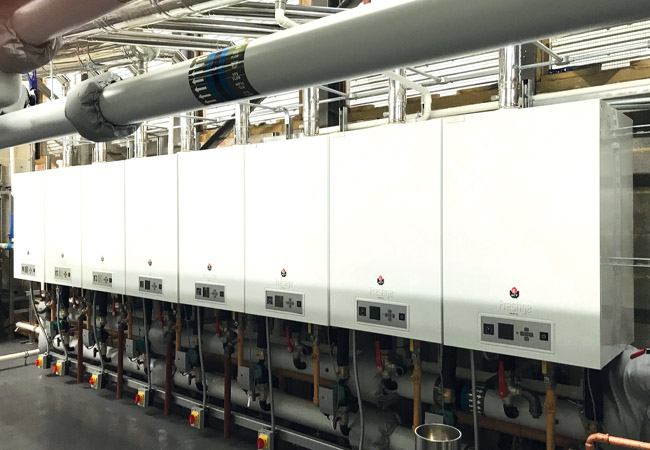
Many materials are used in manufacturing of products for generating and storing hot water for heating and domestic hot water (DHW) systems in buildings. This article provides a commentary on the factors that are driving the rise in the selection of stainless steel for the core working elements of heating and hot-water plant installed in UK buildings.
The principal factors that decide the suitability of a material for a product are its performance and the total life-cycle environmental impact and cost. For gas-fired boilers used for heating, as well as dedicated hot-water heaters that, in this article, will be referred to collectively as hot-water generators, materials have been selected for the heat exchanger with the aim of maximising effective and reliable heat transfer from the gas flame – and resulting combustion gases – to the water.
In common with hot-water stores, a key challenge for hot-water generators is to maintain long-term performance while limiting the risk of corrosion caused by the water and its impurities.
CIBSE Guide G1 defines corrosion as ‘the reaction of a metal with its environment resulting in damage which impairs the function of a component or system’. Depending on the material, oxygen is one of the most important factors when considering corrosion. In closed systems, such as heating circuits, oxygen levels may typically be controlled by limiting fresh make-up water or using deaeration devices. DHW systems, however, will necessarily have continually replenished – and so oxygenated – water.
Wet corrosion is the most significant form of corrosion, and occurs by an electrochemical oxidisation reaction that requires the presence of oxygen. For example, steel reacts with the water and oxygen to form hydrated iron(III) oxide – rust that, unless prevented, will eventually cause structural failure.
The attributes of the water – the ‘water quality’ – that is being heated in a water heater, whether for a closed heating system or a DHW system, will directly impact the potential amount of corrosion affecting the materials used in the fabrication of the heater (as well as in the wider distribution system). Water quality will depend on the geographic location of a building, as well as whether the water is supplied from a mains pipe or sourced from a local aquifer.
The hardness of water relates to minerals suspended in the water, such as calcium and magnesium bicarbonates, measured in parts per million (ppm), and is normally related to the geology of the region. ‘Hard water’ derives from groundwater passing across limestone, chalk and gypsum deposits and is typically designated as a water hardness in excess of 280ppm.
‘Soft water’, where hardness is 100ppm or less, is prevalent in areas that are formed of hard igneous rock, such as granite. The pH of water tends to be lower, below pH 6.5, and so acidic, in soft water areas, and hard water is considered as most often having a pH above 8.5, so alkaline, that is also referred to as ‘basic’ water.
Across the UK, groundwater drawn in Scotland, the south west and north west of England, west Wales and most of Northern Ireland is typically soft water.
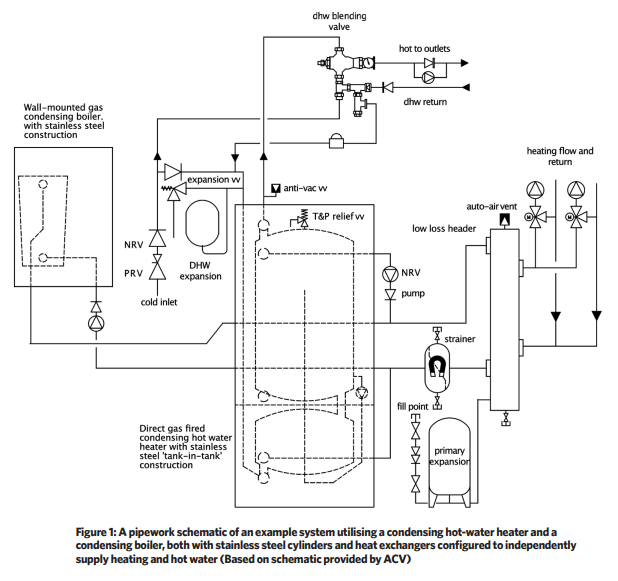
In hard water areas, the excess minerals in the alkaline water may accumulate as the water is heated and then solidify as scale, which will reduce the performance of heat exchangers and impede the flow of water, as well as interfere with the operation of valves.
