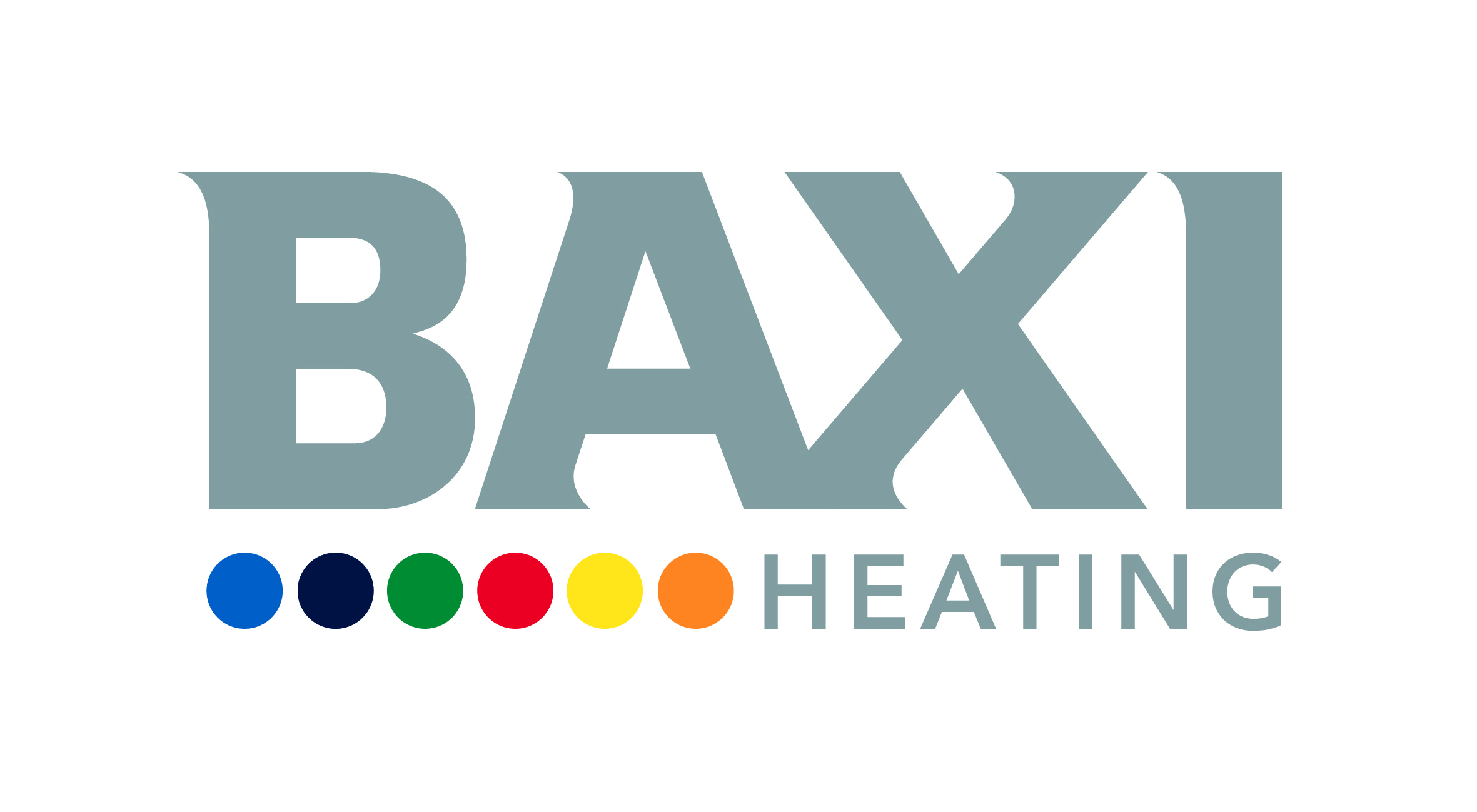
Bespoke and mass-produced systems and subassemblies can be created in factory-controlled, weather-protected environments, using dry materials where there is less risk of problems associated with moisture, environmental hazards and dirt. Such a properly managed and controlled factory construction environment will also present considerably fewer health and wellbeing risks, accidents and associated liabilities.
