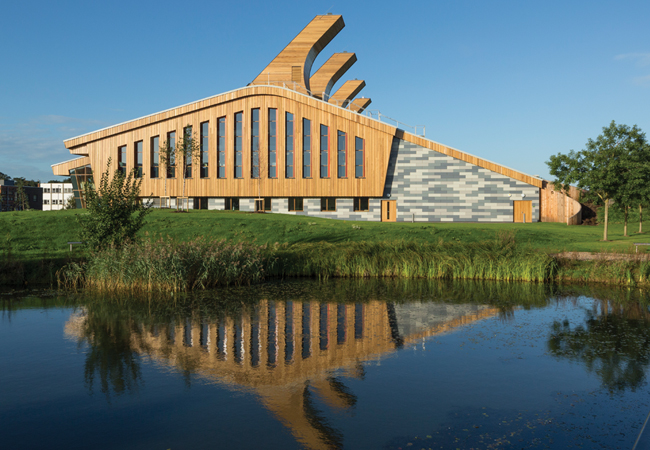
Think of low-energy buildings – and space-age labs for generating the latest advances in chemistry may not spring to mind. Yet, the GlaxoSmithKline (GSK) Carbon Neutral Laboratory for Sustainable Chemistry boasts a Breeam Outstanding rating for its environmental credentials, putting it in the top 1-2% of buildings.
The centre is the latest development by the University of Nottingham on its Jubilee Campus. As the name suggests, the £15.8m facility aims to be carbon neutral over its 25-year lifetime. The energy required to run the laboratory is met by solar power and sustainable biofuel. Excess energy will produce enough carbon credits over 25 years to pay back the carbon used in construction, and is being used to heat a nearby office development. But in September 2014 – 52 weeks into an 84-week build – the centre was gutted by a huge blaze. No blame was attached to the build process (an electrical fault in the temporary site supply was thought to be the culprit) and principal contractor Morgan Sindall has rebuilt it, largely using the same design.
From concept to reality
Part funded by a £12m gift from GSK, the building occupies 4,500m2 over two floors, and includes lab space for 150 researchers, dedicated instrument rooms, a teaching laboratory, offices and space for outreach activities. The striking design, by architect Fairhursts Design Group – with its ‘horns’ to assist ventilation in the laboratories – includes a solar photovoltaic (PV) array on the southern aspect, a north-facing grass roof and a communal winter garden.
Aecom was the building services consultant on the project. ‘We were employed by GSK to develop and validate the concept of a naturally ventilated, very low-energy chemistry laboratory,’ says Matthew Butler, associate director, building engineering at Aecom. ‘When GSK gifted the concept and supplied the funding, we had to evolve the design – as some of the requirements of the university are quite different – but still keep the zero carbon status.’
A secondary ‘doomsday’ gas-fired boiler backup is for use only if there are problems with biofuel delivery
Central to this is delivering a building with a low embodied carbon content. The target is a 70% reduction, compared to a conventional new build. ‘There is lots of wood,’ says Butler. ‘That presents a few challenges. For example, wood tends to vibrate more than other materials, sensitive equipment has been housed on the ground floor.’ Wood can also absorb chemicals that may be splashed onto surfaces, so some areas have been treated, while parts of the labs have sacrificial panels that can be replaced.
The next challenge was to cut energy use. ‘We have targeted areas, such as the ventilation system for the fume cupboards, and put heat recovery units on them,’ says Butler. ‘We’ve also included cooling only where necessary and done all the standard things, such as low-energy lighting.’
Renewables in the mix
The third part of the strategy is to generate energy from renewable sources. ‘Solar power was always planned to be part of the mix and the building has a large roof area for the [PV] array,’ says Butler. Panels can sit flat on the roof without a frame, giving an output of 230,000kWh per year.
