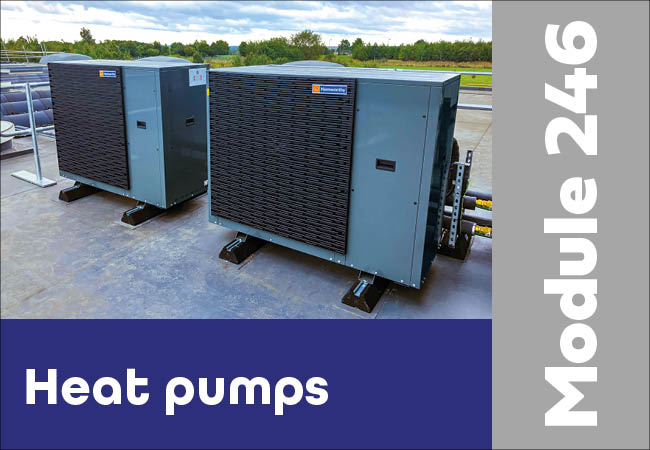
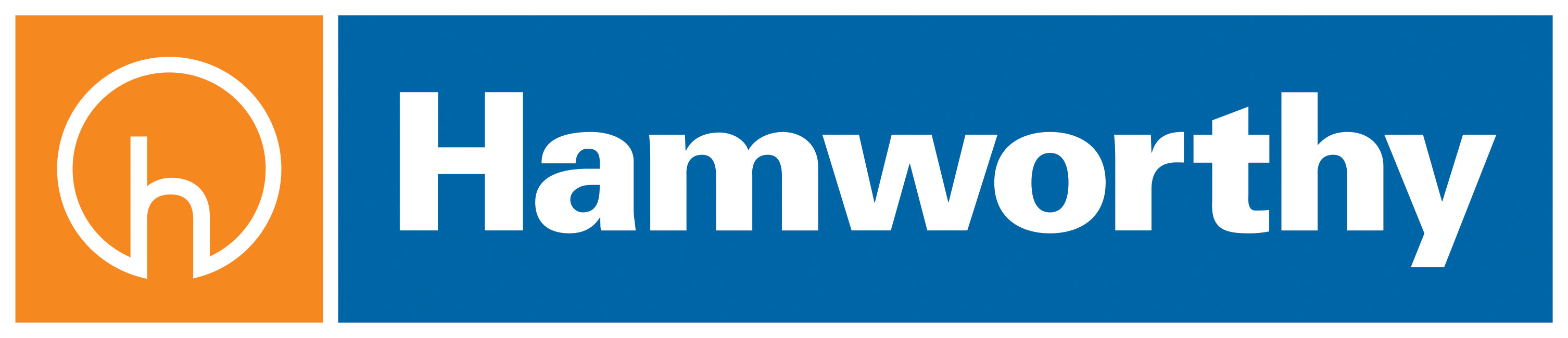
This CPD will explore how readily available, tried and trusted heat pump applications can efficiently deliver hot water at temperatures that can satisfy the demands of ‘traditional’ heating and hot water systems. Applications of many refrigerants are evolving, both natural and synthetic – this article will focus on R32 and R290 (propane) as examples of low-pressure refrigerants that are being widely used in commercially available ’subcritical’ vapour compression heat pumps.
Many believe residential and small commercial heat pumps struggle to deliver temperatures efficiently above 50-55°C. However, as shown in Table 1, there are well-established refrigerants that can meet the needs of medium- and high-temperature heat pumps. These are now widely used in applications requiring higher heating capacities or temperatures, such as space heating and domestic hot water (DHW), which were previously challenging with single-refrigerant systems.
