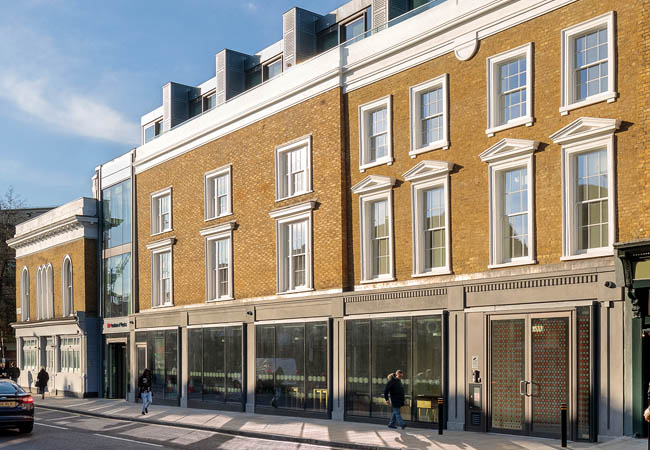
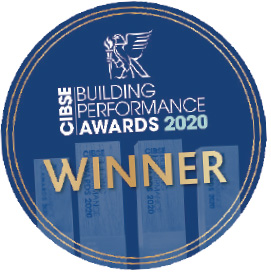
The Institute of Physics (IOP) has an ambition to become a more public-facing organisation, showcasing the impact of physics on the way we live our lives. It’s a philosophy the institute was keen to realise with its new £13m headquarters building in the Keystone Crescent conservation area of London’s King’s Cross.
This five-storey, 1,488m2 net internal area scheme has been constructed behind a retained brick façade. It features: a basement lecture theatre, exhibition space and plantroom; a ground-floor reception and exhibition area, with workspaces and facilities for local start-up businesses; two intermediate floors of offices; and a top floor of seminar rooms and a council chamber.
The HQ houses education and exhibition facilities for the institute, but its building services feature extensive metering and measurement, so turning the building into a ‘living laboratory’.
‘We created a higher-spec BMS with multiple monitoring points, over and above what would generally be required to operate the building,’ says John Edmondson, associate director of Aecom, the scheme’s MEP engineers.
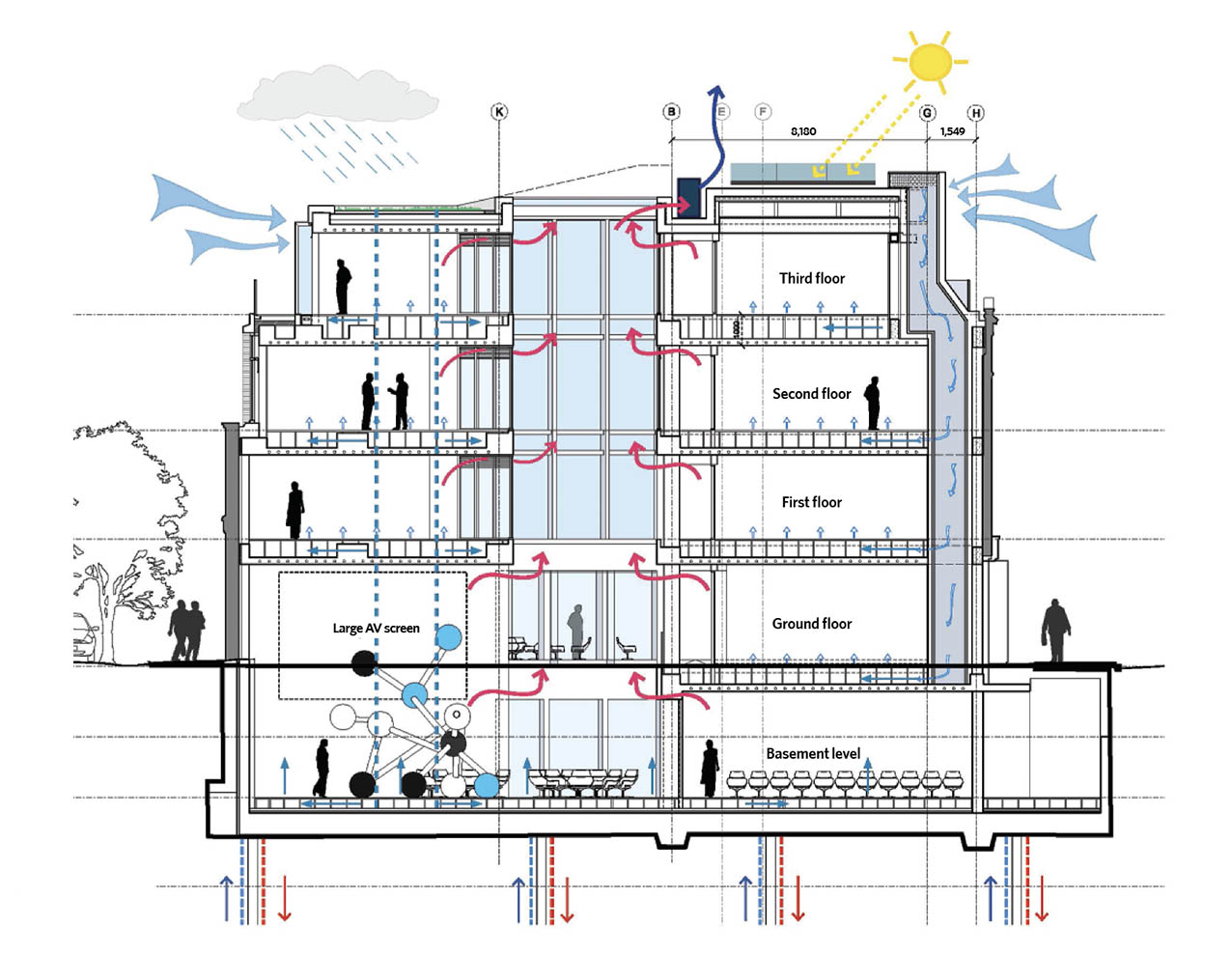
Section of the IOP’s headquarters
