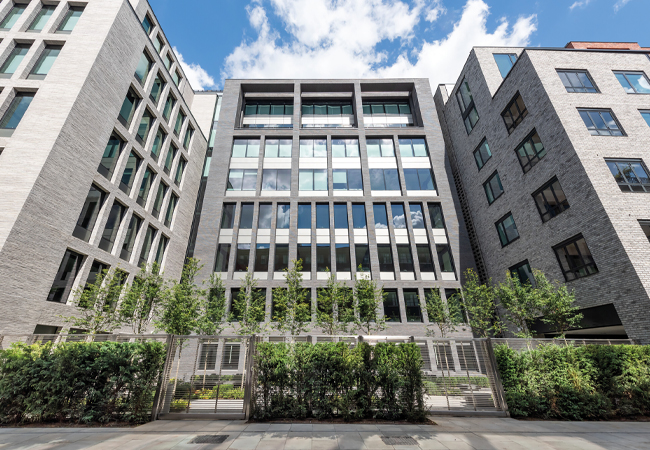
Retaining and stitching together existing buildings on the site meant the project took more than a decade to complete
The mixed-use scheme at 80 Charlotte Street is developer Derwent London’s first net zero carbon project. Completed in May 2020, this 35,000m2 development occupies a prominent island site bounded by four streets in London’s Fitzrovia. It features residential, retail and office space, plus a new public pocket park inspired by Paley Park in New York.
The engineering of the 30,000m2 speculative office building that anchors the development is key to the scheme’s low carbon credentials. It is one of the first major offices in London to be designed as an all-electric scheme. As such, it is heated and cooled using air source heat pumps (ASHPs) and powered by renewable electricity certified to be of guaranteed origin.
It has taken more than a decade for this pioneering project to come to fruition, largely as a result of trying to retain and successfully stitch together the collection of existing buildings that occupy the block. Architect Make worked with Arup to develop the design, the main element of which is a 90m2 block, built in the 1960s as offices for the Post Office and later occupied by advertising agency Saatchi & Saatchi. A section of the building’s façade is now woven into the new-build elements.
PERFORMANCE DATA
- Onsite energy generation – 2.4%
- Annual mains water consumption – 5.9m3 per person
- Airtightness – 50Pa 3m3.h-1.m-2
- Heating and hot water load – 4.95kWh.m-2 per year
- Overall area-weighted U-value for the façade – 1.32W.m-2.K-1
- Systems design life – 25 years
- Building design life – 60 years
- Embodied carbon (A1-A5) – 685kgCO2e.m-2
- Annual CO2 emissions (TM54 regulated and unregulated figures) – 25kgCO2.m-2 per year
‘There is a retained façade on Whitfield Street, which is part of a conservation area; beyond that, we’ve had to rebuild all of the building because of the condition of the existing structure,’ says project lead Rahul Patel, director, buildings, at Arup, which was the mechanical, electrical and sustainability consultant on the scheme.
The forward-thinking decision to consider an all-electric scheme was mooted by Arup way back in 2009, when gas was still the go-to fuel for heating. However, the proposal chimed with Derwent London’s ambitious sustainability goals, which include achieving a net zero carbon portfolio by 2030.
At the time the scheme was being developed, Arup was reviewing the potential for the electricity Grid to become greener in the future, and how this could result in buildings being designed to be all-electric, including the potential to be heated and cooled using heat pump technology. ‘We discussed with Derwent a series of likely scenarios for the carbon content of Grid electricity, the unit price of electricity, and the performance of heat pumps, all of which we expected to improve over time,’ explains Patel. ‘They trusted that our forward-thinking approach was right – and that has paid off.’
The decision to go all electric was based on carbon considerations and sound economics, Patel adds. From a carbon perspective, electricity is a ‘no-brainer’, he says, while its benefits from a cost perspective depend on the difference in price between gas and electricity. ‘What we couldn’t do is develop an all-electric scheme that means the tenants have to pay through the nose for energy.’