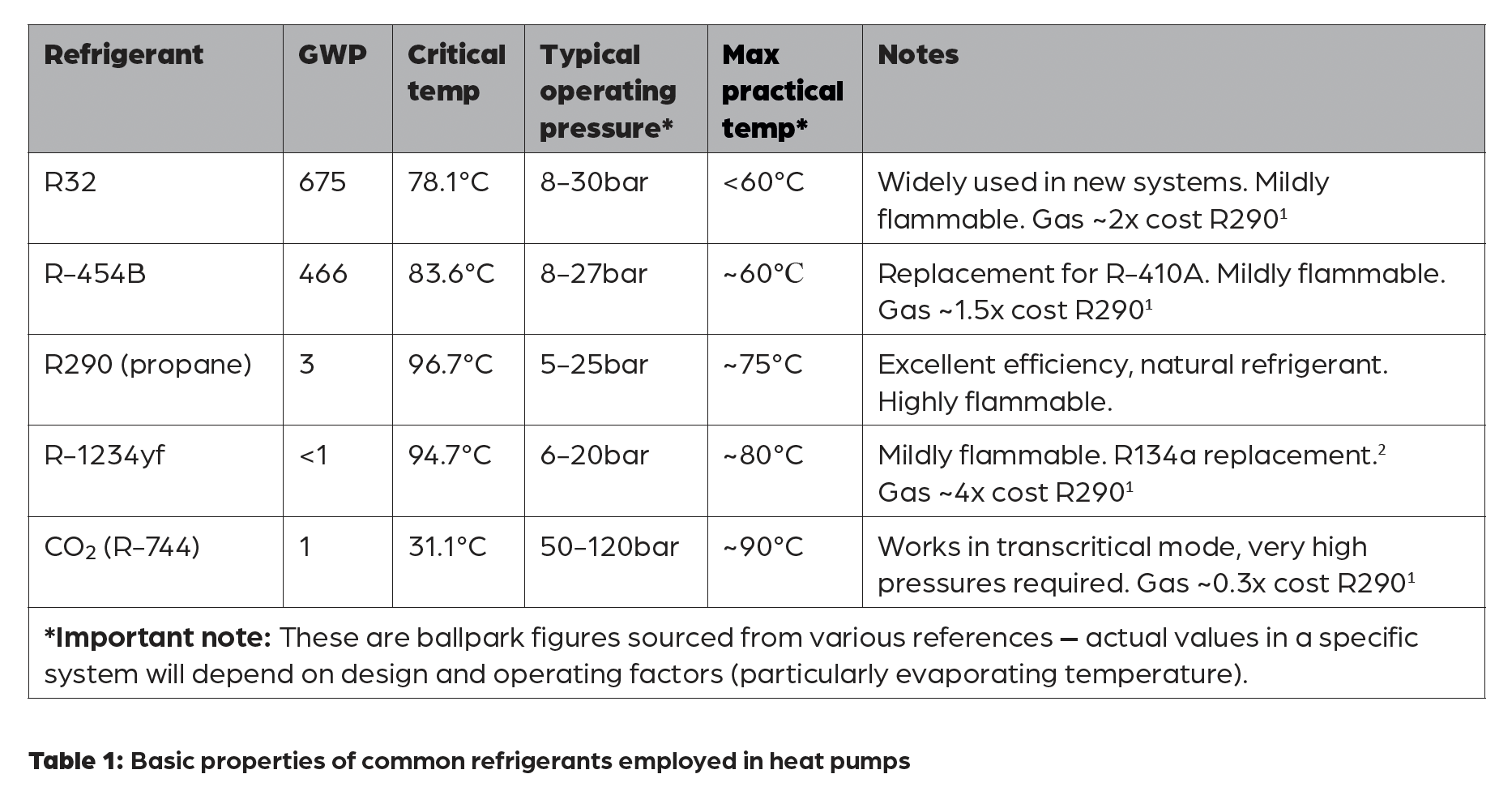
The simplified pressure enthalpy diagram in Figure 1 indicates a basic vapour compression refrigeration cycle, with superheat at the inlet to the compressor and subcooling at the intake to the expansion device. In this basic system, the condensing process, a latent process 3⇒4, will provide much of the heat (to meet the heating load) at the condensing temperature.
There will also be heat available from the higher-temperature sensible cooling process 2⇒3 and the sub-condensing temperature sensible subcooling process 4⇒5. The evaporating process 6⇒7 provides the bulk of the ‘free’ heating, and the process 1⇒2 represents the ‘paid’ power input during compression.
