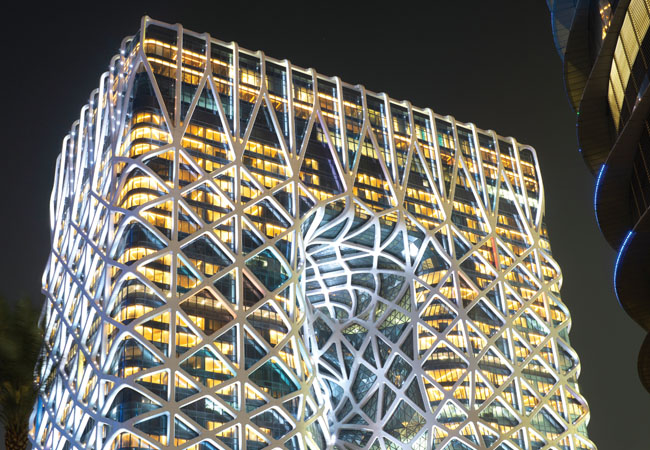
It might look like a brick wrapped in a string vest, but Morpheus is Macau’s latest, and most remarkable, luxury hotel. Designed by Zaha Hadid Architects, the 40-storey, building is supported by, what is claimed to be, the world’s first ‘free-form high-rise exoskeleton’. This sinuous, external structure rises up to wrap, vine-like, around the rectangular building, which is formed from a pair of towers linked at the podium and roof levels. The steel-tracery also envelops two amorphous sky-bridges, which connect the towers, mid-height, to create three irregularly shaped voids that open up the centre of the building.
The architect’s rationale in placing the supporting structure on the outside of the building was to give it a unique external identity while minimising the need for interior columns to maximise internal flexibility. The challenge for BuroHappold Engineering’s façade engineers was to clad this serpentine, structural skeleton – and the layer that sits behind it – in a single, homogenous, glazed skin.
To add to the challenge, the façade has to be able to withstand typhoon-force winds, which – as Typhoon Mangkhut recently reminded us – are a feature of this part of China’s coastline. Such potential for extreme weather has also resulted in the hotel’s syphonic rainwater system being designed to handle 216mm/hr of rainfall, while the rooftop lightning system uses the cladding of the exoskeleton as a down conductor, in accordance with BSEN62305.
Servicing the Morpheus
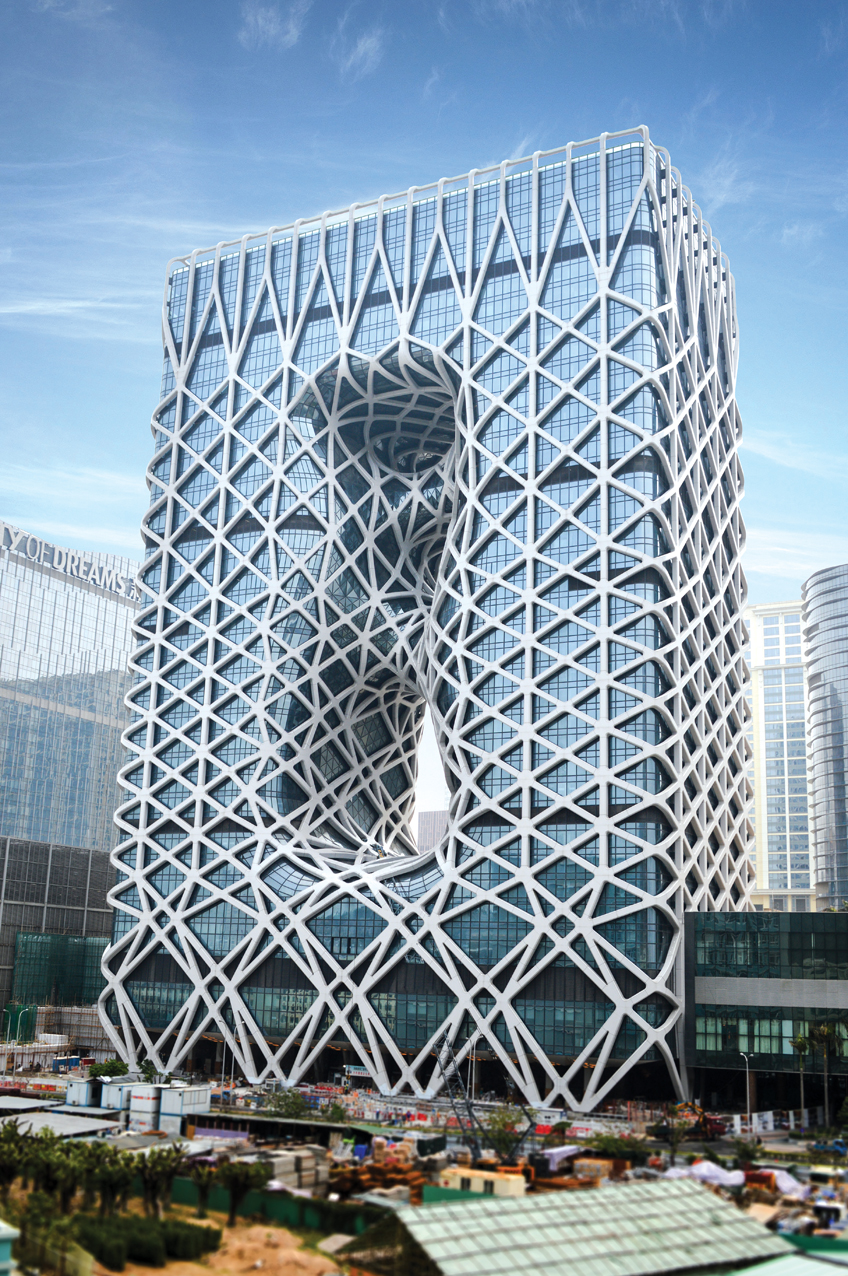
The stunning Morpheus Hotel rises high into the Macau skyline
Away from the façade, the hotel’s chilled and low temperature hot water is supplied by a central energy plantroom for the City of Dreams resort and casino. Its heating and chilled water circuits are isolated from the primary mains by heat exchangers, and the chilled water supply temperature on the secondary side is maintained at 6°C, and the return temperature at 14°C. Heating and chilled water mains rise up through concrete cores, and there are separate duct and pipe risers. The hotel has centralised hot-water plant based on gas-fired condensing hot-water boilers and water-storage vessels.
