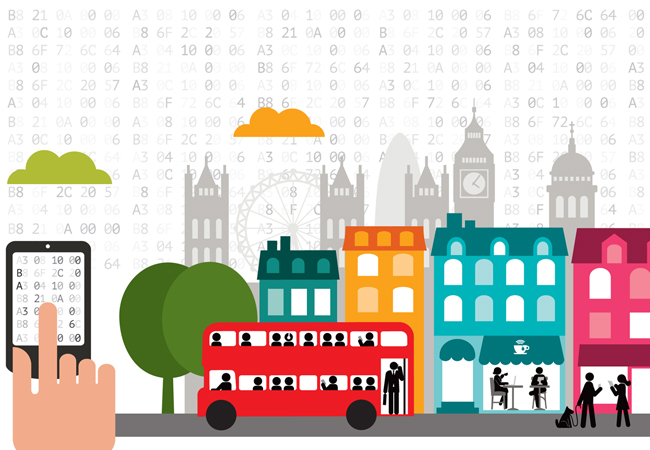
The importance of data management has increased in recent times because of the significant value in creating information that can be used to improve performance. Consequently, data generation has expanded drastically and the term ‘big data’ has become a common concept in the built environment.
In this new era of data-based decision-making, we can look towards a more integrated approach to building performance. This includes: performance-based design; connectivity within design and build; the way a smart building operates; the needs of the workplace; digital technology; the platform for integration; system integration; continuous measurement of performance; and analysis of data and decision-making.
Big data seeks to offer a solution based on databases and data analysis; it is not just about storage and availability. The objective is to analyse the data to make sense of it, and leverage the value that can come from it by joining up different data sets to form a broader understanding of building performance.
Overall objective and vision
In truth, the data we can abstract from buildings isn’t really so big – most of it is very manageable, if structured in an organised way. This means measuring things, auditing, carrying out technical reviews, behavioural change and applying a collaborative approach to reducing energy waste, while not diminishing occupants’ comfort. The maintenance activities and life-cycle status of the systems and fabrics must also be incorporated into the overall plan of action.
Focusing on the delivery of the construction of educational facilities – especially in the field of building energy efficiency – collecting big data, using different kinds of measurement and analysis, can help improve the process of creating more efficient facilities in the future.
Performance and energy in schools
We must be realistic about the way buildings perform and the cause of the performance gaps. The first step is to identify simple metrics for monitoring performance, and comparing to benchmarks and data from a range of buildings.
For schools, we use the carbon-per-pupil metric. This is because schools can vary widely in their levels of carbon emissions as a result of their size, use, management, system selections and building shapes and fabrics. They can also vary in performance because of their age, size, style and technologies. CO2 per pupil in primary schools can range from 180kg to about 500kg per annum, and in secondary schools from around 400kg to 900kg per annum.
Interestingly, older schools can perform at much lower levels of CO2 and energy than some newer facilities. This is because some modern services such as mechanical ventilation can use more energy during their operation.
The key to any energy strategy is to assess the capability of the building and its technical systems to achieve the performance targets that have been set. This includes the training and competency of the onsite team that maintains and operates the systems.
In some facilities, how control systems work – and how control parameters can be maximised while safeguarding comfort conditions for the occupants – isn’t always well understood. Also, responsibility for control-system maintenance is often subcontracted out, which can lead to a lack of single-point ownership.
Control sensors can be out of calibration – or even obsolete – as these elements can be overlooked in the planned preventative maintenance (PPM) scheduling. This can cause systems to operate ineffectively, waste energy and cause disruption.
The operation of facilities can be complex. Energy consumption can increase outside of school hours – for example, during additional functions at weekends and in the evenings. So targets for the facilities need to be structured accordingly.
Occupant behaviour in relation to energy use can also be part of the ‘big data’ picture, when occupancy levels, use of areas, and the management of doors, windows and lights are considered. It is essential to make staff more aware of these important features, as well as to implement an energy-communications plan.
We have established a key principle of improving the management of energy in schools, which requires the integration of engineering and controls expertise into the monitoring/management activities around energy and the building management system (BMS).
Remote monitoring and management
A remote monitoring and management capability that operates on a number of facilities is the best way to improve energy performance. This is in place in more than 20 secondary schools in the north of England, with the remote monitoring operated from our head office in London. Most of the schools are new-build, with only two extensively refurbished.
The remote-management facility was developed to bring specialist expertise within the business in contact with the day-to-day delivery of contractual requirements. It serves key elements around building performance and energy.
Improving the management of energy in schools requires the integration of engineering and controls expertise into the monitoring/management activities around energy and the BMS
Various contractual requirements mean the facilities must be operated efficiently. For example, energy and water has to be managed within benchmarks established during the first two years of operation. We are also required to maintain specific environmental conditions within different room types. Classrooms, games halls and gyms, and circulation spaces have to be managed to tight criteria, with financial penalties for failures.
A building energy management system (BEMS) was installed at each school and connected – via stand-alone networks – to head-end management stations at the local office. Once this was complete, the team in London began to review basic settings around time clocks, temperature requirements and settings, and put in place a number of management protocols to control how – and when – changes to the system could be made. Access to the system was restricted, and training given to regular users to maintain good operational order.
Once this early phase was completed, the team began to make use of the advanced features of the system to log and report on hundreds of individual data points. A detailed set of logs was initiated within each controller – including boiler flow and return, calorifier and space temperatures – and elements such as valve position and pump activity were recorded. Control signals being sent by the system were also tracked, to allow for the monitoring of equipment responses to instructions sent.
Making big data work
This capability generated large volumes of data that – to be meaningful – had to be processed, analysed and acted upon.
We developed, and continue to develop, data-mining tools to turn this big data into useful information. Such tools, and the active system monitoring, have allowed us to support total carbon reductions of around 11,500 tonnes of CO2 over five years.
There are many advantages to the operational capability this system gives us. We can: very quickly identify and alert the team if there is an issue; reduce the risk of a compliance failure on a space temperature condition; and ensure we are operating the facilities at a level of efficiency that is well inside our benchmarked conditions.
As a result of using this data, carbon emissions associated with energy consumption have fallen from 603 tonnes per pupil in the first year, post-benchmarking, to 497 tonnes per pupil today. This is a reduction of around 18% in five years and, with the data revealing ever more opportunities, we expect emissions to continue to fall.
We are working towards greater integration between systems, maintenance, energy use and expert diagnoses, to achieve performance excellence. A greater vision could be to establish a predictive model, which can assimilate total building operations and adjust systems to achieve the best possible performance automatically.
- George Adams is UK engineering director and Liam Rock is energy manager at Spie UK