As discussed in the recent BSRIA2 report, it is becoming increasingly common to produce plant subsystems in parts or sections, and then combine them on site to provide the complete plantroom or service space. Once in place, the incoming services and distribution systems are connected to the various plant and equipment within the plantroom.
There are potential significant economic opportunities in producing systems off site. The UK Government’s recent call3 for evidence (closed July 2019) on how best to adopt and embed a ‘platform approach’ to design for manufacture and assembly (p-DfMA) indicated that the UK construction sector – encompassing contracting, product manufacturing and professional services – had a turnover of around £370bn.
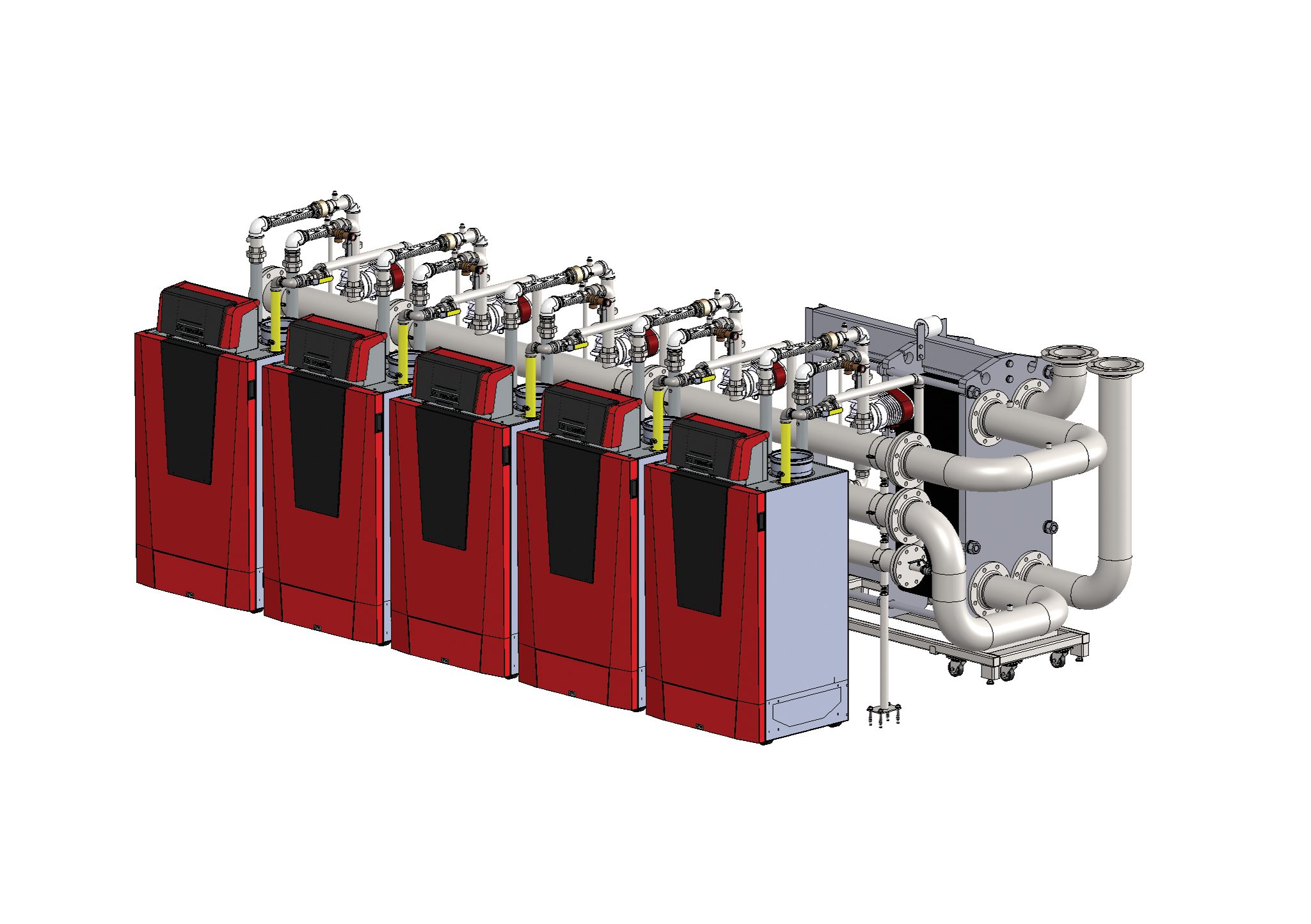
Figure 1: Modular boiler and plate heat exchanger installation, as visualised in modelling environment (Source: Remeha)
However, the potential of the construction sector is considered to have been held back by poor productivity growth, which has been significantly lower than the wider economy – for example, in manufacturing, which has seen a 50% increase in output per hour worked between 1994 and 2015. Among the many and varied measures of productivity, the potential benefit of offsite production was recently4 highlighted by a report suggesting the productivity of factory staff is 80% relative to 20% productivity of onsite workers.
