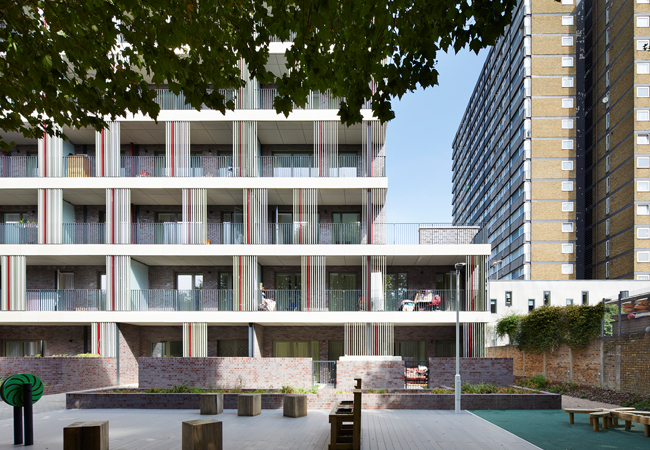
Balconies control solar gain and allow Agar Grove apartments to enjoy large amounts of natural light
If all residential projects were like this, people would be very happy!’ That was the verdict of the judges at this year’s CIBSE Building Performance Awards, where the Agar Grove Estate Regeneration Phase 1A won Project of the Year – Residential. ‘The M&E design is great, the architectural design excellent, and the pre- and post-occupancy evaluation very thorough,’ said the judges, who might also have added that, when completed, the redevelopment will be one of the largest residential Passivhaus schemes in the UK.
Agar Grove Estate Regeneration is the redevelopment of a 1960s North London housing estate in the borough of Camden. It is a project in Camden Council’s Community Investment Programmme, designed by Hawkins\Brown and Mae architects in consultation with the tenants, with Max Fordham providing M&E and Passivhaus services. The architects’ masterplan is based on a layout designed to reinstate the area’s established street pattern, with the addition of community spaces and gardens. To help fund the metamorphosis, the masterplan has increased the development’s density. This has involved demolishing tired, low-rise buildings and replacing them with new energy-efficient council homes, plus the sale of new-build and refurbished flats on the open market.
The scheme will be redeveloped in six phases, to enable the smooth decant of existing residents; allowing residents to move in when a new block is completed, releasing their old block for demolition. When the project is complete, it will provide 507 new homes, of which 359 are set to be built to Passivhaus standards.
Passivhaus is a fabric-first approach to delivering energy-efficient homes. For a building to be classed as Passivhaus, one of the key targets is that it must have an annual heating and cooling demand of less than 15kWh·m-2. The design-check-improve process is central to certification – the building’s design, construction, components used and commissioning process must all be certified, which is why Passivhaus schemes perform as designed. ‘The rigour associated with Passivhaus is a good way of closing the performance gap,’ says Katie Clemence, senior engineer at Max Fordham, the project’s building services engineer.
Project team
Architects: Hawkins Brown; Mae; (Architype)
Main contractor: Hill
Structural engineer: Peter Brett Associates
Services engineer: Max Fordham (Robinson Associates)
Passivhaus consultant (designer): Max Fordham (Architype/Elemental Solutions)
Passivhaus certifier: Warm
Landscape architect: Grant Associates
Project manager & QS: Arcadia
The assured performance was a big attraction for the London Borough of Camden in its redevelopment of Agar Grove. The energy efficient construction associated with the standard would ensure residents’ fuel bills are kept to a minimum – helping tackle fuel poverty and carbon emissions – while the fabric first approach reduces the need for complex technical solutions, and the enhanced build quality should reduce long-term maintenance costs.
At the time the masterplan was being developed (2013), Passivhaus had not been applied to an inner city scheme of this scale in the UK, so Max Fordham set out to analyse its feasibility. One of the biggest challenges faced by the firm was that the development was subject to planning rules that were not always compatible with Passivhaus principles. For example, the Greater London Authority (GLA) was pushing for the scheme to have a CHP engine connected to a district heat network, which linked together all buildings on the development. The problem with this approach is that heat losses from the district heating’s distribution pipework would have increased the scheme’s primary energy demand beyond what is acceptable under Passivhaus.
‘We determined that this option would result in high distribution losses from the unavoidable need for longer heating pipe routes, resulting in a system with low efficiency,’ says Clemence.
