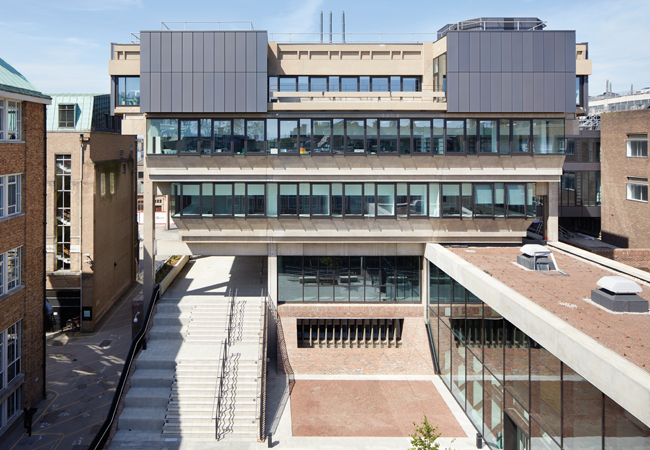
‘A drama of violence’. That was the description architectural historian Sir Nikolaus Pevsner gave of the University of Cambridge’s Arup Building in 1971, while the building was still under construction. Now, more than 40 years later, Sir Philip Dowson’s design is recognised as an important example of one of the 20th century’s most controversial architectural movements. More recently, architectural historian Barnabas Calder described the building as ‘Cambridge’s most elating piece of brutalism’.
Dowson worked for Arup Associates – hence the building’s name – and his design celebrates concrete as a construction material. The building has a reinforced-concrete frame, which rises up from a two-storey, brick-clad podium and a slender ground-floor space to support a massive superstructure of three reinforced-concrete floors, each extending out over the one below. Even the building’s façades are concrete, albeit interspersed with ribbons of steel-framed single glazing.
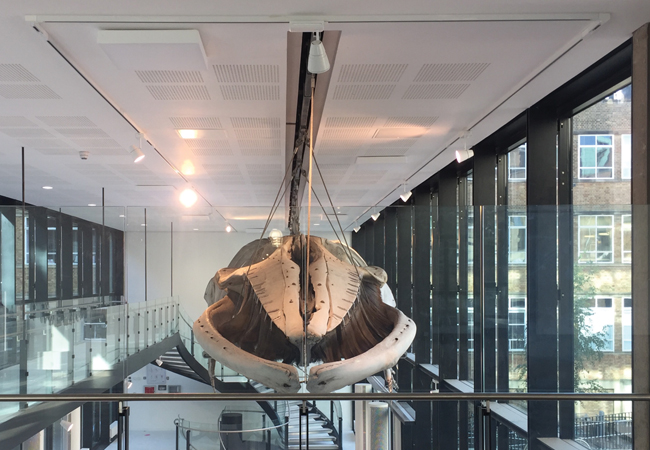
While architectural historians might find the building’s appearance joyous, the experience for occupants was anything but. The façade was poorly insulated and this – combined with the large areas of single glazing – produced a building that was too hot in summer and too cold in winter, and that leaked energy. In fact, its energy performance was one of the worst of any building on the university’s estate.
In 2012, engineer BuroHappold was appointed – along with Nicholas Hare Architects – to develop a refurbishment solution for the 16,000m2 building, which housed laboratories for the university’s materials science, metallurgy and zoology departments on its upper floors. Its podium, meanwhile, was home to a 450-seat lecture theatre and the Museum of Zoology. The proposal was for the podium lecture theatre and museum to remain, but for the upper floors to become the new home for Cambridge Conservation Initiative (CCI), a collaboration between the university and a group of local biodiversity and conservation organisations.
The CCI was looking for a building actively to encourage collaboration between its members, to maximise its impact. From the outset, the new tenant made clear that it wanted its campus to be ‘as green a building as was possible’. It pushed for the sustainability credentials to go well beyond the industry norm, to become an exemplar and help reinforce its message to visiting academics, conservation practitioners, policy-makers and business leaders.
