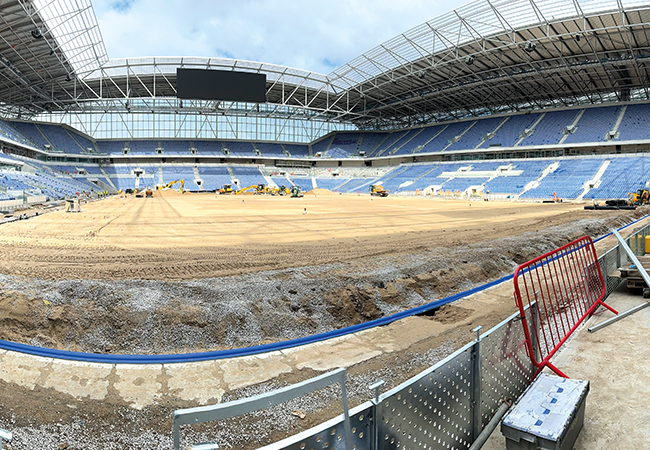
The design for manufacture and assembly (DfMA) approach meant less work and fewer workers on site
Nil satis nisi optimum – ‘Nothing but the best is good enough’. Everton Football Club’s motto is perfectly suited to the no-compromise approach to digital design and offsite manufacture used in the construction of its new stadium nearing completion at Bramley-Moore Dock, Liverpool.
Modern methods of construction and digital design have played a pivotal role in the scheme from the outset, with 70% of the stadium’s mechanical, electrical and plumbing (MEP) services – and much of its superstructure – delivered to site as prefabricated and modular assemblies.
It has been quite a task: ‘There are 53,000 elements, of which nearly 40,000 are mechanical, electrical and plumbing services, so we’ve had to think modular from day one,’ says Ian Siddy, associate mechanical engineer at Buro Happold, the project’s engineers.
Project Team
Main contractor: Laing O’Rourke
Concept architect: MEIS Architects
Delivery architect: BDP Pattern
Building services engineer: Buro Happold
Facade engineering: Arup
The move to a new home has been a long time coming. Everton has been at its current Goodison Park site since 1892; the club was one of 12 to participate in the first football league season in 1888. Unable to upgrade its existing stadium because of constraints imposed by its location, the club secured a new site in Liverpool’s Northern Docks area in 2017. In 2019, US architect Dan Meis was appointed to develop a concept for the club’s new home. Its design draws on the brick-warehouse typology of neighbouring buildings, including the Tobacco Warehouse and the Titanic Hotel, with four brick-clad stands surrounding the pitch. Unusually, these are topped by giant picture windows that bring views of Liverpool and Merseyside into the steeply raked seating bowl. The stadium is crowned with a distinctive curved barrel roof.
Working with Everton, Dan Meis and technical architect BDP Pattern, Buro Happold helped refine the stadium’s design. In 2020, Laing O’Rourke (LOR) was appointed as design and build contractor under a pre-construction service agreement (PCSA). The PCSA shifted the project focus from design development to design optimisation, to enable the stadium to be split into components and modules for manufacture offsite, under LOR’s design for manufacture and assembly (DfMA) process.
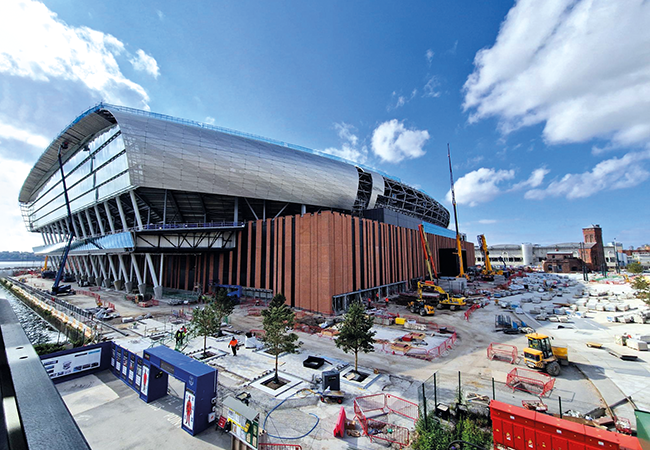
The stadium’s design draws on the brick-warehouse typology of neighbouring buildings in the Northern Docks area of Liverpool
‘DfMA is a design approach that focuses on the ease of manufacture and efficiency of assembly; by optimising the design of a product, it is possible to manufacture and assemble it more efficiently, more quickly, more safely, and at a lower cost,’ explains Siddy.
