The Ecodesign regulations for ventilation units provide the standards that are employed across the EU and the UK to determine whether a manufacturer’s system can be formally marked as meeting reasonable levels of operating efficiency. Undoubtedly, these standards have encouraged developments in products so that they can meet requirements.
However, an unintended consequence of universally applying such prescriptive rules is that it can restrict the acceptability of alternative methods and products that are able to deliver a higher level of performance. This CPD will explore how this can provide unexpected levels of performance from a new generation of ventilation units that may, on first inspection, not meet Ecodesign requirements.
In Great Britain and Northern Ireland, the Ecodesign for Energy-Related Products (ErP) Regulations 2010 are the underpinning legislation to set efficiency standards for ventilation units. EU regulation 1253/20141 implements Ecodesign requirements for ventilation units and enables products to be CE marked.
The EU legislation provides the basis of the UK’s post-Brexit requirements for the UK Conformity Assessed (UKCA) mark. (Until 31 December 2022, practically all EU-recognised, CE-marked, goods can continue to be placed on the market in Great Britain.)
Fan power
Specifc fan power (PSFP or SFP) is a standardised measure of how much total power is required by the fan to move air through either the VU alone at set parameters, or the whole connected system, and is expressed variously as W·L-1·s-1, kW·m-3·s-1 or (multiplied by 1,000) as W·m-3·s-1. Typically, SFP = (total electrical power, W)/(air volume flowrate, m3 ·s-1)
The ErP requirements for non-residential applications of bidirectional VUs (BVUs) are defined by a reference model of being cased with internal intake and extract fans, a heat recovery system, a clean fine inlet filter and a clean medium filter on the exhaust-side, as illustrated generically in Figure 1. The EU regulations’ most recent phase was implemented in 2018, as summarised in Table 1.
Key parameters in assessing the energy efficiency of ventilation units are the specific fan power (SFP – see boxout) and the thermal efficiency of the heat recovery device. The standard includes specific requirements for control and the heat recovery performance.
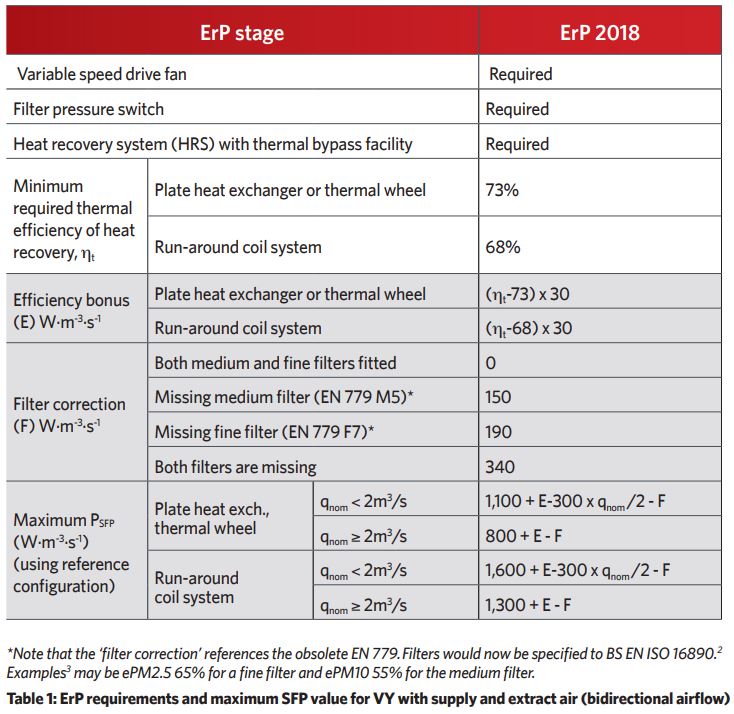
The shaded area of Table 1 (overleaf) is used to determine the limiting SFP for a unit. The electrical power input – including that used by any motor control equipment – is considered at the maximum flowrate in the manufacturer’s declaration for the unit and is not the power marked on the fan nor, potentially, the power consumed at the best efficiency point for the fan. In the case of a BVU (such as in Figure 1), this would be the sum of both the supply and extract fan powers.
