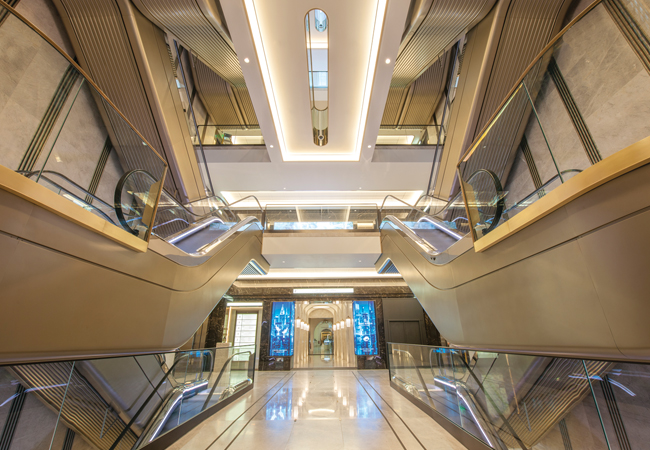
With 447 departments spread over more than 93,000m2 of floor space, Harrods is considered the jewel in the crown of London’s department stores. Selling everything from Jimmy Choo shoes to teddy bears, the store’s motto is Omnia Omnibus Ubique – ‘Everything for everybody, everywhere’.
This year, shoppers searching for their January sales bargains will be in for a treat when they enter the Knightsbridge store through its newly refurbished grand entrance hall. With a £20m investment from its Qatari owners, the store spent most of 2016 returning the Hans Crescent escalator hall to its former glory. Harrods’ owners wanted to bring back the glamour of the early 1900s by restoring original elements, including luminaires and the façade.
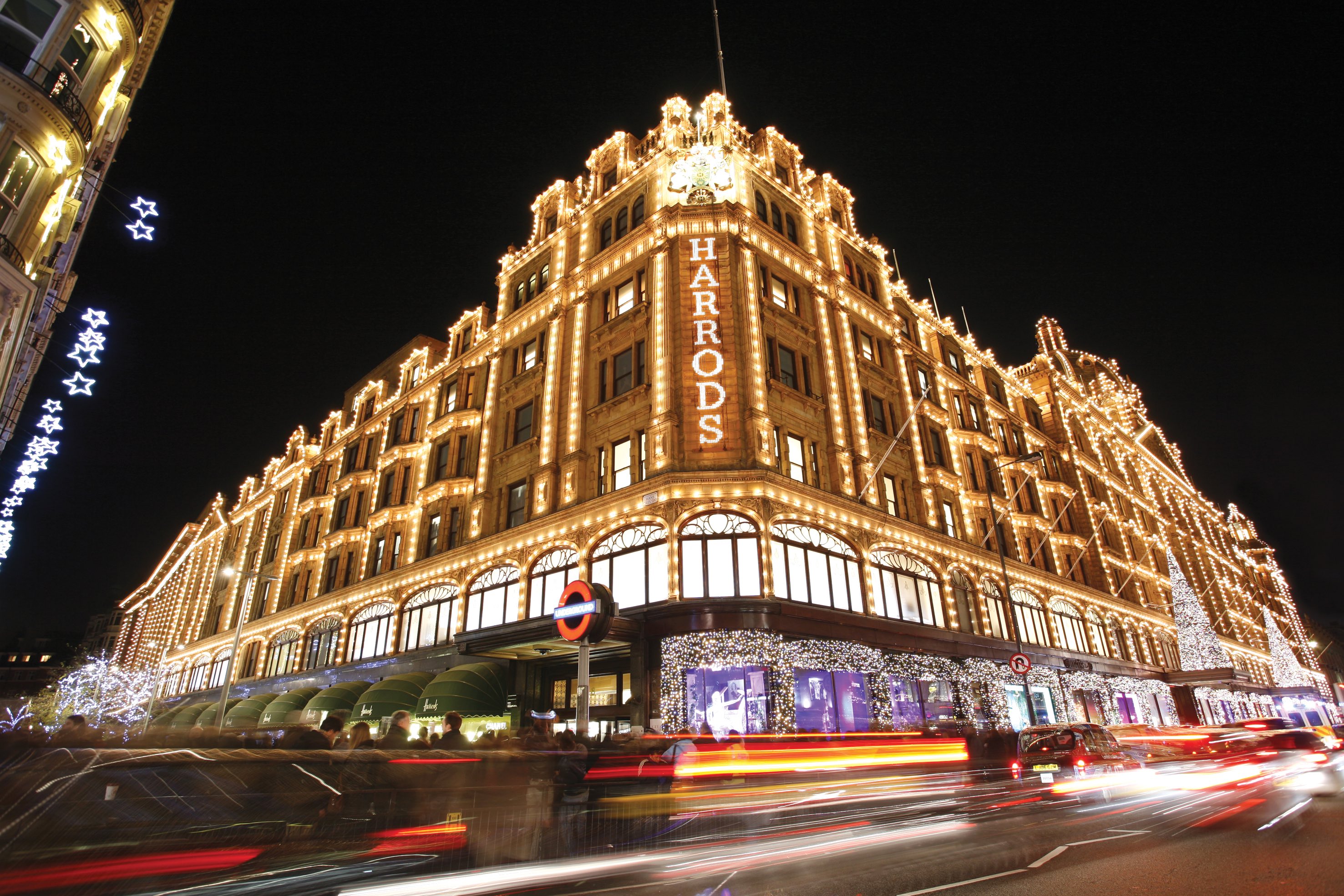
A key part of the client’s brief was to ensure the building services design matched the architectural finish.
‘We’re making all the architectural features work quite hard so we can keep the space in line with the original history of Harrods – everything we do goes back to the history,’ says John Allcock, senior building services project manager at Harrods. ‘We have a modern building, but we want to keep it looking like the Harrods people know and love.’
The design team had to marry the new and the old seamlessly, using sympathetic techniques such as concealing ventilation ductwork behind decorative aluminium grilles installed in the 1930s, opening up original windows, and redesigning a glass roof dome to allow customers to gaze at the sky from the ground floor. A total of 16 escalators have also been installed – between the lower ground and the fifth floors – in one of the most complex refurbishments attempted in the Grade II-listed building.
