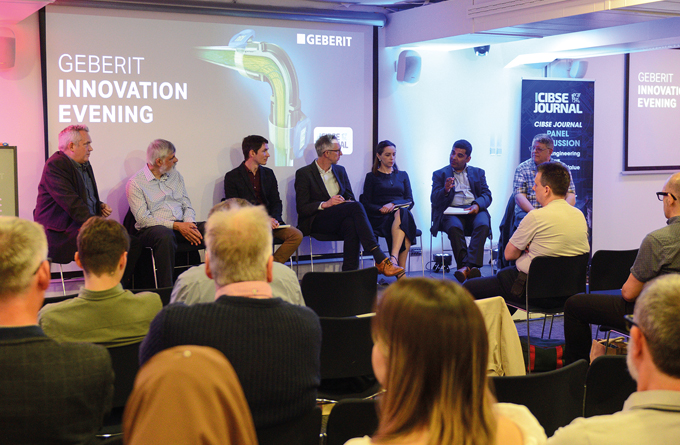
In a break from CIBSE Journal’s roundtable format, Geberit sponsored an innovation evening with key industry panellists and a live audience at the Building Centre, London.
Martin Murray, national specification sales manager of piping at Geberit, kicked off the May event by introducing the topic: value engineering versus engineering value. This subject generated an interesting debate, with the discussion raising other issues, including: the implications of the new competency regulations under the Building Safety Act 2022; the importance of early value engineering workshops at the pre-planning stage; and the benefits of collaboration between the design and construction teams.
The panel
Chair: Alex Smith, editor, CIBSE Journal
Malcolm Atherton, director, and design engineer at Water Consultants
Antony Corbett, product applications engineer at Geberit
Hywel Davies, chief technical officer at CIBSE
Ana Santos, principal public health engineer at Aecom
Minesh Varia, project director at Hoare Lea
James Warne, director of Inhabit
Malcolm Atherton, director, and design engineer at Water Consultants, began by considering whether value engineering on a project goes beyond the cost of the materials and construction methods? ‘Every single project that I’m involved with [dealing with above-ground drainage and domestic water services] is about cost. It’s never about a suitable alternative,’ said Atherton. ‘Quite often, the contractor will ask can we change it to a cheaper material, or how can we change things to make the cost come down? That’s their perception of value engineering.’
Minesh Varia, project director at Hoare Lea, agreed, but added that he has seen a shift in the way clients are expecting a more sustainable approach in projects. Post-Grenfell, he has also seen a heightened sense of scrutiny with projects and greater engagement between fire engineers and building control officers.
‘There is proper value engineering, rather than cost cutting, and the larger, mature clients are wanting a higher standard of product,’ he said.
Ana Santos, principal public health engineer at Aecom, said her experience is similar, and that her involvement with a range of projects – including offices, high-end residential and fit-outs – has given her a different perspective on value engineering.
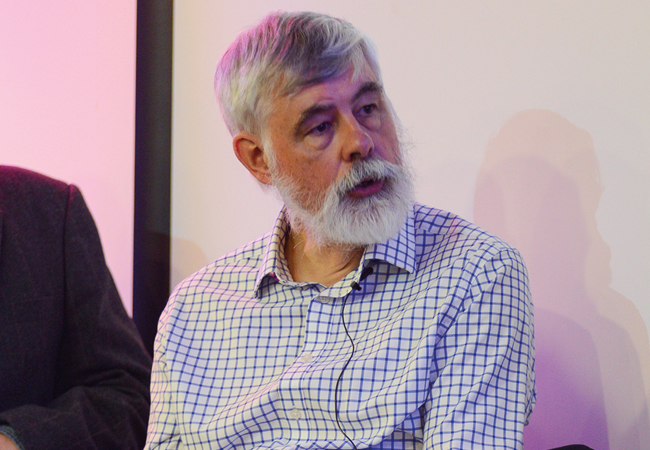
New competency regulations will present some serious challenges and implications for anyone wanting to value engineer a project – Hywel Davies, CIBSE
‘It depends a lot on the scale of the project,’ she said. ‘The big-scale projects are normally focused on providing their client with a good sustainable product, while the fit-outs must often be done quickly and cheaply. I think there will be a shift, especially with the Building Safety Act and other changes that will force the way we see value engineering.’
