the Electrical Contractors’ Association (ECA) indicated that fewer than one in six of those surveyed – who were predominantly building services manufacturers, suppliers, consultants and contractors – were ‘fully ready’ to apply BIM in a project. The majority considered that there was not enough practically useful and publicly available information on BIM – a challenge that has most recently been taken up by CIBSE, with the rollout of the CIBSE BIM Roadshows currently touring the UK and Ireland (see cibse.org/bim for details).
The survey also provided evidence of some reluctance to apply BIM, with respondents strongly agreeing that ‘BIM is not relevant to what we work on’ and ‘the projects that we work on are too small for BIM’. This could be factually correct and, possibly, the audience for the survey was not a population of current or potential BIM users – although that could be considered unlikely, as they did have interest in completing a BIM survey. It could, of course, be the very lack of accessible and usable information that was causing the reluctance to engage.
In his account3 of how the building services industry is slow to take up BIM, consultant Steve Hunt identifies that ‘many suppliers haven’t inputted their products into [a form suitable for BIM integration] and cannot, therefore, be considered for specification on BIM jobs’. The need for the early engagement of the building services engineer is reinforced in the recent case study4 of the mixed-use building project at Mansfield College, Oxford, where architect Andy Matthews lamented that the ‘full benefits of design coordination could not be realised because the services engineer did not produce an MEP model’ at an early stage in the BIM software environment. He continued that ‘there is a bit of a problem in the industry, in terms of where the MEP design should occur. BIM front-loads the design more, so the interface between MEP outline and fabrication design has to shift back for BIM to be more successful’. This shift to altering practices – and, presumably, fee scales – for working with a timeframe that is conducive to successful BIM implementation is a not just a challenge to the building services sector. Writing in his 2015 review article, Hunt notes that ‘many architects are still designing projects in [traditional CAD rather than with BIM tools]. Around 85% of the architects we work with are still working with 2D software, and we simply cannot then crowbar in a 3D building services design. The building services sector cannot work in BIM if the project has not been designed in [appropriate BIM tools] by the architect.’
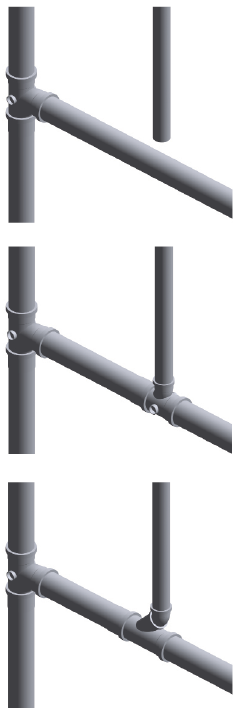
Figure 3: The development of a swept connection (Source: Wavin)6
In an initiative to provide more detailed product information that is suitable for integration with BIM software tools, CIBSE is leading an industry group to produce the product data templates (PDTs). These are a developing set of templates that allow manufacturers to supply non-graphical basic product data in a simple spreadsheet form that can then be read and integrated into standard BIM software tools – assisted by the newly available CIBSE BIMHawk toolset. The completed PDTs are not only designed to offer detailed sizing or graphical information, but also to provide links to other resources – such as manufacturers’ and third-party detailed BIM object libraries – that can include graphical and other parametric information. These are specifically designed to provide data at the early stages of the BIM flow and continue to feed information throughout the project. They are discussed more fully at cibse.org/bim
Moving intelligent plumbing objects into BIM
As an example of how contextualised BIM tools can provide an enhanced design process, consider the design and selection of waste-water systems. Even in the absence of specific manufacturers’ product data, current BIM software tools are able to: apply fundamental and empirical fluid-flow relationships; ‘look up’ tables of demand and discharge ‘units’ and flows; and detail pipe-flow characteristics. This can establish basic sizes of plumbing piping in, for example, domestic hot water, domestic cold water, and sanitary pipework systems, so that it meets the recommendations of CIBSE Guide G.5
As an example, the most commonly used ‘out of the box’ BIM software tools are able to determine automatically the drainage pipe sizes and gradients, producing piping schedules and graphical output as shown in Figure 2. Once the sanitary fittings are chosen and located, all that is needed are single-line connections between sanitary fittings, and the software determines appropriate nominal sizes of soil pipework and fittings, based on in-built algorithms and data sets.