As an energy efficient alternative, Max Fordham developed a scheme based on Passivhaus with communal heating provided by gas-fired boilers on a block-by-block basis. When it compared the block-based scheme with one based on CHP and district heating, the comparison showed life-cycle costs to be broadly comparable; while the Passivhaus option had a higher initial capital cost, it worked out to be better value over the scheme’s anticipated 60-year lifespan.
When the engineer compared the carbon emissions associated with the two options, the benefits of abandoning CHP and district heating in favour of Passivhaus and communal heating became starkly apparent.
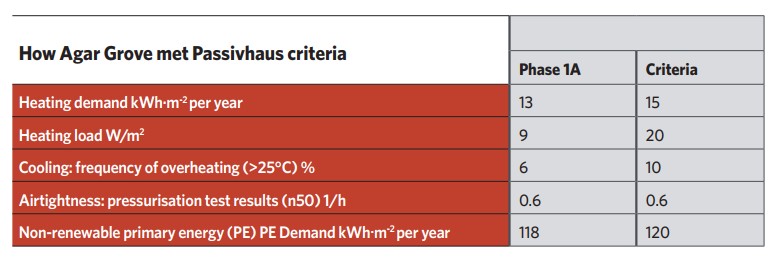
Planning policy in London requires a scheme to meet challenging carbon targets, and compliance is assessed using SAP methodology. At the time, SAP included an assumption that heat losses from a district heating network were 5% of the network’s total generated heat. Max Fordham was sceptical about this, so looked at a number of actual district heating case studies for Passivhaus and non-Passivhaus developments. These indicated average network losses to be around 50% of the total generated heat – 10 times more than the figure used in SAP. ‘SAP’s 5% heat loss assumption was a significant factor in making district heating look a more favourable option,’ explains Clemence. When the scheme was modelled using more realistic heat losses, Max Fordham found the Passivhaus option used less energy and emitted less carbon. As a result of the detailed analysis, the GLA gave the Passivhaus option the go-ahead.
“Resident feedback on summer temperatures was mixed, prompting Camden to educate some residents on the benefits of lowering window blinds and keeping windows closed during the heat of the day”
The first block to be completed was Phase 1A, an £11.5m development of 38 social rented Passivhaus homes. Architect Hawkins\Brown optimised the building’s form to help minimise heat losses. The window-to-wall ratio was set at around 35% to limit summer solar gains without the need for solar control glass. Architype, the delivery architect for main contractor Hill, worked with Max Fordham and Warm, the project’s Passivhaus Certifier, to simplify construction detailing to make it easier to build to Passivhaus.
The block, comprising a ground floor and six storeys, is supported on a concrete frame, with an infill of brickwork chosen to blend in with the local vernacular. On the roof is the communal plantroom complete with four gas-fired cascade boilers supplying several flow and return risers. Each dwelling contains a heat interface unit (HIU), which connects directly to the riser by short pipework legs on each landing.
The traditional solution for riser distribution at the time would have been to use a single heating flow and return pipework riser per block, connected to the HIU in each apartment via pipework legs snaking out above each of the block’s communal landings. Max Fordham proposed an alternate solution involving a number of vertical risers next to apartments (three per block) to reduce the heat losses associated with lateral pipework. When Warm came on board, it expressed concerns that heat losses from Max Fordham’s rationalised communal heat-distribution pipework would still be too high for Passivhaus. ‘We were nervous about the communal heating system meeting the primary energy requirement of Passivhaus,’ says Sally Godber, a director at Warm.