Although the Arup Building is not listed, the task for the design team was to turn this uninsulated, single-glazed, brutalist icon into a showcase of sustainability best practice, while preserving the architectural integrity of the original design. To establish the project goals, stakeholder engagement workshops were held, involving the future tenants, the university’s estates energy, environment and facilities management team, the architect and BuroHappold. Rather than aim for a specific Breeam rating for the refurbishment, BuroHappold pioneered what Andy Keelin – a partner at BuroHappold Engineering – terms ‘a bespoke sustainability framework’. He says the solution was developed ‘because of the lack of environmental assessment methods that deal with a building of this nature, with its multiple uses, the tenant’s level of ambition and the increased emphasis on some aspects of sustainability’.
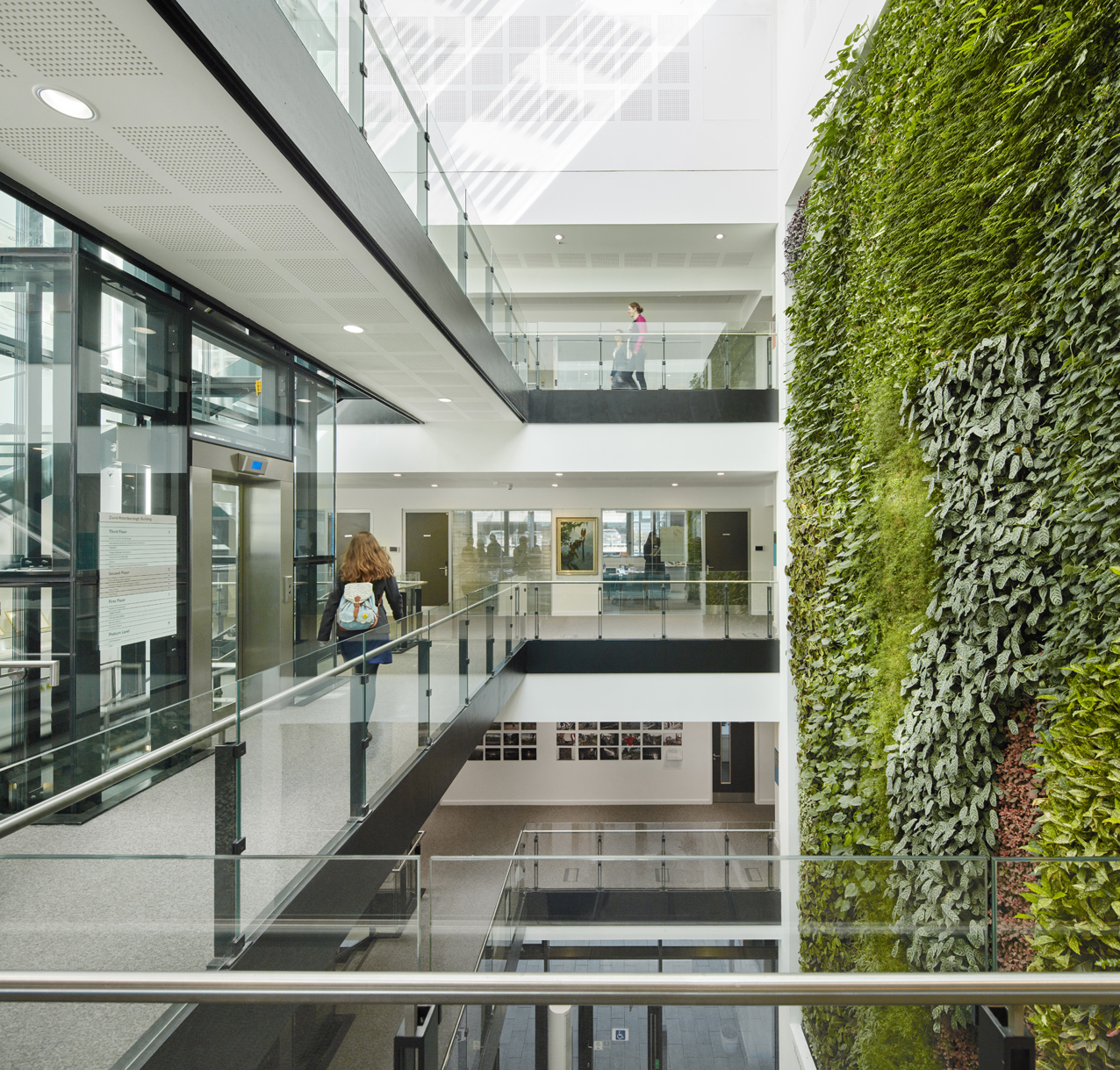
The framework set project-specific targets across 10 headline themes and 50 sub-themes. These included sustainability targets for the design team and for the building users, once they took up occupancy, to ensure the sustainable potential of the building was maximised. Headline targets included a 40% reduction in operational carbon emissions, a 30% reduction in water use per person, and 60% of the roof given over to a biodiverse green roof. The framework also included less-conventional aims, such as occupant wellbeing and ensuring the building educated visitors and facilitated collaboration. According to Keelin, the framework went down well with the planners because ‘they could see how seriously we were taking sustainability’.