The concept was proven to be viable two years into design development. By then, Arup was able to model the building’s anticipated energy use in detail. ‘At that time, using a reasonably conservative analysis, the cost of electric was shown to achieve parity with gas,’ says Patel.
The forward-thinking decision to consider an all-electric scheme was mooted by Arup way back in 2009, when gas was still the go-to fuel for heating
Electricity is used to power three roof-mounted ASHPs, which provide all of the heat and most of the cooling for the building, with additional cooling supplied by two roof-mounted air-cooled chillers.
When the building operates in heating mode, the heat pumps – which are variously sized to enable heat supply to be matched to demand – provide all the heat. When the building has both heating and cooling demands, the heat pump system will supply heating and cooling simultaneously. Rather than reject heat, it is put back into the building.
When the building is operating in this mode, an optimiser will ensure the heat pumps are prioritised over the central chillers. ‘At that point, the coefficient of performance [COP] will go through the roof, because you’re getting extra bits of heat for the same input of electricity,’ says Patel.
For peak summer cooling, the chillers are prioritised. ‘Air-cooled chillers are slightly more efficient than a heat pump at providing cooling,’ Patel explains. ‘The optimising algorithm will bring the systems together from a COP perspective.’
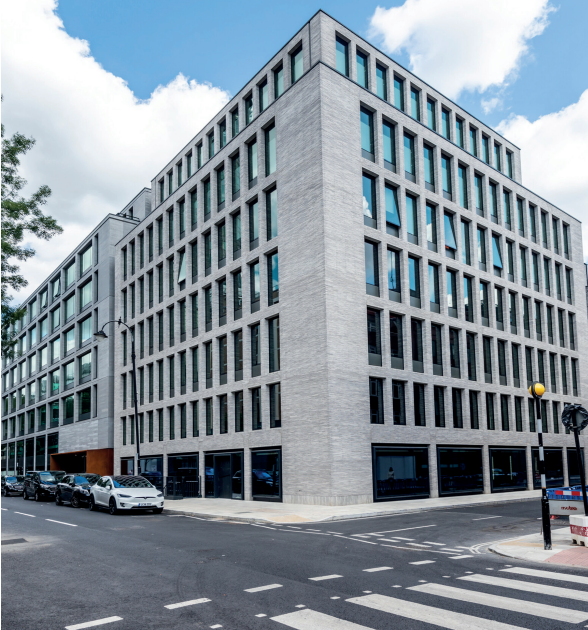
80 Charlotte Street occupies an island site bounded by four streets in London’s Fitzrovia
Heat generated by the ASHPs is supplied to trench heaters that ring the external perimeter of the 10 floors of offices, consisting of ground and lower-ground floors, and eight storeys above ground. Patel says the heating system design was ‘a bit more challenging’ using heat pumps because of the lower water temperatures.
‘To get the right efficiency of performance, heat pumps typically deliver water at around 45°C, which means the terminal devices, for example, need to be a little bit bigger to give the same output than if they were connected to a boiler supplying heat at 80°C,’ he explains.
Also, because the heat pumps use outside air as a heat source, ‘they need to see sky’, so have to be located on the roof. As a consequence, the roof has to have sufficient area to cope with the larger footprint of the ASHPs compared with that of a conventional gas-fired boiler with the same output.