Project team
- Client: Harrods
- Architect: Make Architects
- Building services engineer: E+M Tecnica
- Lighting: Nulty
- Main contractor: Jaysam Contractors
- Vertical transportation: WSP Parsons Brinckerhoff
- Fire consultant: Affinity Fire
Going up
Harrods debuted the UK’s first escalator – a woven-leather conveyor belt, with a mahogany and silver, plate-glass balustrade – in 1898. To calm their nerves after the experience, customers were offered a stiff drink at the top. More than a century later, Harrods has kept up the tradition of bringing innovation to its store. ‘Charles Henry Harrod did something that had never been seen before – and that has stayed with the brand over the decades,’ says Allcock. ‘In creating the grand entrance, it was important to make the best possible first impression.’
This meant changing the positions of the up and down escalators to create a more expansive space and ensure better vision for customers entering the store. The ground-floor escalator – which was cantilevered off a newly constructed column – now appears to be floating, allowing views into the lower-ground floor. Inverter drives have been fitted so the speed of the escalators may be reduced when they have no passengers.
The biggest challenge during construction was actually installing the escalators, which had to be carried in manually at ground-floor level and winched up inside. At night during a four-week period, the escalators – the largest of which weighed five tonnes – were delivered, craned off the lorry, wheeled along the pavement and craned into the hall, before being winched up into position.