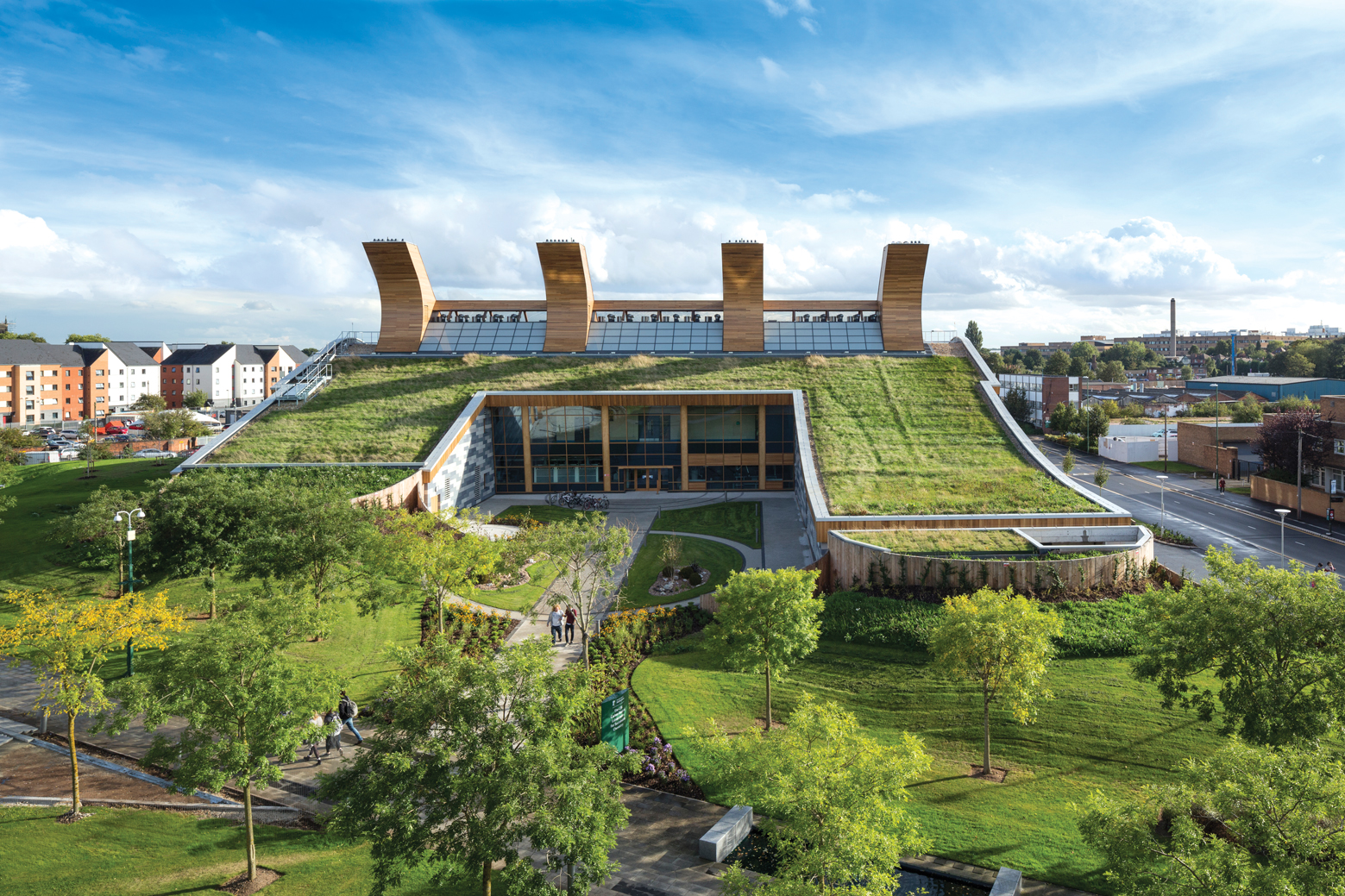
The distinctive ‘horns’ give very high flue-gas discharge rates
The building also uses a biofuel combined heat and power (CHP) unit. ‘Gas-fired CHP plant wouldn’t have got us to carbon-neutral status,’ says Butler. ‘We looked at solid-fuel biomass, but – at the time – the technology was struggling in terms of handling the fuel and getting the heat and power out of it.’
