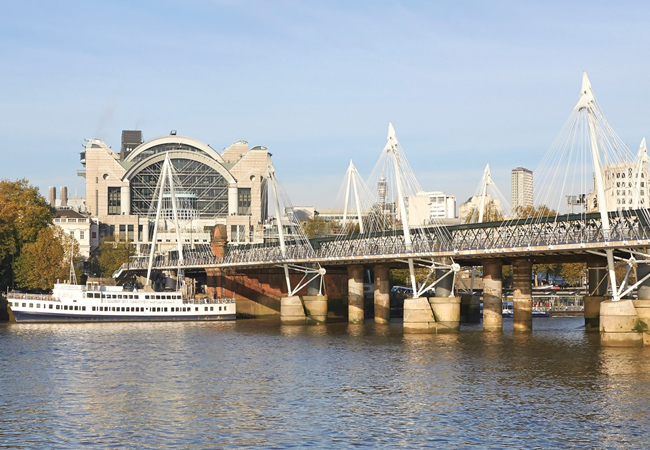
One Embankment Place is among London’s most prominent examples of post-modern architecture. The 11-storey office building, by architect Terry Farrell, has been sitting above Charing Cross station since 1990, and is now an established part of the cityscape.
In 2010, as the building approached its 20th year, the occupiers – accountancy firm PricewaterhouseCoopers (PwC) – decided on a major refurbishment. While the aluminium and granite façade had stood the test of time, the interior was in need of updating. Deep floor plates meant offices were deprived of daylight, for example, and the dark atrium created an unwelcoming entrance. The building compared unfavourably with PwC’s new light-filled offices at More London, near Tower Bridge.
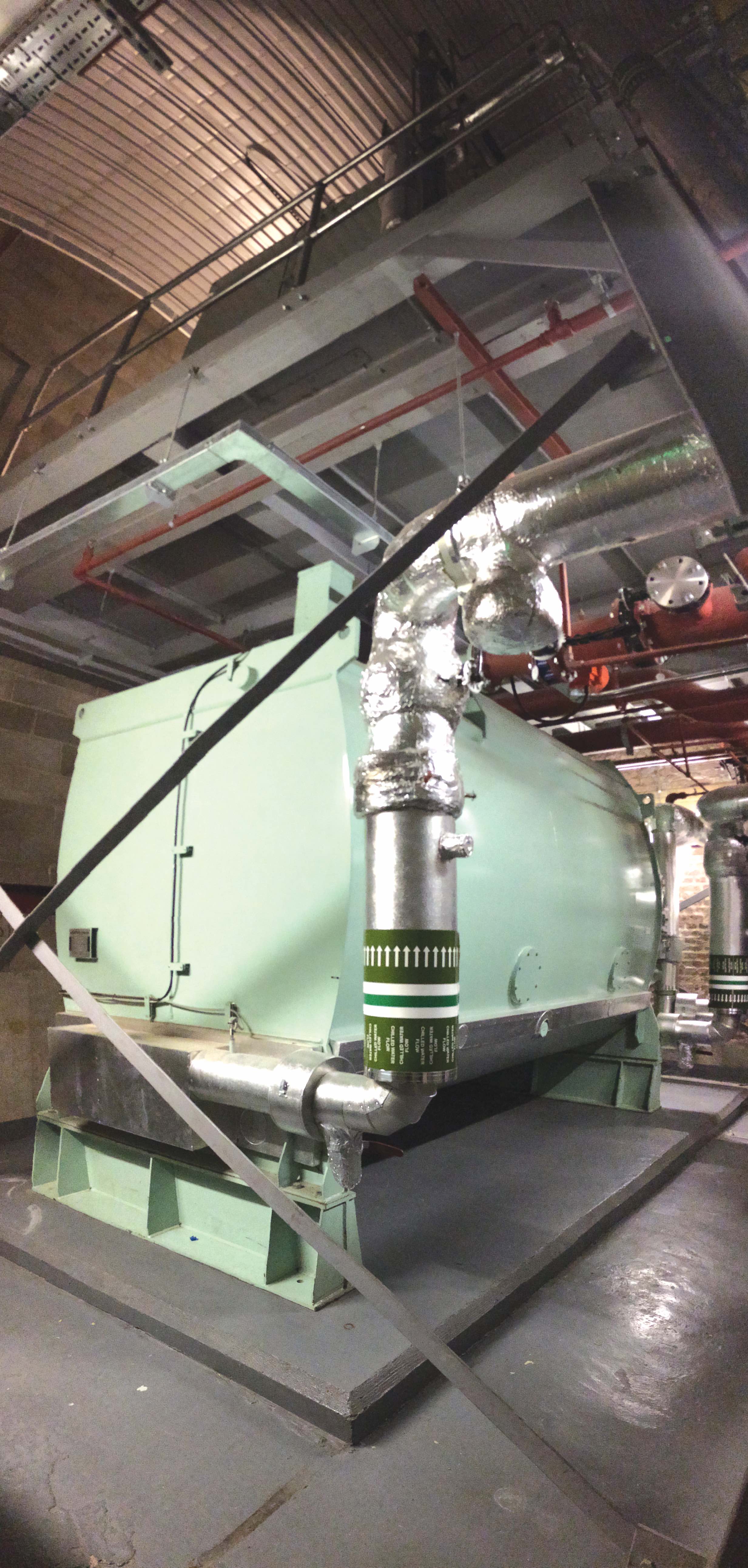
Adsorption chillers stacked within a vault
A team – including project manager Turner & Townsend, architect TP Bennett and building services engineer ChapmanBDSP – was tasked with breathing new life into One Embankment Place. Prime among the design objectives was improving the building’s environmental performance and achieving the highest possible Energy Performance Certificate (EPC) and Breeam ratings. Initial investigations revealed that an EPC B rating and Breeam Excellent could be achieved by implementing energy efficiency measures. However, to attain the highest ratings, the team calculated that a significant amount of renewable energy generation would be required.
