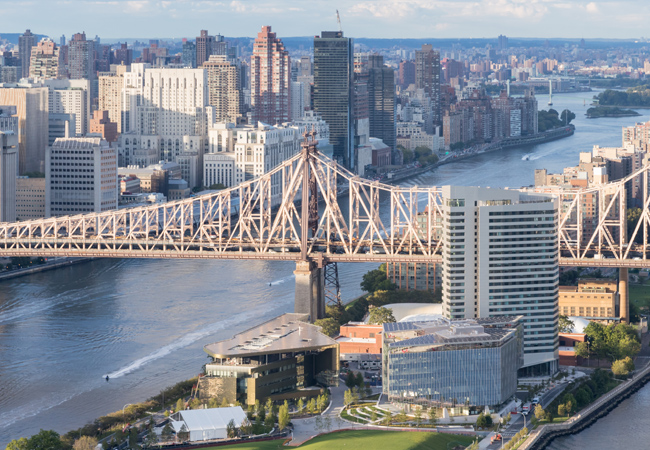
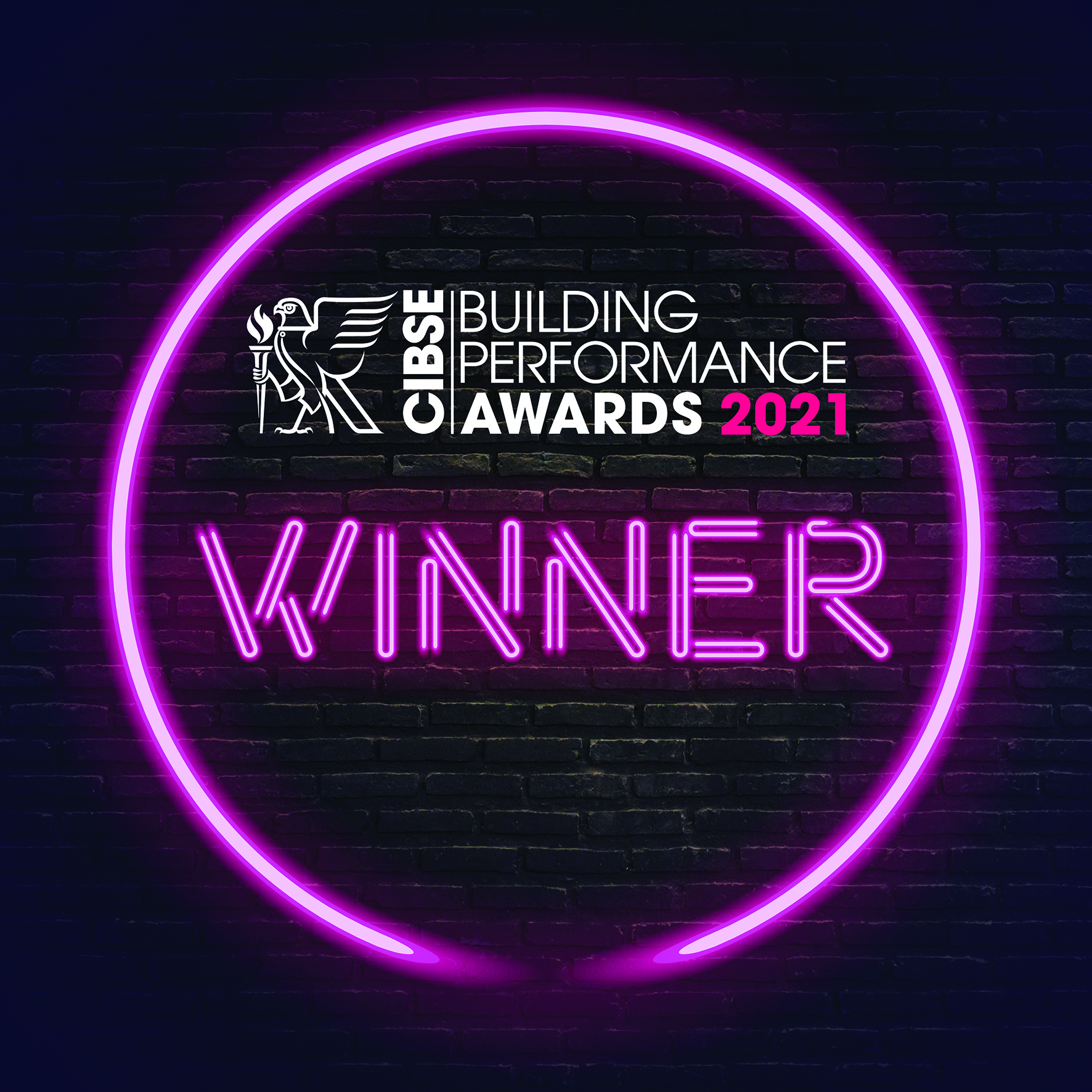
It was the CEO of Hudson Companies who threw down the gauntlet and said “we’re going to do Passivhaus on this project”,’ recalls Julie Janiski, a principal at Buro Happold. The project was a new, 352-unit student and faculty accommodation block for Cornell Tech, the technology campus of Cornell University, being developed in the shadow of Queensboro Bridge on Roosevelt Island, Manhattan, New York City. Hudson Companies was one of the university’s development partners, while Buro Happold was the project’s MEP, structural and lighting engineer, working with Handel Architects to design what was, at the time, the world’s tallest and largest residential Passivhaus building.
