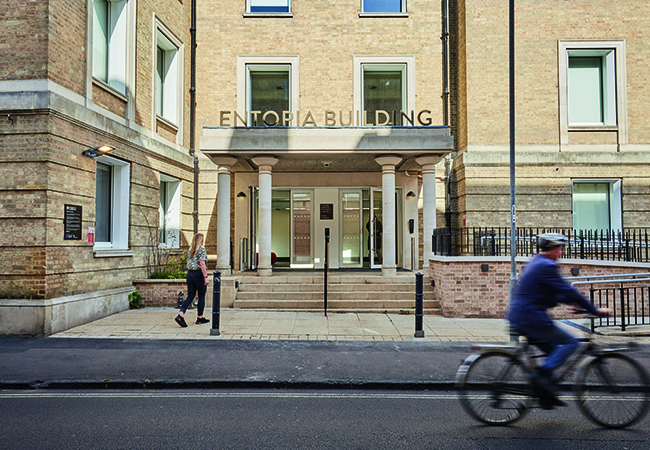
Entopia is an exemplary retrofit. It had to be. The 1930s building in Cambridge, originally a telephone exchange, has been transformed into a new energy-efficient home for the Cambridge Institute for Sustainability Leadership (CISL).
Project team
Client: Cambridge Institute for Sustainability Leadership
MEP & Passivhaus: Max Fordham
MEP engineers up to RIBA stage 3, Passivhaus designer from stage 3 to completion, BREEAM Assessors: BDP
Architect and Passivhaus designer up to Stage 3: Architype/Feilden & Mawson
Main contractor: ISG
Mechanical contractor: Kershaw
Electrical contractor: REL
Controls specialist: Learnd
Air handling units: Swegon
VRV system: Daikin
Architype was PH designer up to Stage 3 and then BDP to completion
The brief set by CISL for the retrofit was for the revamped building to achieve Breeam Outstanding, EnerPHit Classic and Well Gold. The client also wanted the scheme to target low embodied carbon and to maximise its use of bio-based materials. Most challenging of all, CISL wanted the scheme to demonstrate that, with a challenging brief and a committed design team, a deep, green retrofit could be delivered at a cost competitive with that for a conventional office refurbishment.
As with all Passivhaus projects, the starting point in delivering this ambitious retrofit was adopting a fabric-first approach. Although not listed, the concrete-framed, brick-clad, five-storey building (plus basement) is located within a conservation area, and the planners were keen to retain its somewhat utilitarian appearance.
To improve the thermal performance of the building envelope, the mock Georgian sash windows were replaced with energy-efficient triple-glazed units. Without the timber lattice of transoms and mullions, the new windows had 60% more glazed area, which helped increase daylight levels. Internally, wood-fibre insulation and lime and cork plaster were added to the walls, to improve their thermal performance and enhance fabric airtightness.
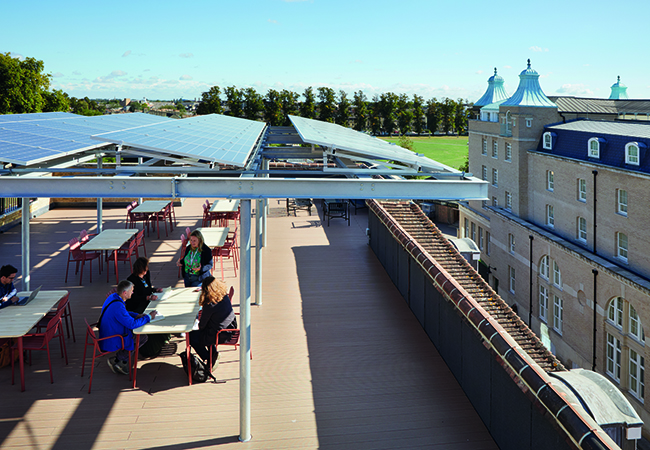
PVs are mounted on a steel frame that was used on a Marvel film set
‘The massing of the building is fairly efficient, so by the time we’d made the glazing work hard and improved the airtightness, we didn’t need to fit a huge amount of insulation,’ says Gwilym Still, director of Passivhaus at the project’s MEP engineers, Max Fordham.
The benefit of having a thermally efficient envelope is that it contributes to the efficient control of internal conditions and reduces reliance on building services. ‘Improving the thermal fabric performance significantly reduced the amount of plant required, which, typically, is one of the largest impacts on a refurbishment project,’ Still explains.