There is underfloor heating in the guest bathrooms, while comfort in these rooms is maintained using four-pipe DC fan coil units (FCUs), which are controlled by in-room temperature sensors and fan-speed controllers. Pre-treated fresh air is supplied via air handling units (AHUs) on the plant floors – 3, 19 and 39 – and AHUs with cooling and heating coils maintain perimeter comfort in the entrance lobby and the giant atrium.
AHUs with cooling only serve the interior spaces. The units supply fresh air, via jet nozzles, to the occupied zone, based on CO2 concentration of the return air. Buoyancy forces then drive the stale air upwards and it is exhausted at high level.
Unsurprisingly, however, it is the Morpheus Hotel’s façade – rather than its building services – that steals the limelight.
The Façade of the Year Competition
The annual international competition run by the CIBSE Society of Façade Engineers is open for entries. Closing date for submissions is 15 October 2018. The awards recognise, reward and promote excellence in the key disciplines of façade design, engineering and application. For full details visit: sfecompetition.org
Design parameters
BuroHappold’s highly engineered solution incorporates more than 30 façade systems, including: unitised with flat glazing; unitised with single-curved glazing; unitised and stick with faceted glazing; giant free-form, triangulated glazed panels; and an aluminium panel system in which to clad the structure.
Understanding the building’s geometry was key to developing the façade. From the outset, the design team worked in a three-dimensional environment. ‘You wouldn’t be able to construct this building in a traditional way, using 2D drawings, because the geometry is unique,’ says Victoria Cameron, BuroHappold associate and façade engineer for the project. ‘It was so complex, it forced us to change the way we designed.’
Most of the geometrical modelling was done using Rhino3D CAD application using the Grasshooper visual programming language for analysis. A set of parameters was agreed as the basis for the design. These included: ensuring the nodes of the exoskeleton aligned horizontally with the floor-edge beam; and that the stub-beams – which project from the nodes through the façade to connect to floor beams that transfer forces between the exoskeleton and each tower’s concrete core – are both horizontal and perpendicular to the face of the façade.
