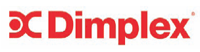
Opportunities and enthusiasm for the application of electrical systems in buildings – and particularly homes – are on the rise where, until recently, the standard selection of environmental services would have probably included the combustion of fossil fuels. This CPD will examine some modelled scenarios to evaluate whether a sample of currently available electrical systems can be applied to meet the demands of regulatory performance standards.
In systems designed for new dwellings, a mixed mode of delivering hot water and space heating will probably prevail, which will use several electrical technologies to meet both the heating and hot water load – the provision of hot water being the dominant heat load.
The systems that have been considered in the modelling, as described later in this article, are listed in Table 1. These are based on well-established principles and technology, with some of the systems’ components having been more recently refined and developed into products that can deliver high performance with flexibility and a lower environmental impact than traditional systems.
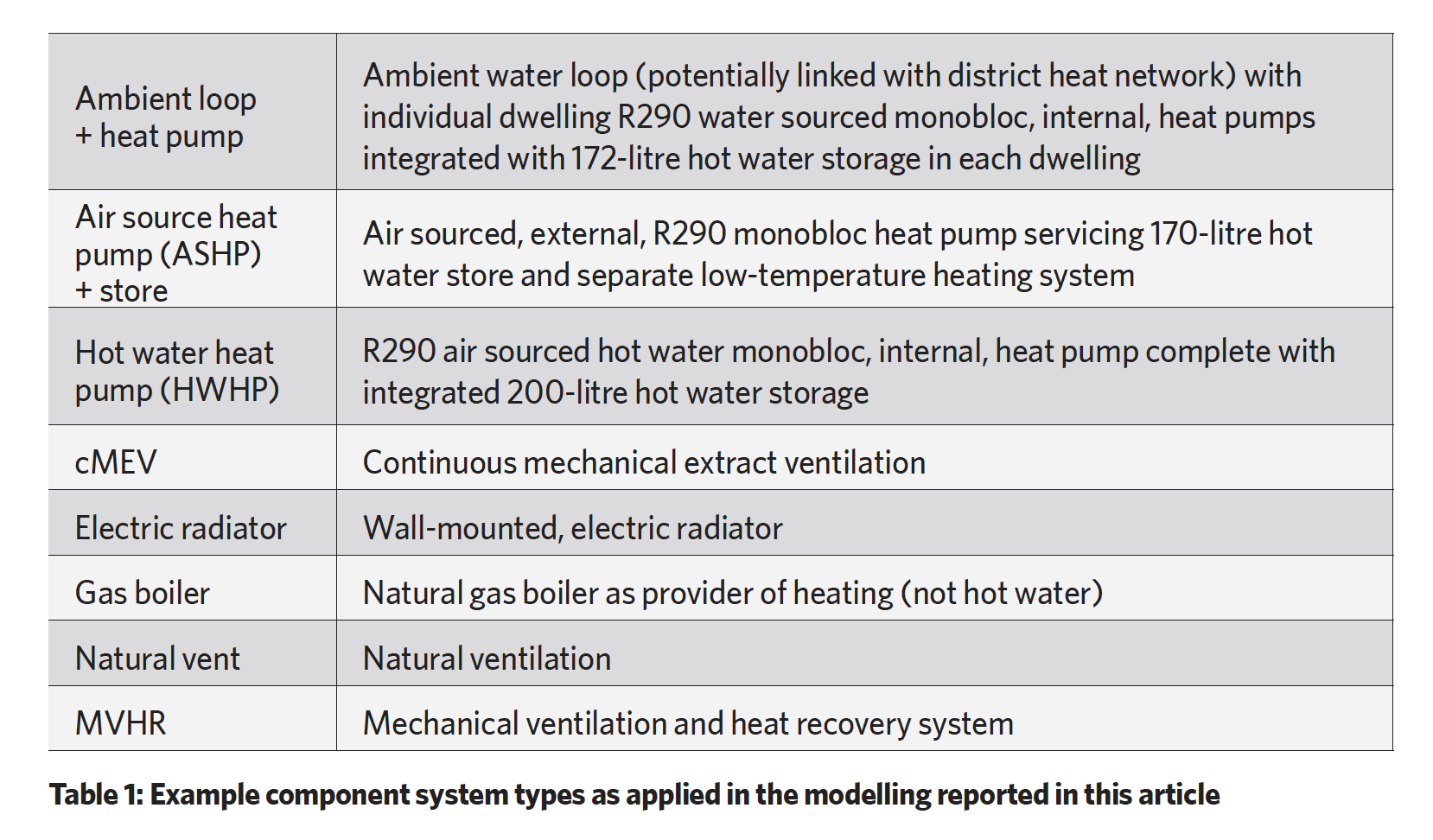
Whichever combination of systems is employed, the success of the whole building will be dependent on the method of control and how ‘smart’, well integrated and accessible it is for the building occupants. The systems and sub-systems will typically include linked sensors and local control (including independent timing/zoning), which communicate via wireless communication (using, for example, Wi-Fi, Bluetooth, ZigBee and proprietary protocols).