To enable the removal of the building’s gas supply, the building services solution is all electric. Max Fordham’s approach is based on the conventional Passivhaus methodology of supplying fresh air via a mechanical ventilation with heat recovery (MVHR) air handling unit (AHU). This supplies variable air volume (VAV) boxes, linked to temperature and CO2 sensors, to control the volume of air supplied to each space. A master VAV box controls the total volume of air supplied to each of the floors. Air extract is via corridors and WCs, back to the thermal wheel heat exchanger in the AHU before being expelled.
The AHU is the main source of heating for the building. As such, it incorporates an integral air source heat pump. ‘The AHU can supply about 80% of the total heat demand,’ says Still.
Embodied carbon
A major focus of the project was the optimisation of carbon over a 100-year period, with upfront and long-term costs and carbon influencing every design decision. In addition to retaining the main building superstructure, materials used in the refurbishment were either repurposed or selected to minimise embodied carbon.
Bespoke assessments included the existing WCs; while replacing them added more upfront carbon, it also significantly reduced water usage, which meant this carbon was paid back quickly.
Existing materials were reused where possible, including carpet tiles in the entrance area and raised access floor panels, which were cleaned and put back without a floor finish.
In addition to the steel from a film studio for the PV rooftop canopy, and the 350 light fittings from a fit-out project in London, the building incorporates a reception desk recycled from Netflix and is finished using paint with 35% recycled content.
According to CISL, the total whole life embodied carbon of the refurbished building was 409kgCO2e/m2, including in-use and end-of-life carbon, over a 100-year building life (based on a RIBA Stage 5 construction stage assessment), which, CISL says, ‘compares very favourably to new construction’. Omitting in-use and future phases, and considering only the carbon embodied in the building at handover stage, the figure stated by CISL is much lower, at 130kgCO2e/m2.
In winter, the heat exchanger pre-warms the incoming supply air using heat reclaimed from the exhaust air. Supply air then passes over the heat pump heating coil, which can further heat it up to a maximum temperature of 27°C.
The amount of heat that can be supplied to a space is limited by fresh air flowrates and the temperature of the supply, so some of the spaces also incorporate wall-mounted, direct electric radiators to top up the heating provision. These are under occupant control and operate independently of the building’s Trend BMS.
Summer comfort provision relies on a combination of the building’s exposed thermal mass, natural ventilation provided by opening windows, summer bypass on the AHU heat exchanger fresh air supply, and night cooling using the mechanical ventilation system. The temperature of the supply air can also be lowered to around 23°C by running the AHU heat pump in cooling mode.
Still says: ‘The temperature of supply air is based on outside air temperature, but the flowrates into the spaces are based on space temperatures and CO2 levels; if a room is getting a bit warm, it will get more mechanical ventilation and occupants can open the window.’
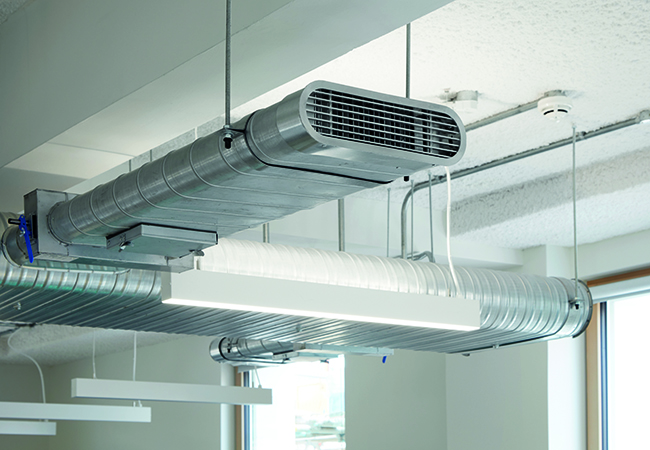
The AHU heat pump can supply air down to 23°C in the summer
This cooling strategy is supplemented with a variable refrigerant volume (VRV) system linked to fan coil units (FCUs) to provide local cooling, as well as heating in winter. The system was introduced after detailed thermal modelling showed that rooms with higher occupancy and/or solar gains would require active cooling to keep them at a comfortable temperature. FCUs are controlled via the BMS and by occupants via wall-mounted local controls. Branch selector boxes allow the FCUs in different zones to operate in heating and cooling modes simultaneously. This hybrid cooling strategy was tested against current weather files and showed a pass for Well and Breeam, and for adaptive comfort criteria, based on 2050s weather data.
Blinds are installed on the windows to prevent glare and reduce the risk of overheating. Still says there are ‘opportunities’ to improve summer comfort and future-proof the building. These include: enhancements to the cooling delivered by the central AHU beyond ‘the peak lopping base case’; increasing night-purge ventilation; and leaving windows on upper floors open overnight. Other potential interventions include the addition of solar-control film on the glazing and external shading, and increasing the capacity and extent of the VRF system.