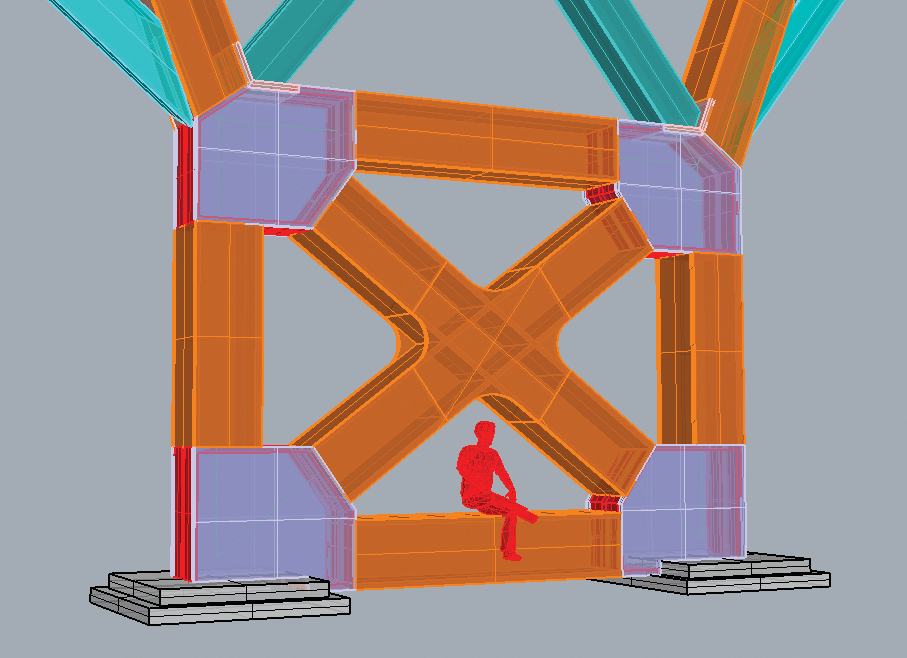
Rhino3D was used in most of the geometrical modelling for the Morpheus Hotel
The architect supplied a wire-frame model of the exoskeleton and a reference surface defining the outer boundary of the glazed envelope. Using these parameters, the team defined a topological mesh that describes the outside surface of the façade envelope. Within these geometrical constraints, BuroHappold’s façade designers then established which system could be used, and where, to support the building’s glazed skin. ‘We took the envelope and broke it down into its different geometries. By understanding the technical limitations of how far we could push each system and, rationalising the geometry within these, we established the areas of unitised, semi-unitised, stick system and faceted glazing. This was followed by rationalising the use of flat, single-curved and double-curved glass,’ explains Cameron.
Four principal façade types are used:
- Flat glazing and unitised façades covering the hotel rooms
- Single-curved glazing supported on a unitised system on the building’s corners
- Faceted glazing supported by a combination of unitised and stick façade systems
- A triangulated glazing system for the façade surrounding the atrium voids, which Cameron calls the ‘free-form area’. ‘Nothing was standardised, so we’ve had to custom design each system,’ she adds.
Perhaps the most straightforward parts to clad were the areas of flat façade that surround the two tower structures, where the majority of the hotel rooms are located. ‘We used a traditional unitised, reinforced-aluminium frame façade system for the towers,’ says Cameron.
The building’s geometry was so complex it forced us to change the way we designed
The glass here is double-glazed, typically 12mm thick with a 16mm gap, and is solar control, high-performance. This was selected to limit solar gains to the rooms while giving the same visual consistency, whether flat, curved, single- or double-glazed. All the glass came from the same manufacturer and has the same low-E coating. On one side of the tower, the double-glazed units are acoustically treated and the inner and outer glass is laminated with a polyvinyl butyral (PVB) interlayer to prevent noise from MEP plant penetrating the façade.
Before the façade could be fitted, the building’s structural exoskeleton had to be installed – which meant conventional installation, from the outside, could not be used. So BuroHappold designed a system that could be put in by operatives working on the floor plates. First, the opaque spandrel panels were fixed to the edges of the floor slabs, then the vision panels were fixed between the spandrel panels from inside the building.
‘Even on the flat areas of the façade – where we were using the more traditional, unitised façade system – we had to break it up into spandrel and vision panels, to enable it to be installed from inside the building,’ says Cameron. This allowed any glazed panel to be replaced from inside the building in the event of breakage. Single-curved glazing is used in units that wrap around the towers’ corners.