Numerous scenarios were analysed, including recladding the barrel-vaulted roof with photovoltaics, installing wind turbines on the turrets, and using biofuel as the main energy source. PwC had recent experience of the latter; it had pioneered the use of biofuel within a combined heat, power and cooling plant (CHPC) – or trigeneration plant – at its More London office, and decided to use the same source of fuel for One Embankment Place.
The biofuel used by PwC could not be more locally sourced; used cooking oil (UCO) from London restaurants is refined in railway arches in Southwark. The use of UCO has been innovative, but not without teething problems. It is more corrosive than other fuels and PwC’s building operators have had to work closely with engineers to ensure that the performance of the CHPC is not compromised by the fuel’s properties.
Other issues associated with More London were low loads and high exhaust temperatures from the absorption chillers. The team at One Embankment Place was able to learn lessons from this and improve the efficiency of the plant. The biggest change was the move from an absorption chiller to adsorption chiller, which the team calculated could save £240,000 in maintenance and replacement costs. (See panel, ‘Chiller life-cycle assessment’).
Project team
- Project manager: Turner & Townsend
- Architect: TP Bennett
- MEP and sustainability consultant: ChapmanBDSP
Originally, the plan was for the base build installation to run on virgin-crop biofuel – unused oil directly from crop that would usually be intended for use in the food chain – but, according to Jon Barnes, head of building and technical services at PwC, this was not sustainable enough: ‘Taking crop from the food chain is something PwC would not do.’
With a view to finding a sustainable source of biofuel, PwC approached Uptown Oil, which – as well as supplying new cooking oil to the company – recovers waste oil from the kitchens of its central London offices.
At the time, Uptown Oil was refining waste oil into fuel not far from PwC’s proposed new office near Tower Bridge. Its proximity was attractive; biofuel delivered from further afield would have incurred a heavy carbon cost in terms of transporting it from a collection site, via a remote refinery. ‘We were pioneering in what we were doing,’ says Barnes. ‘At the time, there was virtually no knowledge on UCO in HVAC systems – but, despite this, PwC opened its 7 More London office with a trigeneration system powered by UCO.’
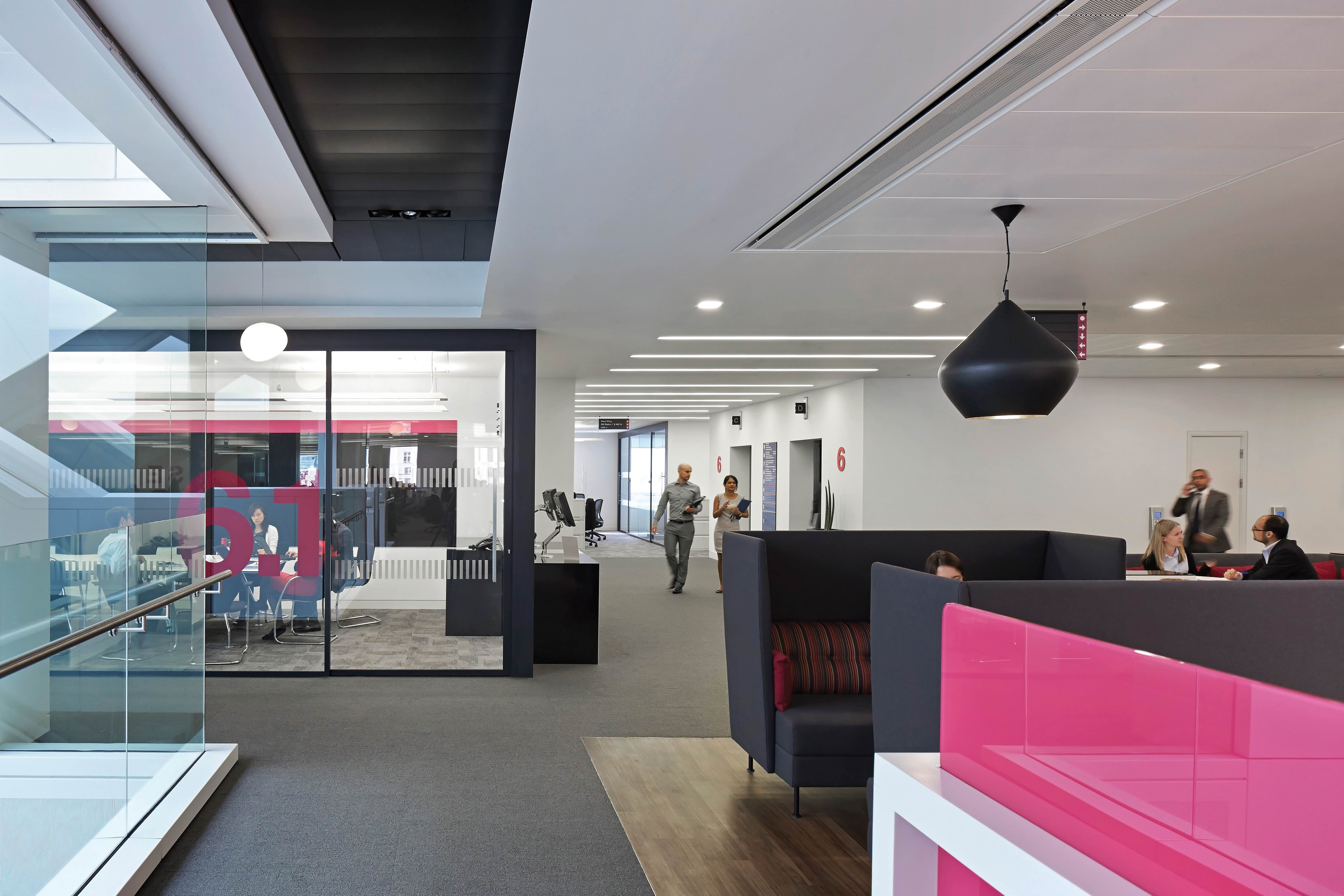
