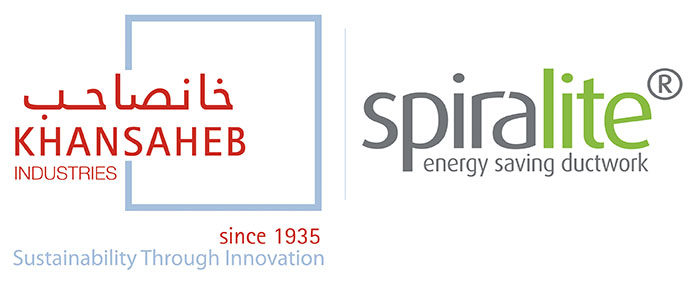
Alternative materials have increasingly been applied in appropriate applications, which in recent years have included ductwork made of faced phenolic foam insulation boards. This CPD will explore some of the significant factors that determine the appropriateness of employing phenolic foam ductwork systems in commercial buildings.
Much of the change to traditional ductwork practices is being driven by the requirement to reduce the environmental impact of building services systems. CIBSE Guide Part L 2020 Sustainability discusses the two types of CO2 equivalent emissions associated with buildings: the embodied emissions of the products that make up the building, and the operational emissions that are mostly associated with the energy consumption of the day-to-day use of the building.
The stages that are combined to provide a standardised measure of embodied carbon, as defined in BS EN 15978,1 are illustrated in Figure 1. CIBSE TM 652 notes that a large proportion of building services products’ carbon emissions is associated with extraction, transport and processing of materials, and the energy consumption used in the manufacture of the products (stages A1-A3), so the majority of the embodied carbon in mechanical services will be directly related to the ‘product’ stage. Environmental product declarations (EPDs) are a standardised way of expressing embodied carbon and other environmental impacts throughout the life-cycle stages of a product.
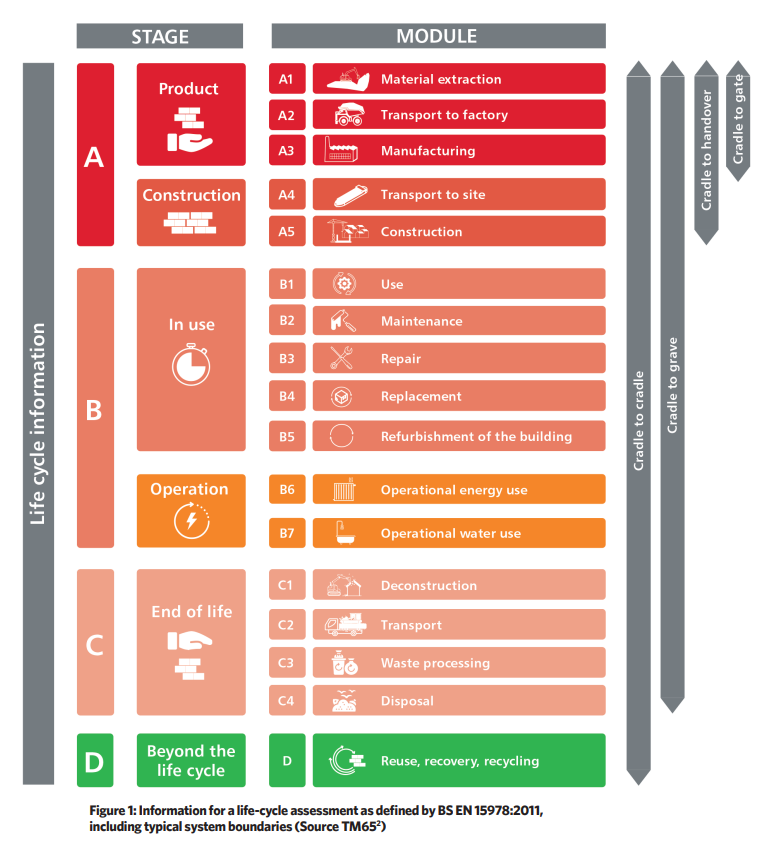
TM 65 notes that an EPD should be considered as the most reliable source of information about the environmental impacts of a product. In the discussion of the assessment methodologies, it is noted that ‘maintenance, repair, deconstruction and transport to waste processing are often not included due to lack of data’ – a challenge that affects current practical assessments and comparisons of products and the ability to determine an EPD, since that includes an assessment of the end of life stage (C1 to C4) and reuse, recovery and recycling (D).
