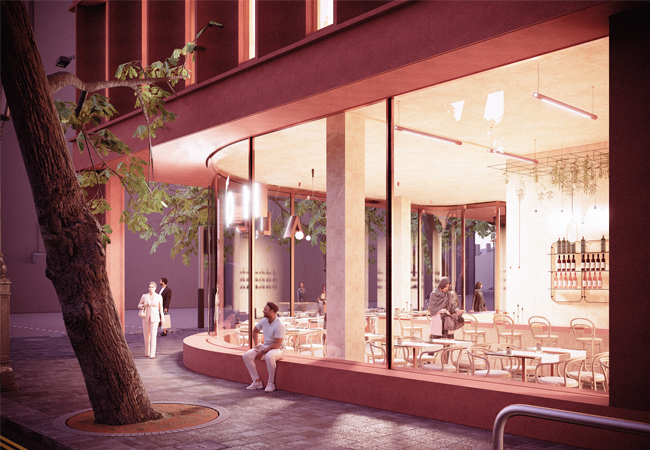
Whole life carbon was considered carefully at 100 Gray’s Inn Road
Embodied energy is becoming increasingly important for anyone planning a project. Consultants are now having to calculate whole life carbon of buildings to meet planning requirements and the expectations of clients.
In June, planning permission was granted by Camden Council for an office redevelopment on the corner of Gray’s Inn Road and Clerkenwell Road, London, for what is believed to be the UK’s largest full-timber, net zero carbon office building.
Building services engineer Max Fordham has used whole life carbon modelling to calculate the embodied and operational carbon of the project. It aims to exceed RIBA 2030 Climate Challenge and Greater London Authority (GLA) planning energy performance targets.
The designs for the eight-storey project, by architect Piercy & Company, will result in the construction of an 8,826m2 (95,000ft2) office building on the site of the former Holborn Town Hall, in central London, for Global Holdings. The eight floors will include contemporary workspaces and a communal rooftop garden and restaurant.
A second 1,115m2 (12,000ft2) building – currently known as 88 Gray’s Inn Road ¬ will also be developed on the site, and is expected to include six affordable buildings and a ground-level affordable workspace.
The team aims to outperform the UK Green Building Council’s (UKGBC’s) Net Zero Office target, with the design seeking to lower operational carbon emissions by up to 82% compared with a typical office building. It is also targeting a Nabers UK 5.5* energy rating for the main building.
One of the headline-grabbing aspects of the development is the main building’s full-timber structure. This will result in a much lower embodied carbon compared with a typical office building using concrete or similar materials, explains Max Fordham’s Edmund Chan, principal engineer and lead project engineer for the 100 Gray’s Inn Road project.
‘Everything in terms of superstructure will be timber, made from highly sustainable glue-laminated (glulam) timber beams and cross-laminated timber slabs as part of the overall design,’ Chan adds.
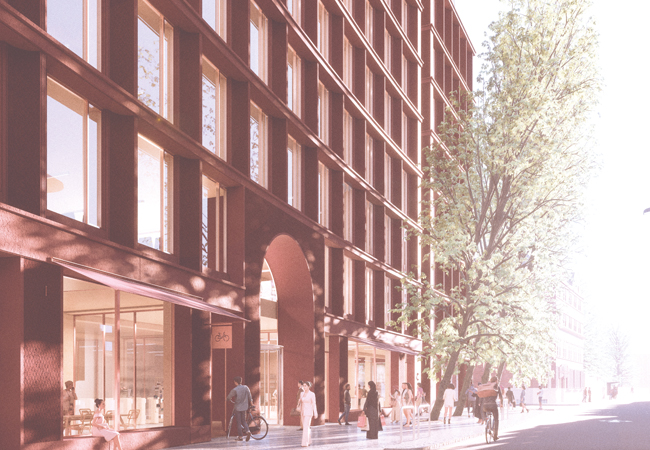
Embodied carbon in future refits has influenced design
According to Andy Heyne, director at project structural engineers Heyne Tillett Steel, the timber structure, combined with its high-performance façade, should outperform the UKGBC’s Building the case for net zero office baseline target by more than 50%. ‘With more than 2,400 tonnes CO2e stored within the timber, the structure is effectively carbon negative during its lifetime,’ he says.
The reinforced-concrete basement walls of the existing buildings will be repurposed for the development. ‘While the basement will be dug deeper [for the new building], we are reusing the foundation on the perimeter. We will be using as much as possible down at that substructure level,’ says Chan.
The Max Fordham team has gone through a process of identifying, assessing and pre-auditing the existing buildings in terms of soft-strip and deconstruction of building elements. ‘There is a lot of material that can be reused from soft-strip, such as raised access floors, lighting and MEP strip-out material,’ says Chan.