UCO had been used at More London for just a few months when One Embankment Place also investigated employing the fuel source. This meant there was an opportunity to learn from the earlier installation and the issues it encountered. Injector and fuel-pump failures – and high exhaust temperatures caused, partly, by variable fuel quality – were the main challenges of using UCO. The generators at More London soon began to suffer from its corrosive effects, made worse by biofuel remaining in the fuel lines and engine components overnight.
‘The biofuel is actually very aggressive. If left in contact, it will eat through rubber seals in no time,’ says Mick Hunt, building engineer at PwC.
So the project team at One Embankment Place enabled the generators to be started and stopped on red diesel. This facilitated a much easier start-up and flushed the engine fuel lines, fuel pump and injectors, to ensure the corrosive biofuel was not shortening the life of these components while standing idle.
This improvement resulted in the loss of the Breeam innovation credit for the system, because there was concern that it could be run on red diesel at any time. During actual operation, this has not been the case; PwC’s fuel-consumption figures at One Embankment Place reveal that only 3,000 litres of red diesel is used in a year, compared to the 4,000 litres of biofuel used every day.
Chiller life-cycle assessment
Lifespan, cost and maintenance were factored into a life-cycle assessment of the intended life of the fit-out. The adsorption chillers – at more than double the cost of absorption chillers – could be demonstrated to have potential savings in maintenance and replacement costs of more than £240,000. This excluded the potentially reduced downtime and better turndown ratio allowing more heat energy to be used from the generators at part-load. This reduced the overall installation and maintenance cost over a 15-year period from an estimated 2p/kWhc to 1.3p/kWhc.
Experience at More London showed that biofuel degrades quickly, so smaller tanks were installed to ensure that turnover was high and storage periods minimised.
The team spoke with generator and engine manufacturers to determine the best systems to operate with the proposed fuel. Suppliers with older engine technology demonstrated how lower injector and pump pressures were able to cope with the alternative fuel.
There was a clear need to improve the consistency and quality of the UCO and – with the engine manufacturer pressing for it to achieve EN14214 standard – a sample of the fuel from More London was sent away for testing. A number of issues were found, including high moisture and methanol content.
A Knowledge Transfer Partnership study with London South Bank University followed. Working with Uptown Oil, the fuel-refining process was improved to pass the independent testing to EN14214 and to achieve a high level of consistency in fuel quality. This was completed before the new trigeneration facility at One Embankment Place went on line.