Before starting to develop a sustainable engineering solution for the refurbishment, BuroHappold set out to gain an in-depth understanding of the thermal performance of the existing building. This included a thermal-imaging survey of its fabric, which showed the worst-performing aspects of the façade to be the single-glazed windows and their steel frames, and the concrete panels above and below the glazing.
The engineer carried out a full energy audit – using data from the past three years’ energy bills – to benchmark the building and to show the pattern of energy use. BuroHappold also undertook a Building Use Studies occupant satisfaction survey, to garner information from the current occupants about comfort conditions within. Unsurprisingly, this revealed that the building was too hot in summer and too cold in winter.
The investigations also threw up some interesting facts. ‘We found out that the boilers were undersized for the job that they had been asked to do, which meant gas consumption was unrealistic – but no-one had realised because the occupants had compensated for the lack of available heat by plugging in electric heaters,’ says Keelin.
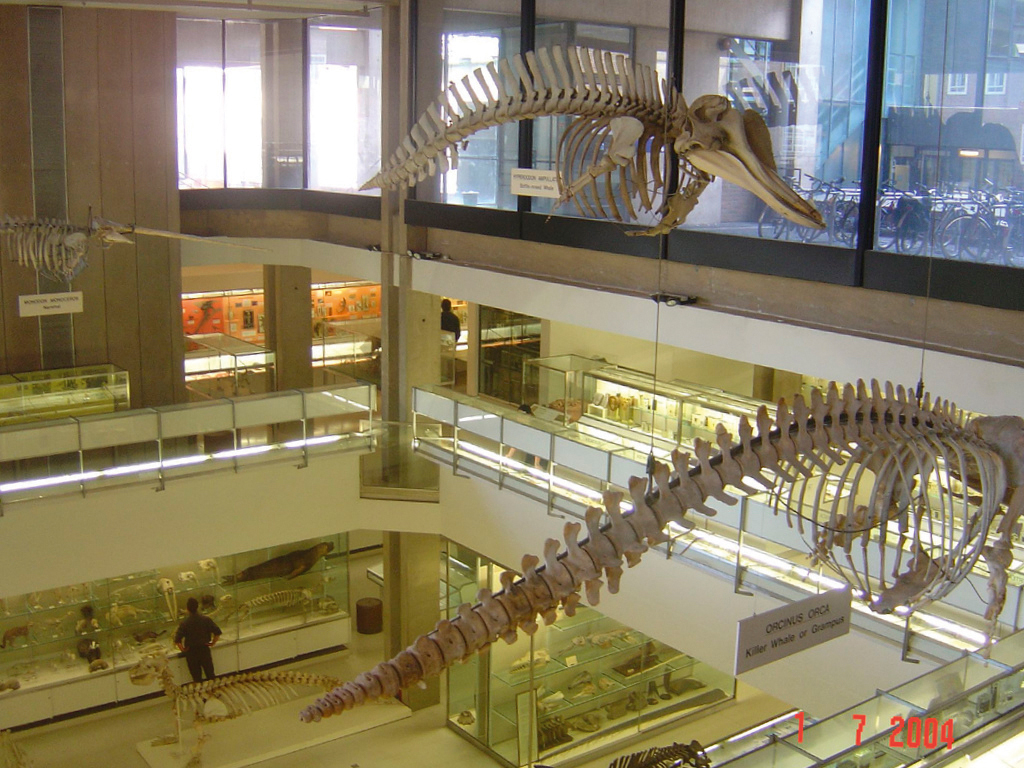
In addition to the energy surveys, the building was point-cloud surveyed to get accurate dimensional data for the interior. ‘Because it is a refurbishment, you have to understand the constraints imposed by the building on the proposed design solutions,’ Keelin says. The engineers also modelled the new atrium the architect wanted by extending an existing lightwell down to the lower floors to bring light into the heart of the building. ‘We modelled this to demonstrate the value it would add.’