The critical temperature, as shown in Figure 1, is the highest temperature at which a refrigerant can exist as a liquid, regardless of pressure. If the heat pump’s desired condensing temperature is close to the refrigerant’s critical temperature, the latent process, 3⇒4, is necessarily limited. This reduces the available latent heat transfer, making the heat pump less effective and lowering the coefficient of performance (COP).
Also, as a refrigerant operates nearer its critical temperature, it requires an increasingly high compression ratio (CR) to reach the required pressure, resulting in high compressor discharge temperatures that can damage the compressor (over time) or require extra cooling (as discussed later in the article), which can lower the overall system efficiency. (CR = absolute discharge pressure/absolute suction pressure.)
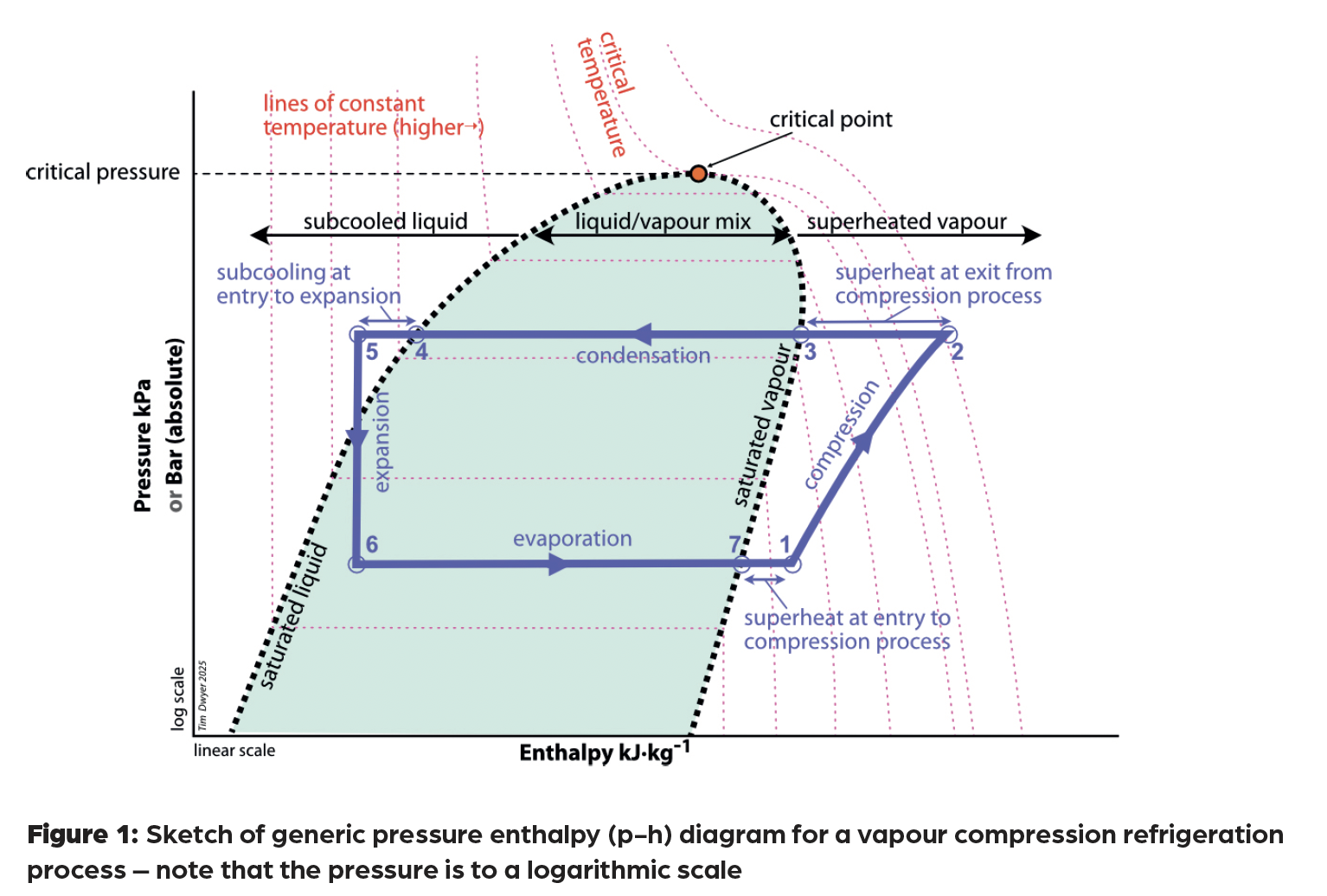
The hydrofluorocarbon (HFC) refrigerant R32, a single-component refrigerant, has a relatively low critical temperature of 78.1°C, which might appear to be a limitation for higher-temperature heat pump applications. However, it remains a strong candidate because of several key factors, and is suitable for heat pumps targeting output temperatures in the range of 55°C to 60°C.
