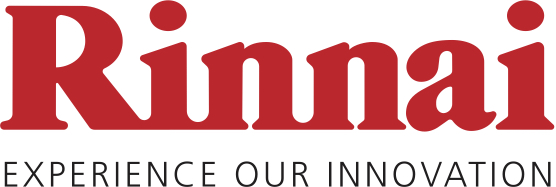
Setting the standards for the efficient supply of hot water
The Energy Related Products Directive (ErP) has provided a common reference – based on extensive cross-Europe research – by which to set standards for water heaters and, when used in conjunction with local regulations, is promoting increasingly effective systems.
The ErP is made up of two parts – Ecodesign and Energy Labelling. Ecodesign covers water heaters with a rated output equal to or below 400kW, while Energy Labelling is required for water heaters up to 70kW. The actual requirements for water heating energy efficiency are set according to the heater’s output power and use profile, with the efficiency requirements rising with the size of the heater.
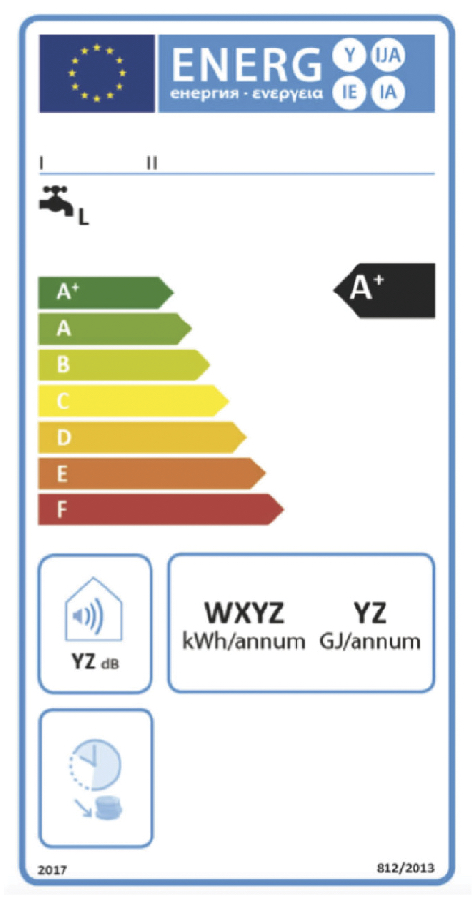
Figure 1: The label that will supersede (in September 2017) the current label that is used for hot water heaters. The new label shifts the scale from the current G→A to F→A+
The Ecodesign requirements (as defined by EU regulation No 814/20131) set minimum efficiencies and operational parameters that go beyond simple thermal efficiencies. They include allowances for ‘smart’ control – that effectively modulate the energy consumed and the water output to meet the demand – and for the use of energy employed for the overall control of the appliance.
The required performance is related to a ‘load profile’ of hot-water use, ranging from the smallest 3XS (a heater for the supply of hot water at 35°C to meet the typical needs of a single outlet), through L (serving a bath, sink and shower at 55°C), to the largest 4XL (indicatively representative of the supply at 55°C to meet the typical use of 16 showers and outlets serving a residential home). As well as energy efficiency, other relevant factors – such as the storage volume for storage water heaters and the heat loss from hot water storage tanks – are included. From September 2018, Ecodesign will also set a maximum nitrogen oxide (NOx) emission level of 56mg·kWh-1 for gas water heaters.
The actual minimum overall thermal performances as currently required by Ecodesign are quite modest, particularly for small water heaters – for example, 3XS 22%, L 30% and 4XL 32%. These are set to go up in September 2017, most notably for the larger capacities – so 4XL will rise to 64% – but this should still be well within the capabilities of modern water heater systems.
To differentiate between the performance of various manufacturers’ systems, the energy labelling scheme for water heaters – as required by EU regulation 812/20132 – came into force in 2015. The minimum level on the label is set by the relevant Ecodesign requirement. The scale goes from G to A, but as of 26 September 2017 will be modified to show a scale of F to A+ (see Figure 1), to link in with the more demanding Ecodesign requirement. The calculation to determine the ranking of a particular water heater includes factors that attempt to assess the overall environmental impact of operation.