Another key member of the team was Steven Winter Associates; the consultant joined the design team as the project progressed, to provide specialist Passivhaus consultancy services. ‘They were familiar with the technology and challenges of designing and building a highly insulated, airtight building envelope,’ Janiski says.
Project team
- Client: Cornell Tech
- Architect: Handel Architects
- M&E and lighting engineer: Buro Happold
- Passivhaus consultant: Steven Winter Associates
- Structural engineer: Buro Happold
- Main contractor: Monadnock Construction
Importantly for this pioneering project, Steven Winter Associates had an established relationship with the Passivhaus Institute in Germany. This meant it was able to have conversations about the details, and how to handle the fact that the building had a different typology from the ones more commonly certified as Passivhaus, such as the single family home.
When it came to developing the pioneering Passivhaus for Cornell Tech, the design team was fortunate that the campus masterplan had conveniently placed the building on an east-west axis, so its principal elevations faced due north and south. ‘The building’s orientation and rectangular form are ideal for minimising east and west exposure to low-angle sun and solar heat gain,’ says Janiski. Although, just to be sure, the team modelled the building in alternative orientations: ‘The impact of changing orientation from facing north-south added up to 15% to its energy demand,’ Janiski adds.
In keeping with Passivhaus principles, and in the context of a climate that spans very cold winters and very hot and humid summers, the building’s envelope is formed from a highly insulated metal-panel cladding system incorporating operable, triple-glazed windows. None of the apartments has a balcony, a feature that helps dispense with tricky airtightness and thermal-bridging details, while making it easier to wrap the insulating façade tightly around the building’s concrete frame.
Low energy heating/cooling
A variable refrigerant flow (VRF) system heats during New York’s winters, and cools during hot summers
- Indoor unit for heating and cooling. Individually controlled by residents
- Outdoor unit
- Metal grill enclosure on mechanical balcony
- South-side refrigerant
- North-side refrigerant
- Each pair of residential floors is served by two stacked condenser rooms: one condenser room serves two floors of north-facing apartments, and the other served two floors of south-facing apartments.
- A metal grille enclosure, painted to echo the façade palette, hides a ‘mechanical balcony’ that houses the outdoor unit for each floor.
- Indoor units in each apartment give residents complete climate control, while individual billing and building dashboards influence behaviour.
The architect has, in fact, taken the ‘wrap’ concept and contrived the façade design to make it appear, visually, as if the building is swathed in an insulating blanket; this seems to start at the vertical louvre on the west elevation, wraps around the building, and then finishes as if tucked behind the same louvre. The feature is most apparent at the top of the building, where a residents’ rooftop lounge is located, and at the building’s base, where the wrapper has been lifted to form an angular canopy over the entrance.
It is the louvre on the façade’s west elevation that is key to the building’s heating and cooling solution; behind it, on every floor level, is a space created specifically to house the outdoor units for the building’s variable refrigerant flow (VRF) system. The design team calls this plant space ‘the mechanical balcony’, because it is classed as being outside and, as such, is thermally isolated from the main building structure. Access is through an opening on each floor, into which the contractor has fitted a big, thick, white walk-in freezer door, complete with a hand lever. ‘The per-floor, air cooled VRF option was viable once we’d worked up the balcony solution with the architects,’ Janiski says.