These can apply a variety of regimes including timed, optimum start, weather compensation, adaptive and predictive control. Heat pump compressors will typically have variable speed control to satisfy a wide range of operating conditions.
There are three variants of heat pump applications in Table 1. The ambient loop + heat pump arrangement was discussed in CPD module 190 (CIBSE Journal January 2021). This employs a local or district heat network, typically circulating treated water with a flow temperature of between 15°C and 25°C to supply heat (or coolth) to an indoor unit. The ambient heat network might receive low-grade heat from any suitable source, such as waste heat recovery from processes and buildings; high efficiency low temperature heat pumps (water, ground and air source); sewage treatment; and mine water sources.
Although there are a number of possible permutations for moving the heat into the residence, a flexible arrangement, allowing individual occupier control (and billing), is to provide a compact monobloc heat pump and water cylinder in each residence, which is connected to the central ambient water loop. The heat pump is designed to supply both the domestic hot water and hydronic heating systems (and, optionally, cooling).
Units are designed to fit within a standard utility cupboard or kitchen unit. The connected heating distribution may be any suitable hydronic sub-system (such as underfloor heating, fan assisted or plain radiators, or fan coils).
The air source heat pump (ASHP) + store is an external monobloc heat pump that, using inverter speed control, is able to supply variable temperature primary heating water to an internal unit (as in the example of Figure 1). The internal unit controller sets the external unit to supply water at the correct temperature to either service a hydronic space heating sub-system or to heat the domestic hot water store.
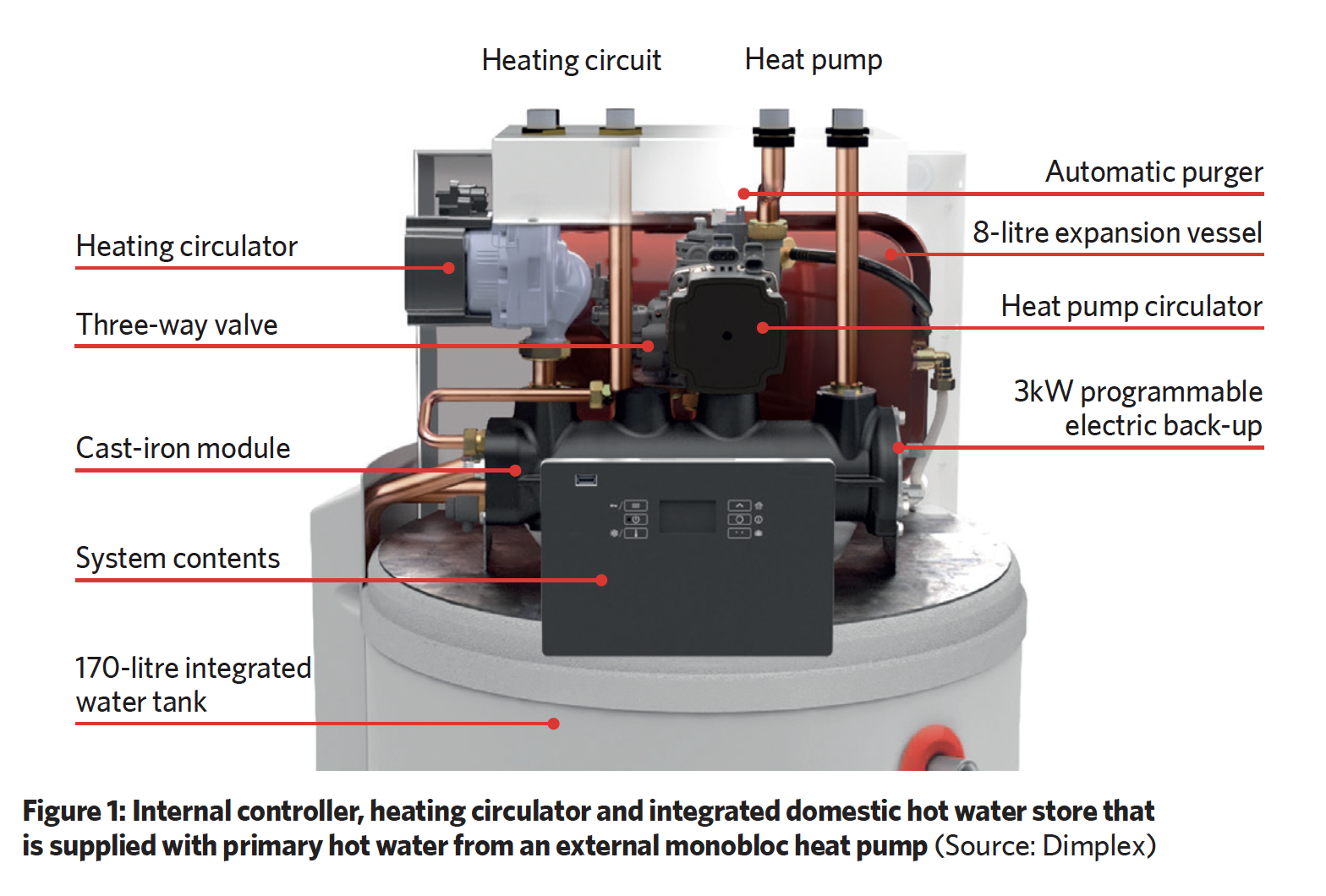
