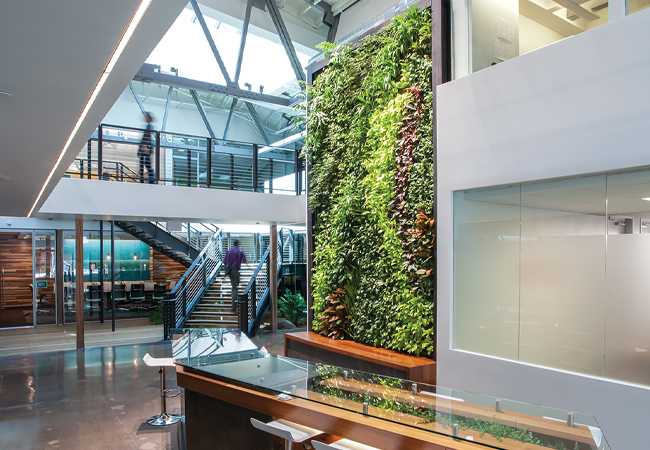
Improving the environmental impacts of the built environment has become a priority given our climate crisis. Greenhouse gas emissions responsible for global warming – measured in carbon dioxide-equivalent emissions – need to be reduced drastically.
The industry has long focused on operational carbon, but has ignored emissions related to the rest of the life-cycle stages of buildings. To make well-informed decisions that will mitigate global warming, engineers, architects and clients need to embrace whole-life carbon emissions.
This term refers to both operational and embodied carbon emissions, from manufacturing, transportation, and constructing, repairing and maintaining a building, through to deconstructing the building and processing waste. This can be quantified through life-cycle assessments.
In the case of building services, engineers have long been considering the operational carbon through the impacts of wider mechanical, electrical and plumbing (MEP) strategies – such as encouraging natural ventilation and free cooling over active cooling – and specifying highly efficient plant.
Recently, there has been a drive to shift the generation of heat to electricity, through the use of heat pumps, rather than gas. This, along with fabric efficiency improvements – which reduce the heating load in the development – and the increasing decarbonisation of the electricity grid have led to reductions in the operational carbon of developments. However, the whole-life carbon impacts of MEP do not end with operational carbon.
Engineers need to understand the embodied carbon emissions of the systems they design and the products they specify, so that informed choices can be made using ‘whole life’ thinking.
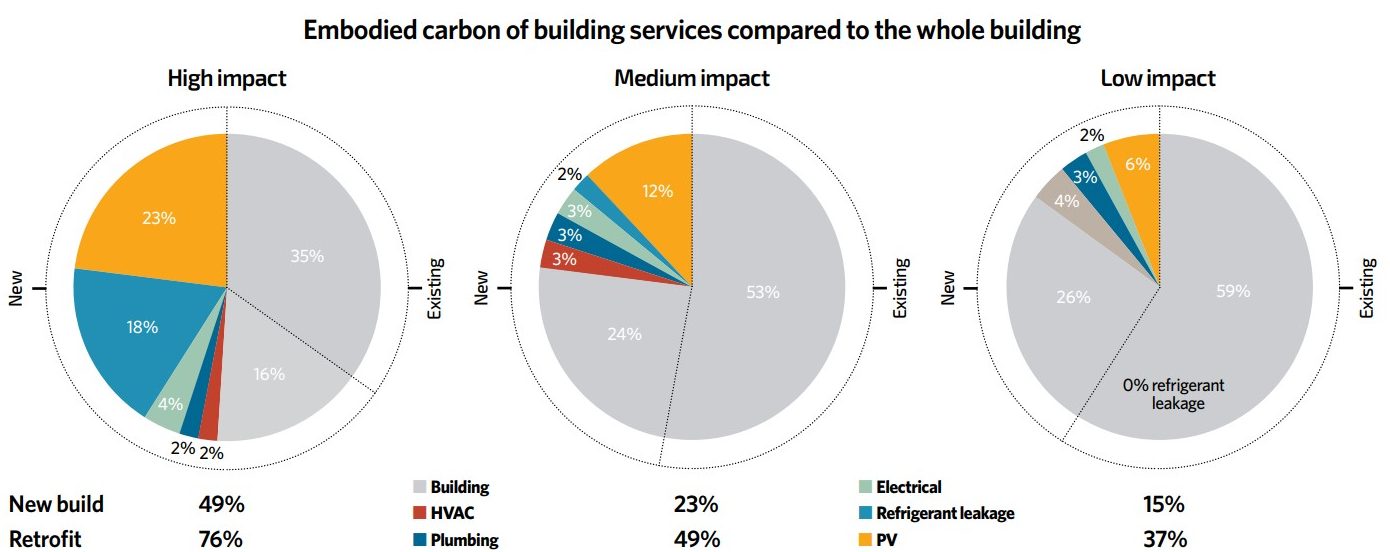
Figure 1: The high impact scenario refrigerant leakage accounts for a large proportion of embodied carbon
Whole-life carbon study
Globally, there is limited data and information on the embodied carbon emissions of MEP equipment. Elementa Consulting – a member of engineering and consulting firm Integral Group – has completed a research study with the aim of starting to understand the whole-life carbon of electrical, plumbing and HVAC systems compared with the whole-building emissions, and the variance of embodied carbon of MEP products, through a detailed analysis of an office retrofit.
