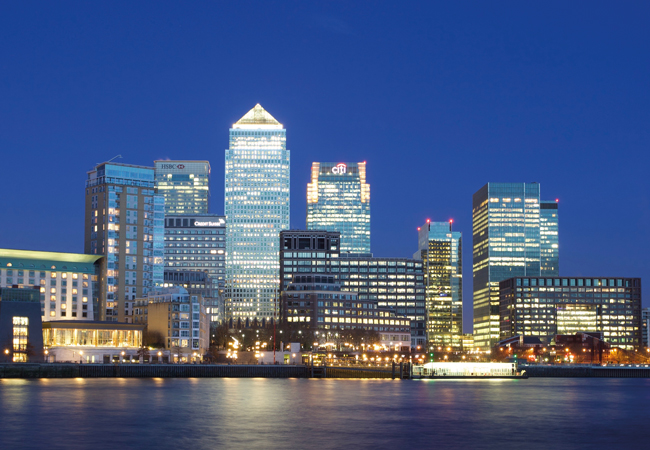
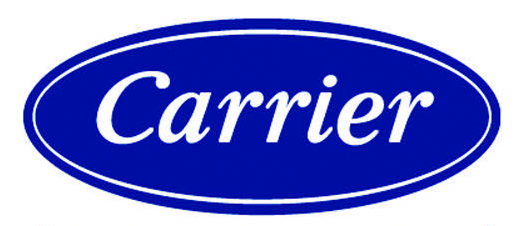
Effective life-cycle asset management, including performance audits and predictive maintenance of building services equipment, can make a significant contribution to decarbonisation efforts. This article will explore a key driver that has helped raise the level of industry expertise in this area, provide some examples of the elements and outcomes of engineering condition surveys, and reflect on the advance of digital technologies as a means of assessing systems’ performance – all as part of a holistic effort to decarbonise built environments.
A significant driver in the development of an increasing body of expertise for building services asset management has been the Energy Savings Opportunity Scheme (ESOS).1 This is a mandatory energy assessment scheme for large UK undertakings that, although having its roots in the European Union (EU), is underpinned by UK legislation and will continue into the foreseeable post-Brexit future.
ESOS aims to identify tailored measures that lead to significant energy savings and carbon reductions, so organisations can choose actions based on their specific context and energy consumption patterns. The current ESOS phase 3 includes companies with more than 250 members of staff, a turnover greater than £44m and an annual balance sheet total of more than £38m.
ESOS assessments are conducted every four years to provide audits of the energy used by buildings, industrial processes and transport within the organisation. The ESOS reporting includes building energy intensity ratios (kWh per square metre) as well as total energy use in kWh or money spent. The rationale is that, while there are costs associated with the audit, the savings from implementing the recommendations typically outweigh the expenses.
ESOS mandates a comprehensive energy audit, which often requires improved data collection on building energy consumption. This might involve activities such as installing metering systems, monitoring equipment performance and analysing usage patterns.
ESOS can highlight maintenance issues impacting energy performance. For example, the audit might reveal the need for replacing faulty equipment, cleaning ventilation systems or fixing leaks in fluid distribution systems. ESOS compliance encourages a preventative maintenance approach that can identify potential problems before they escalate and lead to increased energy use. This proactive approach extends the lifespan of equipment and contributes to long-term energy savings.
ESOS can highlight the need for training building staff on energy-efficient practices. This might involve educating them on proper equipment operation, occupant behaviour that impacts energy use and procedures for reporting maintenance issues.
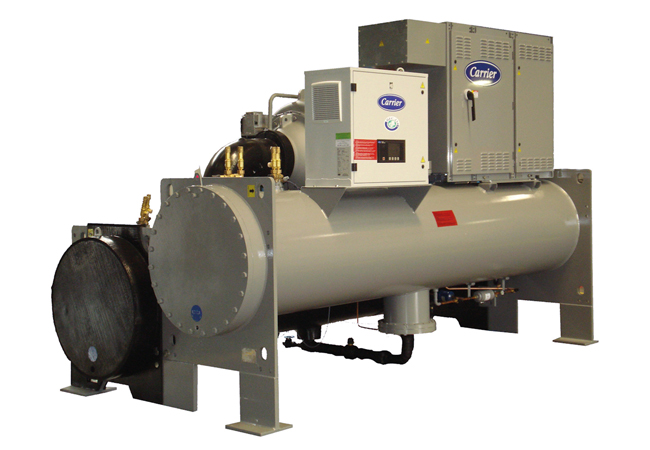
Developing and implementing a carbon reduction plan (CRP) is a central requirement for organisations complying with ESOS, in order to provide a roadmap for reducing their carbon footprint. By requiring organisations to assess their energy consumption, ESOS acts as a catalyst for cost-effective measures that improve building operation and maintenance practices.