The VRF system supplies heating and cooling to the apartments. ‘Given that this is apartment-style accommodation and not a student dorm, the ability of occupants to control the temperature of spaces individually was very important to the developers,’ explains Janiski.
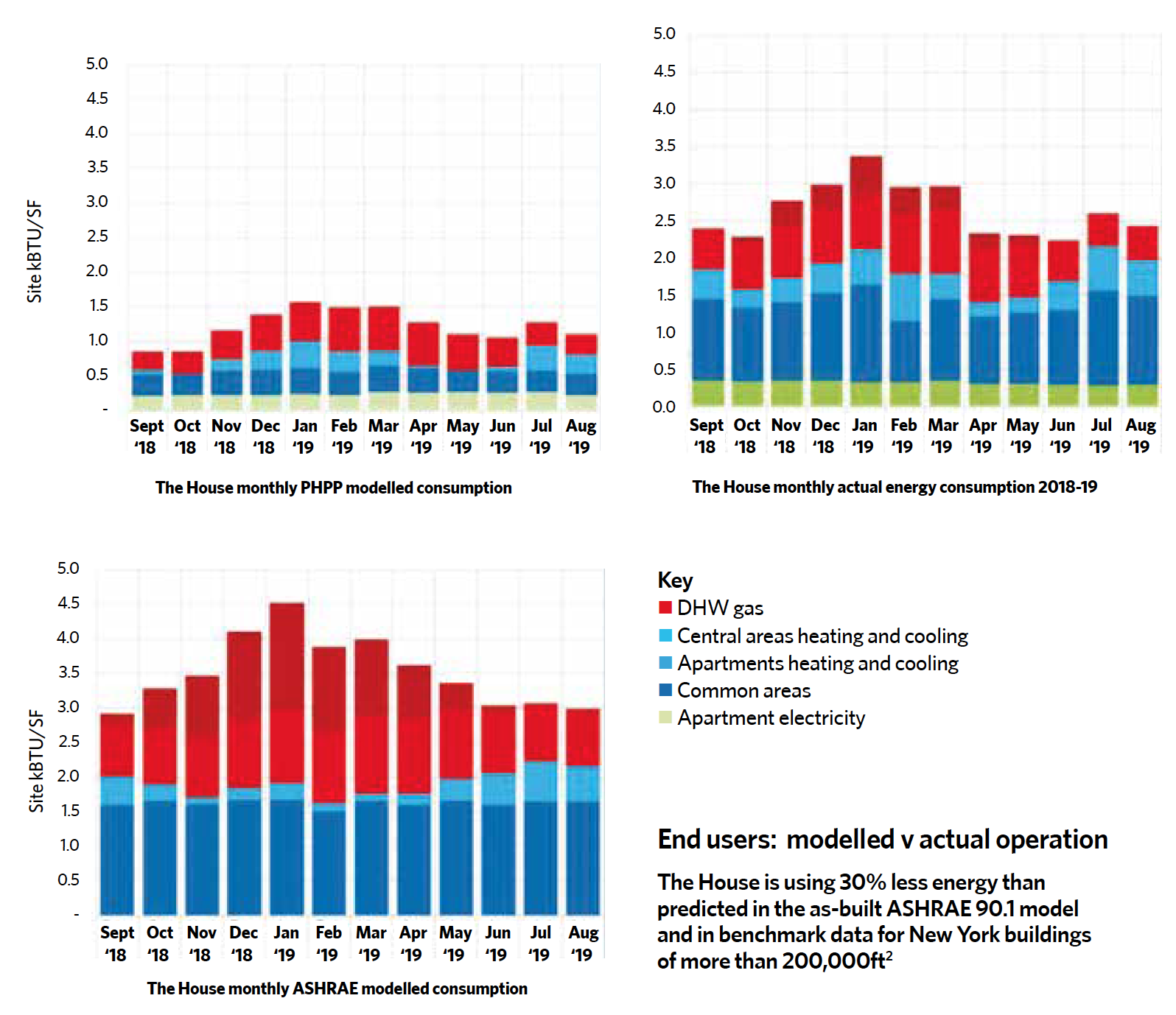
Before opting for the air-cooled VRF solution, Buro Happold assessed the viability of numerous heating and cooling systems based on 17 criteria, including: energy efficiency; space requirements; noise; thermal comfort; individual controllability; the ability to bill occupants based on individual energy use; and, of course, capital cost.