When it came to developing a services strategy, Keelin says the approach was to work with the existing building: ‘We set out to make the fabric work hard to reduce the cooling and heating loads, and to remove as many of the services from the building as we could.’
The original building had been designed with some naturally ventilated areas, but was predominantly heated and cooled by a ducted air system. ‘Our approach was to strip out the ductwork, remove the suspended ceilings to expose the thermal mass of the concrete soffits, and pursue a natural ventilation strategy,’ adds Keelin. This was helped by the relatively generous floor-to ceiling heights.
The key to successful, natural ventilation of the building was to upgrade its fabric to modern standards. At the time, Part L 2013 of the Building Regulations was still under consultation, and not yet enforced, so the designers set out to achieve a fabric performance at least 25% better than the existing Part L2B 2010, in order to meet the expected performance requirement of
the 2013 regulations.
The scheme’s design-stage performance demonstrated that the ‘actual building’ achieved an overall improvement of 30.8% compared with a ‘notional building’ compliant with the limiting elemental requirements of Part L2B 2010. This figure provided a buffer of approximately 5% above the aspirational target, allowing for any minor reductions in as-built performance that might arise through final product selections and their installation.
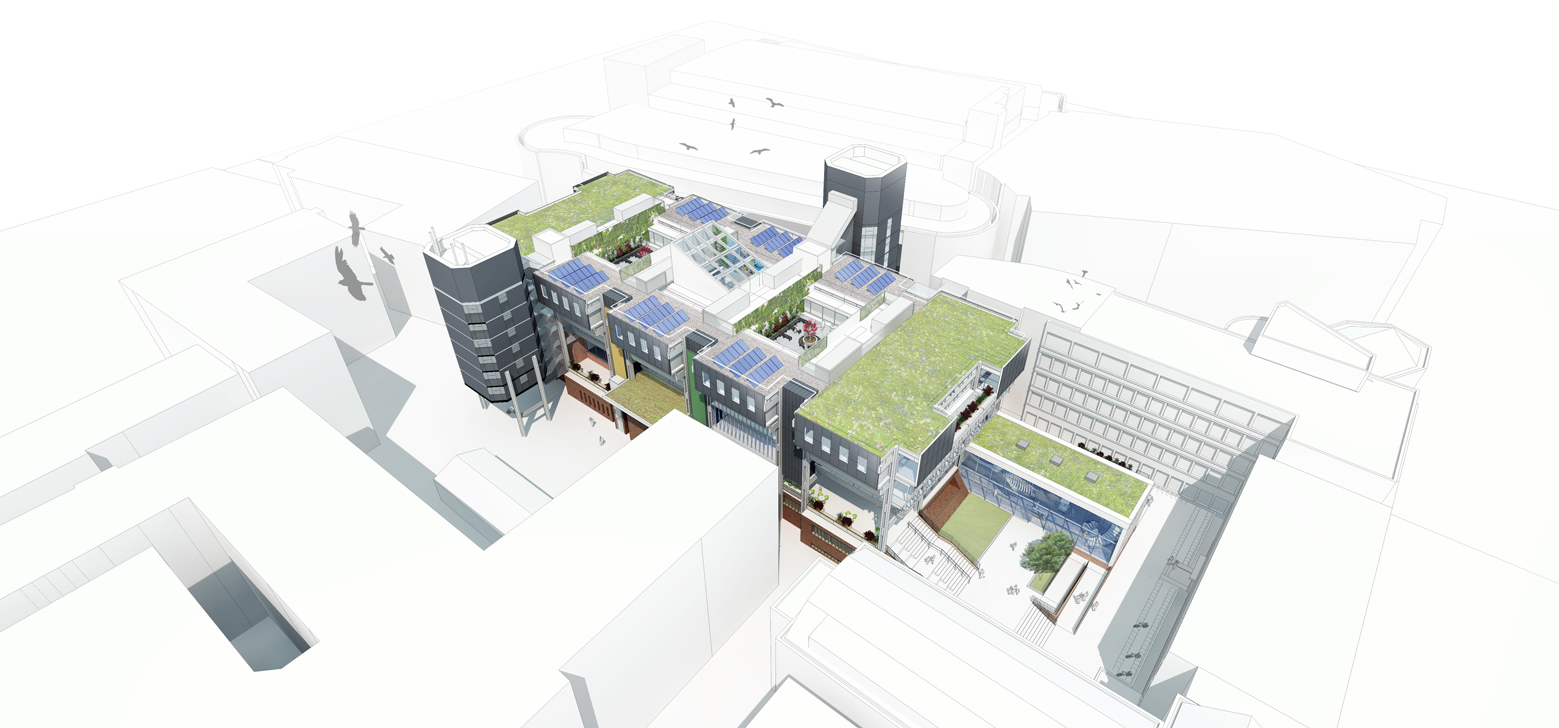
To preserve the building’s integrity, modifications to the fabric were varied depending on the architectural sensitivity of an area of façade. Certain walls on the lower ground and podium, for example, could not be upgraded. As a result, the fabric performance in other areas was upgraded beyond the level required by Part L2B 2010. Using the emissions approach to compliance ensured that the disparity in CO2 emissions from not uniformly upgrading the building fabric could be accounted for through enhanced carbon-saving improvements elsewhere. The final EPC has still to be produced.