The wider adoption of offsite manufacturing can benefit from the increasingly sophisticated manufacturing techniques that can deliver quality, customisation and cost benefits with reduced waste. By employing a controlled manufacturing environment and by following appropriate standards, the subassemblies of the structure can be built to a uniform quality to meet the needs of the end user while also conforming to the demands of the regulatory authorities.
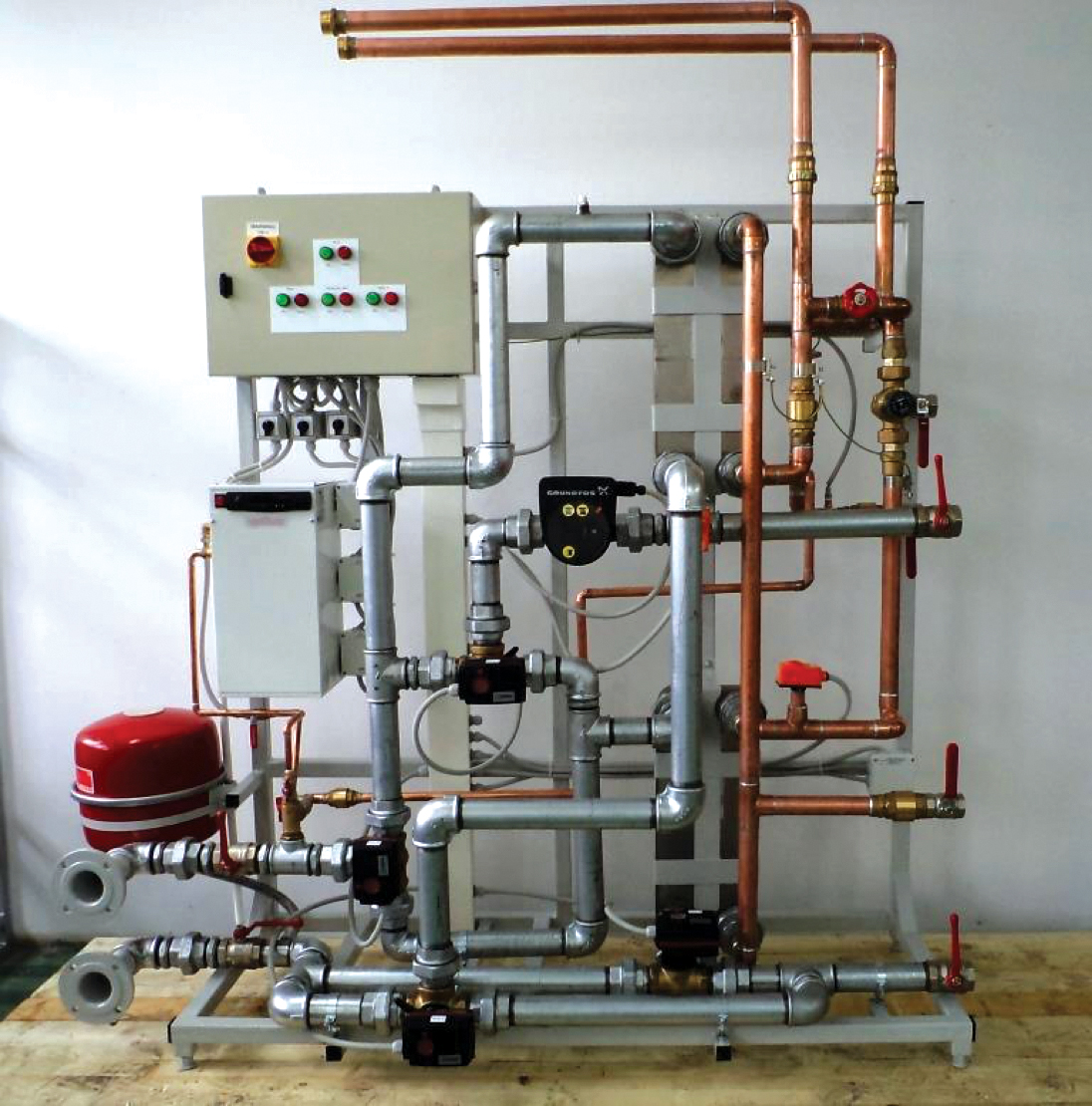
Figure 2: Bespoke domestic hot-water booster set and associated pipework, controls and fittings mounted on skid (Source: Packaged Plant Solutions)
In Bryden Woods’ 2017 document,4 which considered the creation of a marketplace for manufactured spaces, it was estimated that ‘poor productivity and manpower shortage account for up to 37% of delays on site. A DfMA approach reduces hours on site and increases productivity of those hours’, and the reduction in the number of site-based workers reduces the need for temporary site accommodation – saving space, time, and associated environmental and cost impacts.
That same report indicated that DfMA can reduce site waste by 70-90% and reduce vehicle movements local to the site that, aside from reducing congestion in the neighbouring streets, is considered as contributing to a reduction in local pollution by up to 20%.
By manufacturing off site, fewer decisions are required on site, reducing the potential for delay and improving the opportunity for meaningful monitoring and quality assurance, with standardised solutions encouraging more thorough testing, feedback and development. Improved performance-in-use of environmental controls (better assembly and factory-based commissioning) can result in a reduction of up to 30% in equivalent carbon dioxide emissions.4
Equipment systems can be assembled in fully accessible manufacturing bays, with purpose-made lifting, tooling and safety equipment, and benefiting from appropriate task lighting, ventilation and noise control. By limiting the number of hours on site, there is an 80% reduction in incidents.4
The components may be readily tracked through the stages of supply and production (using such methods as attached RFID tags and QR codes), which can follow through into use, maintenance and eventual replacement and disposal. Combined with technologies such as BIM and blockchain, these are, potentially, able to provide permanent and irrefutable records for operational, user feedback and auditing purposes.
This can also deliver in-use data, so that life-cycle costs and impact may be more properly measured and, ideally, enhance the opportunities for a meaningful circular economy.
In the UK Health and Safety Executive (HSE) overview document on offsite production,5 Taylor highlights the significance of the opportunities for creating employment in areas away from the building site. This can be particularly beneficial where there are skill shortages local to the site, and it can expand opportunities for the long-term development of skilled workers, as well as reducing the need for skilled workers to travel (with all the associated environmental and financial impacts).