R32 possesses a high latent heat of vaporisation, allowing it to transfer more heat per unit of refrigerant mass flow, which contributes to a higher COP. Additionally, it has a superior heat transfer coefficient compared with many alternatives, ensuring better heat exchange performance even at elevated temperatures, thereby enhancing system efficiency.
A further advantage of R32 is its high volumetric cooling capacity (VCC), which determines the amount of cooling effect a refrigerant provides per unit volume of vapour at the compressor inlet. A higher VCC allows for more compact system designs, smaller compressors, and lower refrigerant mass flow, leading to reduced energy consumption. R32 exhibits high discharge temperatures, which require careful compressor management.
This may require supplementary cooling mechanisms or system enhancements to prevent overheating, which will be considered below. However, its thermodynamic properties make it well suited for achieving the necessary condensing temperatures for DHW and space heating applications.
Applications of R32 heat pumps will often be paired with a matched DHW storage calorifier that includes an auxiliary electrical resistance heater to allow stored water to be consistently stored above 60°C. Together with proper subcooling and system design, as discussed later in the article, R32 can function very efficiently.
A key benefit of R32, compared with older synthetic refrigerants, is its relatively low global warming potential (GWP) of 675. With many manufacturers transitioning to R32 because of its efficiency and lower environmental impact, the industry is seeing improved component availability, optimised system performance, and ongoing research and development. However, there are some challenges associated with R32, including its mild flammability – classified as A2L – which necessitates appropriate system design and safety measures.
R290 (propane) is a hydrocarbon refrigerant well suited for higher-temperature heat pumps, such as the one in Figure 2. With a higher critical temperature of 96.7°C, R290 operates more efficiently at high condensing temperatures, making it particularly well suited for applications requiring output temperatures above 75°C.
At higher temperatures, as the condenser temperature gets closer to the critical temperature, subcooling becomes less effective, leading to flash gas formation and lower efficiency, so appropriate subcooling methods are normally used. However, because of its higher critical temperature, R290 can more readily maintain subcooling, while R32 will struggle as it nears the critical point.
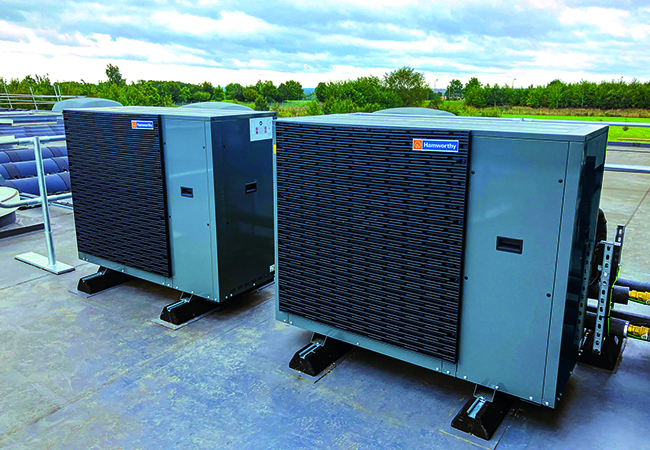
Figure 2: Two 27kW air source R290 heat pumps capable of producing temperatures up to 75°C and operating at outdoor temperatures of between -20°C and +40°C, recently installed on the roof of a UK school building (Source: Hamworthy)
R290 has moderate volumetric cooling capacity and, while lower than that of R32, ensures efficient operation with lower pressure ratios, contributing to improved compressor longevity. Also, R290 demonstrates excellent heat transfer properties because of its high thermal conductivity and superior heat transfer coefficient, enhancing evaporator and condenser efficiency.