The near future of ESOS looks to be focused on strengthening its impact on energy efficiency and aligning with the UK’s net zero targets. Phase 4 of ESOS – with a compliance period of 6 December 2023 to 5 December 2027 – will probably require assessments to consider not just energy savings, but also actions needed to achieve net zero emissions.
This might involve assessing the feasibility of renewable energy adoption or energy efficiency upgrades that contribute to carbon neutrality, while also identifying potential risks of moving towards net zero. ESOS 4 may introduce support to identify potential risks of moving to net zero alongside assistance in creating CRPs. Notably, the use of display energy certificates (DEC) and Green Deal Assessments will be removed as a route to ESOS compliance.
The UK government is considering mandating that organisations act on the recommendations identified in ESOS audits to ensure implementation, leading to genuine impact. Future requirements may demand that a greater range of ESOS data and results of subsequent actions are made publicly available, which could incentivise companies to take strong action for reputational reasons. Speculation suggests that there may be an alignment of ESOS with the Streamlined Energy and Carbon Reporting (SECR) scheme.2 This could potentially bring smaller businesses under the ESOS umbrella. ESOS 4 is likely to see a further emphasis on data collection and analysis, as data-driven insights and automated controls can further optimise energy use and streamline the compliance process. This could include elements such as:
- Automated data collection and analysis
- Machine learning for optimising energy use within buildings
- Digital twin simulations for testing and evaluating energy-saving strategies.
Previously, there has not been a mandated auditing methodology; however, it is likely that BS ISO 500023 and BS EN 16247-24 energy audits – which set out a good-practice method for identifying energy savings opportunities – will be listed as the preferred route to reporting in ESOS 4.
Data-driven insight and digitally enabled automated systems are pervasive in the recent rewrites to CIBSE Guide M Maintenance engineering and management. This demonstrates the accelerating ubiquity of digital systems as the means of delivering effective intelligence on the operational state of building systems. Digitally sourced intelligence can combine with feedback from the building operator and performance management meetings to inform continuous improvement.
Deployment of digital technologies provides unprecedented opportunity for interaction with ‘smart’ sensors, building controls, maintenance history and predictive technology to measure and optimise performance. Automated reports or cloud-based dashboards are increasingly common as a means of monitoring systems that can be benchmarked against commissioning (and recommissioning) data to quantify performance and swiftly identify problems. This can provide the data for condition-based maintenance (CBM) that – unlike traditional planned preventative maintenance (PPM) – is not based on specific time intervals, but on regular, or continuous, monitoring of system performance to indicate any deterioration that may signal the need for recommissioning, maintenance, refurbishment and replacement procedures.
Chiller modernisation in 20-year-old skyscraper
The owners and operators of a ‘glass and steel’ 32-storey skyscraper office building, located in east London’s Canary Wharf, sought advice on the efficacy of their current chilled-water generation systems as part of their carbon-reduction aspirations. The building, originally completed in 2003, was among the first in Canary Wharf to receive an ‘Excellent’ Breeam rating. As part of the initial construction project, six centrifugal chillers were installed with nominal cooling capacities from 1,000kW to 5,300kW.
In 2020, the building systems were assessed with a view to reducing the building’s carbon footprint. The chillers already operated with a respectable seasonal energy efficiency ratio (SEER) of 6.8 and acceptable noise levels. The service modernisation team for the chiller manufacturer analysed potential energy-saving measures, return on investment (ROI) and performance forecasts, to provide a clear understanding of the benefits of any proposed refurbishment or upgrade activity.
The team determined chiller performance could be improved with intelligent condenser water control, installing variable frequency drives (VFDs) and undertaking a full compressor refurbishment on the six chillers. This was aimed at not only improving energy efficiency, but also extending chiller lifespan. The installation of VFDs on each chiller allowed adjustment of compressor speed to match the cooling demand, leading to significant energy savings, particularly during periods of low demand, as well as improving conditions for the occupants.
The project was completed in phases during 2023 to ensure uninterrupted tenant operation improved.
The modernisation has boosted efficiency and performance, with typical energy savings resulting from the VFD upgrades estimated at 20%. The VFDs also reduce mechanical stress on the chillers’ components, and it is thought that this adds a minimum of 10 additional years’ service life, ultimately delivering significant ROI.
CBM can be employed to ensure resource utilisation is optimised, and prevent unnecessarily premature and inappropriate interventions. CBM may be undertaken completely onsite through, for example, the building management system (BMS), or facilitated remotely. Remote monitoring access may be as simple as an internet connection to the BMS, or it might employ continuously connected systems operated by the equipment manufacturer or the provider of maintenance support. Such services are increasingly being offered by equipment manufacturers using cloud-based, internet-connected systems that reference historical and contemporary data from the specific site, as well as the wider user base.