Users and manufacturers have identified the commercial and practical need to provide more detailed project-related information, with more specific sizing and selection algorithms than would be available in either the software’s in-built defaults or, for example, the information drawn from a completed product-related PDT. Add-in software – typically supplied free or at low cost by the drainage pipe manufacturer – is available to extend the capability of the BIM software tool, allowing it to undertake specific contextualised selections of the manufacturer’s components – both more accurately representing the potential layout, and providing schedules and information for bills of quantities.
This can enable more exacting detailed design and incorporation of a piping system into a BIM model that includes appropriate – and, possibly, bespoke – component detail. The add-in software can leverage detailed knowledge of the product range that would previously only have been available with multiple searches of catalogues and communications with the manufacturer. These – often-termed ‘intelligent’ – software tools are designed to enable the user to produce detailed installation designs, while still using the familiar interface of the main BIM software tool.
In the progressive development of the detailed connection of Figure 3, the software user will have created this detail in just a few mouse clicks, but it provides the certainty that the components that make up the junction are dimensionally correct and will generate appropriate scheduling data for estimation and procurement.
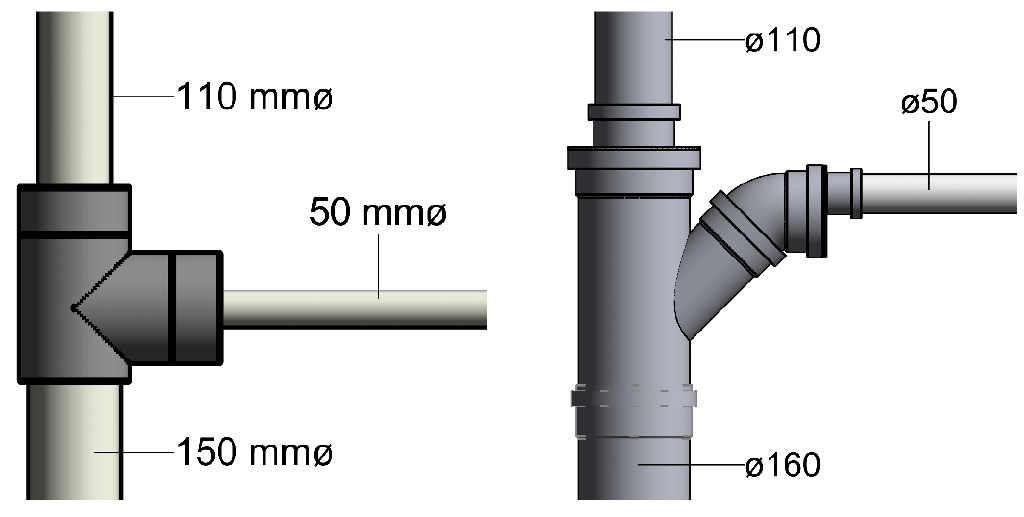
Figure 4: The reality of a simple generic branch (left) may well require multiple components and commercially available sizes that can be selected automatically by the add-in software (Source: Wavin)
The basic BIM software tool is likely to have been able to generate the generic branch; but – although each junction might appear to consist of a single 90° branch fitting – it could, in reality, be a combination of fittings and commercially available sizes (as shown in Figure 4). The manufacturer’s custom software can use its algorithms, rules and data sets to insert the complete set of appropriate components automatically.
Integration of detailed manufacturer data enriches the BIM experience, and may help to convince those wary of integrating it into their work processes that there are direct benefits, aside from the wider – perhaps less tangible – life-cycle ones, of applying building information modelling.
© Tim Dwyer, 2016.
- For an example of the application of manufacturers’ content in a BIM software tool, see the videos at youtu.be/Bz97vtDK-lk
References:
- Wormald B, BIM for integrated design, construction, commissioning, operation and maintenance, CIBSE Technical Symposium, Edinburgh, April 2016.
- Paul E, Integration: BIM design – accessed 5 November 2016.
- Hunt S, Why is the building services sector lagging behind in BIM? – accessed 5 November 2016.
- Cousins S, Case study: Mansfield College, Oxford – BIM shows its worth on student building – accessed 5 November 2016.
- CIBSE Guide G Public health and plumbing engineering, CIBSE 2014.
- Tutorial 9 – Wavin enhanced S&W junctions with Wavin Packages in Revit for BIM, – accessed 5 November 2016.