LOR’s DfMA philosophy is 70:60:30, which means delivering 70% of a build using offsite production, making things 60% more efficient, and saving 30% on programme. A major benefit is that a lot of work that would traditionally be done on site is taken offsite. This ensures better build quality and greater control of wastage, making the process more environmentally friendly. DfMA reduces time on site. Manufactured modules and components are simply craned into position, because every service interface will already have been positioned digitally before module manufacture can begin.
Buro Happold and BDP Pattern were contracted to LOR to ensure the design was DfMA-ready. ‘By reducing the workforce on site, DfMA helps create a more efficient and safer site,’ says John Edwards, project technical leader at LOR. LOR created a federated BIM model of the stadium, which allows models from all disciplines’ designs to be combined in a single place in which to coordinate all objects to the construction programme. This model was linked to detailed construction programme information, to enable a dynamic digital twin to be created to help plan exactly how the stadium’s construction would be executed.
Every service interface will have been positioned digitally before module manufacture can begin
In addition to identifying potential risks or clashes in the build programme, the 4D model allowed the LOR team to identify efficiency opportunities that might not have been realised with more conventional programming methods.
Rather than attempt to modify its MEP designs to make them suitable for modularisation and offsite assembly, Buro Happold took the bold decision to start again. Working with LOR and Crown House Technologies (CHT), LOR’s MEP contracting arm, Buro Happold set about embedding offsite principles into its MEP design from the outset
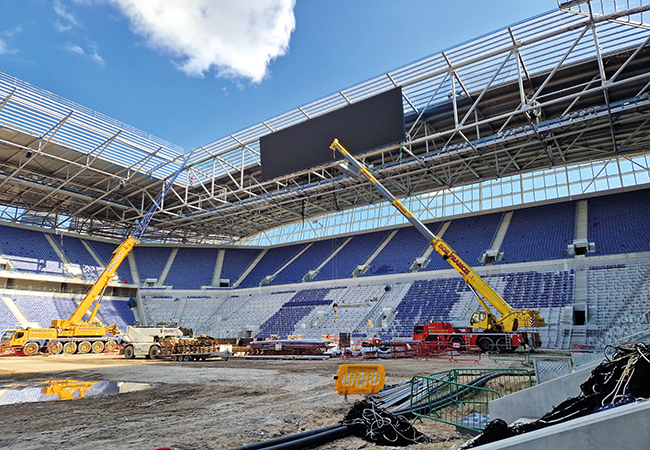
The stands are topped by giant picture windows and the stadium is crowned with a distinctive curved barrel roof
‘We knew the elements that needed to be incorporated. Crown House Technologies gave us guidance, explained how it wanted the systems set out, defined the space needed for access, and explained the capabilities of its manufacturing processes,’ explains Siddy.
The location of primary service routes for the mechanical, electrical, public health and containment systems was defined at the start. Regular workshops enabled Buro Happold to draw on CHT’s expertise to establish these routes, taking into account practical constraints for modularisation, including weights, transportation, access requirements, and spacing of systems.
The adoption of a modular servicing solution also set constraints for the stadium architecture, including ceiling heights, and the location of access points and risers. The West Stand, for example, contains 35 large, prefabricated modules for the primary runs.