This particular R290 system, available with 6kW and 8kW output, can operate in outdoor temperatures down to -20°C and produce hot water in the 170-litre integral store up to 60°C with a seasonal coefficient of performance (SCOP) for the heating up to 4.85 at 35°C and up to 3.93 at 55°C.
(The wider modelling exercise also included a similarly sized split ASHP system and integral store employing R32 refrigerant that provided comparable results to the monobloc system.)
A dedicated hot water heat pump (HWHP) is designed to meet the hot water needs of the dwelling (with the space heating being supplied by other means, such as electric radiators). The example shown in Figure 2 is a R290 monobloc heat pump with COP up to 3.36 (at ambient 7°C, water 53°C), integrated with hot water stores up to 270 litres, supplied with heat from the outdoor air via circular ducting and which rejects cooled air from the evaporator through a separate duct (smaller units employ concentric, single conduit, ducts). Since this is a completely independent unit, it can be employed in a mixed-mode installation with other fuel types.
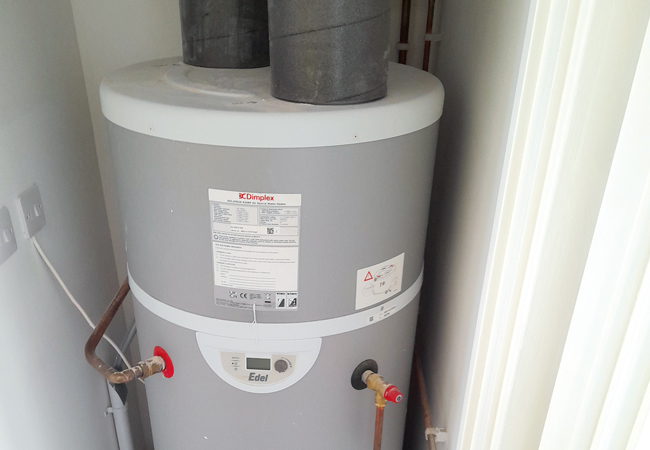
Figure 2: Hot water heat pump installed in the top section atop an unvented, stainless steel, 200-litre domestic hot water cylinder (this particular model also available with 170- and 270-litre cylinders) (Source: Dimplex)
To illustrate the opportunity of employing electrical-powered environmental systems, a selection of example homes with a variety of environmental systems were modelled (on behalf of the supporter of this CPD article) with the method provided by SAP 10.2.
The resulting data illustrated in this article are the individually modelled dwelling primary energy rates (DPER). Primary energy is useful for performance comparisons between various building systems, and is described by the Building Research Establishment (BRE) as being ‘energy from renewable and non-renewable sources which has not undergone any conversion of transformation process’.