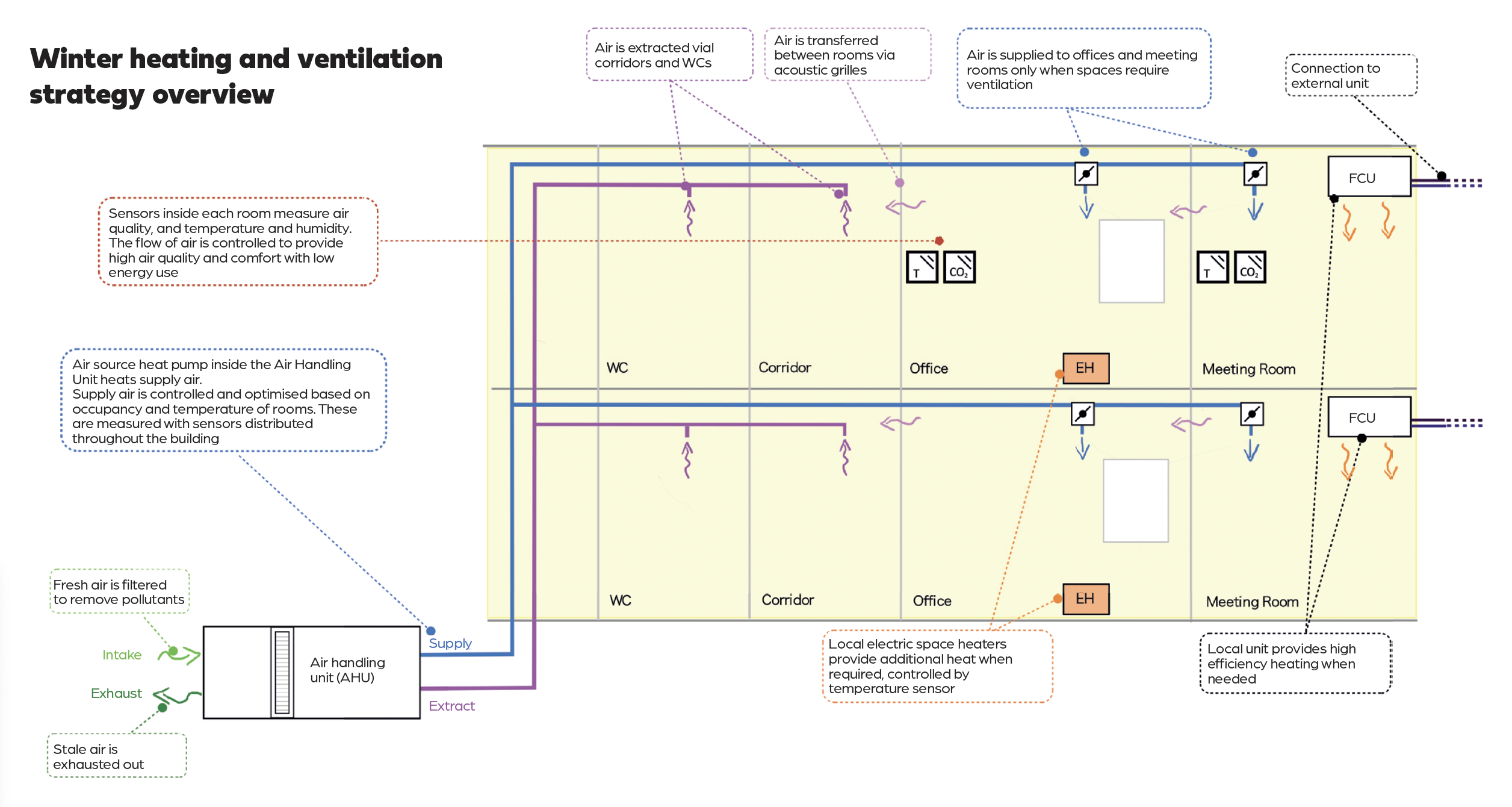
Artificial light levels in the offices are controlled by both daylight levels and presence detection, while over-desk downlighting is controlled manually. Light fittings are a mixture of recycled and new. Recycled fittings were supplied by the main contractor, having been salvaged from a Cat A fit-out in London. New fittings incorporate a 3D-printed plastic case, which Still says is capable of being reprocessed and reused up to six times when the fitting reaches the end of its useful life.
Domestic hot water is supplied through low-flow fittings to wash hand basins and showers using electric point-of-use heaters.
The design team even found space on a flat roof at the rear of the building to squeeze in a small photovoltaic (PV) array. This is expected to generate 13,800kWh/yr. The PVs are mounted on a steel frame salvaged from a Marvel Eternals film set to support it above seating. Still says: ‘I really like this bit of the project; it used to be a plant enclosure with boilers and ventilation kit; now it’s amenity space with the PVs generating renewable energy and providing shade to make the space more comfortable.’
