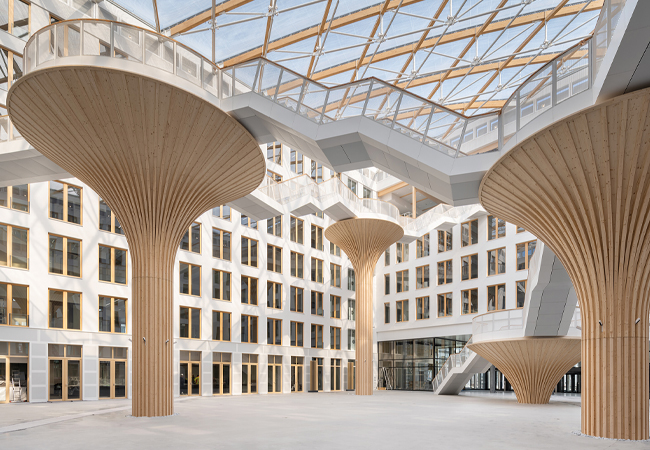
The Edge Suedkreuz development in Berlin was designed using nature-based architectural elements
Characterised by its atrium of flying staircases and timber-clad concrete ‘trees’, the Edge Suedkreuz development in Berlin is inspired by an open ecosystem. Bringing nature-based design into the workspace, sustainability and occupant wellbeing were a key focus for the building.
Berlin-based architect Tchoban Voss Architekten worked with Buro Happold, structural and sustainability consultants, as MEP on the project. The scheme comprises two buildings, the smaller Solitaire Building and the larger seven-storey Carré Building – the focus of this article – which is occupied by German energy supplier Vattenfall.
The sheer number of timber beams on the office floors cover almost 40% of the soffit, restricting space available for the installation of building services
One of the Carré Building’s features is that it was built using an innovative modular timber-concrete hybrid structural system by CREE Buildings. The system was adapted by Buro Happold for this project to deliver on the developer’s modular and sustainability aspirations.
‘Edge wanted to explore the use of prefabrication to help speed construction, while increased use of timber helps reduce the amount of carbon embodied in the building and, where visible, using natural materials helps to create a more desirable office environment,’ says Martin Elze, associate director of Buro Happold.
Timber is visible throughout the building: it includes timber-framed
floor-to-ceiling windows, trussed timber roof beams in the giant central atrium and, most significantly for the MEP engineers, exposed timber beams on the office floors to support the concrete deck of the floor above.
The sheer number of timber beams on the office floors, closely spaced at 1.35m centres, cover almost 40% of the soffit, restricting space available for the installation of building services. ‘Because the space for installing the services was reduced, it was important to use a highly efficient, well-coordinated building services solution to provide heating, cooling and ventilation,’ says Elze.
The solution to keeping the office floors comfortable was developing a bespoke,
high-capacity hybrid active chilled beam. The hybrid chilled beams have a fresh air connection with a heating/cooling coil. Two units are designed to slot between each structural timber beam, measuring 8,100mm long and – together – 800mm wide.
The units provide fresh air and sensible cooling and heating to the floors through a combination of induction and forced convection. The designed summer maximum temperature is 26°C for the offices. Elze says each of the units can produce up to 120W·m2 of cooling, or an average of about 70W·m2 over a floor plate, which he claims is ‘enough for the majority of office spaces’.
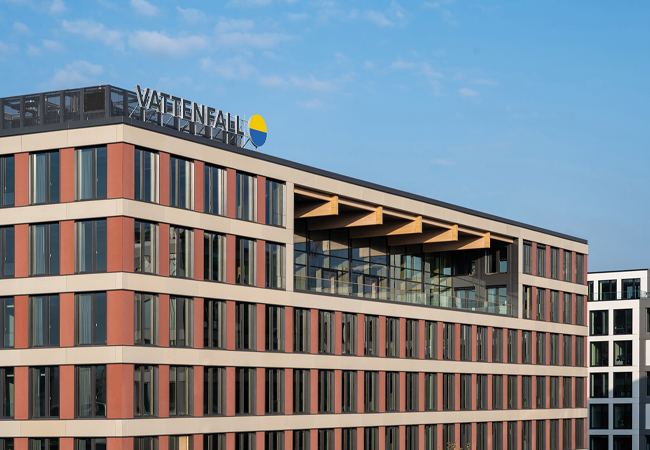
The seven-storey Carré Building in Berlin
Office floors are designed to be predominantly open plan, so chilled beams are controlled in pairs, enabling conditions to be varied every 2.7m. ‘You have the opportunity to install additional valves to control the units individually, which would allow a partition to be installed every 1.35m if needed, so it’s a super-flexible solution,’ says Elze.
