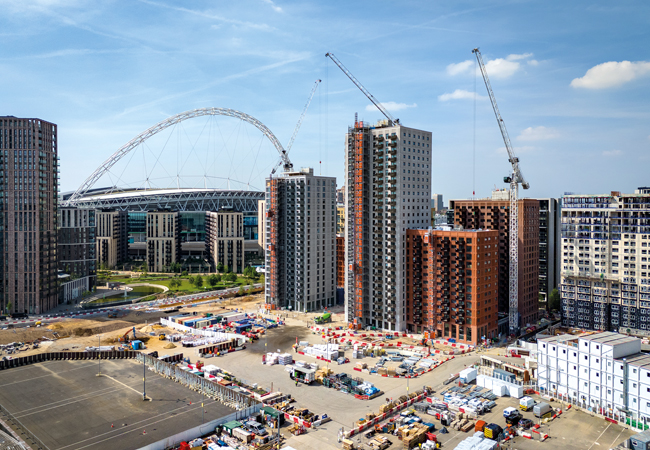
The site welfare facilities for the Wembley Park residential project are in the bottom right-hand corner
Site welfare facilities are generally assembled from transportable, stackable modular cabins that are kept comfortable with electric heating and split air conditioning units. In addition, hot water for wash hand basins, showers and sinks is frequently produced locally, often with electric point-of-use heaters.
It is a setup that can consume a lot of energy during the construction, adding to the contractor’s running costs and increasing carbon embodied in the building.
Now, at contractor Sisk’s residential development for Quintan at Wembley Park, an innovative, containerised heat pump-based energy module is being trialled as a more energy efficient solution to supplying heating and cooling to the site’s welfare facilities. The energy module, designed and built by Solaris Energy, has been up and running since January this year, and it has already helped reduce Sisk’s site energy bill by around £10,000 a month.
The project team
Developer: Quintain
Contractor: Sisk
Heat pump design and installation: Solaris Energy
Building services engineer: ADR Consulting Engineers
Heat pump manufacturer: Kronoterm
What’s more, the energy savings have resulted in 14 tonnes of carbon savings so far this year, which will be reflected in the embodied carbon of the six apartment blocks that Sisk is constructing for Quintain over the next five years.
‘Like all good ideas, this one was formulated in a pub over a cold pint of beer,’ says Daniel Large, director and owner of heat pump specialist Solaris Energy. He had been playing around with the concept of developing a mobile, containerised heat pump system that could be used to deliver energy-efficient, simultaneous heating and cooling. So, when a conversation with the project director turned to ways in which the amount of energy consumed by its site accommodation at Wembley Park could be reduced, Large suggested trialling a heat pump-based solution.
The welfare facility was being planned to accommodate up to 2,000 operatives when the project is at its peak. ‘Sisk sent me details of the proposed facility, which was, in effect, a temporary, four-storey building, complete with offices, meeting rooms, induction rooms, a canteen and kitchen, changing rooms, toilets and showers – it was massive,’ Large says.
Solaris Energy set about developing a heat pump-based solution – capable of meeting all the welfare facility’s heating and cooling demands – that would fit into a standard 6 metre shipping container, to enable it to be relocated at the end of the project.
The heat pump specialist worked with ADR Consulting Engineers to produce a thermal model of the building and its associated heating and cooling loads. It then developed a solution based on two heat pumps (normally used as ground sourced heat pumps) that would deliver up to 160kW of heating and 150kW of cooling.
