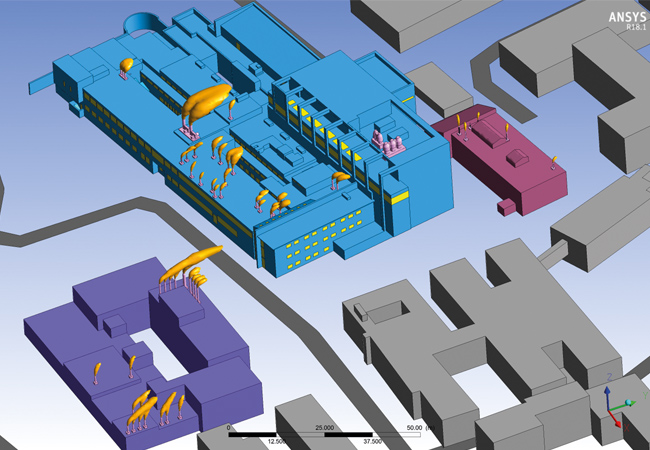
Fumes from labs modelled using computational fluid dynamics
The life sciences sector has seen a massive surge in public and private funding in the past few years. This is driven by an increased demand for biotech facilities because of advancements in technology, and a demand for personalised treatments and therapies as the world grapples with an ageing population.
Retrofit has also become a companion to life sciences development, mainly because of a lack of new spaces that can handle the structural and services demands of life sciences buildings. There has also been a shift in demand for city-centre locations, driven by proximity to universities, hospitals and a skilled workforce.
Cambridge, Oxford and London, deemed as the life sciences’ ‘golden triangle’, are great examples of this. Both offices and retail have seen a decrease in demand, creating an opportunity to repurpose these spaces for science laboratories, where the demand remains strong.
The retrofit challenge
All types of laboratories need supplementary ventilation and some form of fume extraction, and this can be a particular challenge for a retrofit in a built-up area.
The higher ventilation rates required to extract fumes from laboratories means risers need to be larger than those for offices to accommodate more intensive services, and ceiling void space needs to increase by 50cm to make room for larger duct work. Existing buildings that already have high floor-to-floor space, such as shopping centres, are more easily retrofitted as laboratories.
In the past, a lot of buildings were thought to be structurally unsuitable, as external vibrations hindered the ability for optical microscopes in labs to achieve stable images. However, recent technological advancements such as active vibration damping, which operates in a similar way to noise-cancelling headphones, have helped overcome such structural issues.
Specification of ventilation starts with a suitable selection of fume cupboards and biosafety cabinets, for the specific application and chemicals that are anticipated to be used. Ducted fume hoods are typically the most effective for removing fumes.
The placement of hoods must be carefully considered to capture contaminants effectively, by ensuring that there are no obstructions blocking airflow to the hood. Computational fluid dynamics (CFD) modelling is often needed to validate the design before implementation.