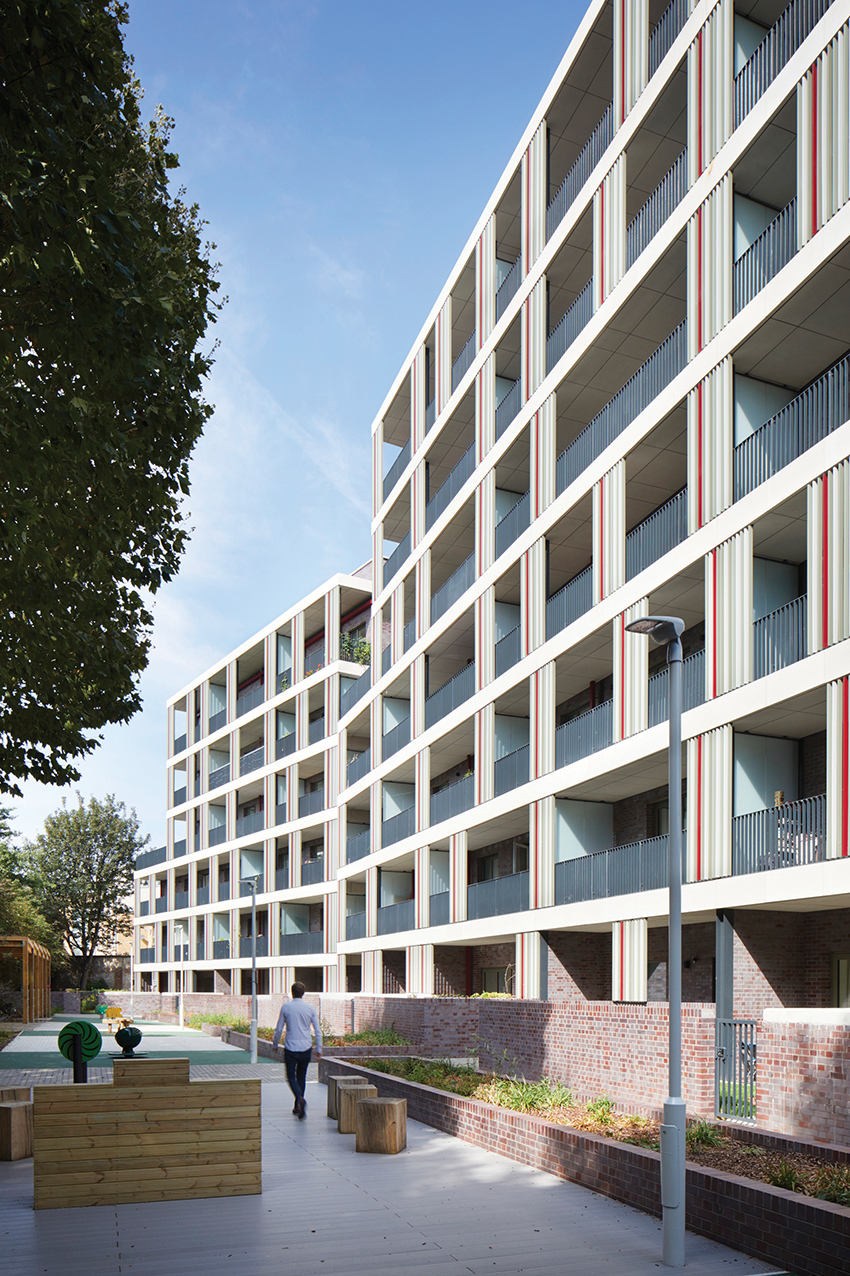
Warm worked with Max Fordham to model the risers in Passivhaus Planning Package (PHPP). This showed the distribution pipes were responsible for 45% of the system’s heat loss, while the HIU was responsible for 33%. ‘A key driver for us was to cut down on distribution losses of the system by reducing pipe lengths, reduce losses from the HIUs to get the flow and return temperatures down,’ says Godber.
To reduce the connection lengths, Warm proposed further reconfiguring both the riser and the apartment layouts. ‘We were fortunate that we were involved early enough in the design to be able to suggest changes to the floor layouts,’ says Godber.
The final distribution strategy meant that the majority of pipework was vertical, rather than horizontal, and the apartment layouts were adapted so the HIU in each dwelling was adjacent to a riser. ‘These changes served to cut the effective length of pipework and its corresponding heat loss in half,’ says Godber. (See panel, ‘Distribution heat losses’.)
Max Fordham selected HIUs with the minimum heat losses. Direct HIUs were chosen to eliminate the flow temperature drop associated with a heat exchanger, which allowed the entire system to run at a lower flow and return temperature. The HIUs provide space heating to the apartments via a single radiator in the living room and a heated towel rail in the bathroom.
Communal MVHR
The fabric-first approach results in a building envelope that is extremely well insulated and airtight. As a consequence, the apartments require an efficient mechanical ventilation system with heat recovery (MVHR) to ensure good air quality in the flats. Fresh air is provided to the bedrooms and living room, with stale air extracted from the kitchen and bathroom.