Manufacturers often recommend a water side flow-return temperature difference of around 5K to 10K for R32 heat pumps, whereas R290 heat pumps range from 10K to 30K (and higher). The higher value for R290 is especially useful in district heating where higher temperatures and efficient heat transfer are crucial. A high temperature difference provides opportunities for reducing water flowrates and pumping requirements for the load side. However, 10K may be suitable for many legacy heating applications.
One of the most compelling attributes of R290 is its extremely low GWP of approximately 3. However, despite its advantages, R290 does present challenges. It is classified as A3, meaning it is highly flammable, so stringent safety regulations and leak-prevention measures must be in place. Therefore, R290 is typically used in outdoor-located monobloc heat pumps, whereas R32 can be used in both monobloc and split systems.
Despite its moderate critical temperature, R32 remains a good choice for higher-temperature heat pumps because of its high efficiency, superior heat transfer properties, and widespread industry adoption. However, for applications requiring higher temperatures or the ability to directly produce DHW temperatures above 60°C, refrigerants such as R290 or CO₂ (in a transcritical system – see module 47) may be more suitable, because of their higher critical temperatures and overall performance advantages. R290 systems have a higher COP than R32 at lower outdoor temperatures, while R32 heat pumps typically perform better at higher outdoor temperatures.
Optimising vapour compression refrigeration systems in heat pumps involves several key technical attributes that enhance efficiency, performance and longevity. Variable-speed compressors significantly improve efficiency by adjusting speed to match heating or cooling demand.
This minimises frequent on/off cycling, which can be detrimental to both efficiency and component lifespan, while also delivering more stable temperatures that reduce energy consumption and improve occupant comfort. Operating at lower speeds, these compressors can also reduce noise levels compared with fixed-speed alternatives.
Multistage compression enhances the efficiency of higher-temperature heat pumps by dividing the compression process into two or more stages, rather than a single step. This reduces the pressure rise across each stage, lowering overall compression work and energy consumption.
The improved volumetric efficiency allows the compressor to handle a larger refrigerant volume per cycle, while intercooling between stages cools the refrigerant – reducing its temperature and volume.
In smaller residential and commercial heat pumps, this is often achieved with an air-cooled intercooler using ambient air. Multistage systems can maintain efficiency over a wider range of ambient temperatures, improving cold-weather performance. However, they are more complex than single-stage systems, requiring additional components such as intercoolers, extra piping and more advanced controls, resulting in higher initial costs and potential maintenance requirements.
Microchannel heat exchangers (MCHEs) offer advantages in both outdoor and indoor applications for air, ground and water source heat pumps. By using a network of very small channels – typically less than 1mm in diameter – they promote turbulent flow, enhancing heat transfer efficiency compared with traditional heat exchangers.
Their high surface-area-to-volume ratio enables them to be smaller and lighter while maintaining the same heat transfer capacity. Despite their compact size, well-designed MCHEs can exhibit lower pressure drops, because of optimised flow distribution. They also help the heat pump achieve higher output temperatures and reduce refrigerant charge, lowering environmental impact.
However, their small channel dimensions make cleaning and maintenance challenging, as fouling can significantly reduce heat transfer performance.
Suction line heat exchangers (SLHXs) play a crucial role in improving efficiency, particularly in higher-temperature heat pumps using refrigerants such as R290 and R32. Their primary function is to subcool the liquid refrigerant leaving the condenser, reducing the risk of two-phase flow entering the expansion device and improving its performance.
By minimising the formation of flash gas, SLHXs allow the evaporator to operate more efficiently, enhancing heat transfer and increasing cooling capacity, while reducing compressor energy demand. Additionally, by simultaneously superheating the suction gas, SLHXs help prevent liquid refrigerant from reaching the compressor, protecting it from slugging.