In addition to using the data generated for the day-to-day operation of its headquarters, the IOP is working with partner institutions to enable access to the data for academic study, which will help inform building design and operation for the future. As well as being a living laboratory, the building is a demonstration of sustainable engineering. ‘The client wanted it to be highly sustainable and innovative, and to showcase physics and technology in general,’ says Edmondson.
Aecom’s initial proposals included literally showcasing the engineering, with a glazed plantroom wall opening onto the lecture theatre, with thermochromic paint on the pipework and plant. However, cost and acoustic issues meant the proposal would have been prohibitively expensive.
Project team
Client: Institute of Physics
MEP and structural engineer, façade engineering, geotechnical engineering, acoustics, fire engineering: Aecom
Architect: TateHindle
Contractor: Murphy
Ground source heat pump specialist: GI Energy
Planning consultant: Daniel Watney
Project managers: Colliers
Aecom’s actual solution is far more pragmatic. It is based on a mixed-mode ventilation system, exposed thermal mass, adaptive set-point controls and an innovative geothermal pile heating and cooling system using Geokoax ground heat exchangers – the first time the system has been used in the UK.
‘The IOP wanted to minimise its impact on local air quality and on the city centre heat island effect, so it opted to use electricity as the main heat-generation medium, rather than onsite combustion. This leant itself to a ground source heat pump-based heating and cooling solution,’ explains Edmondson.