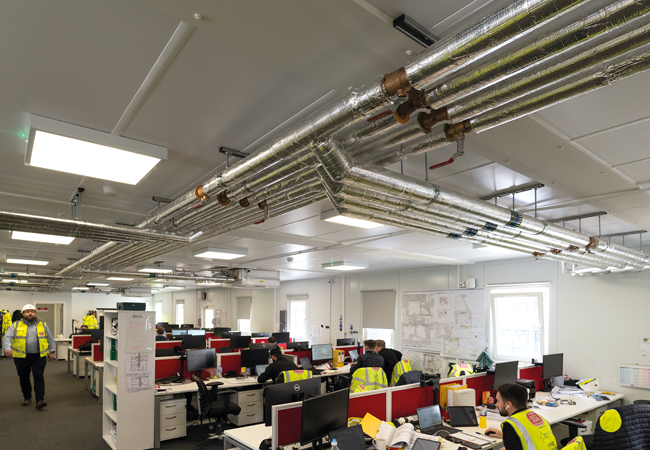
Part of the distribution system in one of the site offices
‘The water-to-water heat pump captures heat from cooling to reuse it for heating, or to pre-heat domestic hot water [DHW]. It simultaneously provides heating and cooling,’ Large explains. In addition to the heat pumps, the container contains a chilled water buffer tank, a low-temperature hot water (LTHW) buffer tank, and a pre-heat tank for the DHW.
The DHW pre-heat uses heat reclaimed from cooling the facility to heat a 500-litre vessel full of water to a constant 55oC. The DHW is pre-heated by circulating the system through a coil contained within the tank of heated water. ‘Rather than oversize the system to meet the once-a-day peak demand from the showers, we decided to continue using electric showers and point-of-use water heaters, which we supply with water pre-heated to a temperature of 50oC,’ says Large. The DHW is then brought up to a supply temperature of 60oC by the point-of-use devices, to kill off any legionella bacteria, with a thermostatic mixing valve to deliver water at an appropriately safe temperature.
ADR Consulting Engineers’ thermal model showed the meeting rooms would require cooling throughout the year, even in winter, and that – for a large part of the year – the facility would require simultaneous heating and cooling.
‘As soon as there is a cooling demand, rather than rejecting the heat outside, we take the absorbed heat to the heat pump evaporator, where it is turned into high-grade heat by the heat pump before being stored in the LTHW buffer or DHW preheat vessel, or it is used directly for heating if there is a demand,’ Large explains.
‘Heat that would have been wasted is recovered and used in the building, which gives a better system COP [coefficient of performance],’ he adds.
The site electricity bill has dropped 60%, to £15-20,000 – even though the price of electricity has
increased by 77%
The heat pumps also connect to two dry air coolers installed on top of the container. These reject or absorb heat depending on the system demand. ‘If there is cooling demand and no requirement for heating – and the buffer tanks are up to temperature – we’ll use the dry air cooler to dump surplus heat,’ Large says. ‘Similarly, in mid-winter, when we might not have any cooling, we’ll use the dry air cooler to source energy from the air to generate heat for heating and hot water.’
A particular challenge with using a GSHP coupled with a dry air cooler to provide heat when it is cold outside is that any moisture on the dry air cooler can freeze and frost the heat exchanger. ‘Frost is not something you’d normally consider when using a water source heat pump,’ Large says.