As noted by TM 65, very few manufacturers of building services products offer EPDs, mainly because of the complexity of mechanical, electrical and plumbing (MEP) products and their supply chain, but also because incentives from the market and regulation are missing. TM 65 provides ‘basic’ and ‘mid-level’ methodologies that are complementary to the EPD in order to be able to assess and compare environmental impact realistically with reduced reliance on stages C and no inclusion of stage D.
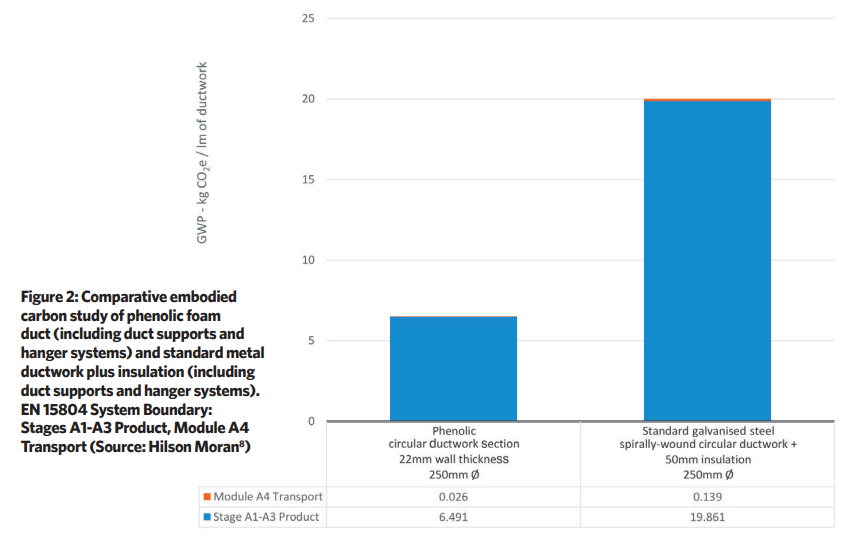
As described by Densley Tingley et al in their very useful paper,3 phenolic foam has a closed cell structure that resists moisture and water vapour ingress, so providing a suitable core material for insulation boards (which are used in forming ductwork), with a low thermal conductivity of 0.020W.m-1K-1 (compared with expanded polystyrene (EPS) at 0.038W.m-1K-1, mineral wool at 0.036W.m-1K-1 and polyisocyanurate (PIR) at 0.027W.m-1K-1).
In further work4 by Densley Tingley et al, they remark that in common with many building products, there is little published work on the end of life stage of phenolic foam (which, in the context of their paper, is referring particularly to external wall insulation systems), and owing to the layered nature of the systems – and the use of adhesives and tapes – it would be likely that any phenolic foam ductwork system removed at end of life would be viewed as contaminated.
As such, it would likely be sent to landfill, although it could be incinerated with energy recovery. It is noted that the importance of developing strategies for effective removal and disposal of such systems might best be taken into account during system development.
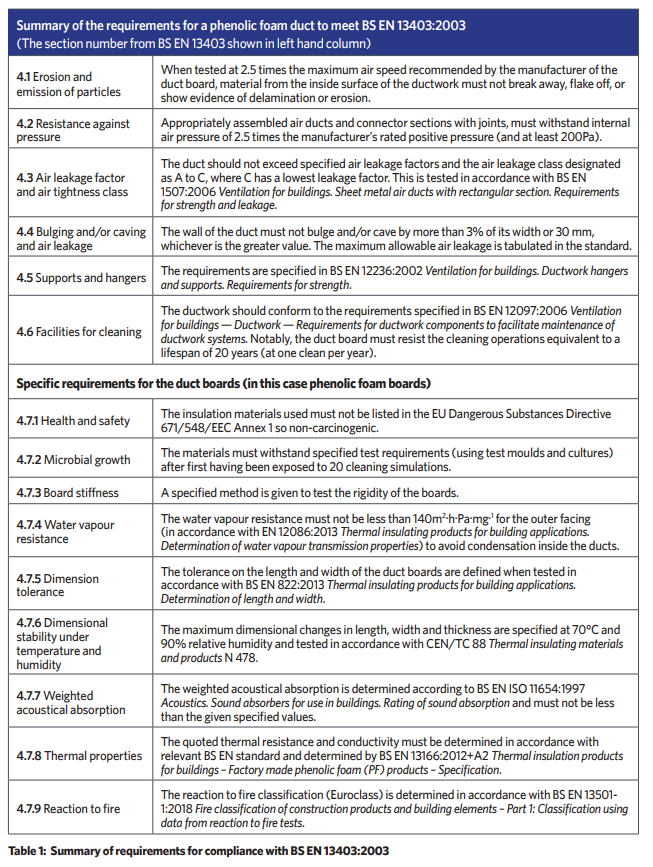
The relevant UK/European standard for the basic requirements and characteristics for ductwork made of insulation boards and used in ventilation and air conditioning systems of buildings (for human occupancy) is BS EN 13403:2003.5 The core requirements of the standard are summarised in Table 1.