Such scale can significantly derate the performance of hot-water generators, and preventative methods – such as water softening – may be required.
Acidic water can promote corrosion by developing pitted surfaces. In closed circuit heating systems, corrosion inhibitors are routinely used to limit corrosion, especially if some oxygenation of the system water occurs. Some inhibitors contain anti-scaling components, but in hard water areas, the use of water softening may be considered.
A balance of factors, which will be specific to the application and the local water quality, will determine the material that provides the most effective solution taking into account the system requirements during the operational lifetime of the product.
The evolution of hot-water generators and revolution in hot-water stores has seen a variety of metals including copper, cast iron, aluminium, steel and stainless steel that continue to be used today.
Copper, with high thermal conductivity, high ductility and malleability, was an early choice for hot-water heaters and in recent years, predominantly for indirect hot water coils and storage vessels such as hot-water storage cylinders (calorifiers).
Copper will typically develop copper oxide films that will coat its surface and, although protective to corrosion from normal water use, are not true passive layers (like the much thinner layers that form on stainless steel and aluminium). General corrosion of copper only occurs in low pH water (acidic) that should never flow from mains water in the UK.2
Increasingly, applications of pressurised, unvented hot-water systems and larger hot-water stores have reduced the application of malleable copper for cylinders.
Cast iron was traditionally the material used in boiler heat transfer surfaces owing to its robust nature and resistance to the impacts of highly sulphurous flue gases produced from burning coal and oil.
Cast iron heat exchangers are thick and weighty; however, cast iron is not suitable for condensing applications because of the risk of corrosion from acidic flue gases that means it struggles to meet the modern environmental, spatial and operational requirements of many applications.
Aluminium has been commonly used over the past 50 years for heat exchangers in hot-water generators. It is alloyed with other metals that can be cast to produce complex, high thermal conductivity waterways in a heat exchanger block that is lightweight with excellent heat transfer properties.
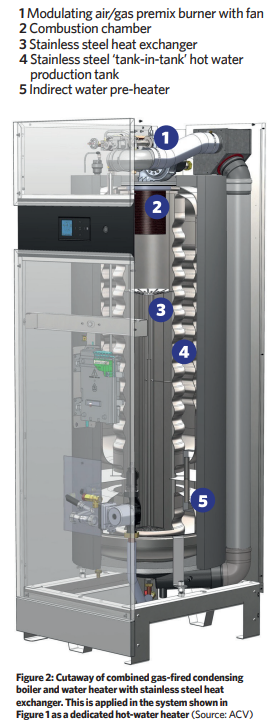
Aluminium is often employed because of its lower cost, low mass and high efficiency, and the low density of aluminium will typically mean that heat exchangers have a similar embodied energy to steel. To prevent corrosion, water should be maintained at pH 6.5–8.5 (where needed, this can typically be maintained with commonly applied water treatment regimes).
With the increased application of unvented indirect hot-water cylinders, larger thermal stores, and direct gas-fired, condensing hot-water heaters, steel has become a popular choice for hot-water heaters, as well as in boiler applications.
Steel provides a robust container for hot water but requires a water-side glass lining to prevent the water corroding the surface of the steel, as well as – where appropriate – a fire-side glass lining to protect against low-pH, high-acidity condensate from the flue gases.
Although such glass-lined tanks are relatively sturdy, it is practically impossible to apply, and maintain, the glass surface coating in a perfect state, so a passive anode rod is typically installed inside the cylinder to provide galvanic cathodic protection against corrosion.
The anode, created from a metal such as magnesium – having a more negative electrochemical potential than the steel – is sacrificially ‘consumed’ in the process of losing electrons, as the water serves as an electrolyte and the cylinder’s steel shell as the cathode.
A functioning sacrificial anode will typically last from three to five years but requires regular physical checking – and replacing as needed – as the rate of deterioration will depend on the actual water quality and flow rate. In hard-water areas, sacrificial anodes can function because of high water electrical conductivity caused by ions in the water.
Soft water, with fewer electrolyte ions, has lower electrical conductivity, reducing the current from the anode to the cathode, so inhibiting protection. A sacrificial anode applied in these circumstances will provide little or no protection and will appear to remain in excellent condition. However, the steel is potentially at risk and either requires a powered anode or should be substituted with a different cylinder material.
The alternative is a non-sacrificial electrically-powered anode (alternatively known as an impressed current anode) that produces a very low current in the water and provides the same protective effect on the steel shell but without significantly corroding the anode. The electrical anode is often made of titanium, which could potentially last the lifetime of the hot-water cylinder.
In extreme soft-water areas, this system may not have sufficient protective effect, as water conductivity can be low. Electrical anode protection can be capitally expensive because of the device costs and the additional electrical connections required for installation.