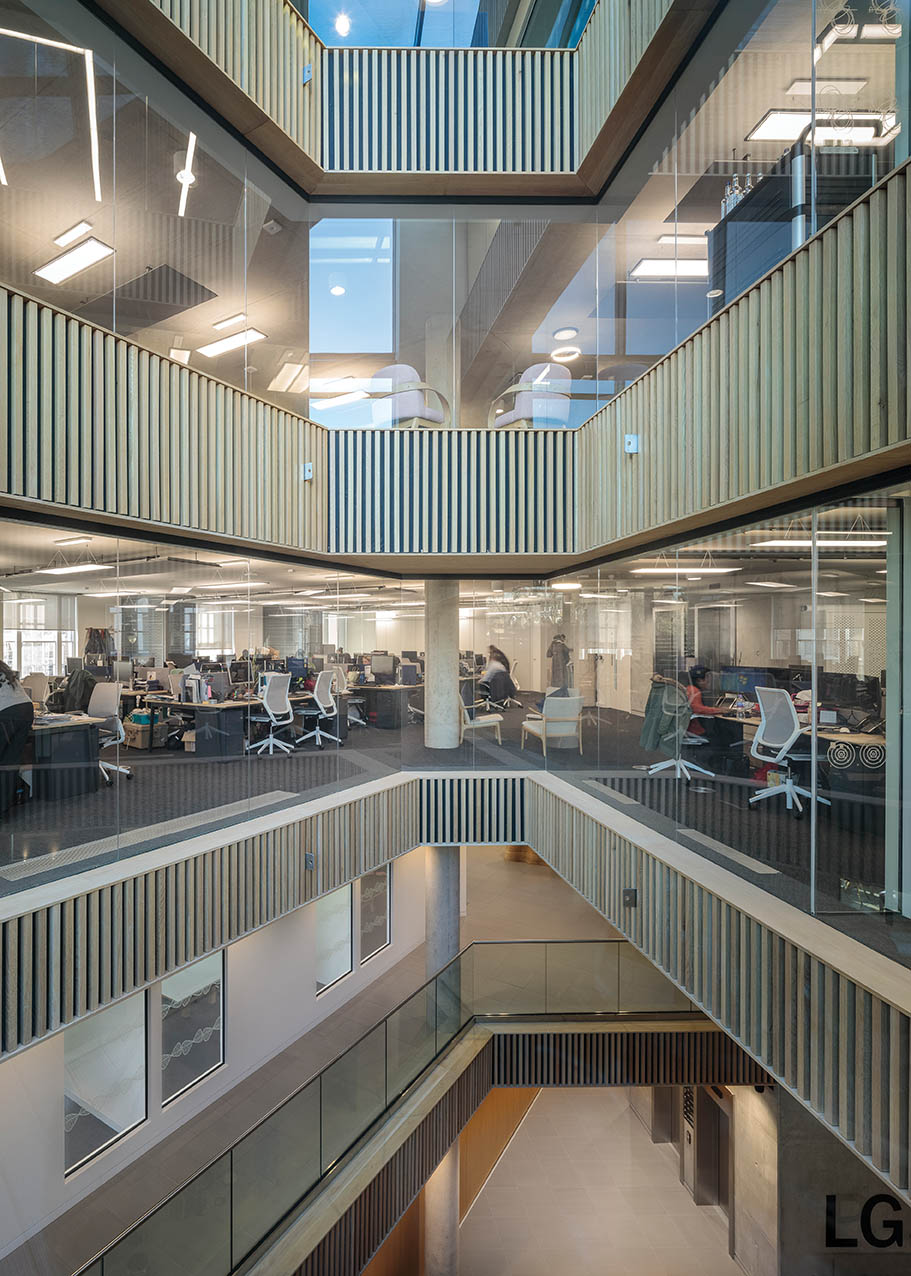
Open-plan offices are situated on mid-floors, while seminar rooms and a council chamber are located on an upper floor
The site’s location, in a conservation area, prevented a heat-rejection plant from being installed on the roof – although a small PV array was permitted – so all cooling had to be provided by the borehole system. ‘It focuses your mind if you know that all you have to provide cooling is a borehole system,’ Edmondson adds.
The Geokoax ground heat exchangers are unusual in that their design enables the area of heat exchanger in contact with the ground to be double that of more conventional borehole systems. In a conventional ground source system, a loop of plastic pipe, usually about 32mm in diameter, is threaded down a vertical borehole before being encased in grout to ensure the pipe is in contact with the ground. A heat transfer liquid – usually glycol or brine – is pumped through the pipe to pick up heat from the ground.
By contrast, these heat exchangers are based on a 130mm-diameter, coaxial, pipe-within-a-pipe arrangement, with the smaller return pipe housed within the larger flow pipe. The heat transfer fluid is pumped down the annulus formed between the heat exchanger’s larger-diameter outer shell and inner return pipe.
This coaxial arrangement significantly increases the surface area of the heat exchanger in contact with the ground, which is the surface where energy transfer takes place.
