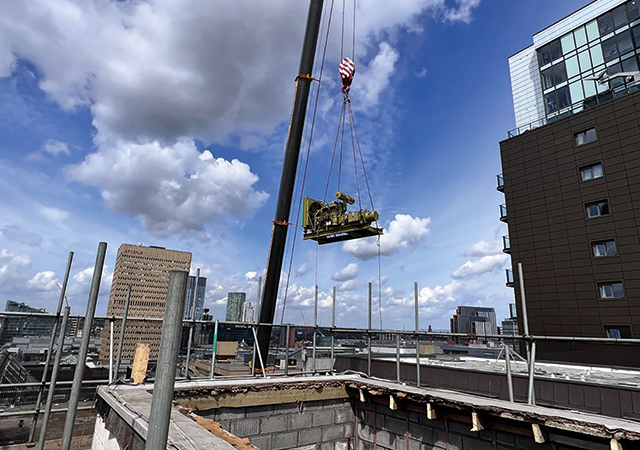
A generator being removed from a former Debenhams store in Manchester will be reused in a railway museum
There is an adage that states ‘if you can’t grow it, you have to mine it’ – but can this go on forever? The Global Resources Outlook 2024, by the UN Environment Programme, sent a stark message that global resource consumption has tripled in the past 50 years. This is expected to double in the next 35 years and, along with it, the wider negative environmental impacts.
In 2020, 10% of global resource extraction (9.6 billion tonnes) accounted for iron, aluminium, copper and other non-ferrous metals. Energy transmission and storage infrastructure will require a significant quantity of metals. The responsible use of resources that have already been mined and are currently in use is critical.
A circular economy model aims to reduce the need for new materials and reduce waste. It does this by keeping materials in use for longer through reuse, refurbishment, repair and by using secondary recycled materials. The sixth Climate Change Committee report, from 2020, includes resource efficiency as a key policy and estimates an annual UK emissions reduction of 8 million tonnes of CO2e by 2035. Efficiency measures include optimisation of design through reduced material inputs, more reuse and recycling, and increasing product lifespan.
The MEP sector must take an active role in the solution by enabling the decarbonisation of the construction sector. Manufacturers of MEP equipment rely, fundamentally, on the global supply chain for various minerals and metals, and are exposed to critical shortages and market volatility. Production supply chains are long, with individual parts sourced from third parties, then assembled and delivered semi-finished, or finished, for installation on site. The rate of technological development and shorter replacement cycles means manufacturers, as well as the construction industry, hold the responsibility for managing the resource flow.
At Max Fordham, our experience shows that it is possible to mainstream MEP repair and reuse, not just for historic conservation reasons, but in everyday practice. This will help scale up knowledge and confidence in doing this more commonly in the sector.
The Passivhaus EnerPHit-certified deep retrofit of The Entopia Building in Cambridge championed efficiency of resource use, as well as operational energy performance. The client’s commitment helped the team to identify ways to overcome risks and accept reuse of the building’s original MEP equipment. Reused items included elements of the generator systems, electrical sub-mains, principal drainage stacks, lightning protection, and lifts. The scheme also reused elements sourced from elsewhere, such as LED lighting in the main office areas, the steel frame for the PV canopy, and raised access flooring.
Reuse of MEP equipment required a higher level of coordination, from early design through to construction. The overall upfront embodied carbon savings, at a building level, from the reuse of these MEP items was minimal compared with the savings from the use of reclaimed structural steel or raised access flooring. So why do it?
The driver was to minimise the wider environmental impact (more than just carbon) and be an example for resource efficiency within a commercial refurbishment scheme. The project team overcame common challenges with reuse by acquiring the maintenance records, assessing the condition of the equipment, and undertaking the necessary tests to provide warranty.
Typically, when a building is refurbished or demolished, most MEP items are marked for recycling. It can be challenging to track the waste-processing routes once an item leaves the site. Manufacturer takeback schemes are available, such as Grundfos, which supplied 10,000 circulator pumps to heat pump maker NIBE with remanufactured, reused rotors. However, these schemes are embryonic: what can we do about equipment that is in good condition, but no longer needed in a specific building, if the manufacturers are not interested?
Another Max Fordham project is the Rylands Building, in Manchester, which is currently in construction. We developed a detailed material-reuse strategy for this refurbishment and conversion of the Grade II-listed warehouse building (most recently a Debenhams) into 43,300m2 of retail and office space, .
More than 20 tonnes of steel from MEP items have been carefully stripped out for reuse by others, thereby avoiding 68 tonnes of carbon emissions. This equates to ~40% of annual operational carbon emissions from a typical 10,000m2 GIA new-build office building.
More than 600 existing LED spotlights were assessed, recovered and sent to EGG Lighting for remanufacturing, saving 14 tonnes of CO2e and 644kg of electronic waste (see Figure 1). Products were fully disassembled and cleaned, reassembled as per BS 8887-221, with new electrical components, including new LED drivers and track adapters. The lights are now available to buy with full CE marking, five-year warranty and a digital passport; some have already been installed in other buildings, including at the London School of Architecture.