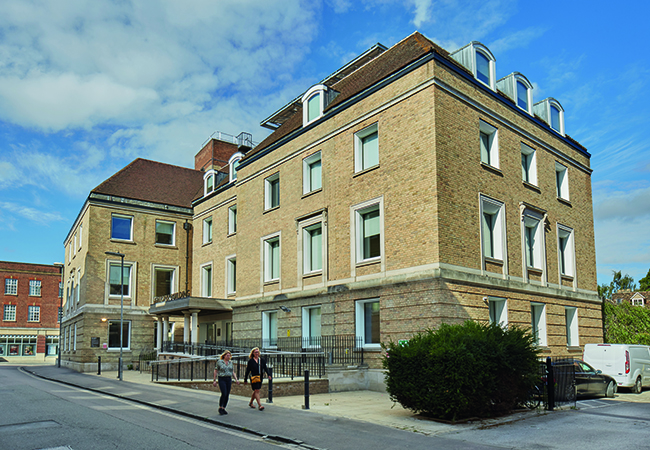
The 1930s building was formerly a telephone exchange
The building was occupied in September 2022. Since then, post-occupancy evaluation and ongoing seasonal commissioning have been used to fine-tune the building, with additional input from the main contractor, AHU manufacturer, and the controls specialist. Occupant feedback was sought as part of the seasonal commissioning process. This highlighted an intermittent issue of cold air being supplied to spaces through the ventilation system when in heating mode. Investigations found the issue corresponded with the times the AHU heat pump was running in defrost cycle.
The solution has been to reduce the supply air temperature and advance the ‘on’ time of the AHU in the mornings, to enable spaces to be preheated more steadily before occupancy.
Predicted energy use intensity (EUI) was 54kWh·m-2 per year. However, the actual EUI is slightly lower, at 52kWh·m-2 per year, dropping to 49kWh·m-2 per year if the contribution from the PVs is included. Still says these figures ‘compare well’ with industry targets for new-build offices, including the LETI Climate Emergency Design Guide and the RIBA 2030 Climate Challenge, which both have a target of 55kWh·m-2 per year.
Carbon: retrofit versus build anew
Desk-based Sankey analysis compared the impact of refurbishing this building with the creation of a notional new building. This comparison suggested that a newly constructed building, including demolition of the existing structure, would generate between 970 and 1,620 kgCO2e.m-2. In contrast, it was estimated that a deep retrofit would generate 400 kgCO2e.m-2 – hence it was the preferred option.’
At £12.69m, the project is estimated to have cost 8% more than a conventional refurbishment. However, CISL expects the additional cost to be ‘recouped within five to eight years from operational energy savings’. ‘That the Entopia Building uses dramatically less energy than its predecessor is a success in its own right,’ said the client.
‘That it has minimised the use of new materials through circular design and concurrently reaches three challenging building standards is exceptional. Its true impact is still to come, however, through its role as a beacon project: an exemplar and teachable resource that creates positive ripples of change throughout the built environment, influencing the course of other projects, policies and investments.’
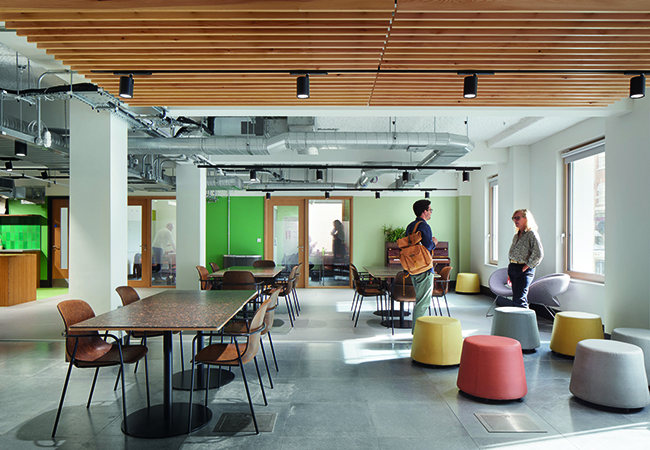
Heating and cooling is supplemented by a VRV system linked to fan coil units
Judges at the CIBSE Building Performance Awards were equally impressed, and the scheme won Project of the Year – Refurbishment, plus the coveted Building Performance Champion award. They said: ‘The Entopia Building showcases the future of environmentally conscious design, achieving a staggering 84% reduction in whole life carbon compared with standard retrofits.’
For more on this project and to access the project data, go to https://bit.ly/CJEntBP