To maximise the rate of heat exchange, the probes incorporate helical blades, called turbulators, in the annulus. The turbulators are designed to create turbulence in the heat-transfer fluid, because heat exchange between a fluid in motion and a pipe wall is greater if a liquid is in turbulent – as opposed to laminar – flow. The turbulators, it is claimed, do not significantly increase pumping resistance.
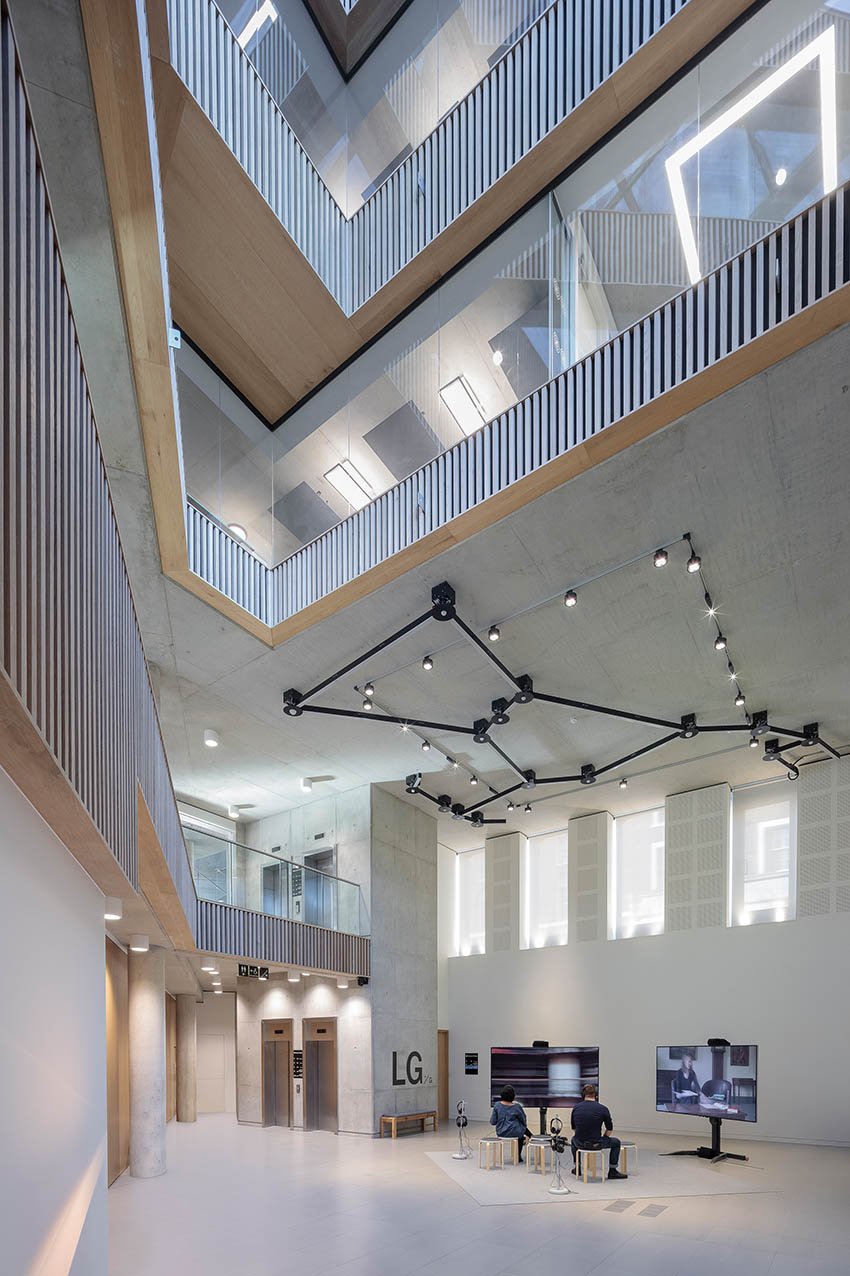
The atrium design minimises the need for artificial lighting
Another advantage of the coaxial heat exchanger design is that the heat exchangers hold around 13 times more fluid than a conventional plastic-pipe-based borehole system. This ensures that, for the same pumped flowrate, the heat-exchange fluid will travel through the annulus at a much lower velocity, increasing the time for heat transfer.