[Well title = ‘SAP – Standard assessment procedure for energy rating of dwellings’]
SAP1 is a UK methodology to determine the energy compliance of dwellings. It sets out the requirements for the energy efficiency of new and existing buildings, including the amount of primary energy use and carbon emissions. The methodology takes into account factors such as the building’s fabric, heating and cooling systems, ventilation mode, lighting, and energy sources.
SAP is occasionally updated to reflect changes in building regulations and advances in technology, and its use is a requirement for compliance with England and Wales Building Regulations. The most recent update is SAP 10.2, introduced in 2022. (For existing dwellings, a simplified version of SAP – Reduced Data SAP (RdSAP) – is used to assess energy performance.) For SAP calculations, dwellings have a standard occupancy and usage pattern, which applies typical values that in practice vary substantially between dwellings of similar size and type. SAP calculations are not suitable for design purposes.
[/well]
The target primary energy rate (TPER) is the regulatory annual maximum primary energy use, expressed as kWhPE per m2 per year. This is determined for a notional building (as part of a SAP10.2 assessment), and the resulting TPER is compared with the DPER calculated for the actual dwelling, using the method in the SAP guidance. Other metrics are provided as output from SAP assessments including carbon emissions and fabric energy efficiency, which similarly have set maxima for compliance.
The modelled dwellings included the following residences, all east facing:
- Two-bed and three-bed end of terrace or semi-detached dwellings with 57m2 and 77m2 floor area, respectively
- Four-bed detached dwellings with 122m2 floor area
- Two-bed flats with 61m2 floor area – situated on the ground floor, intermediate floor and the top floor.
The fabric and lighting specification used for the models are shown in Table 2 and the component environmental systems in Table 1. The modelled houses with electrical panel heating were also selectively fitted with 250Wp solar photovoltaic (PV) panels, as shown in Table 3.
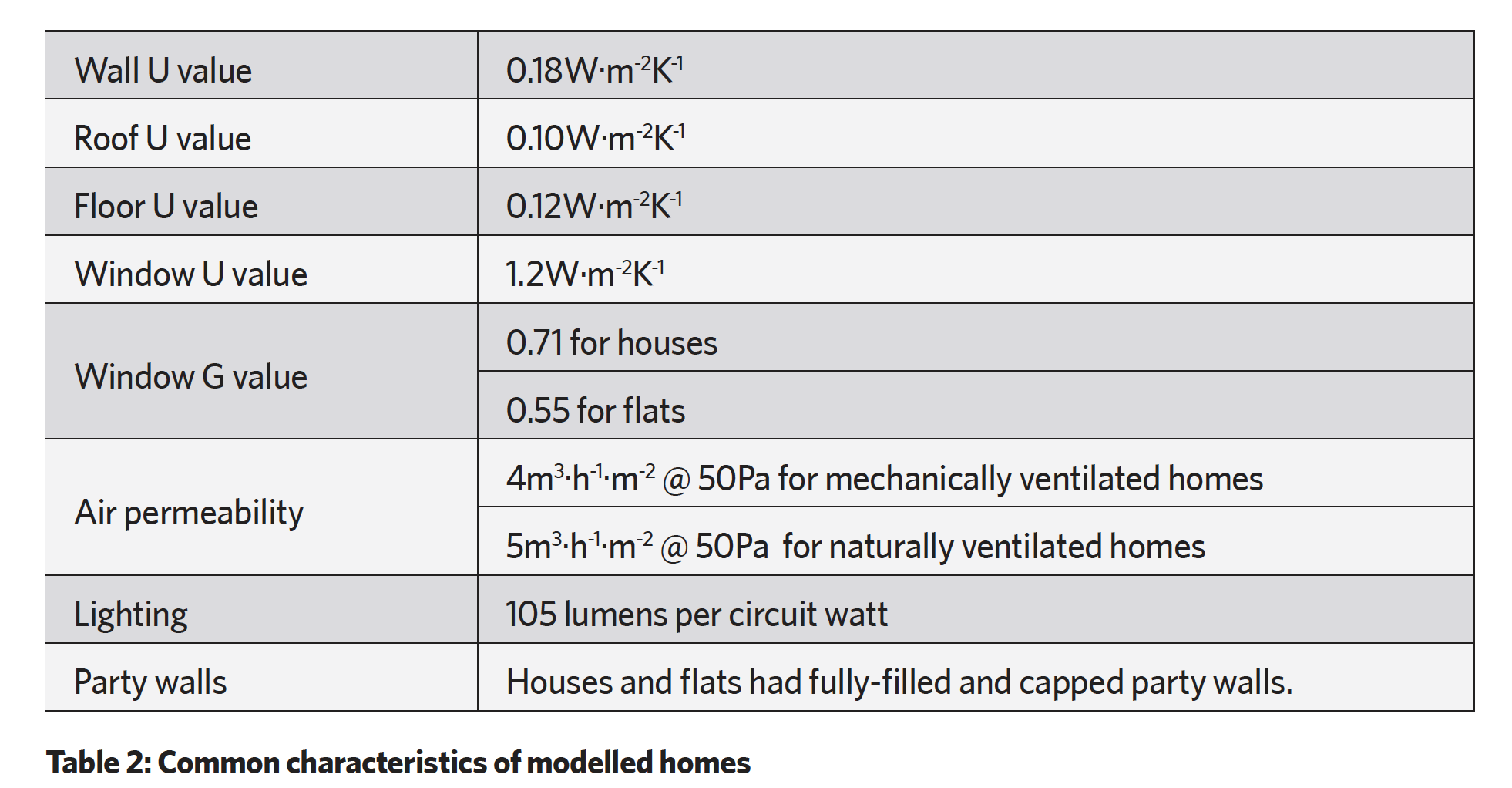
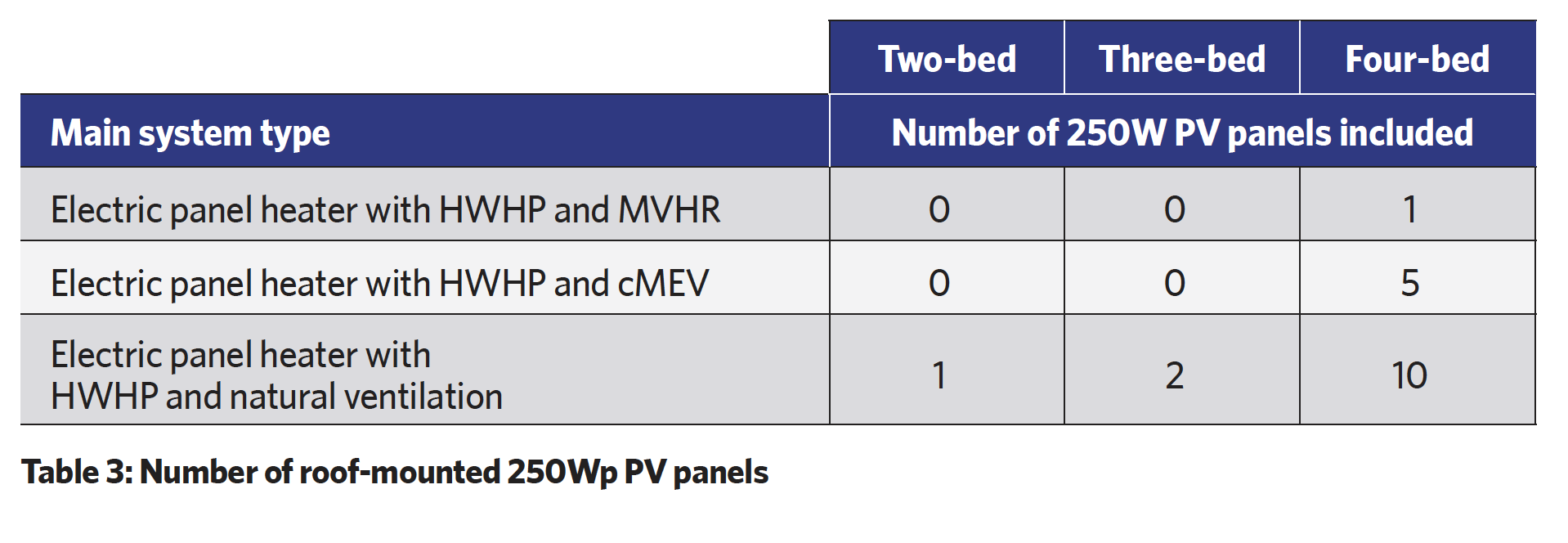
As with any modelling exercise, the output is dependent on the assumptions that were made in creating the digital representation of the building and the systems. The modelling output was used to create the charts in Figures 3 and 4. (The complete output from the model included the full set of metrics used for compliance purposes.)