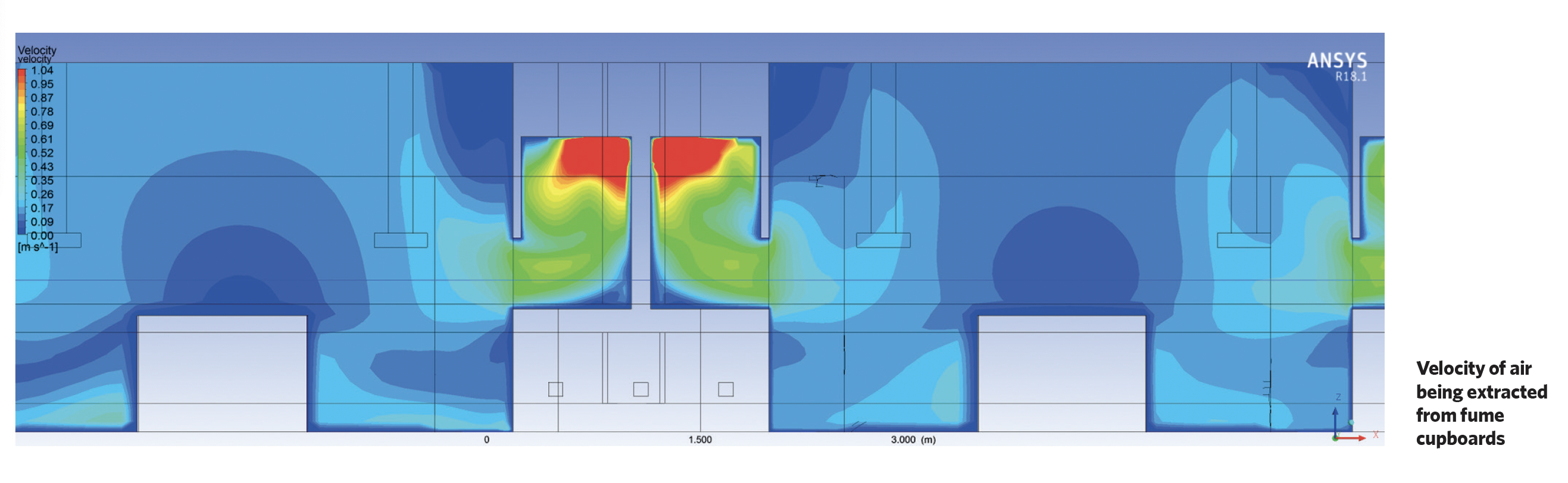
A minimum air change rate must be achieved for safety purposes in laboratories and this is typically three times more than conventional office buildings, requiring larger HVAC facilities.
It is important to consider where the fumes are discharged and their proximity to other air intakes and receptors.
Conventionally, air intakes must be separated from discharges by at least 10 metres, and fumes are discharged vertically at least three metres above other parts of the building. However, for city centres with an abundance of developments, more detailed assessments are often required.
When direct, ducted systems cannot be incorporated, recirculating systems with activated charcoal air filters and scrubbers can be considered, although these are expensive alternatives.
A minimal air change rate must be achieved for safety purposes in laboratories and this is typically three times more than conventional office buildings, requiring larger HVAC facilities
Higher ventilation rates and fume-extraction systems will have a significant impact on a building’s energy use, so it is essential that buildings services pay particular attention to energy efficiency.
As a first step, it is important to work with the scientists who will be occupying the buildings in the design stages, to optimise the parameters and the airflow design, and prevent overdesign.
Where possible, spaces should be lab-enabled, rather than fully fitted-out. This will provide end users with an adaptable blank template they can fit-out however they want. This is more attractive than receiving a fully fitted-out space that may not meet specific requirements and could put occupiers off at due diligence stage, or lead to expensive refit financial and carbon costs.
Modulating the airflow to match actual demand reduces energy consumption during low-activity periods, while still providing adequate ventilation when needed.
Variable air volume flowrate systems and demand-control ventilation can adjust the ventilation rates based on real-time occupancy and contaminant levels. Implementing scheduling controls can also optimise ventilation operation based on occupancy patterns and laboratory usage schedules.
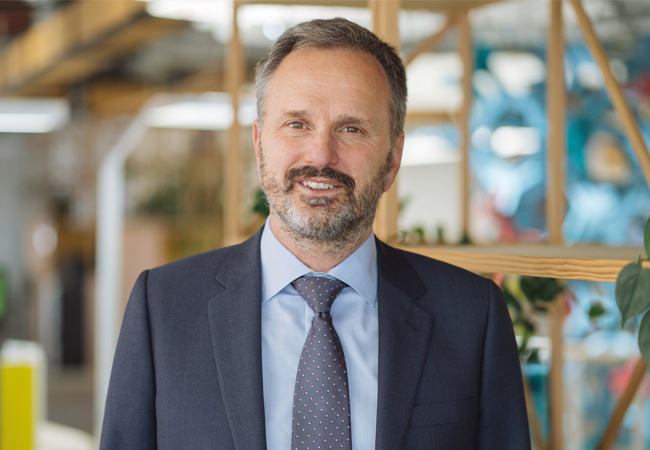
Rob van Zyl
Natural ventilation can be used in certain situations. There are other considerations such as prioritising recirculation over full ventilation by using activated charcoal filters or liquid scrubbing to wash the air as it passes through. Heat recovery systems must also be implemented wherever practical, to capture and reuse heat or coolness from exhaust air to precondition incoming fresh air.