The manufacturer also claims that the increased volume of water boosts the thermal capacity of the system, thereby reducing the number of times the heat pump needs to cycle on and off, improving its performance and lifespan.
The heat exchanger’s improved thermal performance enables the depth of borehole required for the IOP’s new headquarters to be reduced from 200m (for a conventional thermal pile system) to just 75m, saving on drilling time and cost.
‘This was an extremely constrained site in which to drill 10 boreholes, but the system meant the drilling for each borehole could be limited to one day, as opposed to up to the two days it would have taken for a conventional system,’ says Edmondson.
The ground source heat pump (GSHP) supplies heating and cooling to the building via underfloor air handling units (AHUs) and perimeter trench heaters. In spring and autumn, the building has been designed to maintain comfort conditions using fresh air alone when conditions allow, with what Edmondson describes as an ‘oversized’ ventilation system to maximise free cooling during the shoulder seasons.
Outside air is drawn into the building through rooftop intake chimneys, where it is less polluted. The chimneys catch the wind and use positive pressure to drive the air down large vertical ducts, which have been integrated into architect TateHindle’s design.
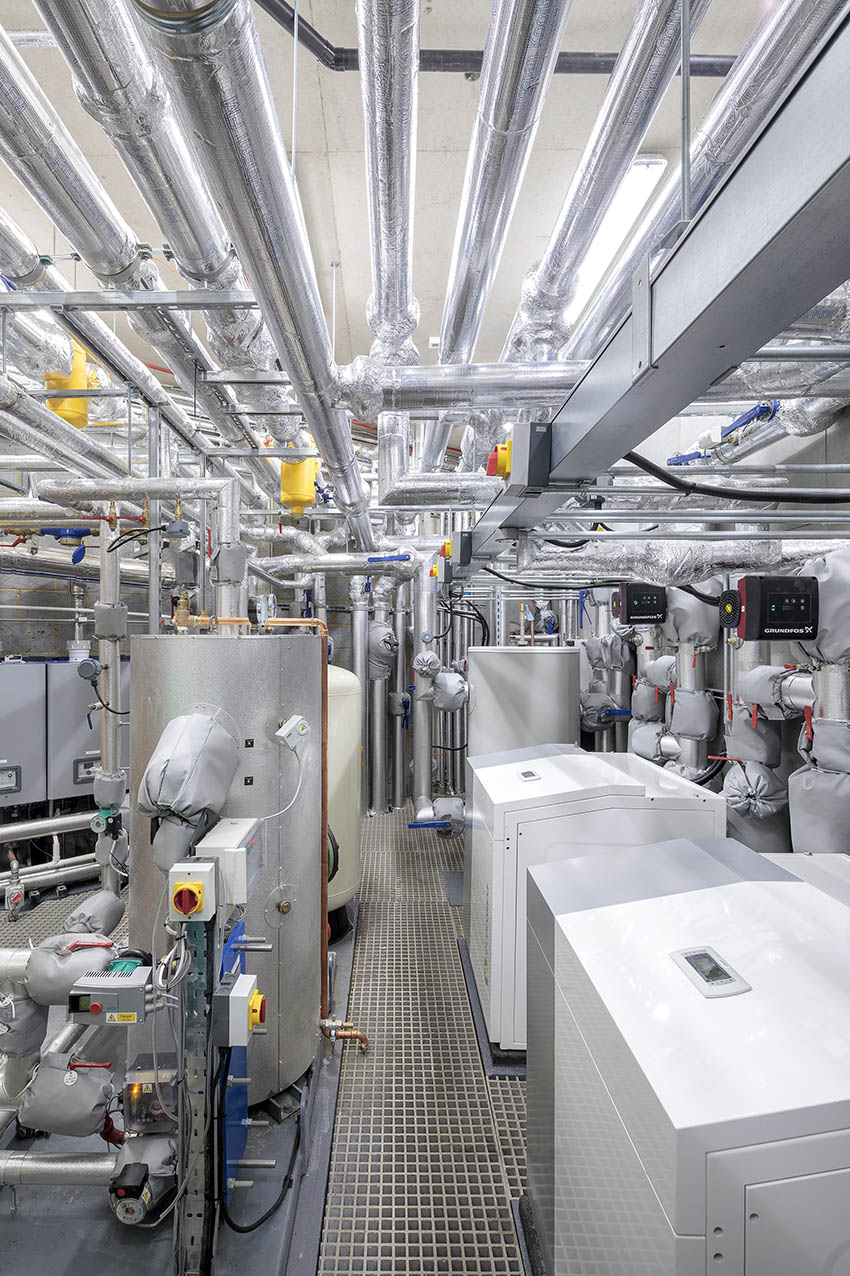
Cost prevented the plantroom from opening on to the lecture theatre
The fresh air is distributed on each floor via an underfloor plenum. This houses a mini AHU incorporating a fan and heating and cooling coils. The AHU is supplemented by a perimeter trench heating and cooling system, designed to deal with heat gains and losses at the façade.