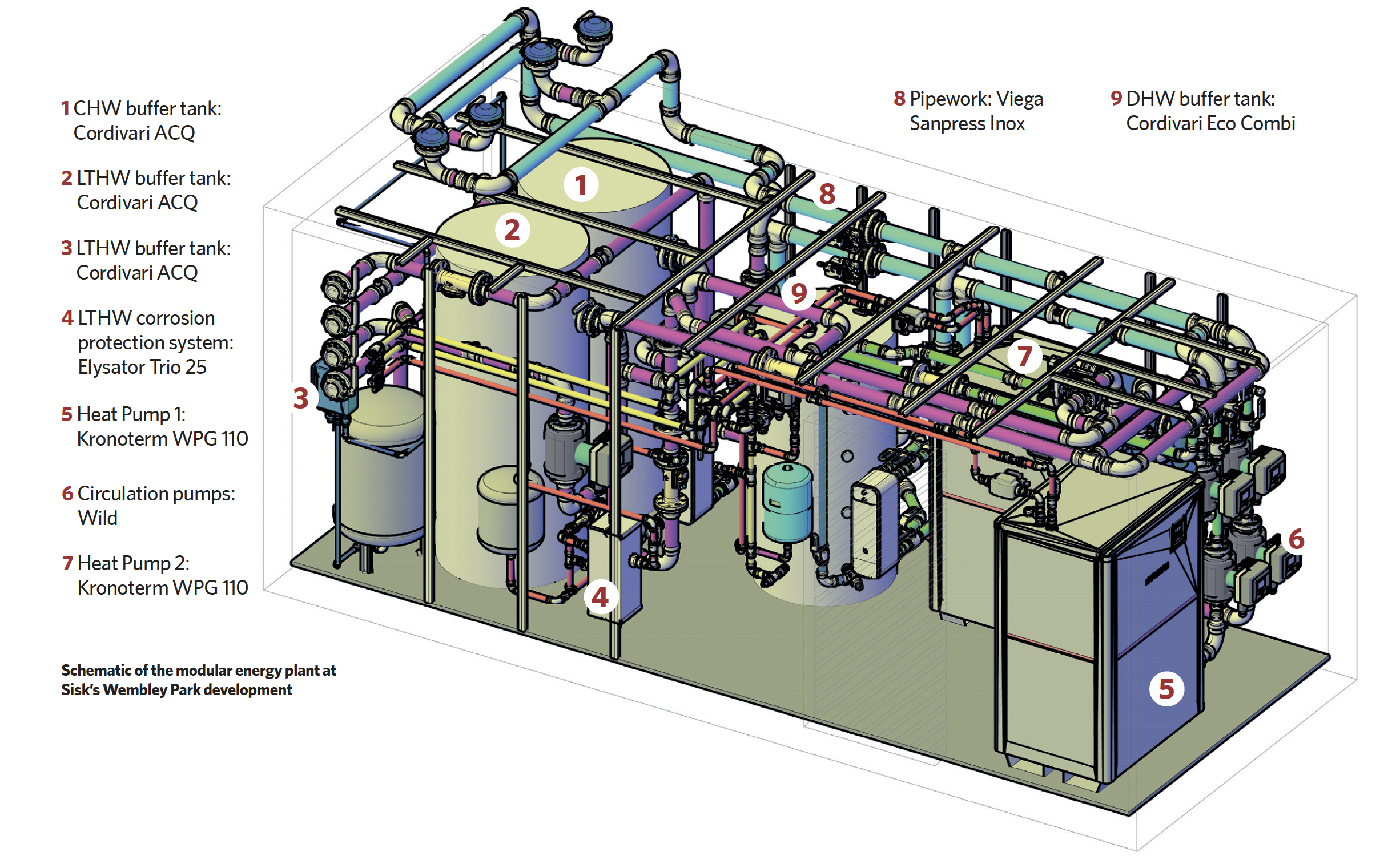
The containerised plant room, with a dry air cooler above, services a fourstorey site accommodation block
Fortunately, the manufacturer was able to adapt its air source heat pump control logic to work with its water source heat pump, so it could run a defrost cycle. ‘This allows us to use the thermal store, or even bring a compressor online, to defrost the heat exchanger if we need to,’ Large explains.
In April 2023, while the accommodation modules were being assembled on site, Large visited the site with ADR Consulting Engineers to establish how best to tie in the containerised heat pump system to the temporary building, and to establish heating and cooling pipework routes.
‘A heat pump is only as good as the system to which it is connected, so we had to develop a low flow temperature solution to ensure we could get the best energy reduction from using heat pumps,’ he explains. ADR Consulting Engineers designed a simple heating circuit, using radiators for the welfare facility’s ground and first-floor site accommodation, and fan coil units (FCUs) to deliver heating and cooling to the second-floor subcontractor office and Sisk’s third- and fourth-floor offices.