James Warne, director of Inhabit, is a design engineer leading MEP, civil structures, façade design, and sustainability. He said value engineering comes in different forms and stages of a project, and argued that it is successful when the team focuses on operational outcomes and uses soft landings, which aims to bridge the gap between design and operation by encouraging ongoing collaboration. But, he added, it can be a challenge to get everyone to attend a value engineering workshop to see what the operational outcomes are.
‘If value engineering is left to the last moment – for example, when the contract is about to be signed – and you’re trying to bring it under budget because it’s over budget, this is cost cutting and leaves things open for contractors,’ said Warne. ‘I’m not suggesting the contractors are doing anything inappropriate, but they are being asked to reduce their costs and they are allowed to do it by any means necessary within the contract.’
He said this happened on a school project on which he worked. A significant amount of money had to be cut from the budget and, as the contractor was given free rein, the design suffered as a result.
‘The earlier we have those value engineering workshops the better, and it’s about engaging with the right people,’ added Warne.
Antony Corbett, product applications engineer at Geberit, echoed the panellists’ views. When Geberit products are specified, he hopes to see them go through to build stage and be used on a project. Instead, what often happens, he said, is that a particular product gets specified and, at the procurement stage, an M&E contractor decides to value engineer. The contractor then selects a product that they deem is an equivalent, but that might not fit the original specification correctly.
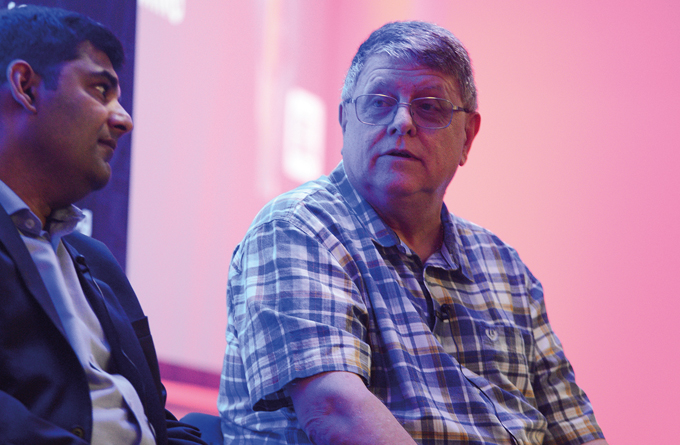
Every single project that I’m involved with is about cost. It’s never about a suitable alternative” – Malcolm Atherton, Water Consultants
‘If our product gets downgraded at a later stage, it’s usually down to cost,’ said Corbett. ‘We’re asked whether we can match a price that comes with a product and, very often, we can’t, because it’s a completely different product and doesn’t fit the original specification.’
Hywel Davies, chief technical officer at CIBSE, cut through the discussion by highlighting the new competency regulations of the Building Safety Act that is coming into force. These will present some serious challenges and implications for anyone wanting to value engineer a project.
If a change is made – whether it be a product substitution or a design alteration – the person making it will need to demonstrate that any alternative is fully compliant and has the same performance as the original. Also, if a design is modified, they will need to prove that they are a competent designer. If they meet these criteria, they need to sign off the modified design and demonstrate that they have professional indemnity insurance.
Davies warned that enforcement action is now being taken very seriously, particularly on high-risk buildings such as hospitals, care homes, residential, and buildings more than 18m tall. It will be against the law to start building works before a regulator has signed off the design, and the penalties are severe.
‘The new competency regulations in the Building Safety Act change many of the building control processes and apply to all regulated building work,’ said Davies.
‘The latest figures from the planning gateway one suggests that as many as 50% of projects are being knocked back by the regulator because the fire strategy is inadequate. I find this staggering, given that it’s been nearly six years since Grenfell.’
However, Varia put a positive spin on the value engineering process. He agreed that it should happen early, at the pre-planning stage, and said that it works well when the client is fully engaged in the process and understands the risks.