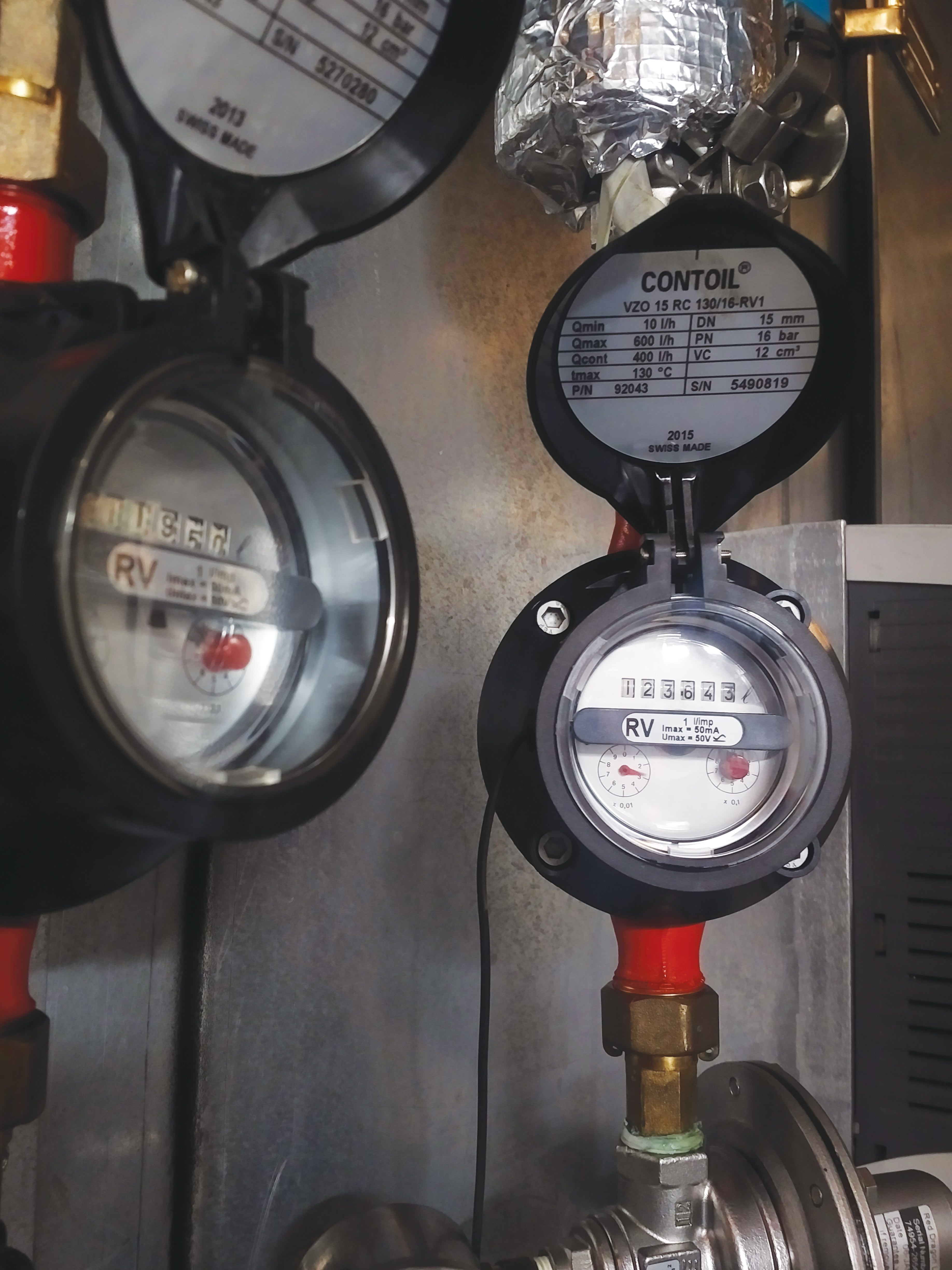
Red diesel and biofuel meters
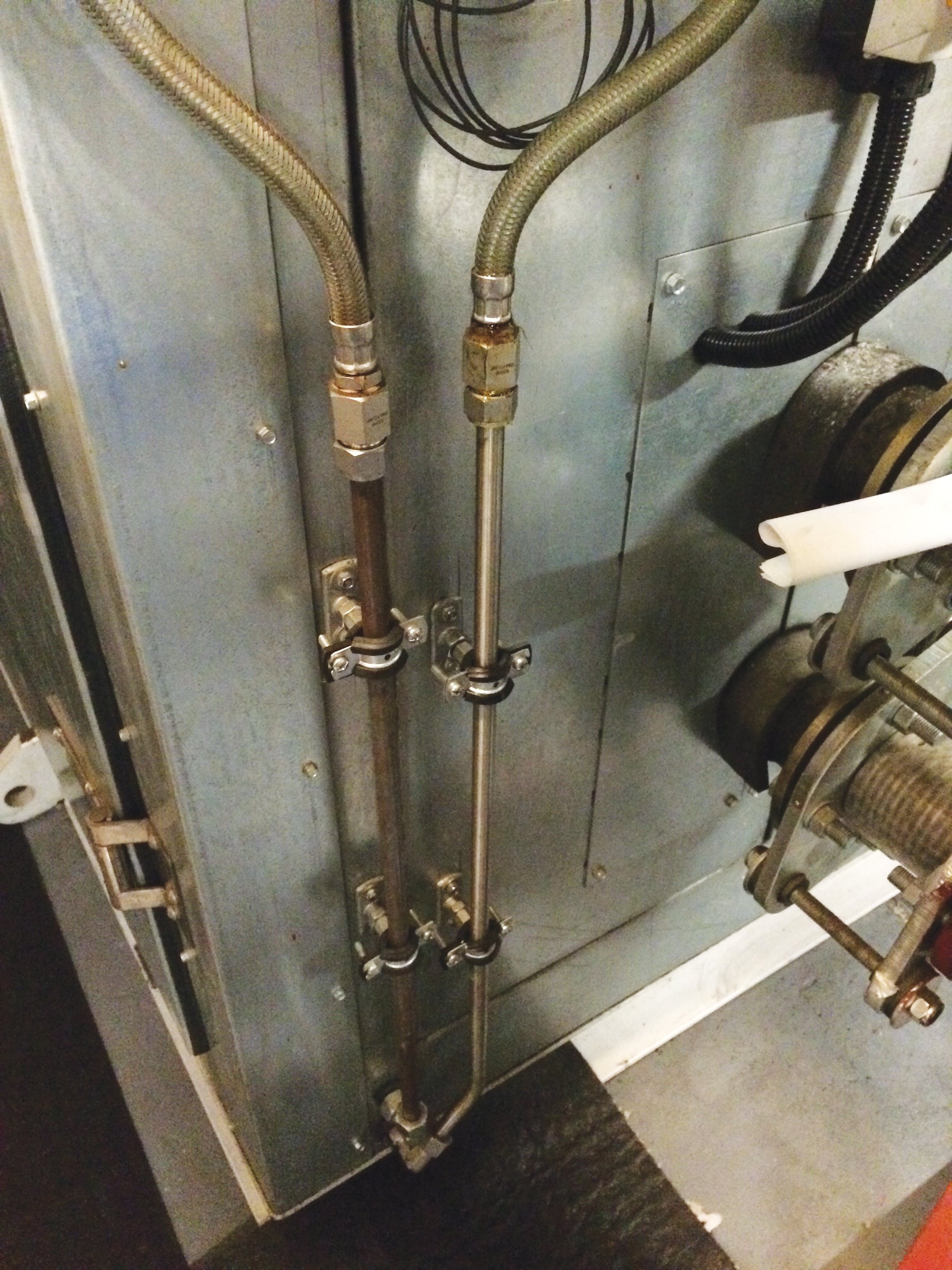
Stainless steel pipework is used for biofuel
The fuel is checked for EN compliance every three months, with each batch tested for ethanol content, which causes the most issues for the system.
The fuel deliveries being achieved are consistent and of EN quality, but it remains a very aggressive substance to store and use. Fuel-pump seals and injector failures are still common, with fuel pumps replaced regularly at More London and One Embankment Place.
Daily inspections are carried out, with the emphasis on looking for leaks caused by the failure of seals on the fuel-delivery systems. PwC has installed leak detection, with alarms affording early alerts. This allows quick shutdown and minimises the cleanup required to enable parts to be replaced and the plant put back in service.
Choice of chiller
Reliability and overall life-cycle of the plant were key considerations for PwC. A study was undertaken to compare the use of silica gel and water chillers – known as adsorption chillers, and manufactured by Weatherite – against absorption chillers using lithium bromide (see panel, ‘Chiller life-cycle assessment’).
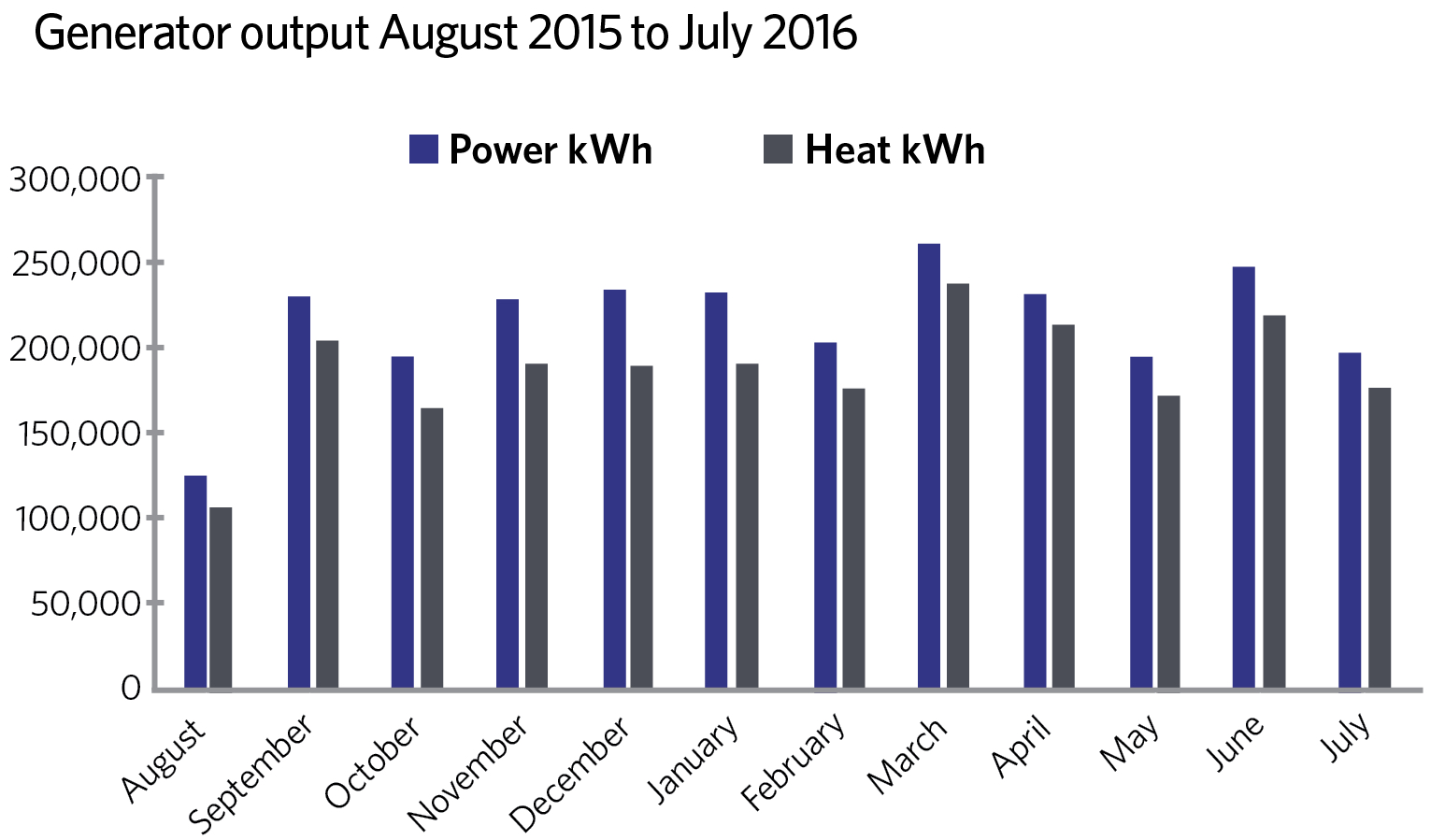
In 12 months to July 2016 , 2,565MWh of electricity and 2,227MWh of heat was generated
The study concluded that adsorption chillers offered a much lower installation and maintenance cost over a 15-year period, and these were specified for One Embankment Place.