Liquid biofuel was the best option, but the exact source of the fuel is a closely-guarded secret. ‘It’s an industrial by-product and that’s all I’m allowed to say,’ says a tightlipped Butler. ‘The fuel isn’t a food source because it needs to be sustainable.’
The CHP unit delivers 200kW of electrical power and 193kW of heat. It acts as the primary heat source, with a biofuel boiler as primary backup. A secondary, ‘doomsday’, gas-fired boiler is for use only if there are problems with biofuel delivery. Heat from the CHP is collected in a thermal store big enough for 3-4 hours’ operation. Space heating is by underfloor heating.
Fume cupboards key to ventilation strategy
There are five labs on the first floor – four are conventional and one is an experimental concept laboratory. ‘One of the challenges has been the university’s requirement for many more fume cupboards than was planned under the GSK concept; that adds to the energy consumption,’ says Butler.
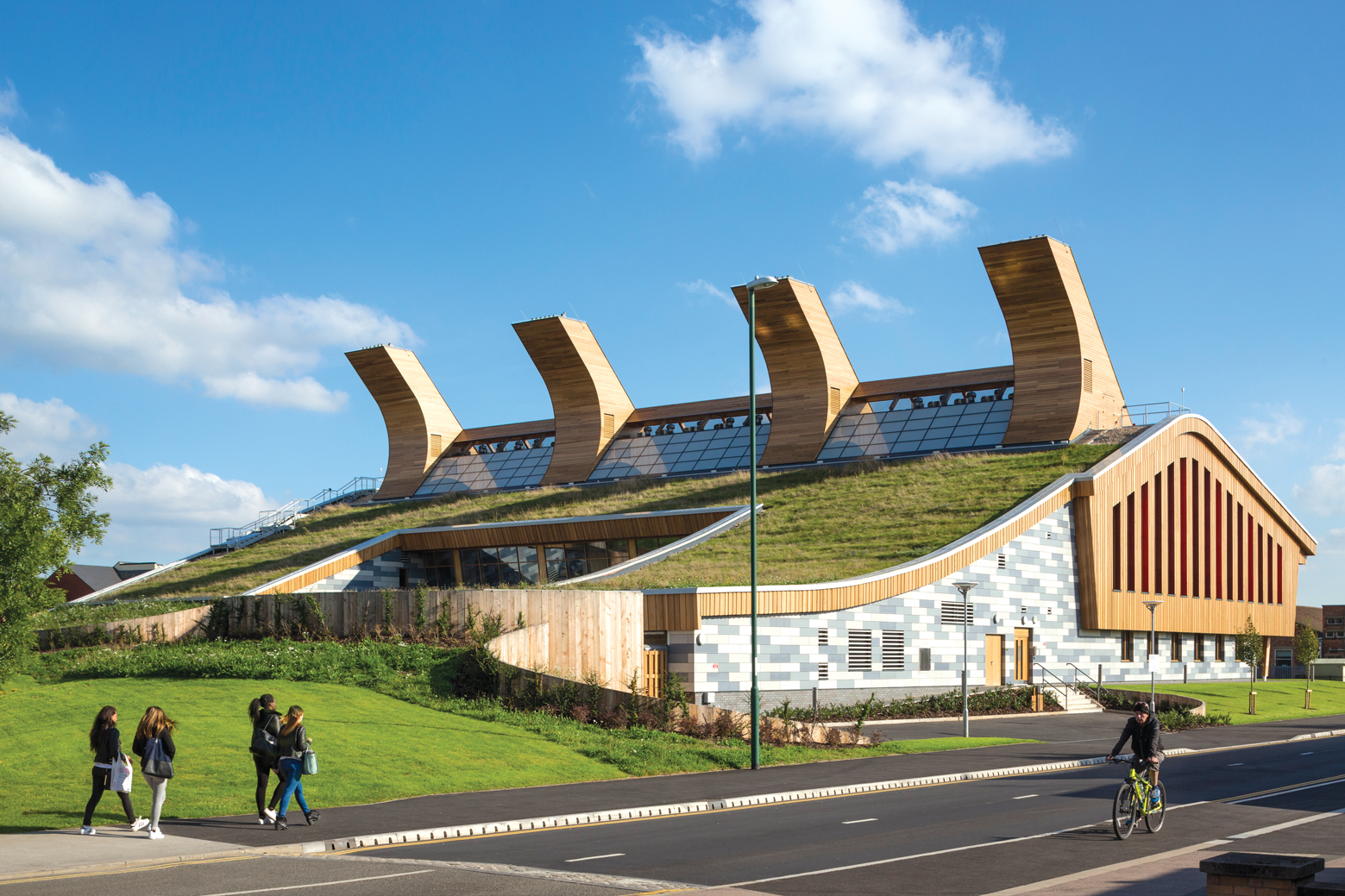