By employing techniques such as machine learning in conjunction with expert product knowledge, manufacturers can offer predictive performance assessment, preventative maintenance planning, and optimised refurbishment and replacement scheduling. The current challenge for the whole built environment industry is to federate this data, and to provide standardised secure, shared access to the streams of data that may usher in increasingly ‘intelligent’ buildings and cities.
Section M13 of the recently rewritten CIBSE Guide M describes the engineering condition survey (ECS) as being a process of systematically assessing the condition of assets in respect of their ability to perform their intended function. Traditionally, a manual (paper) approach has been used to collect data, and this remains an option for many small to medium installations by employing pro forma data-collection sheets.
However, this is typically being superseded by electronic data collection, through accessing BMS, service provider, and manufacturer-based systems and field records. Such surveys may be part of the regular management of assets, in support of the ESOS requirements, or they may be required to identify the extent of maintenance liabilities prior to taking on a property, or to inform a maintenance contract.
The ECS can provide an indication of the expected life of assets and components, which can be used to forecast the asset renewal demands and costs. Facility operators may vary the inspection cycle to suit the maintenance regime and assessment of risk to health and safety, operation and potential for failure.
Non-intrusive ‘visual’ inspection of the plant and associated systems and controlled spaces can provide an impression of the asset operation and wellbeing. However, this can inadvertently overlook unseen operational issues, as impending failure is not always visible. Valuable information can be obtained through conversations with maintenance staff and building users, as well as by reviewing logbooks, servicing reports and certification to help inform the overall view of condition.
While cost may prohibit frequent in-depth surveys, an annual visual inspection supplemented by a more thorough survey every three years might be considered as a reasonable compromise. A thorough survey should include examining maintenance reports for major plant items, and may require the attendance of specialists to provide further insight into the condition of assets.
Non-intrusive surveys can uncover failures that would not be picked up during a visual survey – CIBSE Guide M provides an extensive commentary on different non-intrusive techniques.
It is important that the assets surveyed are uniquely identifiable, with their type and location reliably recorded. A classification system for the major elements of the engineering services will need to be agreed at the outset of the survey. For example, this may employ a classification system from the Royal Institution of Chartered Surveyors’ (RICS) New Rules of Measurement,5 or systems such as Uniclass6 may be appropriate if, for example, asset data is already held in a building information model (BIM). Guide M suggests that categories may be applied to a survey report to help identify priorities for attention, ranging from priority 1 (urgent) to priority 4 (normal maintenance).
Much of the gathered information may be subjective, but is still necessary to give a ‘priority grading’ that allows the planner to prioritise the work to be carried out and model future budgets. Condition grades can provide an approach for recording the assessed condition of the assets to ensure a consistent interpretation by both the engineering surveyor and the recipient of the results. Guide M proposes a four-point condition scale, from A (fully operational) to D (very poor condition), with an extra designation of X if it is beyond repair.
The scope of an ECS will vary according to the requirements of the building and application. However, CIBSE Guide M considers that a typical survey report is likely to include detail on:
- Functional suitability of assets and components
- Operational integrity
- Physical condition
- Compliance with legal and health and safety requirements
- Conditions affecting operation and maintenance
- Economic life and obsolescence
- Energy efficiency of assets.
The format of the report will be determined by the client’s requirements, and include a summary for each asset identifying the maintenance and remedial requirements, their costs, and the timescale to undertake work. Spreadsheets may be used to illustrate expected maintenance and replacement costs based on predicted values (such as those illustrated in BSRIA guide BG 35/20127).
This will then provide accessible and useful information enabling a client to set – with a reasonable level of confidence – priority objectives, and plan both short- and long-term maintenance and replacement needs. A comparable process was recently employed in the assessment and refurbishment of the chilled-water installation for a 20-year-old, 32-storey skyscraper office building in London’s Canary Wharf (see boxout).
The management of building services systems as a means of delivering safe, comfortable, effective built environments with reduced carbon footprints, is a truly holistic task. Starting with the original – or refit – design, through the appropriate selection and installation of systems (and their all-important controls) to eventual refurbishment and reuse, the effort to decarbonise will have the greatest opportunity to succeed only if the aspects discussed in this article are considered as part of the more extensive system that reaches far beyond the building façades.
References:
- bit.ly/CJJun24CPD21 – accessed 2 May 2024.
- Streamlined Energy and Carbon Reporting (SECR) scheme.
- BS ISO 50002:2013 Energy audits, BSI 2013.
- BS EN 16247-2:2022 Energy audits – Buildings, BSI 2022.
- bit.ly/CJJun24CPD22 – accessed 2 May 2024.
- Uniclass – uniclass.thenbs.com/ – accessed 2 May 2024.
- Bell, R and Harris, J, BSRIA BG 35/2012 – Condition Surveys and Asset Data Capture, BSRIA 2012.