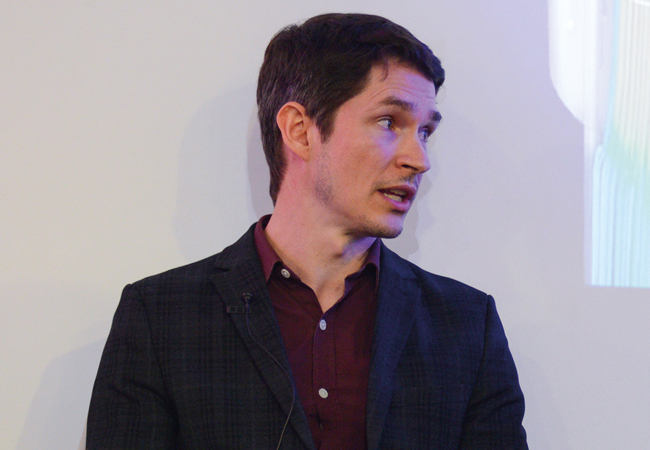
As a conglomerate of manufacturers, we’re having conversations about making sure our products meet standards and that, when any of the products are specified, they meet the building requirements – Antony Corbett, Geberit
‘I sometimes feel we [architect, structural engineer and MEP] work in silos when we go through the value engineering process,’ said Varia. ‘But when we have a collaborative approach, that’s when we get the most significant value engineering opportunities.
‘We’re having more grown-up conversations with contractors, as they have a lot of knowledge on products, buildability and prefabrication. Given that we’re getting tender returns at 20% higher than the cost plan because of inflationary pressures, projects will stop unless we find a suitable compromise with contractors on the budget.’
Santos enthusiastically agreed. ‘As designers, we need to understand that the contractor’s role is difficult and they work to very tight programmes,’ she said. ‘They also work with designs that are not good, and sometimes they need to make changes, which are not always bad. Legislation requires us to build bridges across the different disciplines and we are changing, as designers, in the way we look at this communication.’
Given that sustainability, energy savings, embodied carbon and operational carbon are all in the spotlight, said Santos, these aspects remind engineers that they must design differently. Clients are aware of this, and contractors are being forced to see this, to ensure the project meets the client’s expectations.
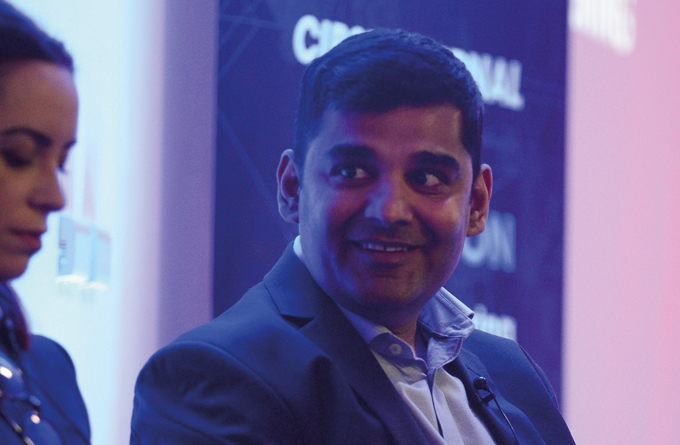
We’re having more grown-up conversations with contractors, as they have a lot of knowledge on products, buildability, and prefabrication – Minesh Varia, Hoare Lea
Santos recently completed a refurbishment project that, she said, was very successful mainly because everyone’s different points of view were respected. There was a desire to do better, and good communication between the multidisciplinary teams was key to its success.
Warne is very supportive of this approach. ‘Without doubt, good results come from collaborative teamwork,’ he said. ‘We need to stop building boundaries and say that we’re all part of one team. We must value engineer, not cost cut, and value engineer at an early stage. Well-informed clients make this process easier, but competent designers should take the lead.’
Warne, however, argued that we face a significant challenge to comply with the Building Safety Act, which requires competent people. Because of the massive skills gap across every stage of the construction industry, he said, there aren’t enough skilled people to do the construction work over the next 30 years. He suggested that modern methods of construction and innovation could be employed to look at how to de-skill processes.