The efficiency bonus, E, in the BVU table is added to the total allowable SFP to provide an allowance for the additional pressure drop through the heat recovery device. The filter correction, F, is a value that is subtracted from the allowable maximum SFP if a BVU is missing one – or both – filters. Effectively this expects that the BVU will require the filters when it is installed. In some circumstances, this could be considered as a penalty for not employing filters that may not potentially be needed in areas with good air quality.
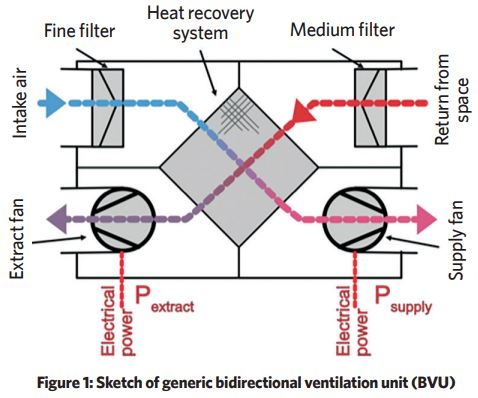
The ‘nominal flowrate’ – qnom – is the ‘declared design flowrate’ so the manufacturer has the freedom to determine such conditions, depending on specific design choices (for example including or excluding a pressure reserve to overcome any ‘clogging’ as the unit becomes dirty). The ‘nominal flowrate’ is delivered at the maximum-rated fan speed.
These ecodesign requirements do not apply to VUs that operate below 30W power consumption per air stream or under special conditions, such as corrosive environments or high temperatures.
A greater level of heat recovery performance typically provides an increased pressure drop, owing to the narrower passages in the heat exchanger unit. This leads to a higher electrical energy use, for both the intake and extract fans. However, greater heat recovery performance will recover additional heat energy that can reduce space heating loads. The energy balance between both is – aside from system characteristics – strongly affected by climate.
In an effort to provide increased energy efficiency, hybrid ventilation systems have been developed that integrate both natural and mechanical ventilation modes. These employ high-efficiency fans and optimised, segregated, automatically switchable internal air paths designed to benefit from maximising the application of natural ventilation, hybrid-mixing ventilation and low-energy mechanical ventilation with heat recovery.
These include low pressure-loss heat exchangers to utilise space heat gains to temper incoming outdoor air. The heat exchanger trades thermal effectiveness for a low pressure drop, as illustrated in Figure 2.
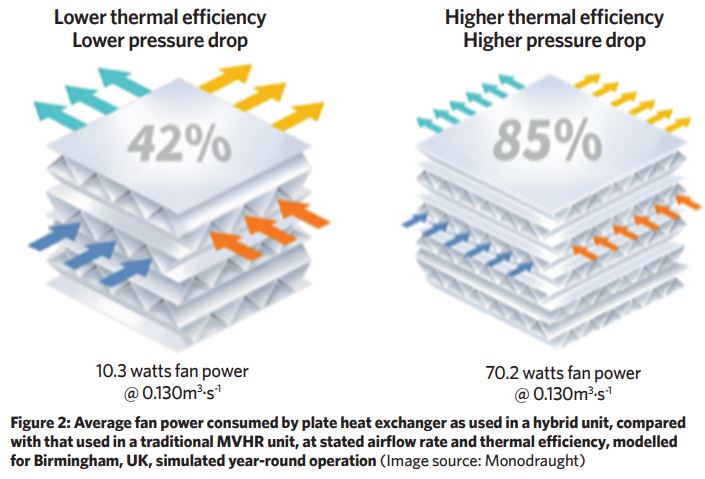
During the summer months, hybrid ventilation – such as the example of Figure 3 – employs the fan to boost the natural ventilation and optimise indoor comfort. During winter, the hybrid system mixes warm internal air with outdoor air to deliver mixed tempered air, and can also utilise the heat recovery function to save energy. The mechanical ventilation combines with openable windows to expel stale air and ventilates the space with outdoor air.