The responsibility for ensuring that a product has an appropriate label rests with the manufacturer, who must provide a standard table of information required by the Eco directives, known as a ‘fiche’.
High-efficiency, condensing, gas-fired water heaters are currently in band A, whereas older, non-condensing water heaters – and heaters using other fuels – are likely to be in bands B to G. For example, many direct electric hot-water heaters are likely to be rated as C because electricity, typically, has a high carbon factor compared to natural gas, so has an increased operational environmental impact.
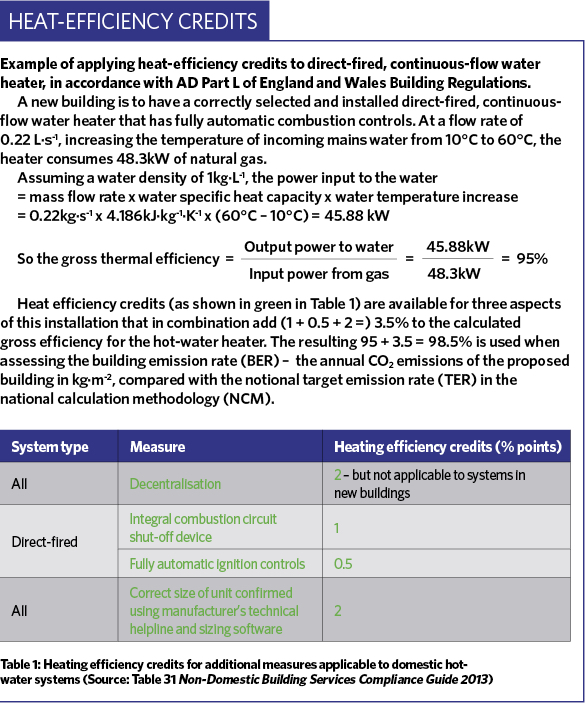
The application of continuous-flow hot-water heaters
Centralised plantrooms for heating and hot water systems have been the traditional solution for the majority of commercial buildings for many years. These, typically, would employ storage of hot water – with the inherent standing losses and space requirements – to meet variations and peaks in demand. They would be sized at the design stage so that there is always a certainty of supply of
hot water available when demanded by the user. This approach often leads to excessive safety margins, which add to the expense of purchase, installation and running costs.
An alternative to the traditional storage-based systems is the application of continuous-flow, hot-water heaters that only consume energy when there is a demand for hot water. Modern continuous-flow, condensing, gas-fired hot water heaters can be connected using a manifold arrangement (as illustrated in Figure 2) to provide a hot-water system capable of coping with virtually any size of site or application. The modularity also allows for additional plant to be added at a later stage if the building hot-water load is increased, and offers some redundancy in the case of module failure and maintenance.
The close control integrated into such systems is able to deliver a continuous flow of hot water at a constant temperature, without the need for storage. With almost all continuous systems, the user can set the required temperature of hot water to suit the needs and demands of the site.