One of the most obvious energy efficiency wins was to replace all of the windows with double-glazed units. The replacements match the fenestration patterns and mullion profiles of the originals, and incorporate actuator-driven opening top lights, to facilitate night ventilation and manually openable low-level units. ‘Because we were recladding the building, we were able to have top and bottom opening windows to increase ventilation efficiency,’ says Keelin. To upgrade the thermal performance of the external concrete walls, an insulated internal lining was added.
The one area where there was little exposed concrete was the building’s top floor, because the original roof was a lightweight construction based on a thin wood-wool slab set on concrete beams. In the refurbishment, this has been replaced by a structural metal deck supporting a warm roof construction above. To add thermal mass, the metal soffit has been lined with phase-change material (PCM) panels, installed between the concrete secondary beams. The addition of the PCM ensures the soffit behaves in a similar manner to the soffits on the lower floors.
The roof
More than 60% of the roof area is vegetated, with planting chosen to replicate that of the local chalkland to encourage wildlife. On the roof are bee hotels, and bat and bird boxes, with live CCTV connections back to displays in the Cambridge Conservation Initiative atrium. The planting improves the thermal insulation and helps to attenuate rainwater run-off as part of the building’s sustainable drainage strategy. The roof also includes 86.22m2 of photovoltaic panels – and 73.5m2 of PV glazing at the top of the new atrium – potentially generating a maximum of 16.5kW of electricity.