Delivering performance
Ensuring the materials selected for the building are as suitable as possible for future deconstruction and reuse is also key. ‘Our retained role is to be part of that strategic approach moving forward, using expertise in these areas and working with the contractor and their supply and delivery chains to make that happen,’ says Chan.
In terms of operational carbon, the building will use 100% renewable grid electricity, rooftop photovoltaic panels, an all-electric heating, hot water and cooling system, and demand-driven displacement ventilation for the office floors.
‘This is one of our first large office projects that went through the updated GLA set of requirements for sustainability and energy efficiency, which includes whole life carbon and circular economy statements,’ says Max Fordham’s principal sustainability consultant and partner, Henry Pelly. Knowledge from the firm’s first Nabers UK 5.5-star project at 11 Belgrave Road (see ‘Ratings winner’, CIBSE Journal, February 2023) was fed into 100 Gray’s Inn Road.
A key challenge in such a project is to ensure that lifetime embodied carbon calculations are realised. Avoiding compromises that might change aspects of the design – which could impact energy performance and, therefore, embodied carbon – is crucial, says Pelly.
‘One of the things about embodied carbon is that everything comes as a package and it all fits together,’ he adds. ‘It’s not like you can just pull out one element because everything’s been designed to work together. The timber structure, for example, is prefabricated off site and assembled on site, reducing carbon inputs.’
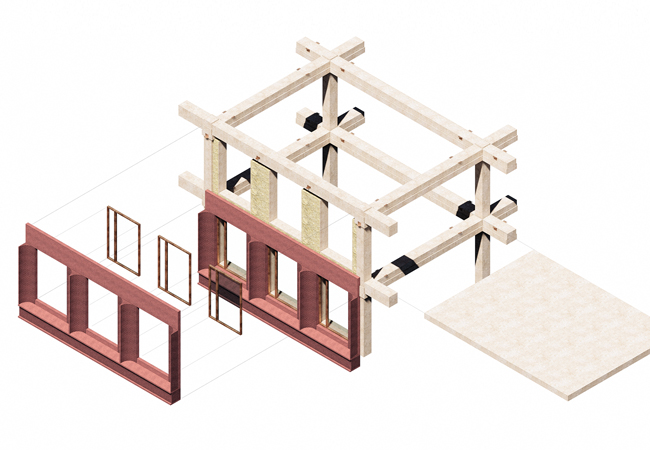
There are 2,400 tonnes CO2e stored within the scheme’s structural timber
Max Fordham’s approach to embodied carbon and energy performance modelling is to be conservative about potential savings rather than assuming best-case estimates. ‘It is quite helpful to adopt a kind of “worst case” embodied carbon modelling approach so that, at every stage of the process, there are opportunities for improvements,’ Pelly explains. ‘Instead of taking potential opportunities for savings early on in the process – for instance, the raised access floors we are reusing – we don’t assume them for the modelling until they are written into the documents and we know they are definitely going to happen.’
This is important to avoid overestimating savings, Pelly adds, and focus on where improvements can be made to the building.
Similarly, while estimating the carbon impact of future deconstruction at end of life is a challenge, the team’s model includes only what is technically possible now, rather than assuming the potential impact of future technologies.
The design decisions reflect potential reconfigurations in the future and the consequent embodied whole life carbon impact. For example, the team looked to minimise ductwork by having more air handling units (AHUs) at each floor level, rather than having multiple vertical ducts running from one centralised AHU.
‘Future-proofing
Part of the strategy was to look at on-floor services rather than having a big AHU on the roof, ducting down via lots of horizontal and vertical distribution. Instead, horizontal AHUs were used in voids under each office floor.
‘We are not installing lots of ductwork,’ says Chan. ‘We are employing underfloor cooling using five conditioned air module units sitting in the cores, which blow conditioned air into the floor plenum.’
Reusable floor plenum materials mean future tenants can adapt space without having to pull out ductwork.
‘We’re enabling the reduction of waste and embodied carbon from Cat A to Cat B fit-out’ says Chan.
‘The design strategy also allows us to keep the timber structure exposed, and it maximises floor-to-ceiling heights, creating that impression of space.’
Enabling works on the project are expected to start imminently, with work starting on site in early 2024. Completion is anticipated for the first quarter of 2026.
Responsibility for keeping to embodied carbon budgets will be held by each of the parties under contractual arrangements for individual packages of work, says Chan. ‘For example, in the concrete work package, they may be able to choose to use lower carbon solutions in different parts of the construction sequence, but they can’t pass down any carbon budget “overspend” to the next contractor to make up somewhere down the line.’
Ultimately, achieving net zero carbon requires a ‘whole building’ approach to design, adds Chan. ‘We’ve driven down the building’s operational energy demands by prioritising passive principles and optimising the façade, engineering efficient active systems, and supplementing through low and zero carbon energy sources.’
Max Fordham is committed to having the in-use performance realised and verified by others. ‘We want to show that low energy design is not a concept, but a reality in our lifetime,’ he says.