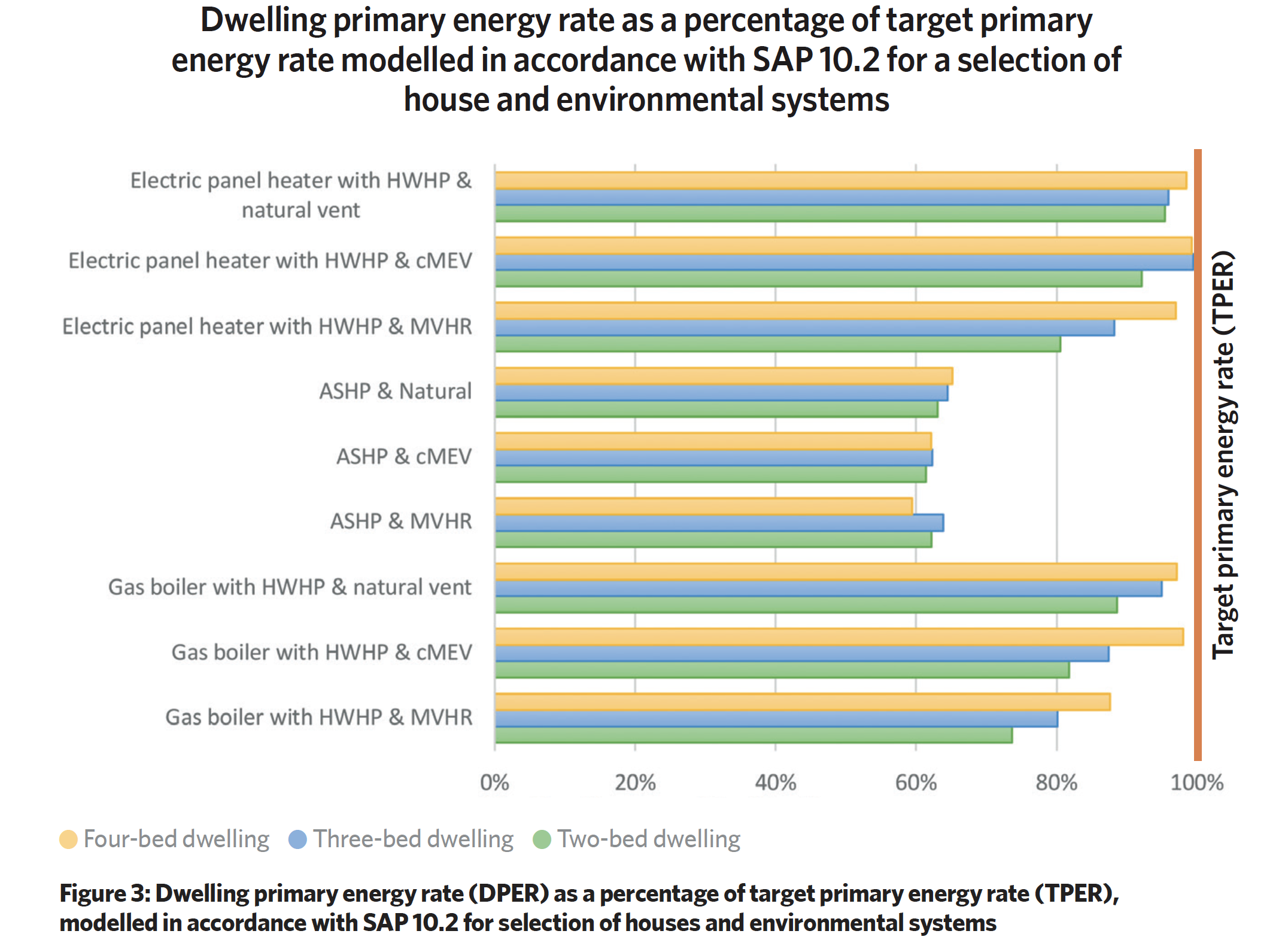
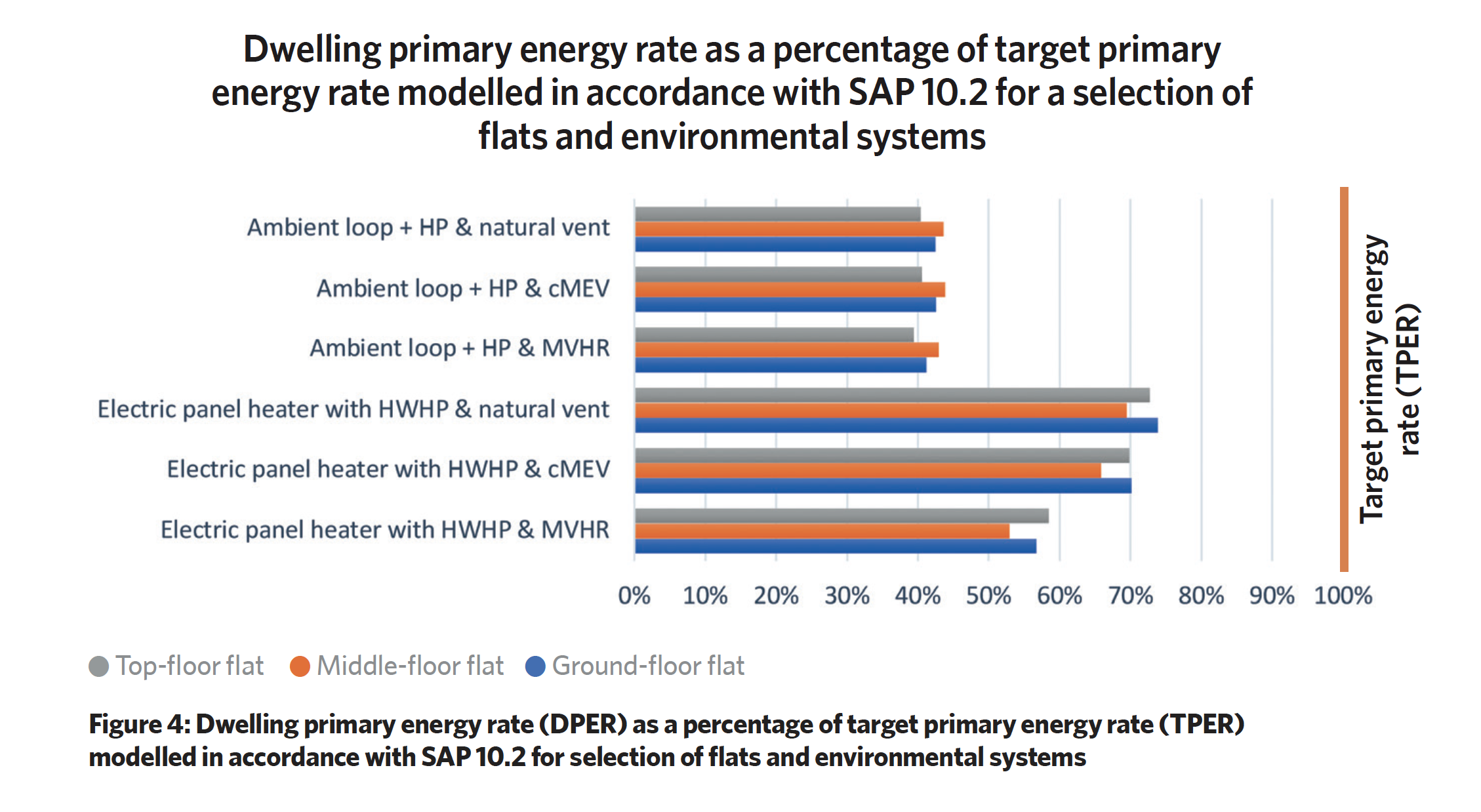
The TPER indicated by the orange line is the maximum that is deemed acceptable in normal new dwellings to meet the requirements of the England and Wales Building Regulations. While acknowledging that this is not a design tool, but a method to test regulatory conformance, the results still indicate that there are potentially significant variations in the operational energy use between systems.
For all these cases, the combination of fabric, systems and energy source met the standard – with the selective use of PV ensuring that all the houses with electric panel radiators met the requirement. The all-electric houses that employed ASHPs had the lowest DPER. In the flats, perhaps surprisingly, the installations that included radiant panels were clearly well within the limit set by the TPER. However, it was the flats employing the ambient loop and heat pump solution that achieved the largest modelled reduction in the DPER compared with the TPER.
The smaller properties performed better. For larger homes that have a greater space-heating demand, performance is likely to require improving with increased fabric performance, renewable systems (such as PV) or systems such as waste-water heat recovery. From this sample of modelled dwellings, a hybrid (and/or mixed mode) approach appears to provide a reasonable solution to meet the requirements of SAP – but, as ever, each particular project requires careful consideration.
References:
- bit.ly/CJApr23CPD26 – accessed 28 February 2023.