Where projects call for the production of numerous subsystems, there may be a case for a fabrication facility local to the site, which may also encourage and promote the use of local labour resources, as local employment will always benefit where factory units are established.
DfMA does not limit the opportunities for innovative design or require compromise in the quality of the systems. As discussed in the RIBA document that considers DfMA in the standard Plan of Work,1 such an offsite fabrication approach may encourage ‘design rationalisation, materials optimisation, just-in-time delivery or logistics planning in order to achieve high rates of productivity on site’.
The goal is to deliver a project that meets the needs of the building user while minimising resources (carbon, cost or time) and optimising the delivery of positive aspects (health and safety, quality and certainty). As reflected in the RIBA document,1 ‘DfMA can be applied to one-off, small-scale projects, as well as to large-scale projects and frameworks.
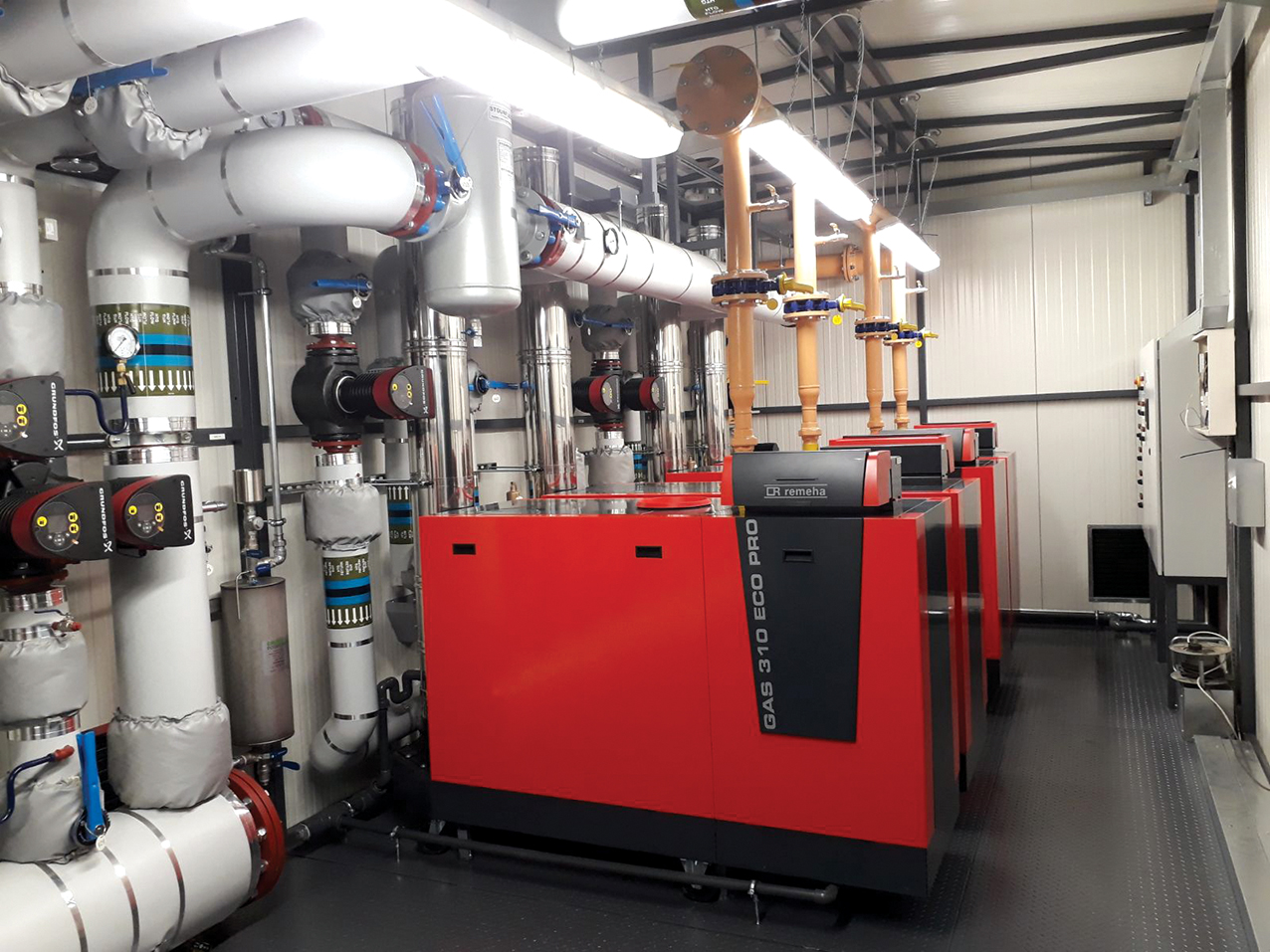
Figure 3: Internal view of boiler plantroom integrated into standard ISO container. (Source: Remeha)
The underlying goal is to use design processes that help facilitate a collaborative approach along the whole value chain, embracing design teams, clients, contractors and offsite manufacturers’. It indicates that a ‘concept design that has been developed with DfMA in mind during [RIBA Plan of Work] Stage 2 will be robust, leading to a more efficient design process at Stages 3 and 4’.
For larger clients and organisations – such as the UK government – a platform approach to DfMA can mean that a set of digitally designed components may be applied across multiple building types, so minimising the need to design bespoke components. So, for example, a single component could be used as part of a school, hospital, prison building or railway station.