Units can also include low air pressure drop cooling and/or heating coils (potentially linked to a heat pump) to control the supply air temperature during periods of higher cooling and heating loads. As with traditional recirculation fan-coil units, these can be used for pre-occupation preheat and night cooling.
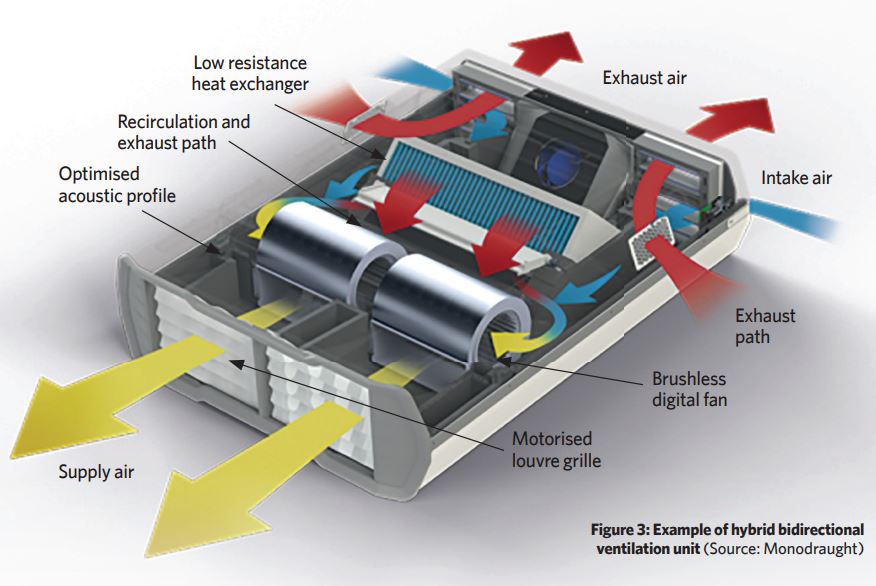
However, as might be suspected, such systems do not conform with the standard operation that would be expected of a BVU by EU regulation 1253/2014. To determine the optimum trade-off between higher electrical energy use and higher heat recovery, dynamic simulation models may be used.
A study4 undertaken on behalf of a manufacturer compared the performance of hybrid and traditional MVHR units, by modelling systems for a newly constructed school in London. The study included models both with and without heat recovery.
The calculation was completed using both the simplified building energy model (SBEM) and a dynamic simulation model (DSM) to evaluate the sensitivity of the applied modelling methods on the CO2 emissions and to produce an energy performance certificate (EPC) rating. The characteristics of a selection of the modelled systems included in the study are summarised in Table 2.
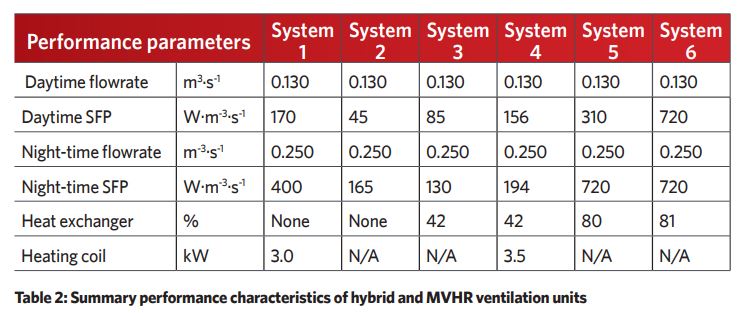
Systems 1 and 2 represent older hybrid ventilation units that provide a mixing function to mix room air with incoming fresh air to temper the supply ventilation air temperature but have no heat recovery device.
Systems 3 and 4 are optimised hybrid ventilation units similar to that shown in Figure 3. System 4 additionally includes a heating coil. It is notable that despite System 3 including a heat recovery device, the SFP is lower than that of System 1, which has no heat recovery.
Systems 5 and 6 are both high-performance MVHR units but with different SFP values.
All the units that were modelled were commercially available from UK companies.