The system alternatives considered included water source heat pumps and water-cooled VRF. ‘The air-cooled VRF was more cost-effective from a capital cost point of view, and it offered the ability for individual fan units in every living room and bedroom,’ Janiski says.
The VRF outdoor units housed on the mechanical balconies are configured in an ‘every other’ sequence, serving two residential floors at a time. One unit serves two floors of north-facing apartments, while the unit on the floor above serves the more tightly packed south-facing apartments on the same floors. ‘To zone based on solar orientation and, therefore, similar amounts of heat gain or loss over the course of a day, and from season to season, it made more sense to have one unit serve two floors of apartments on the north and east, and another serve two floors on the south and west,’ Janiski explains.
The system gives occupants a limited range of settings for the minimum and maximum temperature of their apartments, which, Janiski says, are set in line with Passivhaus criteria.
Although residents can vary the temperature of their apartment, its fresh air supply and exhaust air rates are fixed. As with all Passivhaus schemes, filtered outside air is supplied to living rooms and bedrooms, while dirty air is extracted from bathrooms and kitchens. Unusually for a Passivhaus scheme, rather than use individual apartment units, all 365 apartments are ventilated by two rooftop energy recovery ventilator (ERV) units – otherwise known as mechanical ventilation with heat recovery (MVHR) units. (See panel, ‘Centralised ventilation’).
The House at Cornell Tech was certified by the Passivhaus Institute in September 2017. The Passive House Planning Package (PHPP) model achieved a primary energy demand of 120kWh.m-2 per year for heating, domestic hot water, household electricity and auxiliary electricity. At a PHPP-modelled energy use intensity (EUI) of 120kWh.m-2 per year, the building’s primary energy demand would be 73% lower than the 444kWh.m-2 per year median for residential buildings of more than 20,000m2 in New York City, based on 2013 benchmark data.
However, PHPP models are for certification purposes only and are not intended to predict actual energy consumption, says Janiski. After its first year of operation, the building’s measured primary energy demand from September 2018 to August 2019 was 235kWh.m-2 per year compared with the primary energy demand figure of 120kWh.m-2 per year used in the PHPP model to show that a building has been designed to achieve the required level of performance in the building envelope and systems.
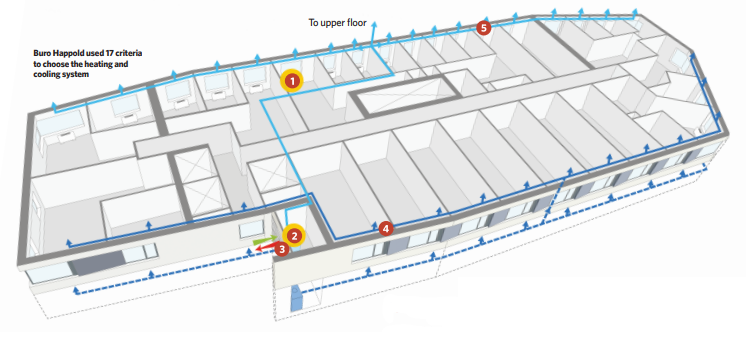
In addition to the PHPP model not predicting actual use, there were some addressable reasons for the higher actual energy use compared with what was anticipated. One issue was the behaviour of the systems and residents. For example, in winter – when the outside temperature drops below freezing – residents entering their apartment chilled from being outside may be inclined to turn up the heat to full immediately, rather than waiting to acclimatise to the internal environment. ‘There were likely situations where there was more heat used than there needed to be, so a cultural shift had to happen,’ Janiski says.
The building’s residents are primarily one-year Master’s students, so the occupants typically change from one academic year to the next. To introduce Passivhaus living and explain how the building’s operation differs from accommodation students are likely to have experienced, the university has created a residents’ guide. This includes information about Passivhaus certification and the intended operations of the heating and cooling systems. The building also features an energy dashboard in the lobby, where all residents can see the actual energy use and how they compare. The energy used during the shoulder seasons for heating and cooling has been flagged as an opportunity for improved operational efficiency.
The modelling methodology in the PHPP also presents a number of significant differences from the local ASHRAE 90.1 modelling methodology, as well as any approaches that seek to predict actual use. For example, the PHPP methodology ‘assumes that, when the temperature and humidity are nice outside, occupants will open their windows and turn heating/cooling systems off’. This action not only needs a cultural shift to rely less on active heating and cooling, it also requires that residents turn off the system when their windows are open, which is acoustically uncomfortable given that the building is adjacent to the Queensboro Bridge.