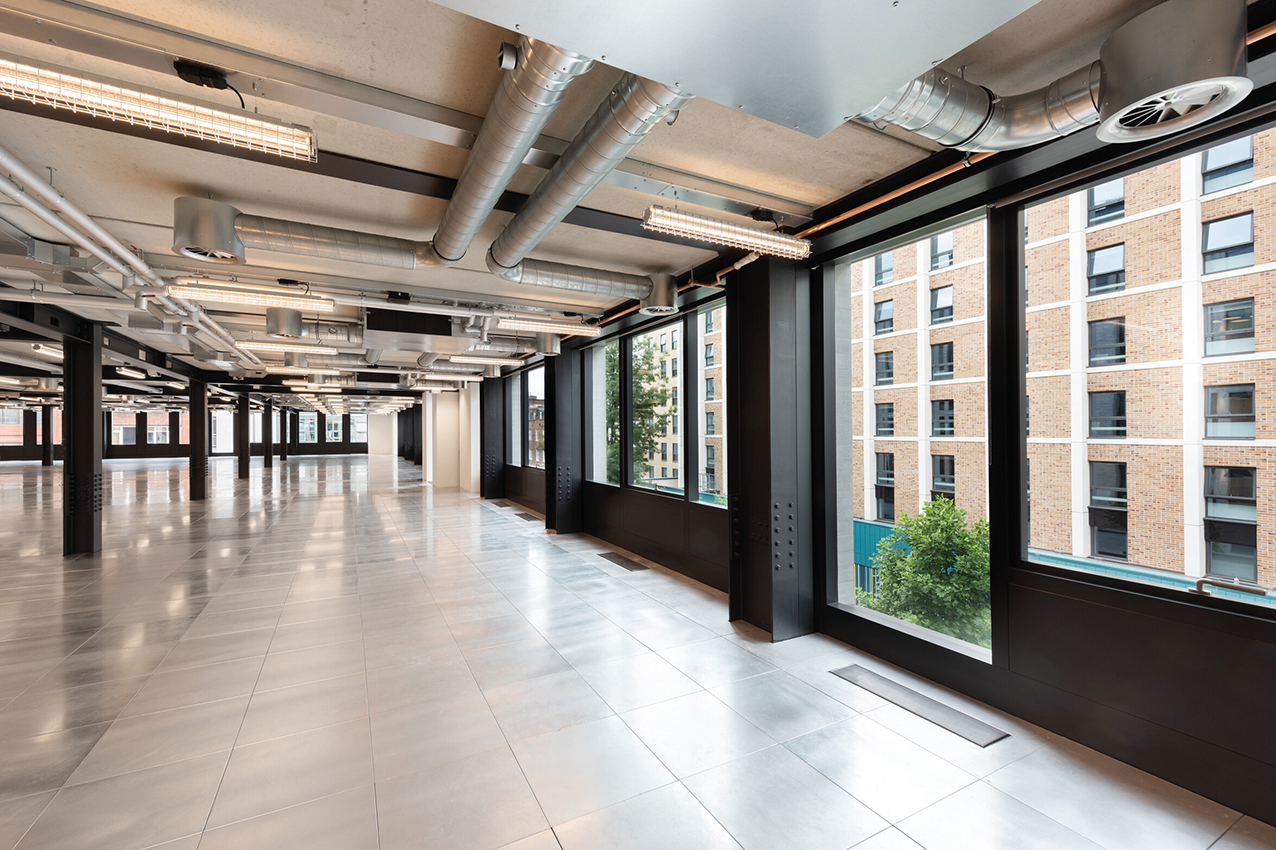
Chilled water, whether generated by the ASHPs or chillers, is supplied to soffit-mounted fan coil units (FCUs) distributed around the floor plates. The FCUs are controlled in two zones: a perimeter zone and an internal zone. To help minimise perimeter cooling loads Arup worked with Make to optimise the location of the glazed and opaque areas of the façade. ‘Glass is generally at high level to contribute to daylight levels on the floor plates,’ Patel explains.
An LED lighting system further minimises energy use in the main office areas. This is coupled to a DALI controller and daylight sensors, to allow light fittings to be dimmed automatically in response to ambient light levels.
EMBODIED ENERGY
The building is being promoted as having lower embodied energy. According to Derwent London, it has been designed to achieve 28% lower embodied carbon intensity than the RICS benchmark, with estimated embodied carbon of 850kgCO2e.m-2, versus the RICS Building Carbon Database (offices) average benchmark of 1,177kgCO2e.m-2. ‘When we designed this building, it’s fair to say that embodied energy was not as high up the agenda as it is currently; that said, the systems we have chosen are robust from an embodied carbon perspective,’ says Patel.