The high-capacity chilled beams also incorporate LED lighting and acoustic absorption along with some of the 17,000 sensors installed in the building, including presence detection and CO2 monitoring to control fresh air supply rates. The LED lighting, manufactured by Signify, is bespoke to this project. ‘Standard luminaires would not fit into the ceiling panel,’ Elze explains.
In common with other Edge buildings, occupants are able to control their immediate environment from their mobile phones. ‘There is not a single switch in the building, everything is controlled by occupants using an app, so when you go into a room you can use your phone to adjust the temperature,’ Elze says. The building’s smart controls also enable meeting rooms to be pre-cooled, heated or ventilated before a meeting via the central booking system.
Fresh air ventilation rates are based on 45m3·h-1 (12.5L·s-1) to meet WELL Certification requirements. This is about the same ventilation rate as Kategorie II DIN 16798-1 and about 16m3·h-1 more than the minimum Kategorie III requirement. All air is returned to the rooftop air handling units/heat exchanger, via an exhaust air intake adjacent to the return air riser in the building’s concrete core. There is no air recirculation.
The solution to keeping the office floors comfortable was developing a bespoke, high-capacity hybrid active chilled beam
Should any of the building’s 2,100 occupants want to increase the amount of outside air on a floor they have the option of opening a window. The windows are interlinked with the ceiling panels to turn off the heating and cooling. ‘It was a client requirement to have opening windows because people feel better and more in control of their environment if they can open a window,’ explains Elze.
To help limit heat gains on the office floors, the full-height glazing incorporates solar protection film. This incorporates a small mesh to provide shading from inclined sunlight while allowing horizontal views out. ‘It’s a passive system that works like a louvre,’ says Elze.
In addition to the ventilation, the majority of the piped services are distributed to the floor plates through risers contained in the central concrete core. On leaving the riser, pipes and ducts enter the floor plates through the dropped ceiling of the adjacent toilet blocks.
On office floors, the ceiling height is 3.0m to the underside of the wooden beams, 3.05m to the underside of the chilled beams. However, in the toilet areas, the ceiling height has been dropped to 2.3m to create space to allow pipes and ducts to be re-routed before entering the office floor.
Office floor plates are intended to be mostly open plan. There is, however, a central spine on each floor where the ceiling height has been dropped to 2.6m to enable ductwork and pipework to be distributed on the floors. Elze refers to this as the ‘corridor’ because the dropped ceiling follows the same linear route along the centre of the floor plates as a corridor would, should partitioning be installed. ‘There is a 40cm space above the toilets to re-route the services and bring them into order before they go into the corridor dropped ceiling,’ he says.
Internally, all of the office floors are linked by a giant, 1.600m2, 26m-high square central atrium that includes a series of striking timber-clad concrete ‘trees’ soaring up to 15m high. Special care has been taken to ensure a comfortable environment in this area
Cooling the atrium
The central atrium features a series of flying staircases bridging between the fours and four free-standing timber-clad concrete ‘trees’. The tallest of these is almost 15m high, the shortest 4.5m.
This atrium gives the building its character; it provides spaces for both formal and informal meetings, including seating spaces in the ‘trees’, along with seating on the ground floor for the cafe. The atrium also includes a loggia on level 5, where there is a sky lounge and access to an external roof terrace.