In the four main labs, Aecom has installed low face velocity, variable-volume fume cupboards with automatic fast closures; when users walk away, they set back on volume. ‘These provide all the ventilation for the space, so we can minimise the air supply to exactly what we require, based on the fume cupboards,’ says Butler.
It is here that the building’s distinctive ‘horns’ come into their own. ‘These give us very high flue-gas discharge rates, so we are able to reduce the discharge velocity, saving a lot of fan energy,’ says Butler. Multiple nozzles on the discharge also allow a greater turn down on the fans. ‘We can open nozzles to suit the desired air-flow rates.’
To save energy, there is a dedicated air handling unit (AHU) for each laboratory. This way, the air volume required for each fume cupboard can be closely matched with the air and temperature requirements for users in the space. No cooling is provided. A plate heat exchanger is used to exchange heat from the fume cupboard extract with incoming air, giving big savings on energy.
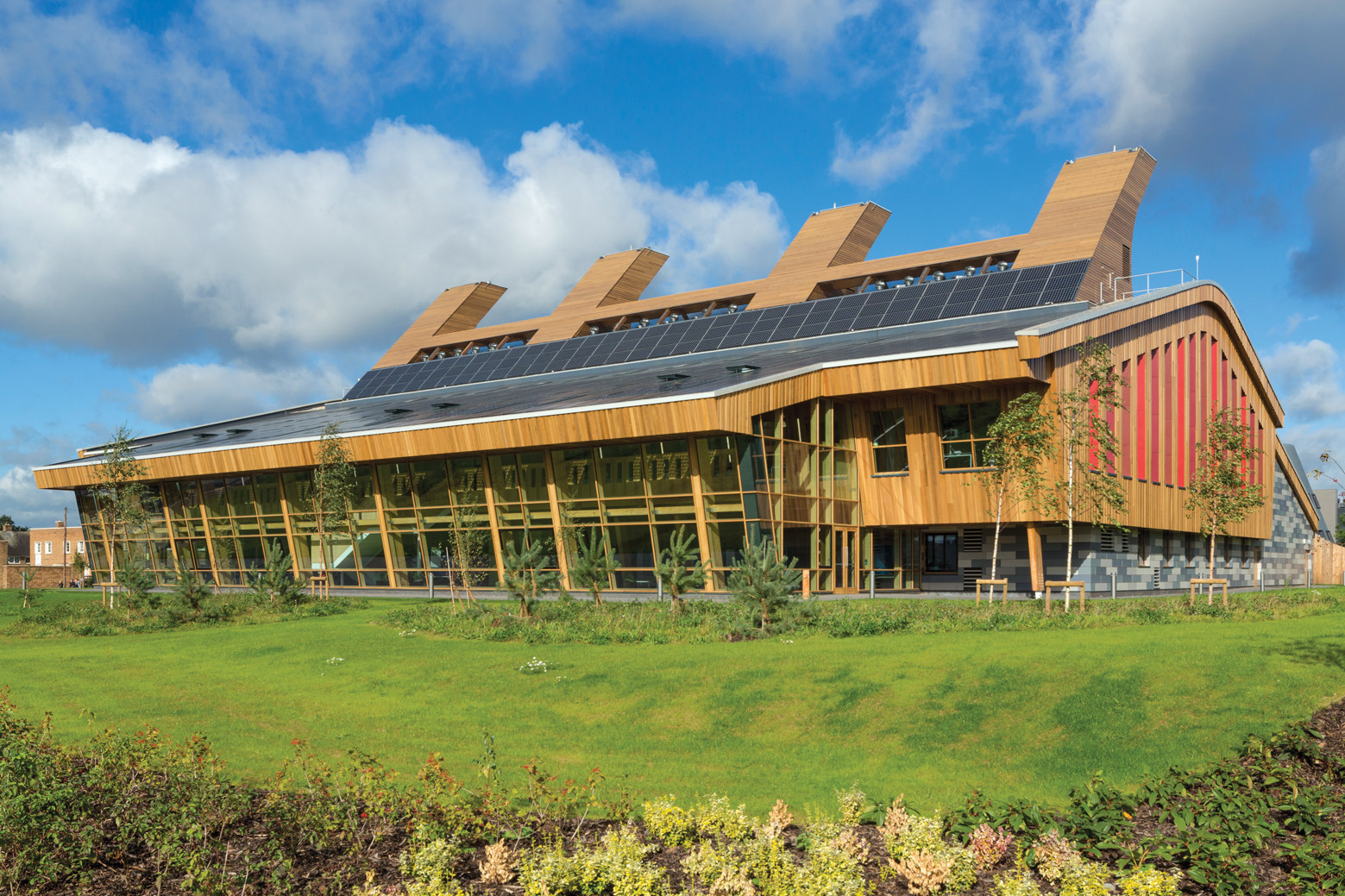
In the centre of the building is the concept laboratory, which is naturally ventilated. ‘The building forms a ridge and we are using the wind pressure on the ridge to drive ventilation through plate heat exchangers to give natural ventilation and heat recovery for a very low-energy lab,’ says Butler. ‘We believe it’s a first; you get naturally ventilated labs, but not with heat recovery to try to achieve a high air-change rate without heat loss.’
On the ground floor are two labs housing specialist equipment that is temperature critical, so cooling has been installed in these areas. ‘A dedicated AHU for each space allows us to maximise the free cooling from outside air before the central chiller needs to kick in,’ says Butler. Also on the ground floor are offices and teaching spaces. Here, ventilation is via a variable air volume system without cooling, again using a heat-recovery heat exchanger unit on the ridge. ‘This achieves very low energy ventilation to the offices,’ adds Butler.