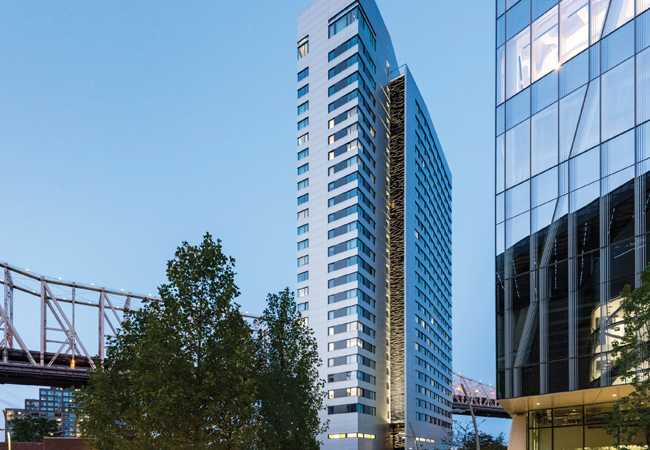
The House at Cornell is situated next to the Queensboro Bridge
The multi-tenanted aspect of the project, which meant the building incorporated amenities such as a gym, yoga room, and a laundry room, were also cited as being outside the traditional family home PHPP model, which, Janiski says, ‘all add up’. The common area electricity, and high plug loads serving a technology-driven resident population, are noted areas of opportunity to find additional efficiencies. The project team has been working with the owner to review detailed building operations data related to equipment, ranging from the heating and cooling VRF system to the elevators, to evaluate further optimisations.
The ambition of the scheme in implementing Passivhaus at this scale was recognised by the judges at this year’s CIBSE Building Performance Awards where it won the Project of the Year – Public Use category. They praised the Buro Happold team ‘for its holistic integration of engineering, social aspects and lessons learned’.
Janiski says it’s an honour to have awards, but ‘the most meaningful part of this experience is that our impact stretches from the scale of the individual occupants’ improved health to the scale of cities through the advancement of energy codes and GHG emissions reductions’.
Lastly, she underscores the importance of the team working together, and her gratitude for having ‘such clear vision and leadership’ from the project developers and university.
Centralised ventilation
Two rooftop energy recovery ventilators (ERVs) were specified, rather than units for each apartment. Buro Happold evaluated the possibility of ventilating each apartment using individual units, but the building’s configuration made these unsuitable. The need to minimise the apartment floor-to-ceiling height to get as many floors into the building as possible meant that fitting an ERV unit beneath the ceiling ‘would be problematic’, says Janiski.
The need for access to maintain the ERV and change its filters was perceived as ‘a significant challenge’ and there were concerns about ‘the large number of penetrations required through the façade’, and the challenge of sealing each of these effectively to maintain an airtight envelope.
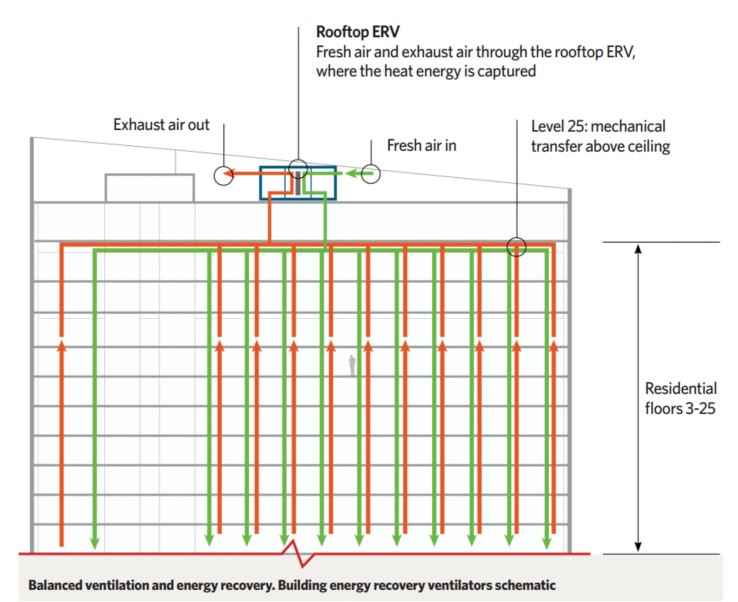
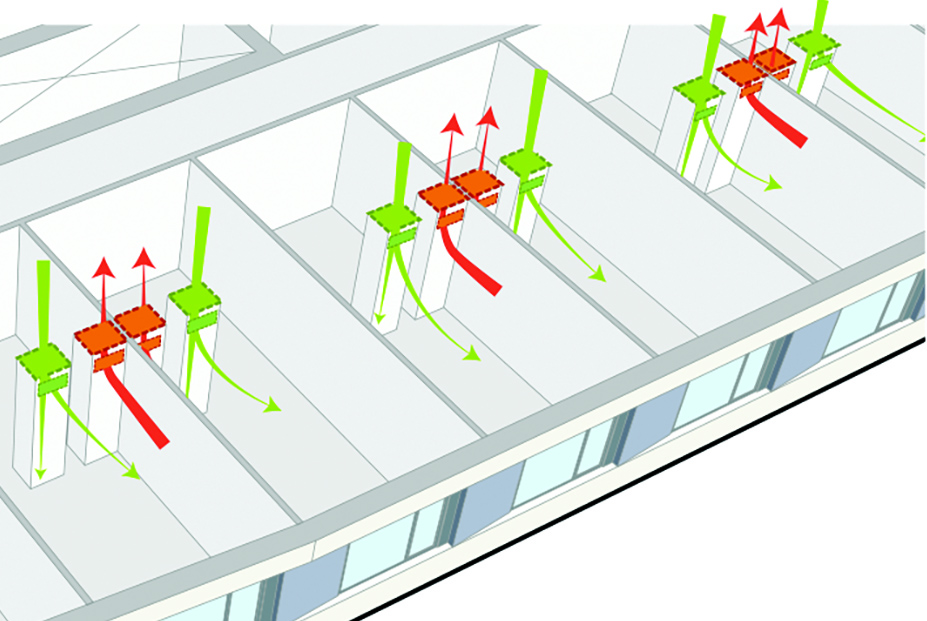
The deciding factor, however, was the large number of ‘micro’ apartments clustered on the southern elevation, which meant it was not possible to separate the locations of the units’ supply and extract terminals effectively.