The concept of ‘mass customisation’ is based around a manufacturing technique that combines the flexibility and personalisation of custom-made products with the low unit costs associated with mass production. Advances in digital production methods – such as robotics and 3D printing – will further enable economic mass customisation.
Each individual prefabricated subsystem can be designed using BIM tools and 3D computer-aided design (CAD) systems, allowing the various stakeholders to collaborate on the system design and to evaluate the functionality before works commence, reducing the risk of project delays.
For example, Figure 1 shows an example of where 3D modelling tools were applied to optimise the offsite prefabrication for a boiler replacement at Gun Wharf, the Medway Council offices in Chatham, Kent. The programme allowed for a short system downtime, as the offices had to remain operational.
The boiler manufacturer worked in conjunction with the contractor to design a customised component and pipework arrangement, integrated boilers, pipework and plate heat exchanger in subassemblies that were manufactured off site, reducing site time and labour and optimising the use of the available space.
The contractor was able to prepare the connecting pipework before delivery of the subsystems, which were then wheeled into place, connected and commissioned – bringing the heating system online in a short period of time and meeting the overall project’s completion deadline.
The presentation by Drigo and Deadman6 includes several examples where DfMA has been applied to produce modular plantrooms and services distribution systems. By applying a ‘skid-mounted’ approach – where components are mounted on a steel framework that can be craned and readily manoeuvred on site – a precisely designed and engineered subassembly can be delivered to site that matches the needs and vagaries of the building structure, while also having dimensions that ensure the prefabricated element can be easily handled via the available access routes.