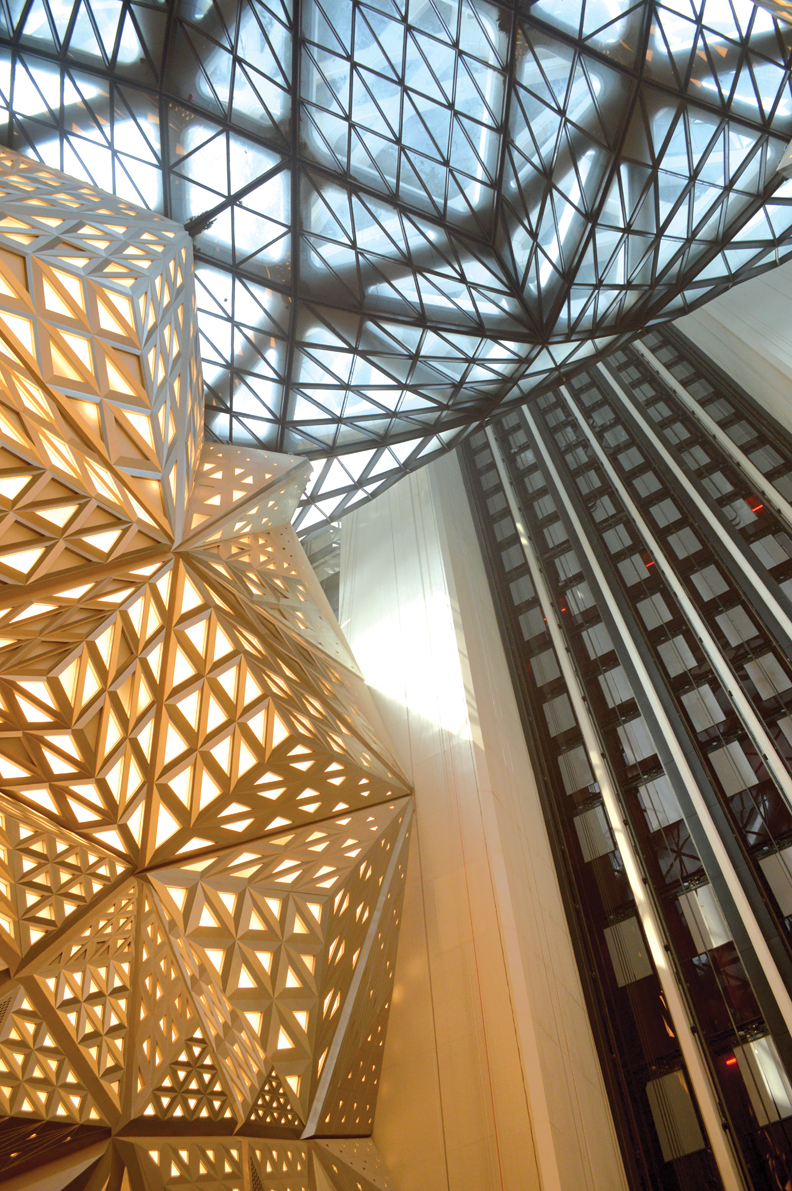
There are no floor slabs from which to attach the façade in the central area of the building, where the sky-bridges surround the central voids – the ‘free-form’ area. ‘We’ve had to attach the façade to the exoskeleton,’ explains Cameron. Although it appears to be a twisting mass of steelwork, the exoskeleton here has been very carefully rationalised, so each structural element is planar and formed from a single, curved steel. All the nodes connecting the steels are also flat, so they can be fabricated from steel plates.
Each of the 242 glazed panels in the free-form area is unique in shape and size. While the geometry of the flat façade surrounding the towers is defined by the vertical spacing of the floor slabs, the façade geometry in the free-form area is based on the three-dimensional spacing of the exoskeleton nodes. ‘At every step of the design, we have tried to rationalise the design as much as possible, but – in the free-form area – it was impossible, because every panel is unique, so we had to bespoke design every one.’
The nodes in this area are spaced up to 20m apart, which meant the diamond-shaped, glazed façade panels that they support measure up to 20m wide and 10m high. These ‘macro-panels’ are made up of smaller, framed, flat-glazed elements that are combined to form large, curved façade elements. This allows the same system to be used to clad the inward and outward sloping parts of the walls and roof. Because of the long spans and high loads, the frames of the macro-panels are formed using solid-steel plate sections. They vary in depth and width as required, to minimise the total steel tonnage.
‘The panels were fabricated as a single piece in the factory, then cut up to allow transportation and lifting on site, before being bolted back together,’ explains Cameron. ‘This was to ensure the complex tolerances would align in three-dimensional space. The panels are only ever supported from one nodal point on the exoskeleton, with the remaining nodes allowing for expansion and movement.’
The panels were fabricated as a single piece in the factory, then cut up before being bolted back together on site
The façade had to be designed to adapt to the exoskeleton’s movements and twists as construction progressed and loading on it increased. Movement is accommodated by a large, flexible joint between each macro-panel in the free-form area. ‘BuroHappold’s structural engineers carried out extensive analyses to understand how the exoskeleton would move throughout construction. We had to separate the façade from this movement to ensure it didn’t impose large stress on the glazing,’ says Cameron.