Agar Grove Phase 1A is one of the very few schemes to make use of a communal MVHR system based on roof-mounted air handling units. There are many pros and cons of central and decentralised ventilation. Godber says the most significant plus for centralised ventilation is the access for maintenance by Camden: ‘Filter changes are a real problem for decentralised systems because access is required to each dwelling. In comparison, Agar 1A has only two AHUs, so only two filters to change; it also helps that those two filters are very large, so they last longer and, because they are fitted with pressure sensors, they send an alarm when they need changing.’
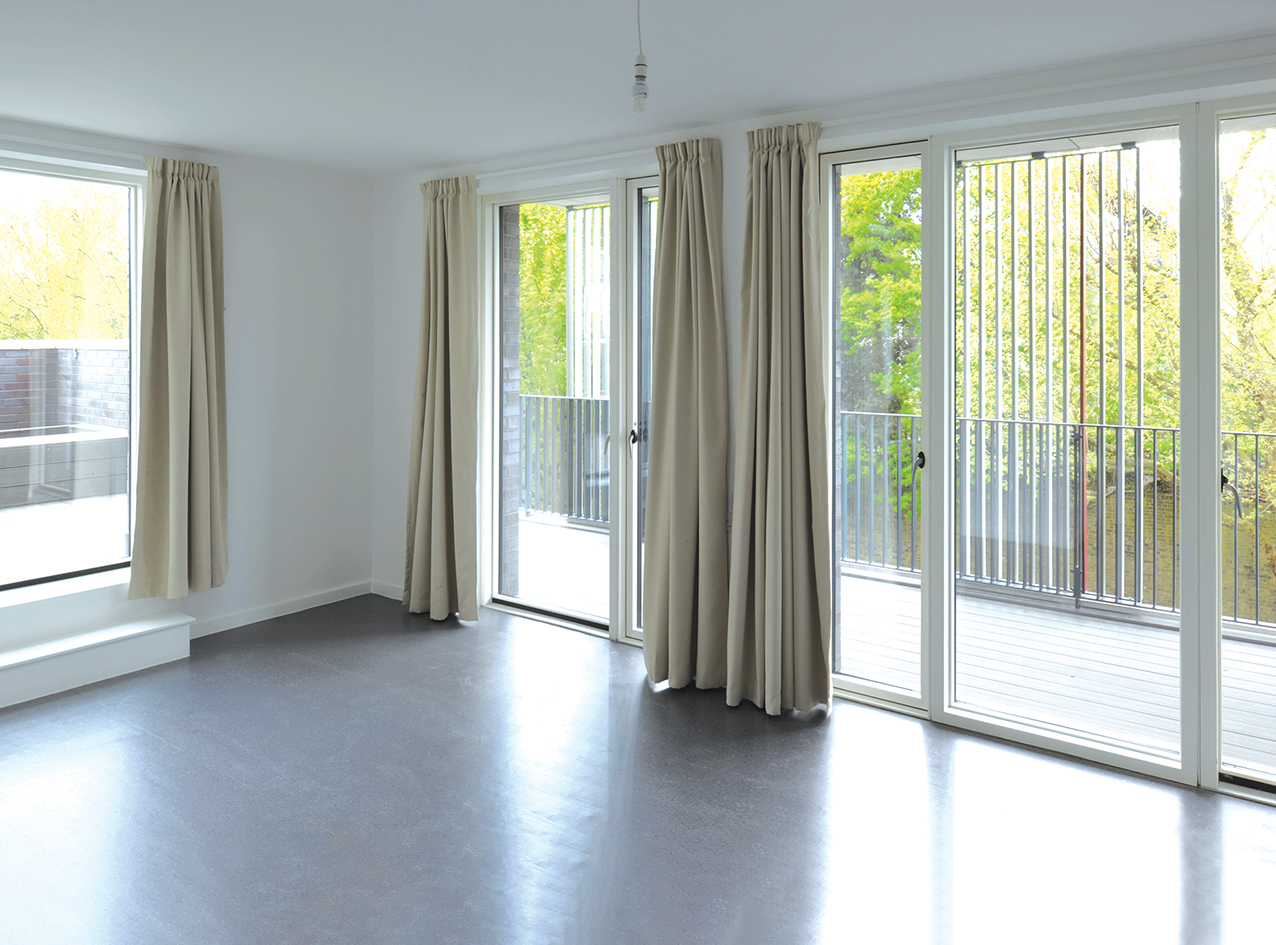
The system offers enhanced air quality in the flats because it enables less polluted air to be drawn from the roof rather than through the façades closer to the street. The arrangement also ensures the ventilation unit cannot be switched off by residents, so it will always operate as designed; and it can be maintained without access to the flats.