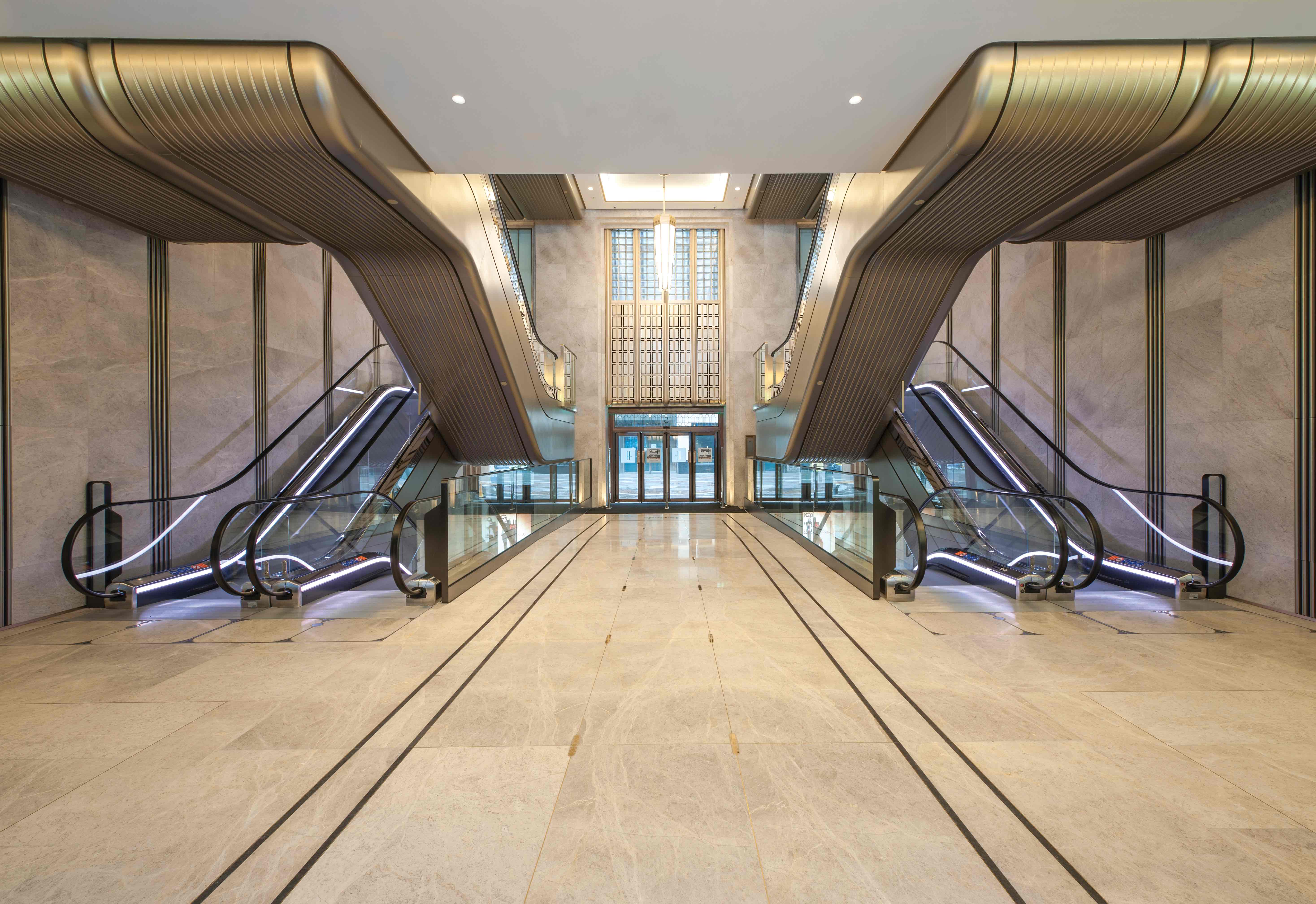
The architectural element above the door houses nozzle diffusers
The decision to swap the escalators around instigated a whole host of structural works after upstanding foundations were discovered at lower ground-floor level. Almost 30 piles had to be buried 23 metres into the ground so the original foundations could be removed and the escalators re-sited.
Separate electrical supplies feed the two sets of escalators, so customers can still move around if power is lost to one side. This meant finding a suitable route for the 250m-long cables supplying electricity from the main sub-basement switch room, located at the opposite end of Harrods. ‘It was quite an extension lead,’ says Adam Heselden, technical director at E+M Tecnica, who spent a day surveying the routes.
To avoid excessive volt drop in such a long run, the size of the cable had to be increased. ‘The longer the run, the more copper you need to introduce and the larger the cable size gets to ensure appropriate voltage is supplied to the escalators,’ says Heselden.
