As consulting engineers, we all ponder overheating, the urban heat-island effect, cost-effective CO2 reduction and the overall sustainability of our projects. We use BIM, passive design, complex analysis, soft landings and a myriad of other tools to better understand our built environment, and the part it plays in wider society.
Overheating and recent climate change of a different sort, however, is also taxing the minds of consultants and contractors. I am referring to the London speculative development market. Never before have we seen so many instant flat sales, off-plan to overseas and wealthy investors. This demand has resulted in a massive increase in this area of the market, one with which designers and builders are struggling to keep pace. Recruitment of good individuals – rather than just the traditional concern of work winning – is taxing many in our industry. Not a bad thing, I hear you say, but is this sustainable? How do we keep diversity in our business to cushion any future slowdowns? How do we generate robust designs that a rapidly growing contractor workforce can implement when skilled labour becomes a rare commodity. Repetition, off-site fabrication, multiskilled operatives and more extensive use of modern systems and techniques must have a part to play.
Let’s start with repetition. This allows installation teams to develop their ability through a project, maximise the use of apprentices and help build growing capacity as more work faces become available on a project. A good level of repetition also opens additional avenues for modularisation and off-site fabrication. When we do get high repetition and a great desire to hand over completed sections of large projects – where connections to prefabricated elements are necessary – there may be benefits from multiskilled teams, again with apprentices growing into the role.
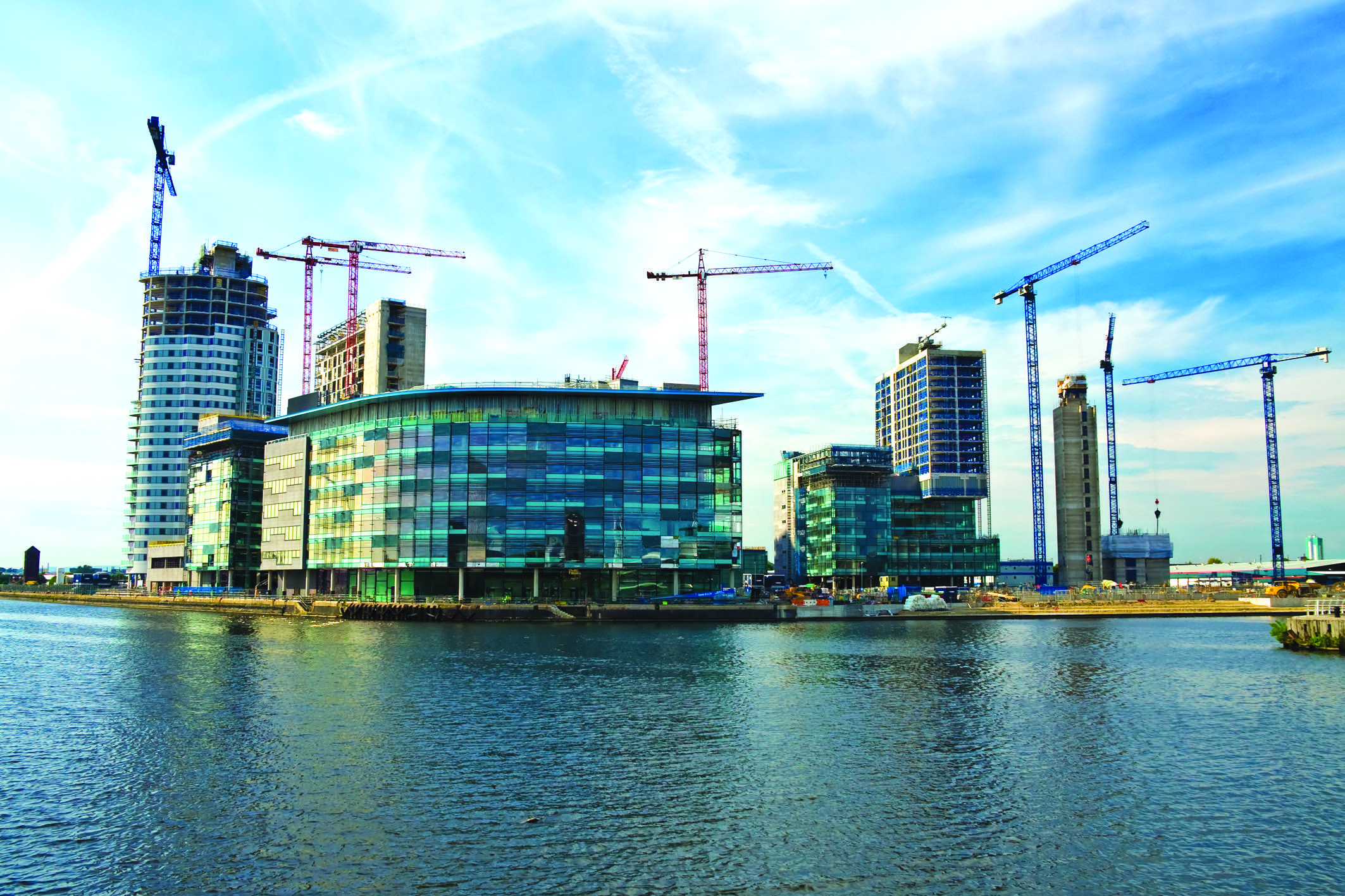
New developments in Salford, Manchester
Large projects have always warranted off-site discussions, with many electing to use toilet pods, some incorporating riser modules, and a few on-floor services and large-scale plantrooms. Now it is capacity, as well as installation speed and quality, that is a key driver in these discussions. Off-site fabrication is often talked of, but we need to change this term to design for off-site fabrication. This ethos cannot be bolted on but must run through the whole design process from day one. Otherwise opportunities for off-site fabrication will be to zero.
So what are the modern systems I have alluded to? Modern may not be the best term, as many of these technologies have been available for some time. From pre-insulated ductwork to self-balancing controls; from plug-and-play lighting and modular wiring systems to proprietary jointing. These exist to make site work and testing easier. Such systems are often discounted on cost grounds, but – in this new climate – engineers need to consider them more fully and help ensure their pricing and cost-benefit analysis are robust. This is at a time when rapid market growth can make effective cost estimation more difficult.
Another area for consideration is the real-life diversity in some of our most expensive residential towers and whether our designs have been optimised for the potential part-load and part-occupied scenarios. We have seasonal efficiency data for key building plant, but our regulations generally assume full in-use buildings. While total energy use may be below that calculated for building control, without careful consideration of controls strategy and part-load performance, relative efficiencies can quickly drop off. As engineers, we often look at this type of analysis, but how often does the ‘what if’ scenario have a real impact on plant selection?
In my business, I have looked at regional diversification to provide some additional robustness and new sector penetration alongside the speculative London market. We now have a good presence in Manchester and are undertaking some large industrial projects, although recruitment of good people here remains challenging.
I may be worried unduly about these additional technical challenges and having lots of eggs in one basket, but I can’t be the only one. Can I?
Geoffrey Palmer FCIBSE is a director at Grontmij, part of Sweco