The building’s natural ventilation design was based on the CIBSE standard approach; for example, the internal temperature exceeds 28°C for less than 1% of the occupied period. ‘Our initial aim was to ventilate the entire building naturally,’ says Keelin. ‘Ultimately, we didn’t achieve that goal; instead, we got to a point where 70% of the building is naturally ventilated, with the remainder mechanically ventilated.’
To maximise the impact of the natural ventilation, open-plan offices have been strategically placed around the building’s perimeter to benefit from opening windows. The spaces that require mechanical ventilation – such as meeting rooms and IT cupboards – have been clustered in the middle of the floor plates. ‘All the spaces that need mechanical ventilation can have it, while everybody else will benefit from natural ventilation at the building’s perimeter,’
says Keelin.
Internal spaces are ventilated using a variable air volume (VAV) system designed with low specific fan power and incorporating heat recovery. A total of 9m3.s-1 of fresh air is provided by five roof-mounted air handling units (AHUs) – and two additional AHUs, one on the lower ground floor and one in the basement – based on 10L.s-1 per person at a temperature of 24°C +/-2K. The archive stores on the lower ground floor are also mechanically ventilated, with air supplied at 18°C +/-2K – and relative humidity at 55% +/-10% – year round.
The boilers were undersized, so gas consumption was unrealistic – but no-one had realised because the occupants compensated by plugging in electric heaters
To support the ventilation solution, BuroHappold assessed the likelihood of the building overheating in the future, based on probabilistic climate data for Cambridge for 2030 and 2050, using a high-emissions scenario. This showed that it could become uncomfortable, so a number of precautionary design measures were adopted, including future-proofing the window actuator controls to enable mixed-mode ventilation to be accommodated at a later date.
The first CCI members moved into the building in December 2015 and, by early 2016, the remainder were established in the new space. The building is extensively metered and the results displayed in the atrium to encourage responsible energy use and demonstrate the building’s exemplar performance. Because of the discovery of asbestos, the museum – the final part of the building – is due to open slightly later than planned, in February 2017.
The project includes soft landings to ensure sustainable occupation. Keelin says it is still too early for any meaningful monitoring results, but reusing the
building is claimed to have saved 82% of embodied carbon.
Another significant detail is that, since its £57.8m refurbishment – and in light of its new sustainable credentials – the building has been given a new name: the David Attenborough Building.
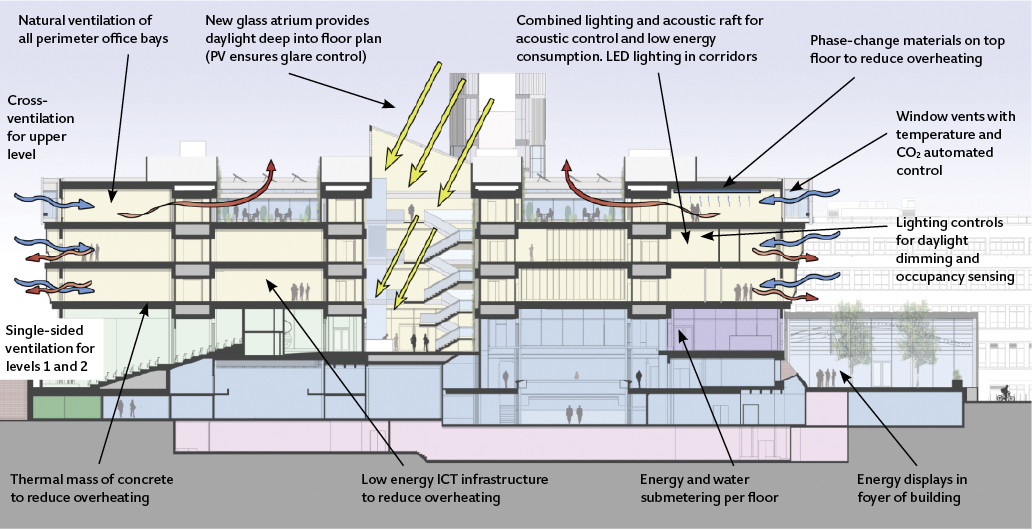
Section view of David Attenborough Building