However, this process increases compressor discharge temperatures, which may require additional cooling strategies. Similar techniques can also be used to provide intercooling in multistage compression systems.
High compressor discharge temperatures can degrade lubricating oils, increase thermal stress on components, and reduce overall efficiency. Liquid injection cooling addresses this issue, particularly in applications with large temperature lifts between the evaporating and condensing temperatures.
In direct liquid injection, a small amount of liquid refrigerant is drawn from the liquid line before the expansion device, and injected into the compressor suction or at an intermediate compression stage via a thermostatic or electronic expansion valve. This cools the refrigerant, lowering discharge temperatures and reducing compressor strain.
A more advanced variation, the economiser cycle, is often used in screw and two-stage scroll compressors with an intermediate injection port. This method involves partially evaporating a portion of the liquid refrigerant before it enters the expansion device, using a subcooling heat exchanger. The separated subcooled liquid is then injected into an intermediate compression stage, further enhancing efficiency. Because the injected refrigerant evaporates instantly upon contact, it prevents liquid slugging while improving overall performance.
By incorporating these advanced system attributes, higher-temperature heat pumps can achieve greater efficiency, improved reliability and enhanced performance across a range of operating conditions.
A key element of heat pump operation in heating applications is to provide efficient defrosting. When the outside air temperature is below 5-7°C (for example, for ~160 days per year in London)3 and relative humidity is higher than 70%, in an air source heat pump (ASHP) the water vapour within the air freezes when flowing through the evaporator, forming ice that accumulates on the coil surface, compromising the heat pump’s ability to operate.
This can significantly reduce heat transfer efficiency and even lead to system shutdowns. There are several methods employed to counter this, with the most traditional being the reverse cycle defrost. This reverses the refrigerant flow so that the outdoor unit acts as an evaporator, transferring heat from the ambient air to the refrigerant.
This heat melts the frost off the coils. This is relatively simple and energy-efficient (compared with other methods), but can be time-consuming (interfering with the normal heating operation), and may not be effective in very cold climates.
Hot gas reheat defrost provides an alternative method, where hot, high-pressure gas from the compressor is directed to a separate heat exchanger within the outdoor unit. This hot gas is used to heat the refrigerant within the frozen coils, melting the frost. This provides a faster defrost cycle compared with reverse cycle defrost, minimising performance interruptions, but requires additional components and may increase energy consumption during the defrost cycle.
A simple method is to integrate electric heaters into the outdoor unit to directly heat the frozen coils and melt the frost. Although simple, relatively inexpensive and potentially fast-acting, this can be energy-intensive, as electric heaters consume significant power during the defrost cycle.
Pulse defrost employs short, intermittent periods of reverse cycle or hot gas defrost to remove small amounts of frost buildup periodically, preventing the formation of thick ice layers. This helps to minimise the impact of defrosting on overall system performance by preventing major performance drops because of significant frost buildup, but requires more sophisticated controls to manage the defrost cycles effectively.
Increasingly, there are advanced control strategies in heat pump operation that include predictive and adaptive defrosting methods. Predictive defrosting uses weather forecasts and historical data to predict frost formation and initiate defrost cycles proactively, minimising the impact on performance. Adaptive cycles dynamically adjust the defrost duration and frequency based on real-time operating conditions, such as ambient temperature, humidity and wind speed.
There are many aspects of heat pump operation that will undoubtedly be touched by artificial intelligence (AI) tools. Machine learning, or AI, is already being deployed to predict the right time to initiate defrosting, avoiding unnecessary defrost cycles and reducing energy consumption of such solutions.
With the growing availability of higher-temperature heat pumps, there are expanding opportunities in both legacy and other higher-temperature systems for successful applications.
© Tim Dwyer 2025.
References:
- bit.ly/CJApr25CPD1 – accessed 1 March 2025.
- Munk, J et al, Field performance of R1234yf heat pump water heaters, US DOE 2023.
- CIBSE AM16 Heat pumps in residential buildings, CIBSE 2021.