Three years on, the silica-gel chillers have performed almost flawlessly – the replacement of an air compressor for the pneumatic controls on one of the chillers has been the only failure.
Maintaining water temperature from the generators to the chillers has been a challenge, with the exhaust heat exchangers seemingly less than ideal in terms of size. This has resulted in insufficient heat being extracted to maintain the required 82°C for full output of the chillers. The silica gel chillers are more controllable across a wider operating range compared to lithium bromide absorption chillers and so the output can be modulated more accurately to meet demand than with lithium bromide absorption technology.
Biofuels burn less cleanly than diesel resulting in fouling of the heat exchangers, reducing their performance and so exacerbating the lack of heat transfer to the water. So the heat exchangers are cleaned on a three-monthly cycle, after which the improved heat transfer can increase LTHW flow temperatures by up to 10K.
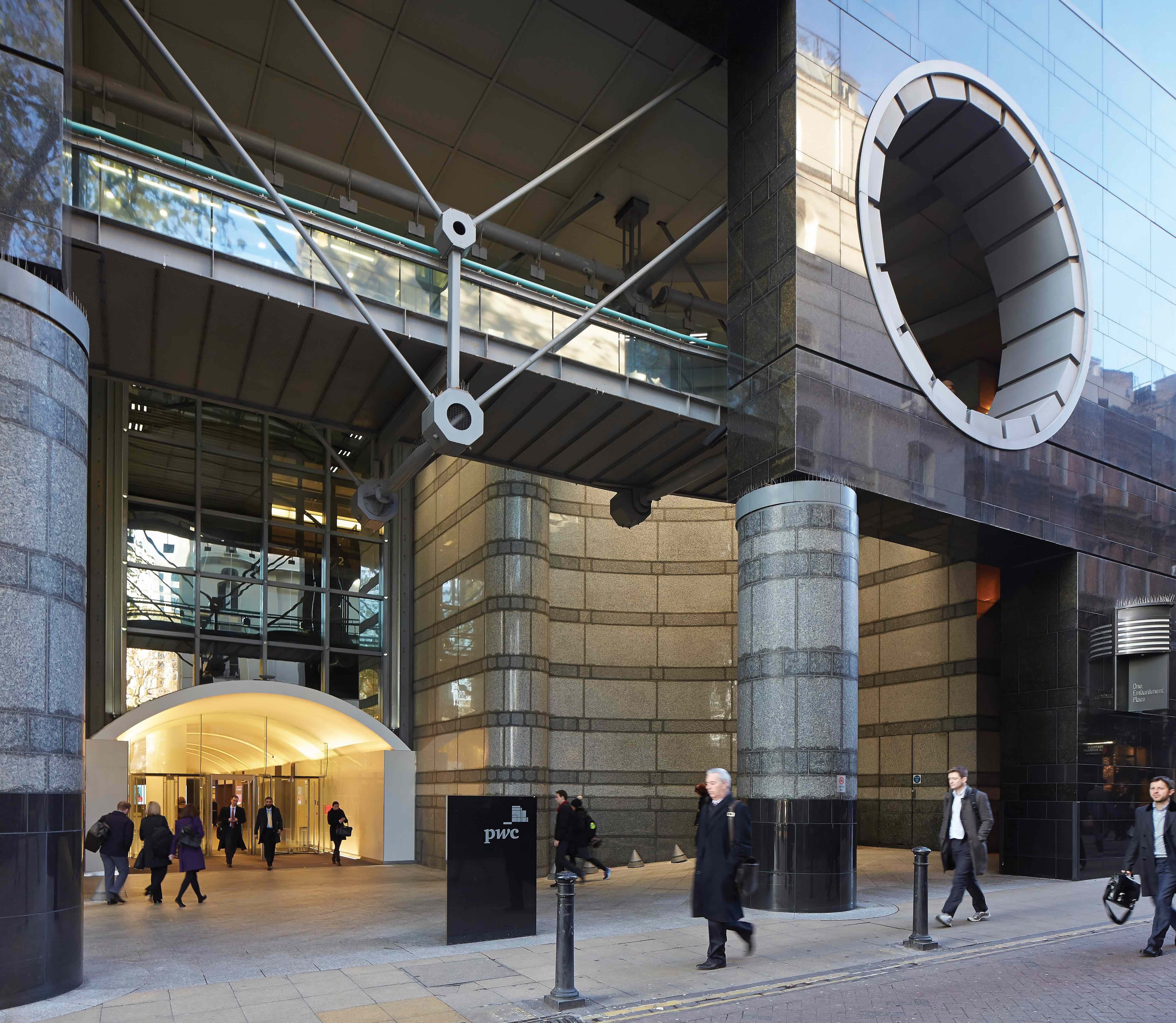
At More London, the trigeneration plant is connected on the power side to the tenant’s small power and lighting load. This means the plant has limited operating hours outside times of peak occupancy because of the low electrical loads for the office floors when unoccupied. To maximise run hours at One Embankment Place, connection was prioritised so that whole-building loads, including landlord plant and common parts, could be served.