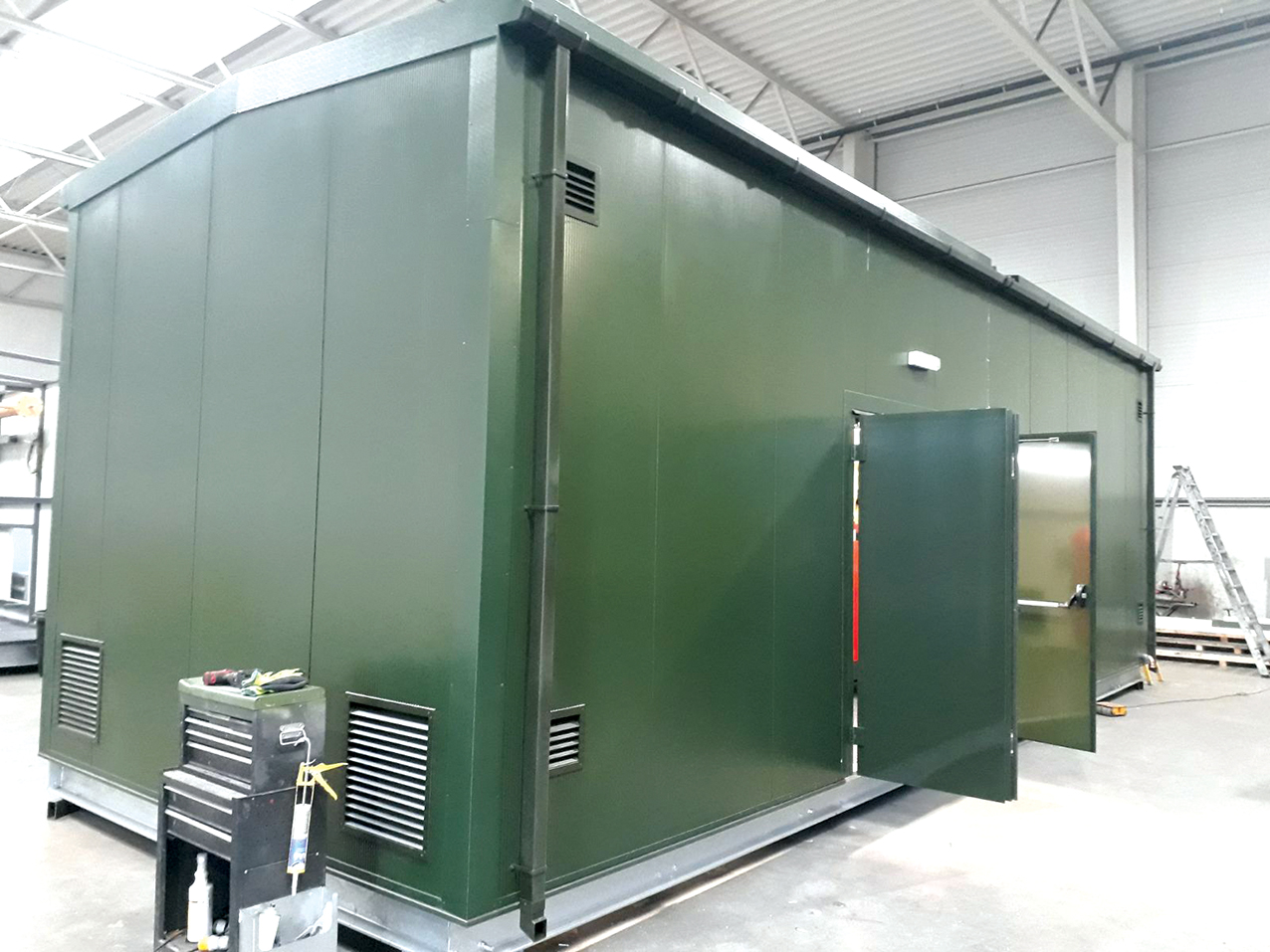
Figure 4: Boiler plantroom integrated into standard ISO container (Source: Remeha)
Each skid can incorporate the same services that would otherwise be fixed separately in a traditional in-situ fabrication process – such as boilers, fans, pumps (complete with inertia bases), valves, pipework, ductwork, controls and sensors.
The skid can be purpose-designed to ensure that it can be transported without damaging component parts, be accurately located on site, and also be able to compensate for practical uncertainties such as unevenness in floor slabs. Smaller modules can be joined together to provide larger systems that are pre-commissioned, so reducing the time required on site to bring the systems into operation.
Figure 2, for example, shows a skid-mounted domestic hot-water booster that was custom-designed for a specific building application that had a very short onsite programme. Using this prefabricated and fully tested offsite solution ensured onsite timescales were kept to a minimum.