Typically, the requirement for safe removal of fumes is to discharge fumes at least three metres above the highest point of buildings, and this means having tall and unsightly stacks.
In the UK, planning regulations impose restrictions on the height of stacks and exhaust vents as part of the overall planning permission process. This is primarily to address concerns of air pollution, visual impact, and potential adverse effects on the environment and neighbouring properties.
Planning authorities need evidence to show that vertical stacks are tall enough to adequately control the dispersion of pollutants and they will want to see how the visual impact of stacks on the surrounding landscape have been considered.
Stack heights need to be specified to minimise impact on air quality. They will be based on factors such as the type of emissions, local air quality standards, and the proximity of sensitive receptors, such as residential areas, schools, or hospitals.
The speed at which air is discharged from a ventilation system – the efflux velocity – can determine stack height. By increasing the velocity of vertical discharge, fumes can be pushed higher and the stack height reduced. CFD modelling can be used to predict whether or not the concentration of released fumes will exceed the required parameters of the nearby receptors. It should be borne in mind that higher efflux velocities require more energy.
New technologies in the sector
Some of the most noteworthy technologies in the sector are recirculation fume cupboards, liquid scrubbing, and active vibration control, which are particularly helpful in retrofit.
Innovations in heat exchanger design and materials are improving heat transfer efficiency and durability. Technologies such as microchannel heat exchangers, enhanced surface coatings, and additive manufacturing techniques enable the development of compact, high-performance heat exchangers that can effectively recover waste heat from various sources.
The integration of smart sensors, data analytics, and control algorithms enables real-time monitoring, optimisation, and predictive maintenance of heat recovery systems based on changing conditions. They can be used to identify opportunities for energy savings and performance improvement.
The importance of heat recovery
As there is a requirement for labs to have a lot of air circulating in the building, it is important to recover as much of its heat as possible. However, effectively capturing and using waste heat can be difficult in practice. In some cases, the temperature difference may be insufficient to extract heat efficiently, limiting the feasibility and effectiveness of heat recovery.
Integrating heat recovery systems can be difficult, as it will introduce pressure drops. It can also create foul air that can be corrosive, which means the ductwork must be made with corrosion-resistant materials that will not be damaged by this.
Science buildings are one of the sectors being considered by the Net Zero Carbon Buildings Standard (NZCBS). Simon Wyatt, sustainability partner at Cundall, is leading the NZCBS1 sector group and is collaborating with market leaders to create assessment frameworks for buildings in the sector. It is still early days for the sector, and there is a lot more data that is needed before benchmarking of life sciences buildings is taken seriously.
Simon Wyatt on benchmarking life science buildings
Life science buildings are typically more difficult to benchmark than commercial offices, schools or dwellings where the occupancy patterns and usage are more defined. They are substantially influenced by their occupiers and usage, two identical buildings could have energy consumption double, triple or even higher depending on their HVAC operating hours, fume cupboard management programmes, plug in loads for research equipment, or chemical usage.
This makes it extremely difficult to compare and predict performance, especially for speculative developments where the end users are unknown. It is, therefore, more important to understand the potential of the building by ensuring that systems are designed to turn down and operate efficiently, especially the ventilation and fume cupboard ventilation systems which shouldn’t default to ‘on’.
A simple way to benchmark designs will be to model them under agreed standard operating conditions and compare their potential performance before the occupiers influence their outcomes. Once the building is designed to be as efficient as possible, providing occupiers with operational guidance will be vital to their success.
About the author:
Rob Van Zyl is a management board partner at Cundall
References:
- UK Net Zero Carbon Buildings Standard www.nzcbuildings.co.uk