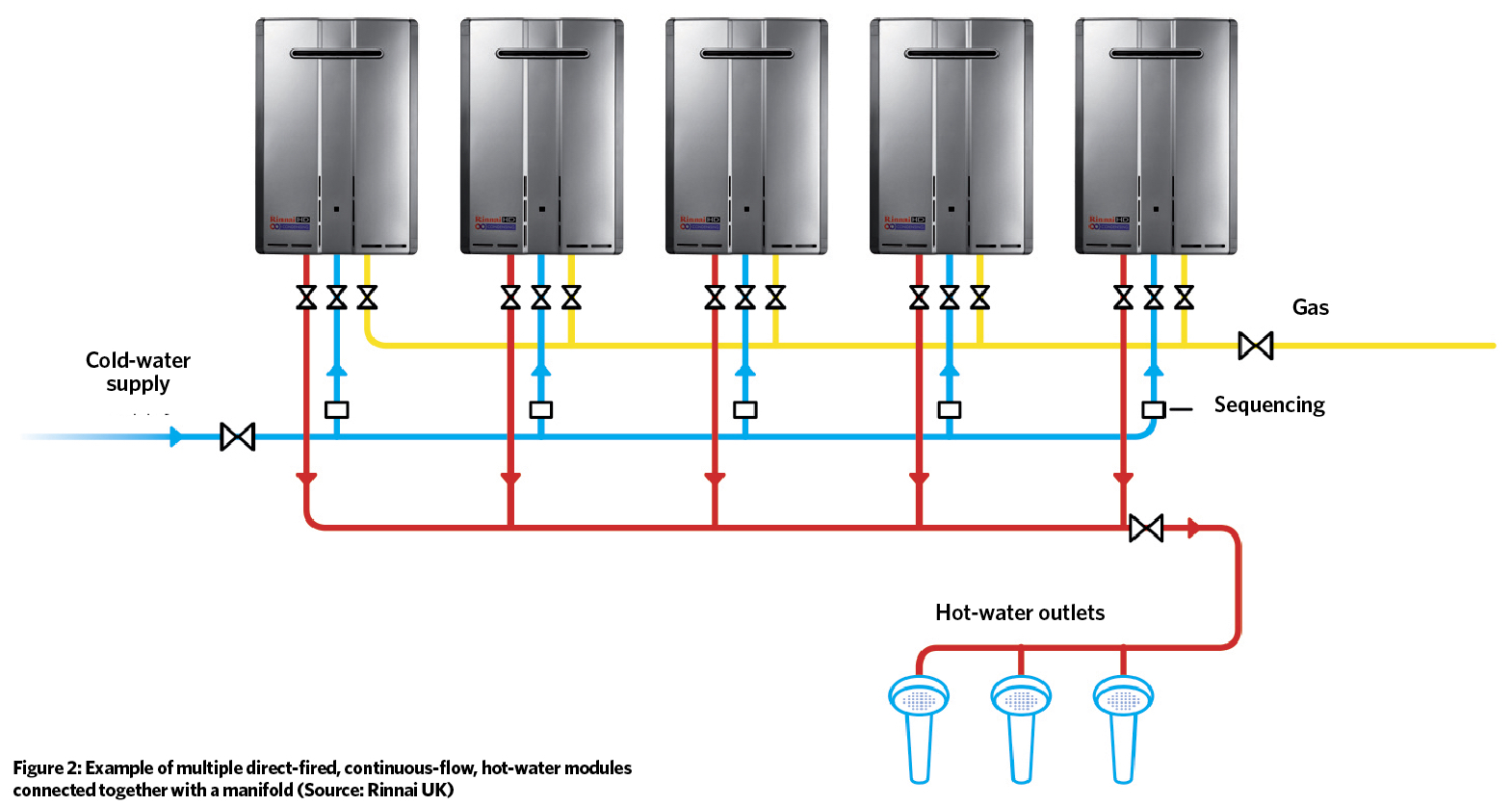
As the systems have the same requirements as a wall-hung boiler, they are also readily applied to decentralised hot-water systems that are in close proximity to the draw-off points, so reducing distribution losses, enabling close temperature control and simplifying the maintenance of the hot-water piping network. The temperature of the water distribution is accurate to ±1K and, as there is no storage of water, there is no need to heat up a volume of storage water to reduce Legionella risk. Smart’ controls can be added to commercial condensing, continuous-flow systems to optimise their performance. Continuous-flow, condensing, gas-fired hot-water heaters can be employed as stand-alone technology or used in conjunction with the other technologies – such as solar thermal or pre-heated water from variable refrigerant flow (VRF) or other heat recovery systems – to provide an efficient source of hot water.
Condensing, direct-fired hot-water systems (such as that shown in Figure 3) are always able to maintain condensing operation because – unlike many traditional systems – there is always an opportunity to condense the water from the flue gases to capture the otherwise lost latent heat. This is because of the availability of low-temperature incoming mains water that is well below the flue-gas condensing temperature (which is typically 57°C). The amount of condensation, and heat recovery, will increase as the flue gases are made cooler.