Independent tests6 on a sample of a commercially available phenolic foam ductwork system indicate that the material and the fabrication method, as shown in a simplified form for a straight duct in Figure 6, produces ductwork that has integrity class C.
The US Underwriters List (UL) standards are often referred to when considering specifications for ductwork. UL 181 is an American National Standards Institution (ANSI) recognised standard for factory made ducts and connectors, which was most recently updated in 2021 – the standard may be viewed at no cost on the UL website.7
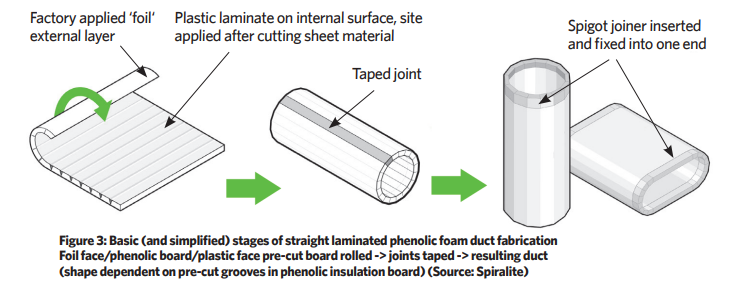
The standard provides a range of performance tests that cover similar areas to BS EN 13403, which in summary includes: testing for flame penetration and burning, and flame resistance (for jointing materials); corrosion resistance; and mould growth as well as tests on the structural integrity (including impact, puncturing, sagging, torsion and collapse) and stability under various temperature and humidity conditions. Ductwork systems that comply with the requirements of UL 181 are listed on the UL website bit.ly/CJFeb22CPD1
A comparative embodied carbon analysis8 was undertaken to illustrate the relative embodied carbon of an example length of phenolic circular ductwork compared with an equivalently dimensioned spirally wound galvanised steel duct. Although not a comparison of EPDs as defined by BS EN 15804, this was undertaken in line with the criteria from that standard for life-cycle stages A1 to A4. The comparison was based on a 10-metre length of 250mm nominal diameter ductwork including duct hangers, jointing and taping, with similar levels of insulation and vapour protection. This study did not include a consideration of the typically uncertain section C ‘end of life’ and section D ‘beyond end life’, but as shown in a summary of the findings in Figure 1, it indicates that the phenolic foam ductwork system had the significantly lower embodied carbon equivalent of the two.
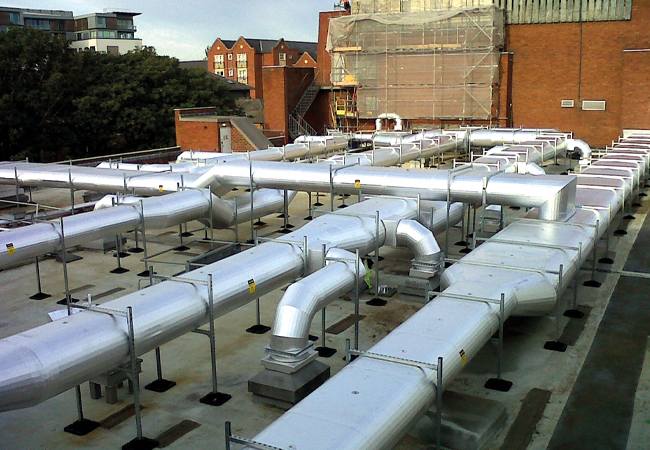
Figure 4: Weather-protected installation of a phenolic ductwork system on exposed roof. The weatherproof UV resistant laminate is tested up to 148C
A whole-life cost exercise (excluding operational energy use) was undertaken,9 comparing a ductwork system fabricated from a phenolic foam and one of mineral fibre insulated galvanised steel ductwork. It indicated a reduction in total cost (in the order of 20% for an installation of capital cost circa £175k) across the range of ductwork sizes in a low-pressure ductwork system. The report indicates that the phenolic foam ductwork system is likely to suffer minimal damage during its life, particularly where ductwork is installed within a ceiling void, and any repairs are relatively simply cut and fixed into the duct.