The More London absorption chillers operate in two stages, from the engine jacket water and from the hot exhaust gasses passing through the chillers. High exhaust temperatures frequently resulted in crystallisation of the solution within the absorption chillers, causing reduced output and, ultimately, the shutdown of the system.
To better control the heat entering the cooling-generation system, it was decided that water-based chillers – rather than exhaust-gas versions – would be used at One Embankment Place. This would result in a potential reduction in the chillers’ coefficient of performance (COP) – so they would be less efficient – but improved reliability compensated for this.
One Embankment Place has very deep floors and a high floor area to external envelope. This, along with the associated internal gains, means the building needs cooling all year round.
The output of the chilled water systems, while metered, has not been recorded. In this cooling-led building, the facilities management (FM) team, led by Hunt, reports that its cooling load can be met during winter by the CCHP system alone.
The only time when the CCHP system is reduced in operating hours is during periods of very hot weather. The condenser water circuit is shared with the main chillers.
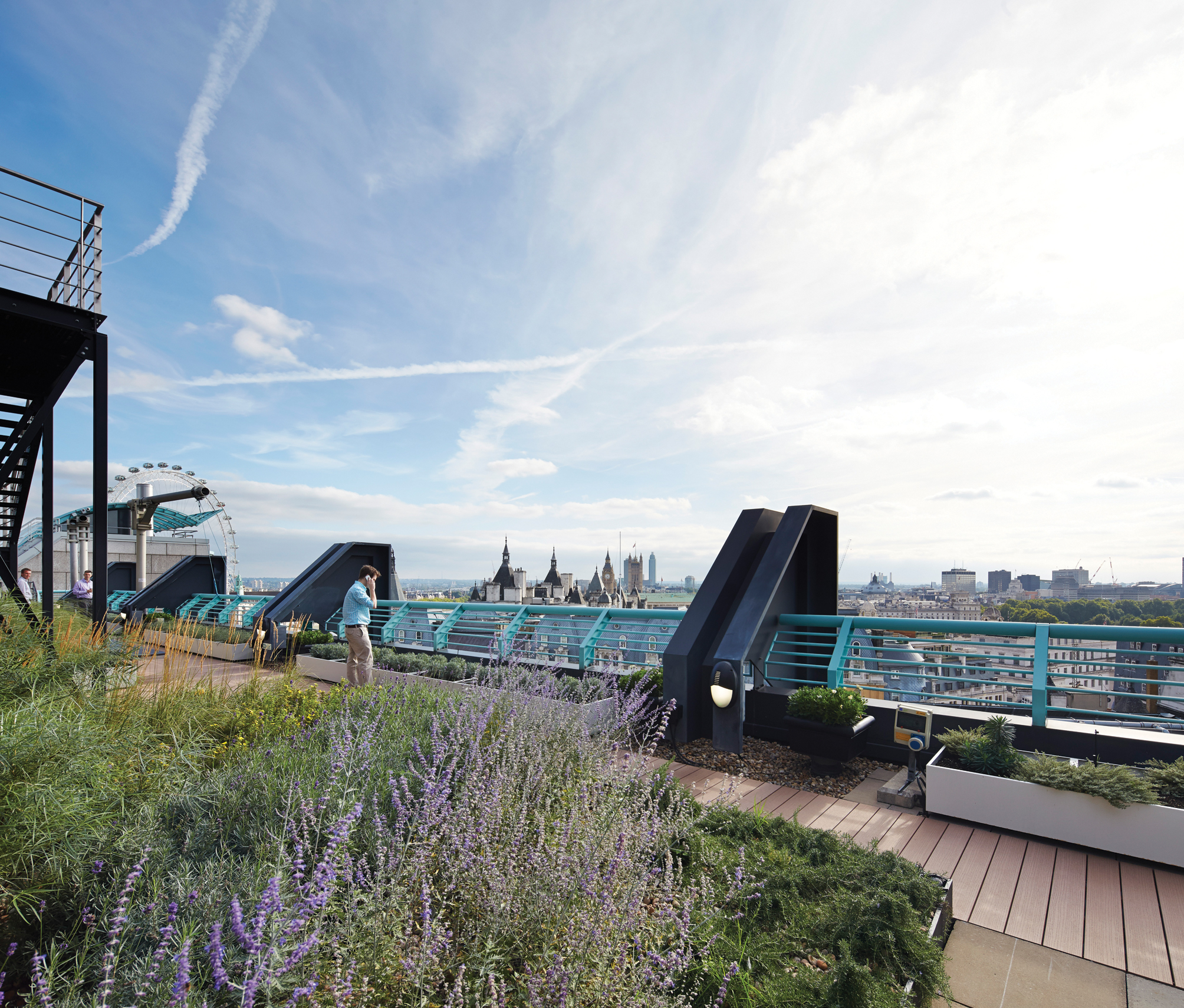