Changing user behaviour
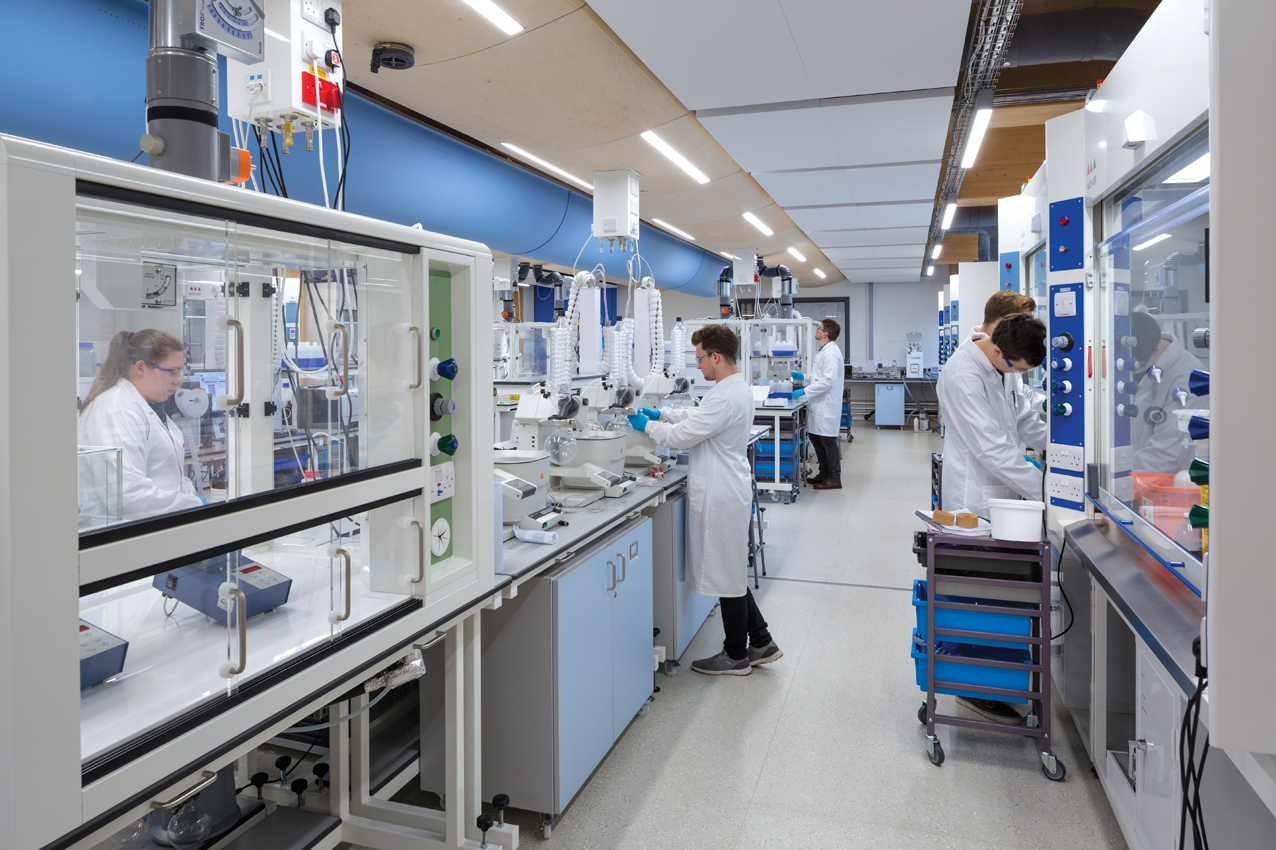
A key part of the energy strategy involves cultural change from scientists. ‘Academics don’t work in the same way that the GSK concept envisaged, so we’ve had to look at things such as backing the ventilation system right down so we can just run one fume cupboard in a lab,’ says Butler. Aecom holds regular meetings with the university to look at energy data and the impact of out-of-hours working. Chemical storage cabinets have also been accommodated. ‘Scientists tend to leave chemicals in fume cupboards overnight, which means they use a lot of energy. The storage cabinets are run with a minimal ventilation rate to take out any vapours, saving a huge amount of energy in terms of fan running costs.’
The fire that gutted the original building did not lead to major design changes. ‘A couple more fire partitions were put in, but that was only because the fire regulations had changed in the interim,’ says Butler. ‘The fire had a galvanising effect and the project benefited from a greater spirit of collaboration after it.’
The result has certainly pleased the client. ‘It’s a project that defines a new way of approaching science and the environment that sits around it – we’re teaching our scientists to work in a way that’s more sensitive to their carbon footprint,’ says Professor Peter Licence, director of the centre. ‘This building has to inspire people to want to do things differently.’