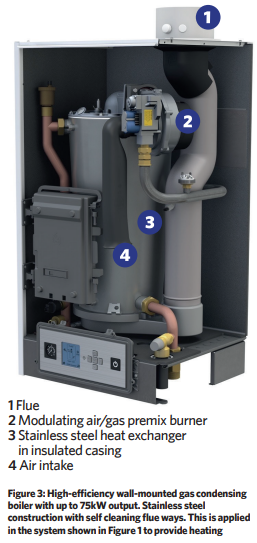
However, over the product lifetime, it can prove more cost-effective than maintaining and replacing sacrificial anodes – though to function, it requires a continuous, uninterrupted, power supply. Both methods of cathodic protection will incur a recurring maintenance activity and associated cost to the life-cycle of the appliance.
Austenitic stainless steel (see boxout ‘Austenitic stainless steel’) does not require cathodic protection in order to prevent corrosion on its surface. As with aluminium, appropriately selected stainless steel is able to withstand the corrosive attack of flue gas condensate and so provides an appropriate material for the cylinder and heat transfer surfaces of condensing gas-fired hot-water generators.
There tends to be regional preferences for employing stainless steel in soft water areas where glass-lined appliances have proven to have a short service life, with stainless steel recommended up to a more challenging pH 9.5. The ability to withstand harsh operating conditions while providing reliable and consistent performance without the use of galvanic protection can be deduced by manufacturers providing long warranties against corrosion for stainless steel hot-water products.
Stainless steel hot-water generators (such as that shown in Figure 2) and hot-water stores are lighter in weight than the equivalent products constructed of the more fragile glass-lined steel and so will require less costly handling and installation. Hot-water generators and stores that employ stainless steel will typically have a higher capital cost compared with alternatives.
The gap in pricing between stainless steel and the equivalent glass-lined steel products can vary widely as the prices of raw materials fluctuate, but the difference may be diminishing because of increases in overall production costs.3
Stainless steel has relatively low embodied carbon compared with other commonly used materials, and selecting products that are manufactured with high-grade, corrosion-resistant stainless steel will contribute to their longevity, and so reduce whole-life carbon impact. Increasingly, building services product specifications are nominating stainless steel hot-water products, as it is perceived to be a ‘safer’ material because of its resistance to corrosion and its long life span.
Austenitic stainless steel
Steel – an alloy of iron and carbon – when heated to a liquid molten state, and then cooled and solidified, forms crystals. The gradual formation of crystals can mean that any one type of steel is actually made up of several crystal types as the metal passes through multiple temperature stages,4 and it is not uncommon for steels to contain a mix of structures.
Austenite is created in steel at 912°C, at which point it transitions to a ‘face-centred cubic’ crystal structure that can absorb up to 2% carbon. The non-magnetic austenitic crystal structure is maintained at ambient temperatures through the inclusion of additives when melting steel alloy.
Stainless steel is a generic name for more than 150 carbon steel alloys that have a minimum of 10.5% chromium, each alloy having its own particular properties and applications.
Chromium makes stainless steel corrosion resistant by oxidising quickly, forming a thin oxide layer on the metal surface that protects the underlying metal from corrosion. With this thin passive film completely covering the metal surface, the metal is passivised and corrosion is greatly reduced.
Common austenitic alloys contain 15–20% chromium together with 6–11% nickel that gives it strength and ductility. 300 series grade stainless steels contain approximately 18% chromium and 10% nickel.
Most commonly used grades of stainless steel employed in hot-water generators are 304, 316 and 316L, which have a high level of corrosion resistance, and the ability to shape and form the metal into tanks and detailed heat exchangers. ‘L’ designates a lower proportion of carbon (not exceeding 0.03%) in its composition, which reduces the risk of carbon precipitation, making it a more appropriate material choice for welding.
By adding 2% of molybdenum to type 304L creates type 316L, which has increased resistance to pitting and crevice corrosion in chloride-rich environments, and is typically used in heat exchangers for condensing boilers. The higher alloy-grade stainless steels will be more costly.
Stainless steels perform best under fully aerated or oxidising conditions to maintain their protective film, and so are ideally suited for DHW generators and thermal stores.
Any conditions that cause the protective films to break down can result in corrosion rates comparable to those of mild steel. Austenitic stainless steels, at high pressure and temperature, exposed to chloride ions can suffer rapid pitting and initiate intergranular attack and stress corrosion cracking, as discussed on the web resource Corrosionpedia.5 An example source of such chlorides is inappropriately selected encasing thermal insulation that has become wet.
Some of the earlier applications of stainless steel heat exchangers suffered from corrosion failures at welded points. With the appropriate selection of materials and good welding procedures this can be minimised, as discussed in a useful web article6 by Kasay Mwiks.
© Tim Dwyer, 2022.