These 10-tonne modules are floor mounted and create a ground level corridor with a integrated service walkway above. They enable ducts, pipes and cables to be safely accessed and maintained. ‘That was the beauty of the PCSA; the earlier we are involved with the client and their consultant team, the more value we can give to a client around the design solutions,’ says LOR’s Edwards.
With the primary routes established, it was important to maintain and monitor the quality of the digital models by reporting and recording clashes and coordination issues early, so they could be resolved before impacting the programme. ‘When we handed over the stage-four model to Crown House, very little changed in developing it into a stage-five model that could be built,’ says Andrew Waugh, associate director at Buro Happold.
Anything but bog standard
Prefabrication of the toilet units was a first for LOR. The number of toilet facilities within the stadium made these suitable for mass modularisation. CHT’s facility in Oldbury manufactured 268 modular integrated plumbing system modules, in two- and three-WC variants.
Each included all pipework and plumbing within panelled enclosures to enable them to be slotted directly into a finished space. The only site operations needed after installing the modules were connecting the hot and cold-water supplies, soil stacks and electrical connections for trace heating, and attaching the WC pans.
‘Imagine how many operatives we would need for a single toilet bay if each was installed as a traditional integrated plumbing system; the jointing of all that pipework, the commissioning and testing that would need to go on. Instead, all of that is done in a clean, hazard-free environment,’ says LOR’s Edwards.
In keeping with Everton’s aspiration for the stadium to be built with sustainability to the fore, building services systems are designed to provide flexibility of operation. The stadium will host around 20-30 matches a season, so there are more than 300 days a year without match-day revenue. On these days, the stadium will host events and conferences, to generate additional income – so the building services have been zoned to allow individual systems to run in isolation, with everything else effectively turned off. ‘If a system doesn’t need to run, then let’s not run it,’ says LOR’s Edwards.
The conditioned spaces are typically hospitality areas. Each area is served by dedicated, decentralised fresh air handling units (AHUs) with integrated reversible air source heat pump, sized to provide cooling and heating based on the occupancy profile of each space.
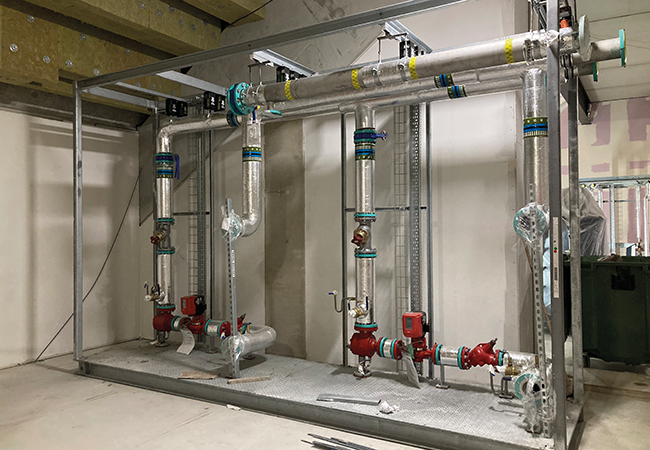
A plant skid manufactured in Laing O’Rourke’s factory
The use of integrated heat pumps helps minimise the size of the centralised heating and cooling plant and the length of pipe runs. ‘Using dedicated heat pump units is really efficient in terms of operational energy, and really good in terms of embodied carbon, because we don’t need huge centralised systems,’ says Buro Happold’s Siddy. ‘Simply by changing the AHU to one incorporating a heat pump, which is practically no bigger, there are huge benefits.’
Water usage, too, has been minimised through the use of low-flow fittings. These help minimise peak domestic hot-water loads, which occur just before kick-off. Buro Happold used its extensive stadium design experience to shed loads and improve security of supply with the addition of buffer vessels. Even so, at 3.2MW of a total 4.5MW heating load, hot-water heating is by far the largest primary heat demand. The inclusion of buffer vessels, however, helps overcome the peak and has enabled the gas boilers to be sized below peak demand. ‘This leads to more efficiency in terms of equipment, cost and everything else,’ Siddy says.