The intention was to develop knowledge of how MEP engineers can prioritise action on embodied carbon and to inform further research streams.
The study was based on an office refurbishment in the USA – the headquarters of DPR Construction in San Francisco, California (see ‘Winning formula’, CIBSE Journal, August 2017).
Operational carbon emissions were calculated based on in-use consumption. Embodied carbon for all elements apart from building services were calculated in Tally life-cycle assessment oftware, and the MEP elements were calculated using the following method:
All building services elements were included, from cables and light switches to variable refrigerant flow (VRF) systems. The material quantities were taken from a detailed BIM model using a Dynamo script and cross-referenced with schematics and plans.
One Click LCA life-cycle assessment software was used to estimate embodied carbon of the MEP products (in kgCO2e per product); where information was missing, data gathered from previous studies was used. The ‘Life Cycle Carbon Global’ tool was used within One Click LCA, as this provided the most available data using a consistent methodology for assessing carbon emissions.
Assumptions about replacement rate, wastage and transport came from One Click LCA’s data.
Generic data from product on the database and specific data were used – through the use of environmental product declarations (EPDs) – with the intention of maximising our dataset.
Low, medium and high embodied carbon scenarios for building services were created.
The DPR office case study is a retrofit, so to understand the full carbon emissions associated with the original building, the embodied carbon of the existing building was also included in the assessment. These are shown as separate values in Figure 1.
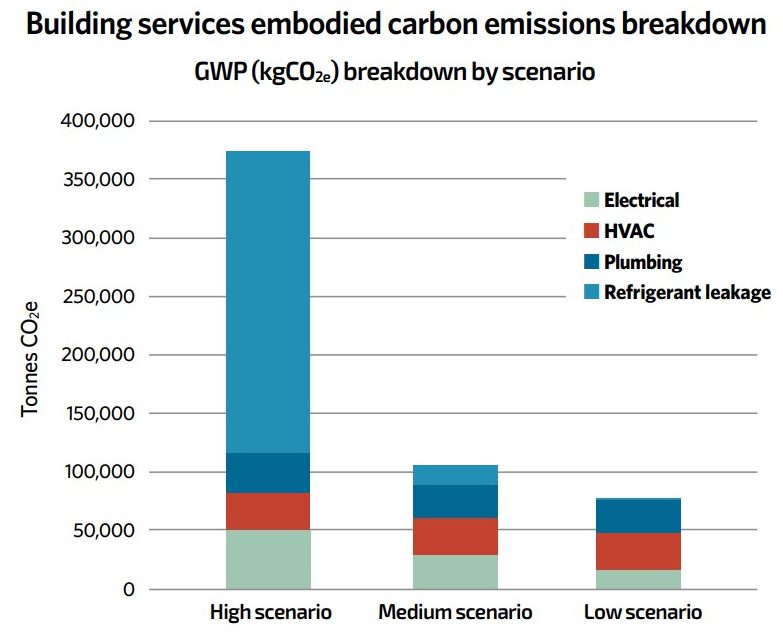
Figure 2: Electrical, HVAC and plumbing have broadly similar embodied carbon emissions
Information challenge
The method above seeks to compensate for the lack of information on building services products. It does this by using all available global data and applying certain factors so that it represents products used in the site location – in this case, San Francisco. Ideally, more data on environmental impacts of MEP products would be available.
There is very little generic data or specific data (such as EPDs) for MEP products. This may be because of a lack of incentives; aside from Breeam 2018 – where it only accounts for one credit – few certification schemes mandate embodied carbon calculations of building services equipment.
Often, when manufacturers are asked about environmental product declarations, they either do not understand what they are or just do not have the suitable information. Another hurdle is the lack of consistency across EPD methodologies because of different product category rules (PCRs) and life-cycle impact assessment methodologies.
The findings
Building services represent a significant proportion of embodied carbon. In the case of a refurbishment or retrofit, building services accounts for 40-70% of embodied carbon emissions. In the case of a new build, building services account for 15-50%, depending on the impact scenario. This confirms that engineers need to engage with embodied carbon, and that there is a need for rule-of-thumb guidance.
Embodied carbon due to the installation of photovoltaics (PV) is included in the percentage figures quoted above, but is required to offset the operational emissions (see Figure 1).
In the high-impact scenario, refrigerant leakage accounts for a large proportion of embodied carbon. This scenario assumes a 10% annual leakage rate and a refrigerant with a global warming potential (GWP) of 2,088 (for example, R410a).