The downside of communal MVHR is that it places additional constraints on the layout because ducts must drop vertically down the building. Because apartment walls are generally part of its fire compartmentation, ducts also need to be fitted with fire dampers at this intersection. The ventilation system operates continuously, so Robinsons, the contractor’s MEP consultant, took great care over the design to minimise system pressure loss. Godber says design static pressure was 101Pa, and the system’s measured static pressure was close, at 115Pa. ‘This is low, especially for a VAV system where commissioning engineers often ramp up the static pressure to about 400Pa to make it easier to set the controls,’ says Godber. ‘We were pleased with the result being so close to the design, which demonstrates a great installation and shows the value of the quality assurance Passivhaus certification brings.’
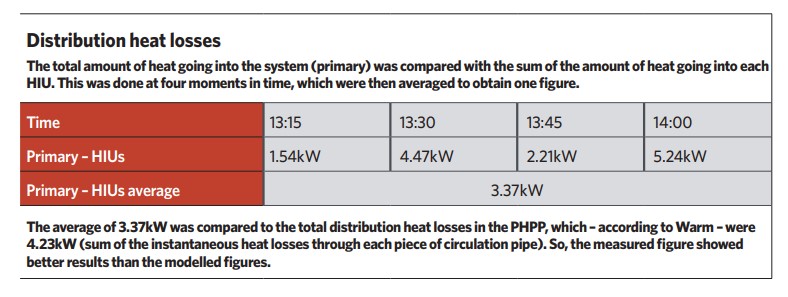
A major challenge of any new development in urban environments is the control of solar gain and overheating. The masterplan was developed to stitch the scheme into the neighbourhood streetscape, so the blocks are not always orientated in the optimum direction for solar control. Fortunately, Phase 1A was orientated north-south, which helped the designers manage solar gains in the most economical manner.
At the time Phase 1A was being designed, there was no specific methodology on how to analyse overheating in housing, so Max Fordham created a strategy to appraise the risk and ensure the design could adapt. Modelling was carried out using the Islington 2030 DSY from the Prometheus probabilistic weather data website. The results were compared against CIBSE TM52’s adaptive overheating criteria.
The modelling determined that living rooms would not overheat providing the windows could be opened during occupied hours. On noisier façades, large openings flush heat from the spaces quickly, preventing the need for windows to remain open for long. Control of overheating was also helped by the majority of apartments being dual aspect, allowing the cross-flow of air. In addition, external balconies have been integrated into the design to help control solar gain. ‘In mid-summer, the balconies block out the high sun, but heat from lower-angle sunlight can enter the dwellings in winter,’ says Clemence. It is a solution that enables the flats to enjoy high levels of natural light while avoiding overheating.
Phase 1A was completed in April 2018. To help residents adapt to their new low-energy homes, the contractor, council and their design teams created guides to explain how their Passivhaus home operated, including guidance on the use of ventilation three-speed control. As part of Camden’s ongoing support to residents, occupant feedback enabled Camden Council to identify how residents could make their homes more comfortable (see panel, ‘Occupant feedback’).
Future phases
The CIBSE Award was for Phase 1A, and the design team adopted a similar approach to ensure Passivhaus compliance for Phase 1B. Detailed design of Phase 1C is about to start; its design has evolved significantly in response to changes to the carbon factors for gas and grid electricity. ‘The carbon factors have changed, so the energy strategy of having communal boilers in the blocks will shift to one based on a heat pump solution,’ says Scott Crease, senior partner at Max Fordham.
The design team is looking at an installation based on an ambient loop system, such as Dimplex’s Zeroth or Daikin’s Altherma Geo3. The ambient loop will have a flow temperature of about 25°C. A water source heat pump in each apartment will draw heat from the ambient loop for space heating and domestic hot water. ‘It’s a more expensive solution, but – in carbon and energy terms – it is completely the right solution,’ says Crease.
Phase 1A of Agar Grove proved that Passivhaus principles can be applied successfully to large-scale residential developments. Phase 1C is set to take large-scale low energy housing to a new level.
• The CIBSE Building Performance Awards 2021 are now open for entries. Visit cibse.org/bpa