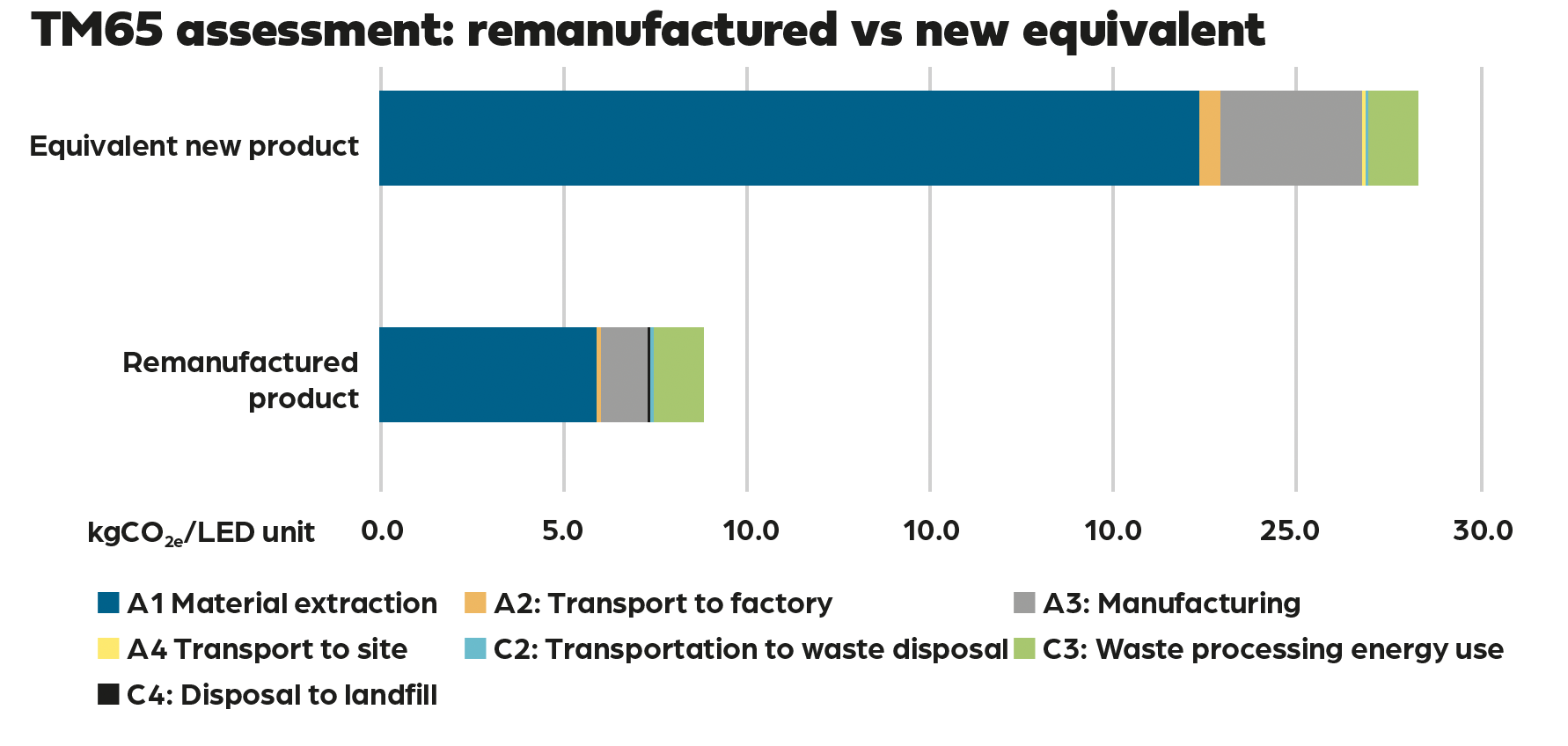
Figure 1: Embodied carbon savings as a result of 600 LED spot lights from the Rylands Building being recovered and remanufactured
From nine redundant escalators, the team recovered 12.6 tonnes of steel, including escalator treads, pit covers, electrical boxes, drive rims and guides, for reuse within the escalator maintenance and repair sector.
The most logistically complex deconstruction was the removal of two generators, which required cutting open a roof and closing a road to allow a crane to lift them out (see image) and load them onto a truck for reuse at Carnforth Station Heritage Centre in Lancashire.
Material efficiency and managing fragility in the supply chain should be high on the agenda for the building services sector. For existing buildings, an early design-stage condition survey of existing equipment via installers, and mapping items that can be reused or remanufactured, is the first step. It will help to build the practical information required at the detailed design stage, overcome the challenges of availability of existing data, and manage contractors’ risk allowances at procurement stage.
Although it’s challenging to deliver, if all in the industry work together, we can build a genuinely circular construction industry fit for the future.

Kiru Balson
About the author
Kiru Balson is whole life carbon and circular economy leader at Max Fordham