Air rises and exits the floors into a full-height atrium, where buoyancy will cause it to rise. An AHU on the roof pulls the vitiated air from the building. A run-around coil removes useful heat and coolth, and uses it to temper the fresh air at the intakes.
Aecom used dynamic thermal modelling to determine how much free cooling was available from the ventilation system. ‘We increase the volume of fresh air drawn into the building until it reaches the point where it is more energy efficient to turn down the fans and to use cooling coils,’ explains Edmondson.
In summer, the GSHP supplies chilled water to the AHUs and perimeter coils at a flow temperature of between 9°C and 14°C, with a return temperature of 17°C. Fresh air rates are minimised in summer and winter based on CO2 levels. In addition, the building’s reinforced concrete superstructure has been left exposed on the soffit of each floor to add thermal mass to the spaces and help mitigate peak summer temperatures.
In winter, the GSHP is the primary source of heat for the building. It supplies heat at 40°C flow (30°C return) to the underfloor AHUs and perimeter heaters. Gas-fired boilers (80°C flow/60°C return) provide top-up heat for cold mornings and heating back-up should the heat pump fail, in addition to heating the domestic hot water.
The geothermal system appears to be working well. Summary data for the first year’s operation show the system has an annualised combined coefficient of performance (COP) of 3.4, although this figure is expected to improve over time as systems are optimised. (See panel, ‘Successful commissioning’.)
Successful commissioning
Aecom is working with the design and build contractor, Murphy, and the client to get the seasonal commissioning right to ensure systems are optimised. ‘One of the strategies we agreed with the Institute of Physics to help minimise peak heating and cooling loads was to use adaptive comfort control, to enable the internal temperature to swing in a manner similar to that of a naturally-ventilated building,’ says Edmondson.
Occupant satisfaction questionnaires were used to garner users’ feedback on internal conditions and to track control modifications. ‘Initial feedback was important when making adjustments to the set points to achieve a base occupancy comfort aligned with the adaptive comfort standards,’ adds Edmondson.
The strategy of no combustion and limited heat rejection makes this building years ahead of its time. Its use of electricity to generate heating and cooling is prescient, given the likely move away from gas as fuel for heating for non-domestic buildings in forthcoming changes to the Building Regulations.
At the time the project was designed, the carbon factor for electricity was 0.519kgCO2.kWh-1 in both the London Plan and in the Building Regulations. Now, however, legislation is catching up with decarbonisation of the electricity grid. The carbon factor of grid electricity has recently been lowered in the London Plan to 0.233kgCO2.kWh-1, to reflect the increased contribution made by renewables – so, on paper, the Institute of Physics’ headquarters would appear to perform significantly better now, in terms of carbon emissions, than it did at the time of its design.
It is precisely because the building services design is ahead of its time that this is an appropriate headquarters for an organisation with a mission to showcase the value of physics to society. It is also what made the scheme a worthy winner of Commercial/Industrial Project of the Year at the CIBSE Building Performance Awards.
Lighting physics
In addition to providing a ventilation path, the atrium allows daylight to flood the floor plates to help minimise the need for artificial lighting. ‘It’s a huge north light that allows daylight to flood the building,’ says Edmondson. The lighting system includes addressable and dimmable controls, and the lighting was modelled using dynamic analysis to ensure optimum illumination with minimum luminaires. The controls ensure light levels are lowered when spaces are unoccupied, to help save energy.