While the building’s façade is almost entirely new – aside from the retained section in the conservation area on Whitfield Street – it has been designed with the local vernacular in mind, referencing Fitzrovia’s variety of buildings, but with a very rational glazing proportion. ‘What is important is that the ghost of the existing building still exists,’ says Patel.
The new building incorporates the existing building’s low floor-to-floor height of around 3.3m, which Patel describes as ‘super lean’. With such a low floor height, the supply of fresh air to the office floor plates could have been an issue. However, the design team’s decision to relocate and consolidate the cores of the existing buildings into the centre of the plan has enabled the creation of three full-height atria. These allow natural light into the heart of the building and, through integration of engineering and architecture – plus an innovative design approach – provide a route for the ventilation ductwork. ‘Working with Make ensured we had atria in all of the right places, which gave us the opportunity to distribute the fresh air,’ says Patel.
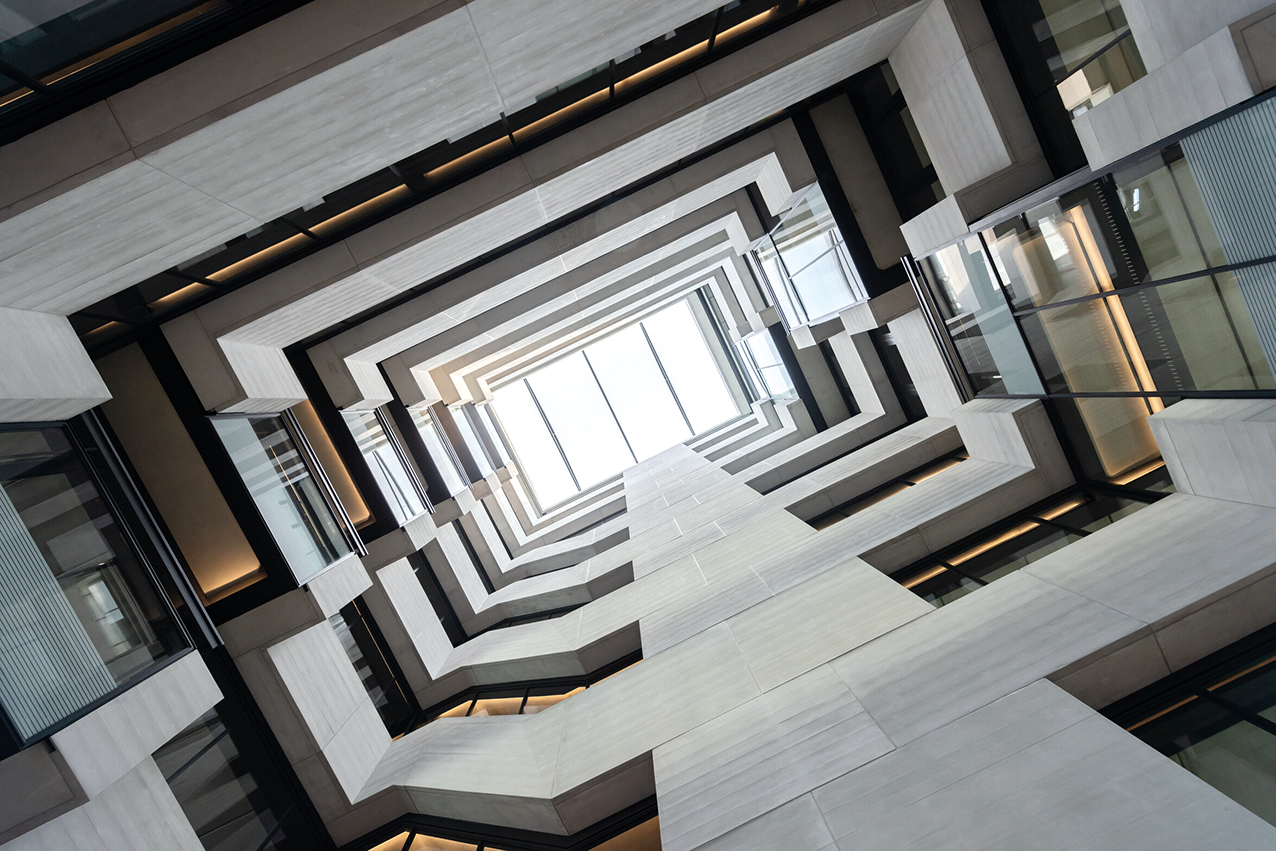
These full-height atria provide routes for ventilation ductwork
Three fresh-air ducts drop down these atria from roof-mounted air handling units, to supply air to the floor voids on each of the office levels. Fans in the perimeter trench heaters help draw the air across the floor plates, and the air returns to the AHUs through a series of ducts behind