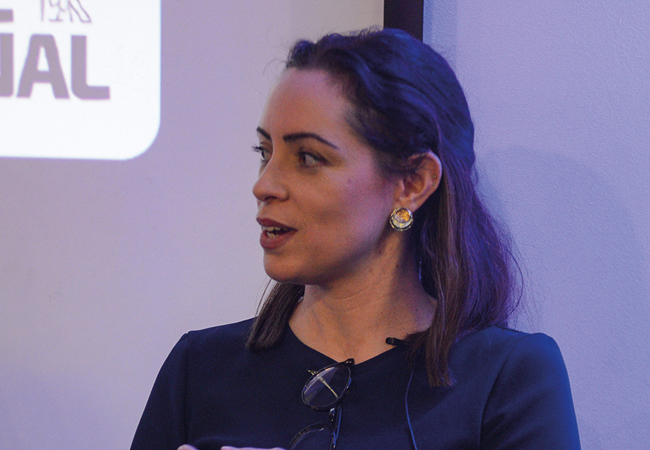
Legislation requires us to build bridges across the different disciplines and we are changing as designers in the way we look at this communication – Ana Santos, Aecom
But Atherton is concerned: ‘The real danger is that, if you go too far de-skilling something, the person physically doing the process won’t fully understand what it is they are doing and the importance of what they are doing.’
Warne agreed about the risk, but argued that the industry needs to find the answer, given the shortage of competent, skilled people in construction. ‘The only way forward is to find a way of constructing a building that’s on time, within budget and requires a de-skilled labour force,’ he said.
‘I’ve got some good news for James [Warne],’ added Davies. ‘One of the other duties we expect to be in there [the Building Safety Act regulations] is a duty to cooperate between all members of the design team and construction team.’
Corbett agreed that conversations with architects, specifiers, consultants, contractors and installers are crucial, helping them to understand the different perspectives and requirements of products. ‘I sit on a couple of technical committees for the British Metal Tubes and Fittings Association and the British Plastics Federation,’ said Corbett. ‘As a conglomerate of manufacturers, we’re having conversations about making sure our products meet standards and that when any of the products are specified, they meet the building requirements.
‘We’re making sure that our products are fully compliant and that they will do what they must do for the lifespan that the client of that building requires.’ Davies was then asked how the industry gets the message across about important regulation updates to smaller building firms, which often don’t have the time to keep abreast of the latest information.
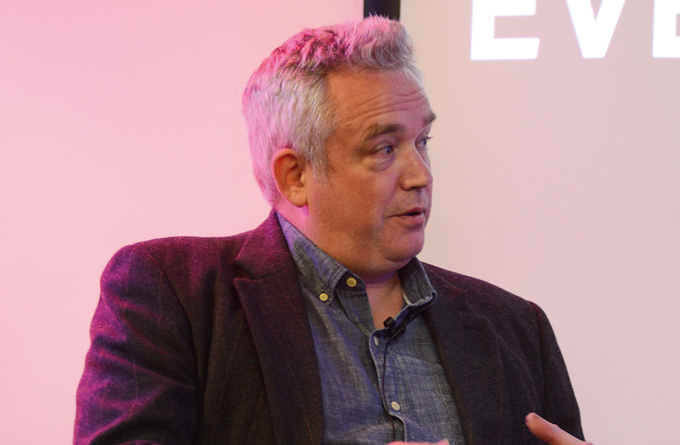
We must value engineer, not cost cut, and do it at an early stage. Well-informed clients make this process easier, but competent designers should take the lead” – James Warne, Inhabit
‘With great difficulty,’ said Davies. ‘Many smaller contractors probably don’t know about the Building Safety Act and won’t make the connection between what happened at Grenfell and the work they do. Responsible manufacturers have got both a role and an opportunity here by providing basic information about the act and the expectations.
‘Manufacturers will need to be careful, though, that their technical literature isn’t seen as design information, because – if something goes wrong – they don’t want to be seen as responsible.’
Corbett added: ‘There will be greater onus on manufacturers to provide precise detail on what their products can do and what they’re manufactured from.
‘Any technical details that are publicly available will be required by the Building Regulations and construction product regulations, and for that information to be correct.’
The new building safety regime and focus on net carbon zero buildings means procurement processes must ensure real value engineering.
Without early engagement, collaboration, and a focus on operational outcomes buildings will fail to deliver on their design promise. As panel discussed the competence of designers will be critical in ensuring high-performing buildings and it will be them who should lead on ensuring true value engineering.