To keep the size of the power leads down, each supply was split between two cables, placed in parallel.
Ventilation strategy
Air is distributed throughout the hall using a plenum arrangement connected to architectural-finished grilles. The general extract is at high level in the roof-dome area. Conditioned ventilation air is transferred from the rooftop air handling plant down the building through three ventilation shafts – converted light wells from the days before electric lighting – at a temperature of 14°C all year round.
The cooling strategy is a constant temperature, variable volume system, with control dampers at each floor. When additional cooling is required, the dampers open to allow a larger volume of air into the space. When cooling is no longer required, the damper will ramp down to its minimum setting to maintain the fresh-air requirements. Air is fed into supply plenum boxes – located at each landing – hidden behind vertical aluminium grilles that run up the walls from the lower-ground to the fifth floor. These architectural strips were incorporated into the original design of the hall in the 1930s, serving a purely decorative purpose. Now they are used as service vents for displacement ventilation to introduce cooling into the space.
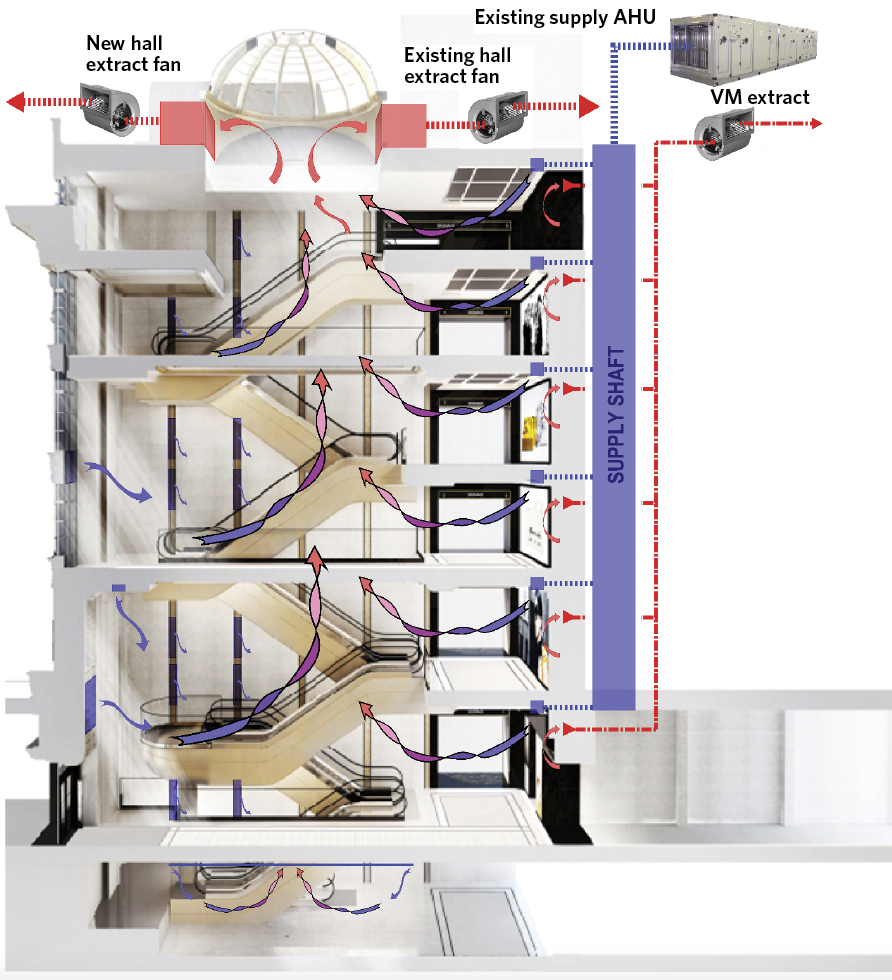
E+M Tecnica's ventilation concept
As well as maintaining Harrods’ heritage, the strategy addresses a key element of the brief – to mask the services. ‘The services strategy had to align to the original 1930s concept, so it was a case of marrying together the historical and the modern,’ says Ben Otiko, mechanical engineer at E+M Tecnica.