louvred panels at the core. ‘If you take the fresh-air ducts out of the main floor plate, you can squeeze the floor height down,’ explains Patel, who adds that the fresh air supply rate of 1.6L.s-1.m-2 is ‘at the higher end of the British Council for Offices scale, based on an occupancy of one person per 8m2’.
The façades incorporate openable windows. When the windows open, the heating and cooling switches off
In addition to mechanical ventilation, the façades incorporate openable windows, allowing the building to operate a perimeter mixed-mode ventilation strategy. When the windows open, the heating and cooling switches off.
The roof – as well as housing the ASHPs – is home to 80m2 of roof-mounted solar thermal panels. These preheat the domestic hot water (DHW), which is then topped up by heat from a dedicated set of ASHPs, to raise its temperature to around 65°C.
‘We looked at various renewable technologies for the domestic hot water, but, at that point in time, there were limited options from an all-electric perspective,’ Patel explains. Using dedicated heat pumps also enables the system to be run out of hours.
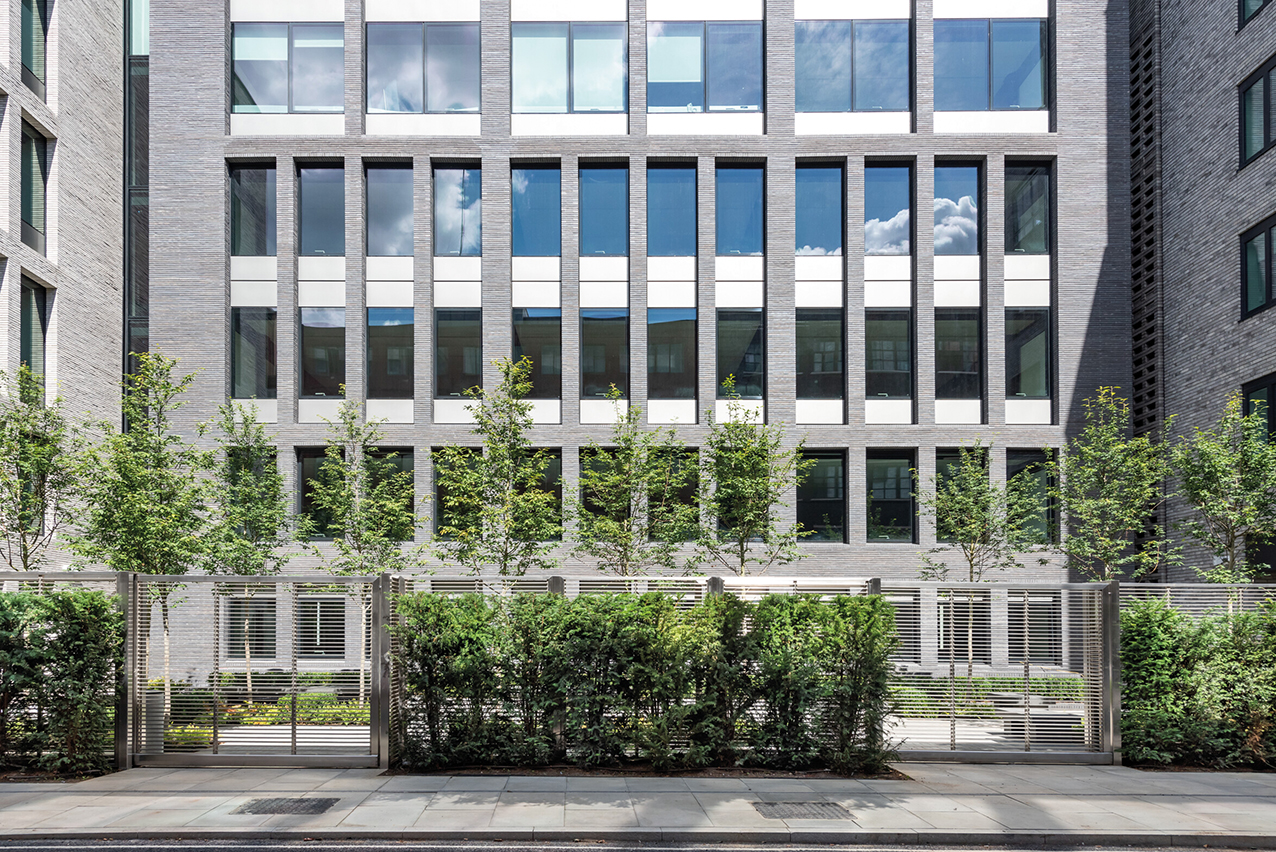
The solar system is self-regulating and sized at peak summer demand. At the limited times when the system generates more heat than required, radiators within the solar system ensure the water and components don’t overheat. The DHW tanks also include an electrical element as backup, but Patel says these are not intended to be used under normal operation.