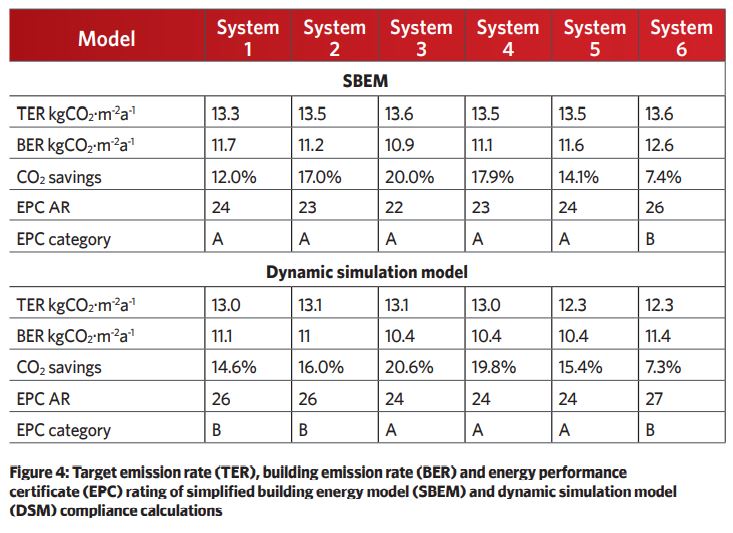
In the SBEM modelling, all units were defined to provide night-cooling operation for 200 hours (maximum) per month. The heating source was a condensing gas boiler with a SCOP of 0.965. System 1 and 4 employed a heating coil in the unit. The remainder of heating was provided by a room-based radiator system.
The results showed an average CO2 saving of around 16% across all VUs compared with the emission of a notional building. The best performance, as illustrated in Figure 5, was System 3, which provided more than 20% savings in both the SBEM and the dynamic simulation model calculation. This hybrid system has a lower pressure drop through the lower-efficiency heat exchanger that delivers a thermal efficiency of just 42% compared with the ErP requirement of 73%.
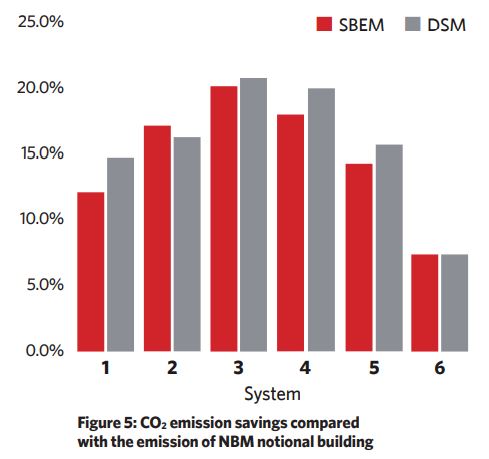
In terms of EPC, the SBEM method was not as sensitive to the individual variations between the unit efficiencies that were generally in a very good category, and all the units provided an ‘A’ for the EPC rating, except System 6 (with its high SFP).
The dynamic simulation model calculation provides more detail, penalising the units without heat recovery so that their EPC rating slipped back to ‘B’.
Ventilation designs that have lower-efficiency heat recovery performance – or in the case of natural ventilation, do not include heat recovery – may be viewed as performing poorly. However, the analysis reported in this article indicates that, when the climatic conditions and the building’s own internal heat gains are included, the thermal efficiency can become less important than the fan power, as demonstrated by the SFP. As with the assessment of many building systems, this suggests that a holistic approach is essential when analysing the options for ventilation, in order to deliver the most effective solution.
© Tim Dwyer 2022.
- This article drew on the modelling and commentary as reported in Compliance modelling for Monodraught HVR Zero systems – available from www.monodraught.com/landing-page/7165
References:
- Commission Regulation (EU) No 1253/2014 of 7 July 2014 implementing Directive 2009/125/EC of the European Parliament and of the Council with regard to ecodesign requirements for ventilation units.
- BS EN ISO 16890-1:2016 Air filters for general ventilation. Technical specifications, requirements and classification system based upon particulate matter efficiency, BSI 2016.
- bit.ly/CJNov22CPD21 – accessed 1 October 2022.
- Report on study conducted by GTA Consultancy on behalf of Monodraught – available form Monodraught.