Detailed modelling simulations ensured comfort conditions are achieved through a combination of passive and active design solutions. These include moveable foils within the ethylene-tetrafluoroethylene (ETFE) roof pillows (ETFE material is extremely low weight compared to glass and offers exceptional light transmission) to control the amount of solar radiation entering the atrium in both summer and winter. There are also additional openings directly beneath the roof on the north and south elevations to exploit the wind direction to remove hot air from high levels in the space.
To ensure the atrium remains comfortable in summer, Buro Happold amalgamated various cooling systems, including: underfloor cooling; cooling from cylindrical air diffusers in the corners of the atrium; and displacement units set into the floor of the seating areas on the trees.
In addition, cooling units above the entrances supply conditioned fresh air; these are connected to roof-top air handling units via run-around coils.
‘We did a lot of energy studies for the atrium in order to determine what cooling we needed; with energy simulation modelling we were able to trim the cooling down to figures that are sensible,’ says Elze.
Cooling is provided by two hybrid cooling towers mounted on the roof.
Managing the electrical loads
Beneath the building, a giant reinforced concrete underground car park connects the Carré Building to its smaller seven-storey sister, the Solitaire Building. This can accommodate up to 218 cars and 300 bicycles. It incorporates an automated parking system to save space by double-stacking parked cars one above the other.
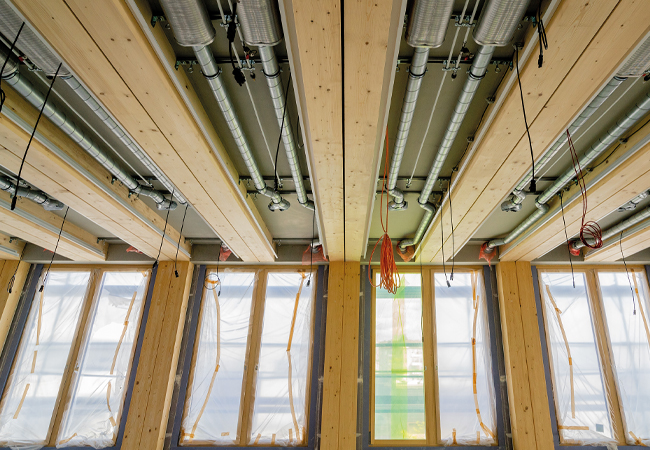
Exposed timber beams on the office floors support the concrete deck of the floor above
Impressively, all the parking spaces incorporate electric charge points. Unfortunately, the city’s electrical infrastructure did not have the capacity to power the building, its kitchen, the building services and to simultaneously charge more than 200 electric vehicles.
The building had a 7.5MW electrical connection, the maximum available. If everything in the building is running, its total electrical demand is predicted to be 6.8MW. Electric car charging adds another 1.5MW, taking total demand over the 7.5MW maximum. ‘For 99% of the time, electrical demand is not an issue, but when the building is fully occupied, it’s lunchtime so the kitchen is running at full capacity, and it’s 40°C outside and the sun is shining, then we may need to act,’ Elze says.
In response, the BEMS constantly checks electrical demand. If it does start to come close to 7.5MW, then the building automatically starts to reduce the charging rate for the cars. ‘We had to introduce some load management, so that on the rare occasions when everything is running, the car chargers will only charge at part speed,’ Elze says.
“The fire brigade is very sensitive when it comes to electric cars because it still doesn’t know the best way to handle them” – Martin Elze
Interestingly, the basement is the only part of the building to have sprinklers fitted. ‘The fire brigade is very sensitive when it comes to electric cars because it still doesn’t know the best way to handle them – especially an entire car park full of them – which is why they have insisted we put in sprinklers,’ says Elze.
Alongside the electric cars, bicycles and sprinkler tanks, the basement also houses two combined heat and power (CHP) engines. ‘We wanted to connect to the district heating in the city, but heat is still produced using coal in some parts of Berlin, so Edge decided to use CHP engines running on biogas to provide all of the building’s heat and additional power,’ explains Elze.
Clearly, sustainability and occupant wellbeing are important drivers for the Edge Suedkreuz. The designers’ innovative response to these imperatives has resulted in the building being pre-certified Platinum by the German Sustainable Building Council and pre-certified Well Gold.