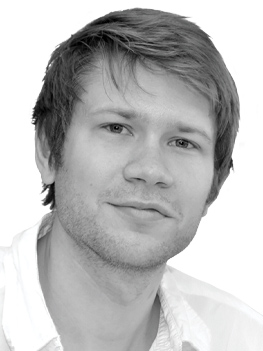
Offsite manufacture and pre-fabrication yield savings in programme, cost and waste. However, we’ve probably all had projects where the aspiration for bathroom pods is scuppered by the sequencing of the façade installation; where the cash flow required to prefabricate façade panels isn’t viable; or where the MEP can’t be built offsite because the design isn’t finished early enough in the programme.
Perhaps the key is to move away from a binary view of whether to manufacture packages offsite and, instead, look for opportunities for ‘componentisation’.
The idea of componentisation was first applied to software design more than half a century ago. Code is broken down into reusable components at every opportunity and combined to form a functioning program. This approach is embedded in pretty much every bit of software you use. It is one of the reasons people can develop the variety of applications they do, at the cost that they do.
In the construction industry, we have an ever expanding range of products at our disposal, and are pretty good at using these to develop more and more complex systems that meet the needs of a modern building. An enlightened design team might undertake reviews at the start of the project to ensure we don’t miss offsite opportunities, but until we start seeking opportunities to componentise these systems, we are leaving value on the table.
Instead of creating systems out of products, we should first ask ourselves where we can combine products to make optimised, repeatable components to replace parts of our systems. This not only creates opportunities for offsite manufacture, but manages complexity to enable us to design better and get the most out of our digital tools. You probably already do this with ‘typical details’ – you just don’t call them components.
At Ramboll, we started our componentisation journey looking at risers (zones for vertical MEP distribution), which are a common target for offsite manufacture, are complex, and affect the usable area of a building. A single chilled water riser, for example, will include pipes, various products (valves for example), insulation, and access zones. We develop staff to have the knowledge and experience to know how to coordinate all these products efficiently into a space, in an installable and maintainable way.
We should ask where we can combine products to make optimised, repeatable components to replace parts of our systems
Every building is different, so every riser is different. However, the approach to how we design a riser, given a set of inputs and constraints, is generally the same – so there is an obvious opportunity to think of a riser as a component that is consistent across all our projects.
For a developer or client, change and iterating through options create exceptional buildings. As engineers, we want to accelerate the rate at which we get ‘front loaded’ information to our clients, but abortively redesigning elements in detail leads to fees that don’t offer a client value, and ‘rules of thumb’ don’t generate the lean buildings we want to provide. Componentisation offers the ability to go further, faster, by reducing complexity to leverage digital tools. If a MEP riser is a component that automatically sizes itself based on its performance requirements and available riser depth, we can rapidly and parametrically assess options without losing detail.
Risers are just one of many elements that an architect needs to coordinate a building. Collaboration is key and componentisation allows the designers of a building to exchange components digitally, for others to coordinate with their work. An engineer passing a movable component to an architect in Revit or Rhino seems more effective than the awkward dance of trying to interpret each other’s information and agree a compromise.
In a lot of cases, components can be defined long before the design is complete. This will allow integration with supply chains and contractors to optimise the performance and buildability of the components, understand cost and cash-flow considerations, and incorporate specific logistical requirements.
For inspiration, let’s look to the automotive industry. A modern car maker produces a vast array of car ‘recipes’ from relatively few ‘component’ ingredients. For example, Volkswagen uses standardised components (its MQB platform) to make hundreds of different cars under 12 brands across 125 factories.
We, too, have the skills to be better, and to create unique and exceptional buildings out of common optimised components – we just need a change of gear.