Between the ground and first floors, ventilation is supplied through nozzle diffusers incorporated into the restored architectural element on the front of the façade – another feature of the original building. The feature is, in essence, a set of openable doors, behind which sit the nozzle diffusers and the fibre-optic lighting boxes that need to be easily accessible.
Temperature sensors on each floor and landing monitor the conditions, allowing the building management system to adjust the control dampers according to the amount of cooling needed. Plenums at the top of the roof dome are connected to Harrods’ existing extract system to remove the vitiated air.
The LED video wall at the back of the hall is served by an additional extract system that directly removes 50% of that heat load.
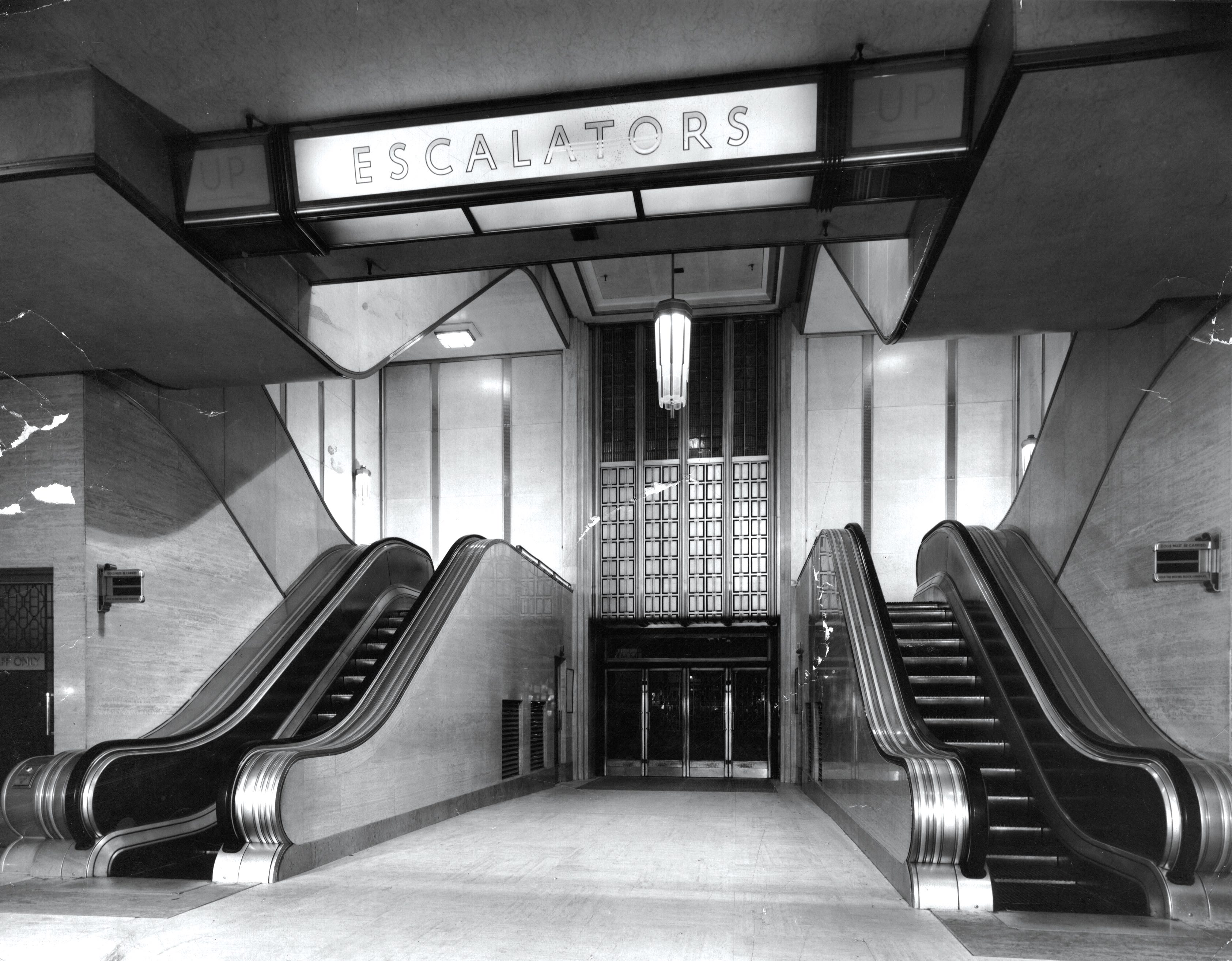
The grand entrance hall in 1939
Lighting up the hall
Indirect lighting has been used throughout the escalator hall to highlight its heritage characteristics, says Emilio Hernandez, associate at Nulty.