There are applications that are not appropriate for phenolic foam ducts including:
- Unprotected outdoor or underground use (an example of properly protected external phenolic foam ductwork is shown in Figure 4)
- Carrying solid particles or corrosive gases
- Smoke extraction from kitchens, laboratories, and so on
- Where the minimum air temperature is less than -20°C
- Where humidity conditions are outside manufacturers’ specifications.
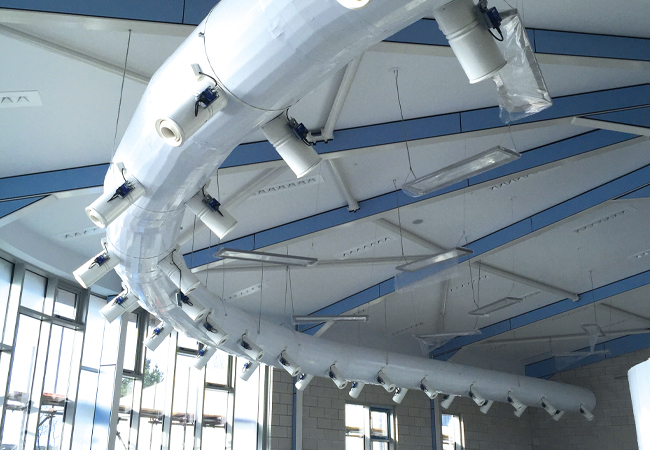
Figure 5: Internal installation of phenolic foam ductwork
However, there are many applications that may be suitable. In commercially available phenolic foam ducting, the plastic laminate coating on the internal duct face has a low equivalent roughness factor that, as well as not supporting mould growth and having anti-bacterial properties,10 provides a low air pressure drop, so reducing energy consumption and operational carbon. The lightweight phenolic foam duct (as illustrated in Figures 3 and 6) can also allow the routing of ductwork in situations where metal ductwork could not be adequately supported by the structure.
Just as with any ductwork system, the stage B ‘in use’ and ‘operation’ factors can be significantly impacted through the quality of the design and the integrity of the installation, operation, and maintenance. Each application must be individually assessed so that the designer has confidence that the solution is safe and can provide an efficient lifetime solution.
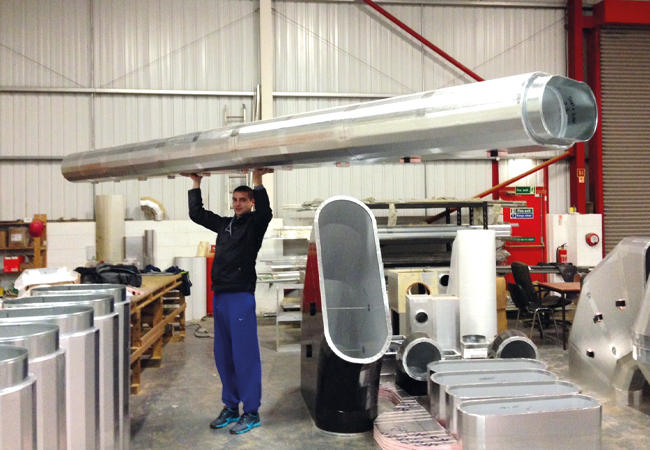
Figure 6: Example phenolic ductwork prefabrication showing end joint spigot/socket connection, illustrating the low mass of the fabricated duct (Source: Spiralite)
© Tim Dwyer, 2022.