At the outset of the project, Arup conducted a CIBSE TM54 study to get an idea of the expected performance of the building. Once the building is fully occupied, in-use electricity data will be analysed and compared against the TM54 modelling calculations completed at the design stage. ‘We have a smart system that links everything together, so we’re able to understand, from an energy perspective, how much we are consuming and where, on both the landlords’ side and the tenants’ side,’ says Patel.
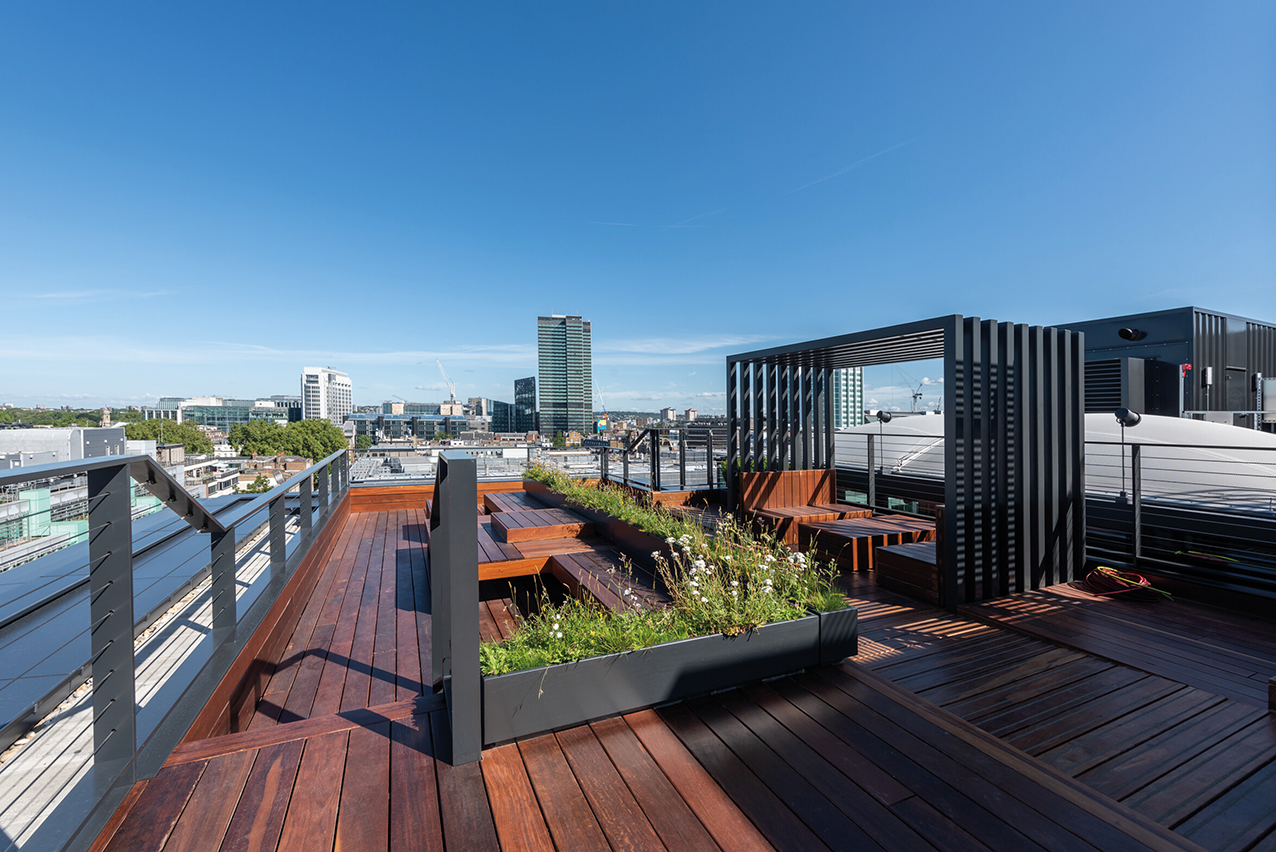
The scheme includes a roof terrace and a new public pocket park (left), based on New York’s Paley Park
As Arup is one of the building’s main occupiers, Derwent London will have a unique opportunity to work with the engineer to optimise its operational energy performance. ‘Our commitment to Derwent is that we’ll do all the commonly employed checks across Derwent projects, such as seasonal commissioning, energy monitoring and targeting,’ says Patel. ‘In addition, as a tenant, we’ll do this at a granular level; for example, we can measure the contribution we’re getting from the lighting switching off when daylight levels are good enough, and from opening the windows in the summer. We have real-time occupancy data alongside power consumption.’
According to Derwent, the building achieved Breeam excellent at design stage and is targeting Leed Gold and an Energy Performance Certificate B rating. Derwent London is now targeting all-electric heating and cooling systems for all its new developments, to help it achieve its goal of a net zero carbon portfolio by 2030. 80 Charlotte Street will be the reference point against which all of its subsequent developments will be measured. CJ
THE IMPACT OF COVID-19
The building was completed at the start of the coronavirus pandemic. Since then, Patel says Arup has carried out a retrospective review of the systems with Derwent, ‘to try to understand all the systems and how we might then address Covid with these’. For example, the review found that opening windows in addition to the mechanical ventilation was beneficia. ‘The building has a really good ventilation rate, but we have the opportunity to open windows and give it a boost if we need it – although you wouldn’t choose to do that all of the time from an energy perspective,’ says Patel.
Completion of the building during the pandemic also required changes in the way commissioning was undertaken. Many of the inspections, for example, were carried out remotely, using video links along with factory tests, where data and monitors were witnessed remotely. ‘You can have FaceTime calls and WhatsApp videos where you can say “this is the gauge I want to see”. We embraced technology to shift the way we do things,’ says Patel.
Some commissioning had to be done in person, however, including the black building tests, where multiple things were happening at once. At such times, Patel adds, design and build contractor Multiplex ensured that attendees could safely maintain social distancing on site.