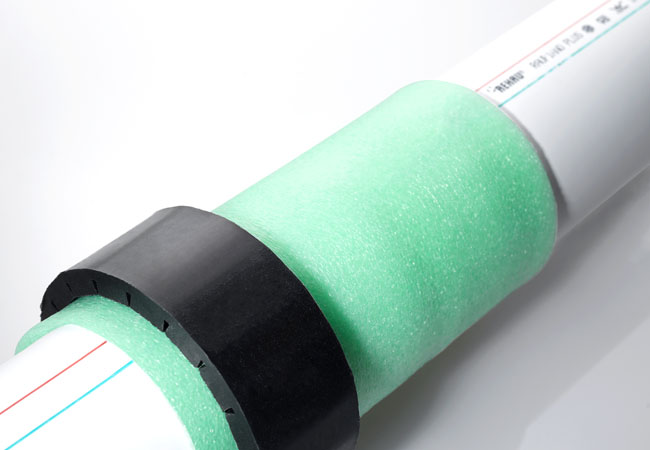
The fire-stop collar minimises acoustic bridges
Today, many people live in close proximity – London has 3,900 residents per square mile. These people are often living in expensive properties and, rightly, expect a quiet environment when they come home.
This expectation goes beyond the multi-residential sector – it applies to hospitals, hotels and offices too. The sounds caused by water vibrations in internal drainage are expected to be silenced at installation stage.
This is not always the case, and a lack of legislation is partly to blame. Part E of the England Building Regulations states a minimum airborne sound reduction target for the noise transfer from one room to another. Specifically, it mandates that airborne sound transfer from one flat to another must be reduced by at least 43-45 decibels (dB) through the separating wall or floor.
But the issue of building service noise is not addressed. Verification on site is carried out without the water running, so problems are often identified retrospectively once tenants are in place. This is more difficult, time-intensive and expensive to fix.
Many countries specify that a building’s technical services must not exceed an absolute decibel level. For reference, 20dBA is an acceptable sleeping room ambience, and 80dBA is the level of ordinary traffic. It is therefore important for consultants to specify above the UK regulatory standard, and for contractors to consider this at installation. Lower specification builds will doubtfully employ an acoustic consultant, so M&E engineers need to consider noise at the design stage to avoid costly retrospective identification and reparation issues.
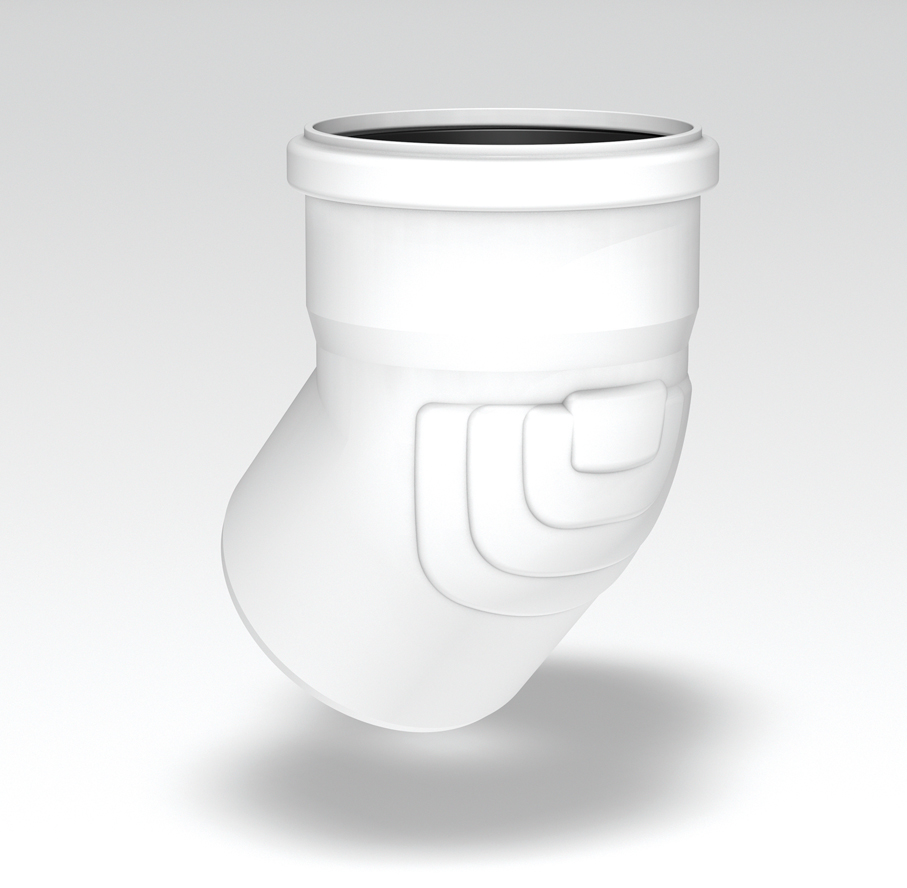
Elbow design minimises vibrations at source
Cavity absorptions, acoustic pipe wrap and acoustic pipe are three methods of insulating against airborne noise. While the first two try to absorb sound, the latter minimises the creation of noise and the transfer of vibrations into the building structure, typically using a multi-layer pipe construction, increasing pipe rigidity and enhancing acoustic properties.
Where possible, it is best practice to avoid noise creation in the first place. This starts with the design process – ideally, systems should be designed with minimum changes of direction. Sharp bends in piping can make a system susceptible to water-initiated vibration as fast-flowing drainage hits the pipes creating ongoing reverberations.
When space is limited and a design void of sharp bends is impossible, it’s vital to ensure the elbows and branch fittings are capable of minimising vibration. Reinforced corners will help, while heavier materials can help dampen noise. Although cast iron can mitigate this problem, it is costly in terms of both the material and its handling on site.
Bracketing is another important consideration for M&E engineers, who should ensure use of recommended bracketing without being swayed by cost. While a lesser product could cut cost, it will not necessarily be helpful in the long term.
When the bracketing is supplied as part of the system, additional aspects have to be considered during installation. When fitting, it is important to avoid direct contact between the pipe and building structure – failure to separate the stack sufficiently from the building fabric is a common problem.
To minimise structure-borne sound transmission to the installation, rubber inserts for walls can be part of a fitting offering a firm and tight grip on the pipe to lower sound into the building structure significantly. Engineers should also select fire collars that have been tested with an extra foam insert creating sound-dampening effects between the pipe and the collar.
Selecting the correct products and installing a complete system with its related components – and tackling potential noise problems during installation – will solve most long-term issues.
Franz Huelle is technical manager for building solutions at Rehau