During periods of very high cooling loads and high ambient temperature and humidity, the electric chillers are prioritised to ensure the full cooling load of the building is met. This is uncommon, and is monitored and implemented manually when the condenser water temperatures rise.
In the 12 months to the end of July 2016, the system generated 2,565MWh of electricity and 2,227MWh of heat, with output reasonably consistent, despite regular maintenance being undertaken.
Each generator has a red diesel and a biofuel meter at the fuel inlets to the enclosure, which allows the use of each fuel to be assigned to a particular generator. While the generators have the ability to start and stop on red diesel, this accounted for only 0.66% of the total fuel used in 2015.
Conclusion
Scalability and adaptability of UCO for application to other buildings is low. There is insufficient waste oil available for many more buildings to use this type of technology and its application may be better suited to waste-processing plants outside of London.
In terms of installation and maintenance, this was far from easy, fit-and-forget technology. It has taken considerable dedication to install and maintain a system that works well on a daily basis.
Installing the plant
One Embankment Place was the largest air-rights building in the UK at the time of its construction over Charing Cross station. This means its main entrance and the plant are located in the vaults below the station – giving the designers the logistical complication of moving gas, heat, power, cooling and people up through the station level to the main function areas of the building above.
Two vaults below the station were identified for the trigeneration installation, and then began the space planning for fitting in the generators, exhaust systems, ventilation systems and – by far the largest items – the two adsorption chillers.
The resulting arrangement had the two generators located side by side in one acoustic enclosure, with a central walkway between the engines and the two adsorption chillers stacked within the vault.
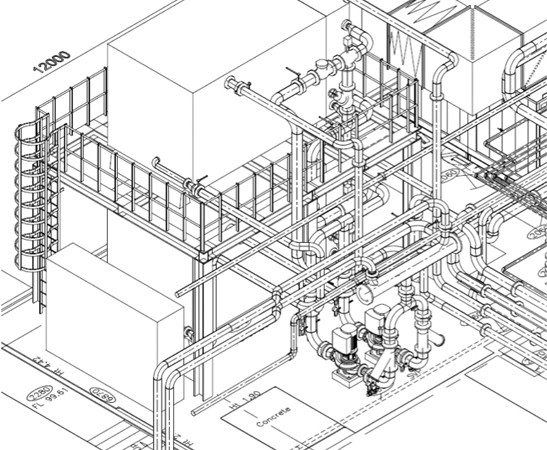
The adsorption chiller arrangement within a vault below Charing Cross station
What this installation proves is that, with effort and intelligent engineering, it is possible to deliver what might have been considered a risky venture.
The benefits to the environment should not be underestimated – PwC is now using around a seventh of London’s waste cooking oil. A considerable achievement.
- Special thanks
The following assisted in the writing of this article: ChapmanBDSP; Jon Barnes, PwC; Steve Smith, PwC; Mike Hunt, PwC; Adam Bushell, PwC; Ross Cruikshank, Honeywell Building Solutions; Mike Trkulja, Honeywell Building Solutions - Darren Coppins MCIBSE is an independent mechanical engineer and environmental design consultant. For this project he was acting head of sustainability for Chapman Bathurst (now ChapmanBDSP)