Single-glazing is used for the façade of the free-form area because its thermal performance was not critical in the large internal atrium spaces. ‘In this part, there is not much difference between daily highs and lows, and the internal temperatures are likely to be higher than the air conditioned rooms because of stratification,’ adds Cameron.
The glazed panels are, however, laminated with a PVB interlayer, to hold the layers of bonded glass in place should a panel shatter. ‘The glass is strong enough to be walked on, internally and externally, by rope abseilers for maintenance,’ she says.
The glass is also heat-strengthened. This is a different heat treatment from that of the glazing units in the hotel rooms, which are tempered. Tempered glass is strongest, so the minimum thickness can be used to withstand the high wind loads experienced in Macau. However, tempering glass also locks in stress. By contrast, heat-strengthened glass has lower levels of in-built stress, so there is a lower chance of spontaneous breakage from inclusions in the glass. ‘Because it is so much harder to access and replace the glass in the free-form area, we wanted the glazing to be as robust as possible,’ says Cameron.
Keeping cool in the casino
In the casino, the gaming areas are conditioned by modular AHUs. Fresh air is provided at a rate of 8 L·s-1 per person, and this is increased to 16 L·s-1 for the smoking areas.
The VIP gaming area has a variable air volume (VAV) system in areas where the ceiling is higher than 4m and a fan coil unit (FCU) system, with pre-treated fresh air, in areas where the ceiling is below this height. The air is supplied at a temperature of 14°C. Independent air conditioning systems are supplied for the smoking and non-smoking areas to ensure a pressure differential between the two areas by ensuring the non-smoking area is always at a higher pressure.
To comply with Macau’s smoking law, high-efficiency air filters and electronic air-cleaning systems are installed in the AHU serving the smoking area.
The casino is sub-divided into air conditioning zones of approximately 2,400m2 that tally with the sprinkler zones. Each AHU incorporates a supply fan, return/exhaust fan, mixing section, chilled water cooling coil, disposable glass-fibre, paper-type pre-filter and HEPA filter, and electronic air cleaner. The AHU fans have DC motors to vary the air-supply rate in response to the space loads, based on CO, CO2 and volatile organic compound (VOC) sensors in the occupied space.
The AHUs serving each air conditioning zone are used to purge smoke from any fires using the return air grilles and ductwork, and AHU exhaust fans.
Glazing installation in the free-form area was done externally, from the top down. The contractor filled the atrium with scaffolding and, as the façade was installed, this was progressively removed. The flat façade covering the towers was installed by a different contractor, from the ground up, so the two passed each other halfway up the building.
The façade to form the transition between the free-form area and the flat façade is formed of irregularly sized, faceted panels, held in position by a unitised aluminium frame. It was fabricated in mainland China. ‘We did look at using cold bending on site for the non-planar transition zone, but the façade contractors were unfamiliar with the technique and would not warranty the installation,’ explains Cameron. Instead, the units are flat and double-glazed, and the panels are fixed to the floor plates internally. ‘It is a similar system to the one used for the flat façade but with a more complex geometry.’
While the building’s façade is glazed, its exoskeleton is clad in 60,000m2 of flat, single-curved and double-curved aluminium sheet. The cladding had to be very thick, because it forms the main part of the lighting-protection system, and the huge quantity of aluminium cladding that needed to be designed and installed meant two contractors were used – one for the flat areas and one for the free-form area.
While the steel members of the exoskeleton internally are planar, the cladding envelope warps and twists to accommodate the reference surface geometry, and maintains a consistent offset from the glazing. A complex system of bracketry was needed and had to fit within a very tight cladding zone, allowing for fire protection and tolerances of the exoskeleton.
Work on the façade design started in 2012, and installation two years later. ‘It’s been a long time in design and construction,’ says Cameron. In June this year, guests were welcomed into the hotel’s 772 rooms and suites, its casino and function spaces, and were finally able to appreciate the façade of this remarkable building.
Project Team
Client: Melco Resorts & Entertainment
Design architect: Zaha Hadid Architects
Executive architect: Leigh & Orange
Façade and structural engineer: BuroHappold Engineering
MEP: JRP
Main contractor: Dragages HK
Façade contractors:
■ Jangho (flat glazing)
■ Kyotec Group (free-form glazing and free-form exoskeleton cladding)
■ Hacely (flat exoskeleton cladding)