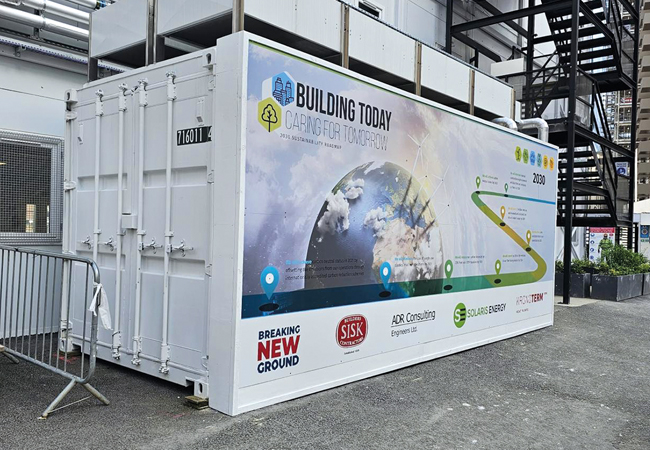
The containerised plant room, with a dry air cooler above, services a fourstorey site accommodation block
Along with the mobile energy module, the radiators and FCUs are intended to be reused at the end of the project. Copper is used for the connecting pipework inside the building, which, Large says, will enable it to be recycled in future ‘when the facility is decommissioned’.
The containerised heat pump system and buffer vessels were connected using stainless steel pipework, along with all the system controls, in an off-site process. ‘It is a plug-and-play solution, with everything inside the box,’ Large says.
The container was shipped to site in October, commissioned in November, and powered into use in January.
Heating and cooling has been scheduled to run between set times, with the system turned off out of hours. Weather compensation is also used to maximise system efficiency by varying the system temperature with outside temperature – so, at 0oC, the heating runs at a temperature of 40oC, which will increase to 50oC if the temperature drops to -10oC. Similarly, the cooling is designed to run at 12oC when it is 20oC outside and get progressively colder as outside temperatures increase.
The innovation has been successful. In the short time it has been in operation, its COP has been improving steadily and is currently running at a COP of 4.9, which, Large says, is ‘pretty good for a temporary welfare facility’.
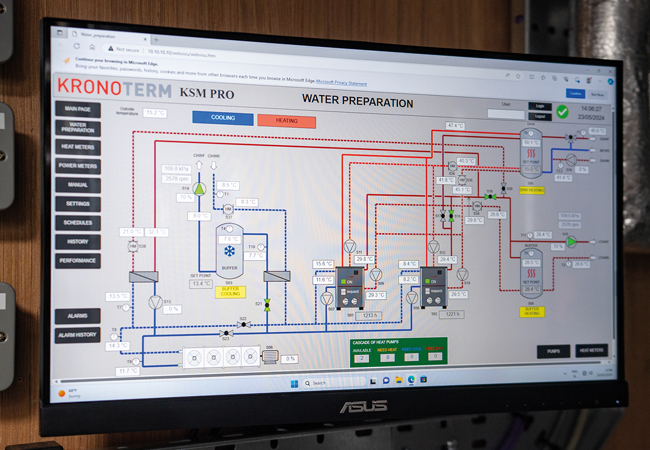
Display showing real-time operational data
Savings in electricity use are equally impressive. On a previous site between 2017 and 2019, when the cost of electricity was £0.13 per kWh, Sisk was spending £25-£30,000 per month on site electricity. On the energy module site, the site electricity bill has dropped 60%, to £15-£20,000 – even though the price of electricity has increased by 77%, to £0.23 per kWh.
Large acknowledges that, if the cost of electricity was to fall, the savings from the heat pump solution would be less impressive compared with an all-electric solution, but the carbon savings would remain the same.
Perhaps more impressively, Large says the figures do not take into account additional infrastructure savings, including a reduction in the size of the site’s leased step-down transformer, which was reduced in capacity from 2MW to 1.5MW, saving an additional £120,000 on set-up and leasing costs to date. ‘If people are truly driven to reduce energy consumption, it can be done. The capital cost can be high, but the savings are not limited to the energy consumption alone.’