Linear LEDs have been installed in a coffer, directing the light towards the ceiling and wall surfaces, which reflect diffused light back into the space.
Because the hall is not a retail space, the team could be more restrained when setting light levels – the floor surface is maintained at 250-300 lux – but the use of a lighter colour palette on the walls and ceiling ensured enough light could be reflected off the surfaces, says Ida Evensen, lighting designer at Nulty. ‘We focused on highlighting interesting architectural details to celebrate the building’s architecture because – even with high light levels on the floor surface – a space can still appear underlit if the walls and ceiling are dark,’ adds Evensen.
Vertical details are emphasised by uplighting, with wall grazing used for metal grilles and stonework, and backlighting on reeded glass. The illuminated coffers also draw the eye upwards and make the space appear taller. To bring natural light into the space, the roof dome – added in the 1980s refurbishment – has been redesigned and repositioned. External lighting was omitted and, instead, the fritting on the dome has been illuminated directly from below the glass element. Previously frosted – like a church window – the roof dome is now clear, offering more light penetration and views to the outside.
Fire strategy
The old point-detection system has been replaced with beam detectors at three locations: the base of the roof dome, and within the cut-out ‘lozenges’ on the second and fourth floors.
The width and height of the fire doors that lead off the escalators had to be increased, which meant losing the fire compartments during construction. ‘We spent a lot of time trying to work out how we could phase the project in such a way that we could still keep people walking through the escalator hall while retaining our fire strategy,’
says Allcock.
Hoardings – made of fire-rated plasterboard, with built-in lighting, smoke detection and cameras – were installed. At night, these were dropped, and the portals onto the escalator hall were blocked with a series of temporary fire and smoke screens while the contractor carried out works. This was done each night for the duration of the project, and flipped back again ready for trade at 10am.
‘The hall is such a thoroughfare from one side of the store to the other, that we couldn’t allow it to be shut, so several hours each night were spent taking the hoardings down and putting them back up again,’ says Allcock.
On the second and fourth floors, there are fibrous-plaster, uplit ceiling coffers, centered over the skylight, which allow customers in the hall to look up and see through the roof dome. The extensive glazing on the front of the façade has also been opened up, while two original chandeliers and the mid-1940s, rectangular, ceiling-mounted luminaires have been restored and upgraded to use LED lamps.
Weekly meetings and workshops were held during the design period. ‘You couldn’t sit in isolation and do your little bit, and hope the contractor sorted it out – we had to work together,’ says Heselden.
Design and construction lasted 19 months, with the world’s first corner LED screens installed at the last minute, having just come off the production line. But for a shop that once hired a cobra to guard a pair of diamond- and sapphire-encrusted sandals worth £62,000, only the best will do.
Picture perfect
The Chinese-manufactured 1.7mm pixel pitch LED screens are completely trimless, allowing a seamless display across the hall’s 62m2 of screens, across 12 locations.
These displays replace the previous LCD screens, which had a small frame around them where they buckled together.
Allcock says: ‘LED technology means the gap is only 1.7mm between the pixels, so our screens are five metres long and three metres high without any interruption.’
Some of the most innovative aspects of the hall are the ground floor corner LED screens.
‘We had to miter the edges of the 2mm pixel pitch LED board so they could fit tightly together to avoid a seam. This is one of the first installations in the world for a corner screen – we got the first one off the production line,’ says Allcock, adding, ‘because technology moves so quickly we held off ordering until the very last minute.’
The screens were installed just two weeks before the hall opened to the public.