Stopping the rot
The stadium’s riverside site is exposed to strong, maritime winds. Buro Happold and CHT visited plant installations close to the site to see how materials and systems were fairing in this harsh environment, to ensure plant and equipment would not need to be replaced more regularly than normally expected.
‘We categorised all the different spaces: if they are completely external and subject to the external environment, they are given a C4 classification under BS EN ISO 13944, and the systems within there would be specified suitably,’ says Buro Happold’s Waugh. ‘Then, as you come away from the salty corrosive environment and into internal spaces, we reduced the classification and specification to suit.’
Water usage for pitch irrigation has been minimised through the addition of rainwater harvesting from the stadium roof.
As with water consumption, power, cooling and heating load profiles also vary considerably between match and non-match days. ‘Match days have short-term peak loads half an hour before kick-off and at half-time, which far exceed anything else,’ explains Siddy.
To come up with realistic power demands for the stadium, Buro Happold used its experience and benchmarking data from recently completed stadiums, including Arsenal’s Emirates Stadium, the Tottenham Hotspur Stadium, and the transformation of the London Olympic Stadium into West Ham’s new home.
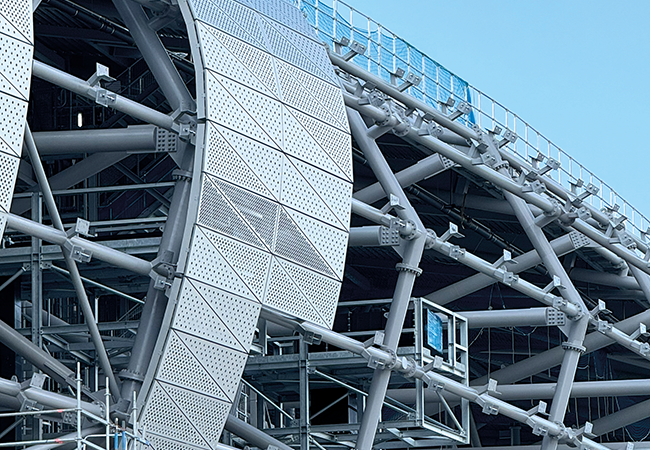
The stadium’s riverside location exposes it to strong winds, so materials and systems have to be able to withstand the harsh conditions
Electrical resilience
The total electrical load for the new stadium’s match and broadcast needs, and for catering, totalled 18MW. However, Buro Happold used its benchmarked data to anticipate how the stadium would actually be used and was able to apply a 60% diversity figure to the total electrical load, which brought it down to a more realistic 7.6MW. ‘The load we requested from Scottish Power Energy Networks is about 43% of the connected load; even then, we have spare capacity built into that,’ says Waugh.
Load diversity was also applied to the main electrical infrastructure, to ensure that it too was not oversized. This enabled smaller cables to be installed, to reduce costs and save on embodied carbon. In addition to diversity, electrical resilience is critical for the safety of the stadium’s 52,888 spectators. If a mains power failure should occur, all life-safety systems will continue to operate, as will the giant screens and all field-of-play lights, to enable the match to be completed with spectators remaining in their seats. ‘Match continuation for a Premier League club is huge; the show must go on,’ says Waugh.