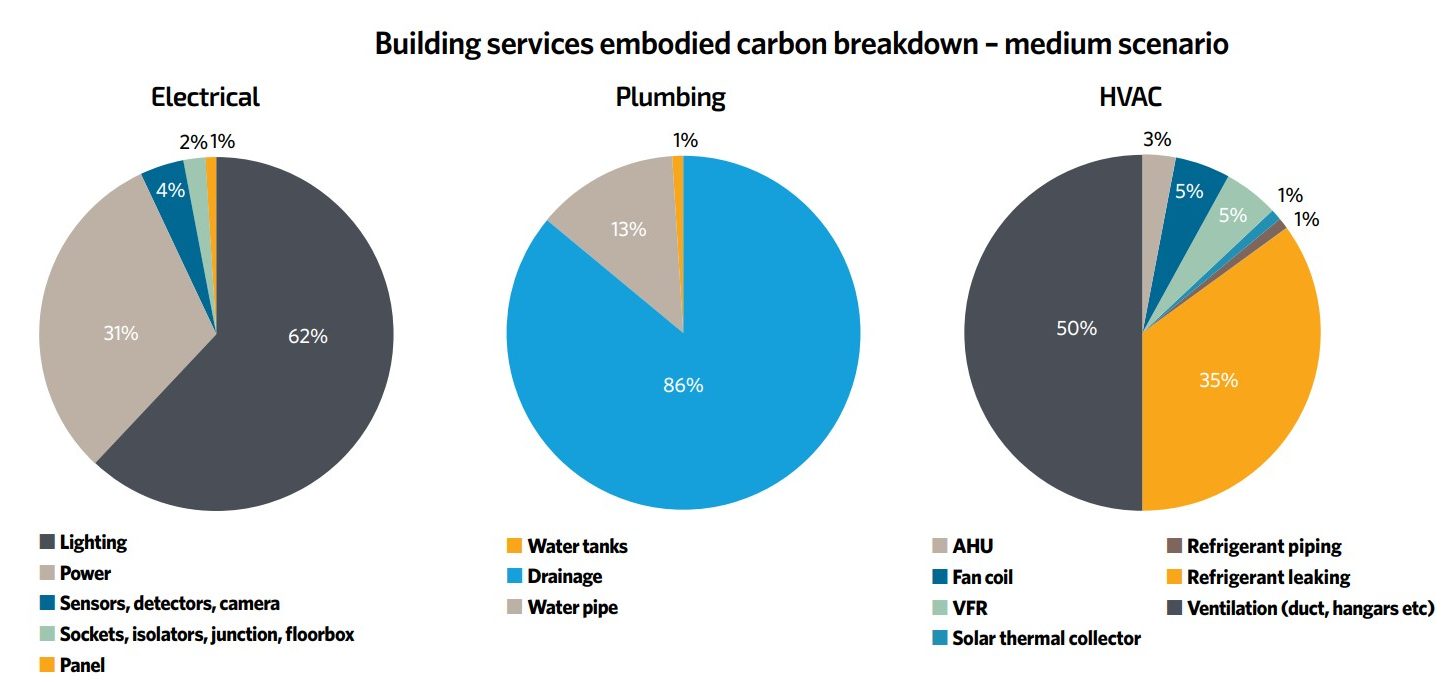
Figure 3: Embodied carbon broken down by building service. The medium scenario is described in Figure 2
Refrigerant leakage must become the absolute priority of engineers, to make sure they specify products with low-GWP refrigerants – typically less than 150 – and ensure ways to prevent and quickly detect leakage (see Figure 1).
The study revealed that plumbing, electrical and HVAC had fairly similar embodied carbon emissions across high-, medium- and low-impact scenarios, so must be tackled in parallel (see Figure 2).
Assessing the full embodied carbon emissions of the DPR case study showed 53% embodied carbon savings over a new build (for a medium-impact scenario for building services).
The research showed LED lighting systems made up the highest proportion of embodied carbon emissions for the electrical category. For the plumbing category it was drainage, and for the HVAC category ventilation systems (Figure 3).
Conclusions and next steps
Embodied carbon of MEP is relatively significant, as illustrated in Figure 4, so – as an industry – we must specify systems and equipment that will ensure low whole-life carbon. For more on reducing whole-life carbon read this feature online at www.cibsejournal.com
The DPR case study will not reflect the reality of all office retrofits, or Californian buildings. So it is important to broaden this research to a variety of building typologies, as well as different locations, and create robust and representative benchmarks, to gain a better understanding of the key levers in terms of system strategy and products.

Figure 4: Onsite PVs offsite operational carbon but not the embodied carbon
The carbon savings because of onsite PV compensate for the operational carbon, but not all the embodied carbon emissions of the building (see Figure 4). When referring to net-zero carbon, we should clearly understand net-zero operational carbon and not whole-life carbon. Some thinking needs to be done to reduce the remaining emissions linked to embodied carbon and then offset it if there are no other alternatives.
About the author
Louise hamot is a sustainability and environmental engineer at Elementa Consulting. Email louise.hamot@elementaconsulting.com