While the centralised ventilation option overcame many issues, it conflicted with New York City’s building codes. In contrast to Passivhaus, where the kitchen and bathroom extracts are usually combined to make it relatively straightforward to maintain the building at a neutral pressure balance, and to simplify heat recovery from the exhaust, the city’s building codes require kitchen and bathroom extracts to be separate systems. Buro Happold met officials to talk them through the scheme: ‘As a compromise, we offered to maintain the kitchen and bathroom exhausts separately throughout the height of the building, only combining them at the point at which they enter the ERV, which satisfied the city,’ says Janiski.
The centralised ventilation solution also made it difficult to incorporate a boost mode on the individual extracts – and, therefore, the supplies to maintain balance – in each apartment, to increase the rate of extract at those times when occupants are cooking or bathing.
To try to provide a continuous-mode and boost-mode airflow, Buro Happold investigated fitting a motorised damper at the points of extract and supply. It came down to two criteria, as Janiski explains: ‘The price tag of having that many [more than 1,000] automated dampers on a project of this scale was enormous, and the reality of a damper manufacturer being able to guarantee the extract rate would go from 4 L.s-1 to 11 L.s-1 was unfeasible, because the manufacturers said the dampers “are not built for that level of precision”.’ As a compromise, the Passivhaus Institute agreed to accept a steady extract rate set between normal and boost mode.
Janiski says the scheme uses two rooftop ERV units for reasons that include a zoned design approach, and that ‘one unit would have been quite large’. To minimise air leakage and improve system efficiency, supply and extract ductwork systems have been sealed using Aeroseal, a polymer sealant blown through the ducts. According to Buro Happold, the polymer ‘reduced air leakage by more than 90%, greatly improving energy efficiency’. Nevertheless, because the ERV units are not Passivhaus certified, their use on the system did incur an efficiency penalty on the Passive House Planning Package (PHPP) compliance spreadsheet.
Minimising air leakage through the building fabric, and through the façade in particular, was fundamental to achieving Passivhaus certification. Contractor Monadnock Construction had the façade prefabricated off site in storey-high sections, which were then hauled to the island site by barge. Once craned into place, the joints between panels were carefully taped to ensure the façade was airtight. A whole-building pressure test measured airtightness of just 0.13 air changes per hour at 50 pascals – against the Passivhaus maximum 0.60.
■ See details of all the 2021 Building Performance Award winners at cibse.org/bpa