Recent independent modelling5 of continuous-flow hot-water systems indicate lower initial capital costs, as well as more favourable life-cycle costs over 20 years, when compared with indirect stored and stored hot-water systems. The detail of the net present value (NPV) analysis employed, together with a more detailed description of the modelling assumptions and inputs, were discussed in the October 2016 CIBSE Journal CPD article. As examined in more detail in that article, a shower block in a holiday camp – with six showers and four basin taps – was modelled to establish the comparative performance of a continuous hot-water system with that of a direct-fired storage option, and with a more traditional condensing gas boiler and storage cylinder.
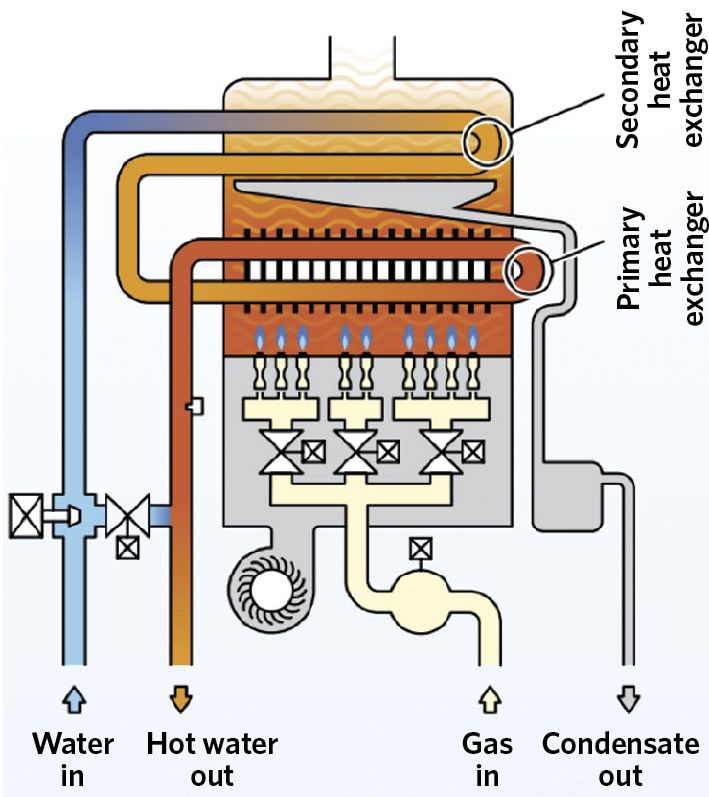
Figure 3: Example of a continuous-flow, condensing, gas-fired hot-water heater (Source: Rinnai UK)
The continuous-flow system was based on four heavy-duty water heaters, each with a nominal output of 48kW – equating to around 14 litres per minute of hot water at 50K temperature rise (from 10°C to 60°C) – and a gross thermal efficiency of 95%. The indirect-fired storage option was based on a pair of 40kW condensing, natural-gas boilers, with a gross efficiency of 89%, heating a pair of 400-litre cylinders. The direct-fired storage option consisted of a pair of 230-litre cylinders with integral burners, each with around 37kW output and gross thermal efficiency assumed as 96%. In this example, the model indicated that the continuous-flow system has a 20-year NPV of 6% to 7% lower than the two storage systems.
A further analysis was undertaken for the increasingly common application of a fast-food restaurant.
Echoing common trends, the boiler used for the indirect-fired storage system was assumed to serve only the hot-water cylinder, as fast-food restaurants typically use heat-pump systems for space conditioning. Using similar standard operational and efficiency assumptions as that of the previous example, the resulting NPVs again indicated that the continuous-flow system is around 6% to 7% lower on fuel consumption than the two storage systems, based on that 20-year analysis period.
The combination of increasingly strict regulations and the evolution of systems to ensure flexible and efficient operation – plus the motivation of the energy label – offers a positive outlook for the reduction in environmental impact of meeting the increasing demand for potable hot water.
© Tim Dwyer, 2017.