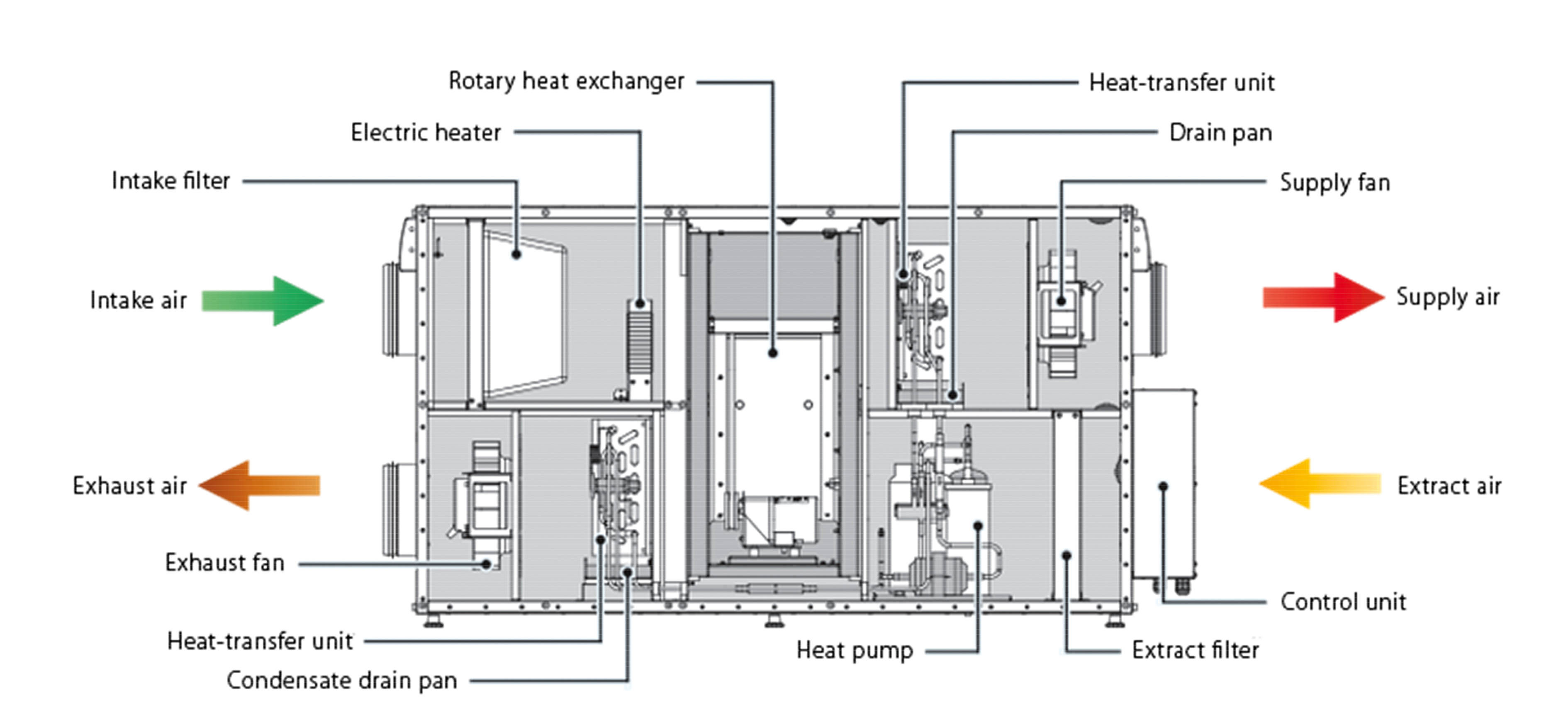
Integrated reversible ASHP heat pump unit
The site electrical supply benefits from two primary 33kV district network operator connections from independent electrical grids, either of which is capable of supporting the full electrical load. In addition, there are three 500 kW battery sets and one 600kW battery set, capable of delivering 9.3MWh of battery storage capacity.
‘If there was a mains failure, that would give us about three hours of continued operation, with some non-essential stadium services restricted, so that a game could easily be completed,’ says Waugh.
Life-safety systems – including public address, voice alarm and emergency lighting – have local, independent uninterruptible power supply systems for enhanced levels of resilience.
Construction of the stadium began in summer 2021 and fit-out is nearing completion. Everton aim to start playing there in 2025 – then we will see whether their new home inspires the Toffees to live up to their Nil satis nisi optimum motto.