On a larger scale, the 36,500m2, 41-storey residential tower that includes 335 apartments at Two Fifty One, Southwark, included – among the many thousands of preconstructed structural elements – 11 offsite-manufactured plantrooms and switchroom units, as well as 11 multiservice vertical riser modules and hundreds of preplumbed bathroom modules.
This construction project was reported7 to have reduced onsite ‘man days’ by 60% compared with a similar site employing normal in-situ construction techniques, and this contributed to a reduction of site programme time by about a third.
DfMA techniques may be usefully employed to provide bespoke and optimised modules, such as the plant shown in Figure 3 and 4 – a self-contained, packaged boiler house, prefabricated within its own ISO container, designed and constructed to meet the heating requirements for a multi-occupancy building.
The packaged boiler house was fully constructed, tested and recommissioned off site, the prefabricated structure was delivered and craned into position as a single piece, and the contractor made final connections before completion of the final commissioning and the system being put into service.
However, there are important lessons to be taken from the experiences described by Drigo and Deadman. The application of DfMA is not always cheaper, and the cost will depend on the particular programme and project constraints. Evaluating the opportunity for success of offsite prefabrication, a number of elements must be considered, such as:
- The installed comparative ‘quality’ (which may include multiple parameters) of onsite and offsite fabricated systems
- Repetition will increase the effectiveness of subsystem production
- Effective communication between the site team and factory is vital
- Without appropriately planned and executed logistics, DfMA will probably fail – regardless of the technical ‘quality’ of the prefabricated system.
In the response8 coordinated by Constructing Excellence at BRE to the UK Government’s recent call3 for evidence for a platform for DfMA, it was noted that the industry must ‘truly embrace manufacturing approaches. This will require manufacturers to invest in new lines, new technology and resources, and require government to support innovation’.
As summarised in the recent House of Lords science and technology committee report,9 the common thread of the different offsite manufacturing options is that they require everyone involved in the project to think in terms of design for manufacture and assembly from the start of the project, as part of the wider digitalisation and innovation agenda in the construction sector.
As explained by Gbadamosi,10 the concept of ‘smart’ construction offers a transition from the traditional methods of construction to manufacturing through the increased usage of standardised components and offsite fabrication. The application of BIM develops an inherently collaborative design and evaluation environment that can accelerate the adoption of DfMA.
Importantly, the recently published Hackitt review11 also highlights that ‘procuring buildings to deliver better whole-life performance, to increase skills within the industry and support the development and commercialisation of digital and offsite manufacturing technologies, will support the delivery of safer buildings’.
References:
1 RIBA Plan of Work 2013 – Designing for manufacture and assembly.
2 Sands, J, TG 17/2019 – Offsite construction for building services, BSRIA 2019.
3 Proposal for a new approach to building: call for evidence, UK Infrastructure and Projects Authority, 2018.
4 Delivery platforms for government assets – creating a marketplace for manufactured spaces, Bryden Wood, 2017.
5 Taylor, S, Offsite production in the UK construction industry – a brief overview, Construction Engineering Specialist Team: HSE, 2009.
6 Drigo, R and Deadman, J, DfMA building services: what have we done and where are we going?, presentation 2019.
7 Clucas A, Design for manufacture and assembly – a new model for construction, Laing O’Rourke, 2019.
8 Response to infrastructure & projects authority proposal for a new approach to building, Constructing Excellence, BRE, 2019.
9 Offsite manufacture for construction: building for change, House of Lords Paper 169, Science and Technology Committee, House of Lords 2018.
10 Gbadamosi, A-Q et al, The role of Internet of Things in delivering smart construction, CIB World Building Congress 2019.
11 Building a safer future – proposals for reform of the building safety regulatory system, UK Ministry of Housing, Communities and Local Government, 2019.
© Tim Dwyer, 2019.