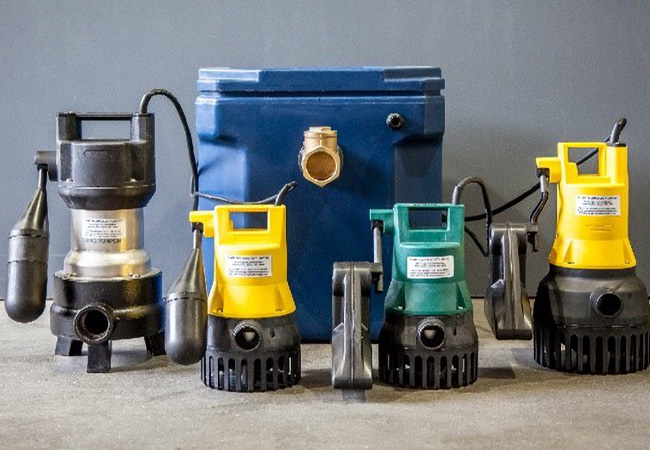
Floor-mounted systems
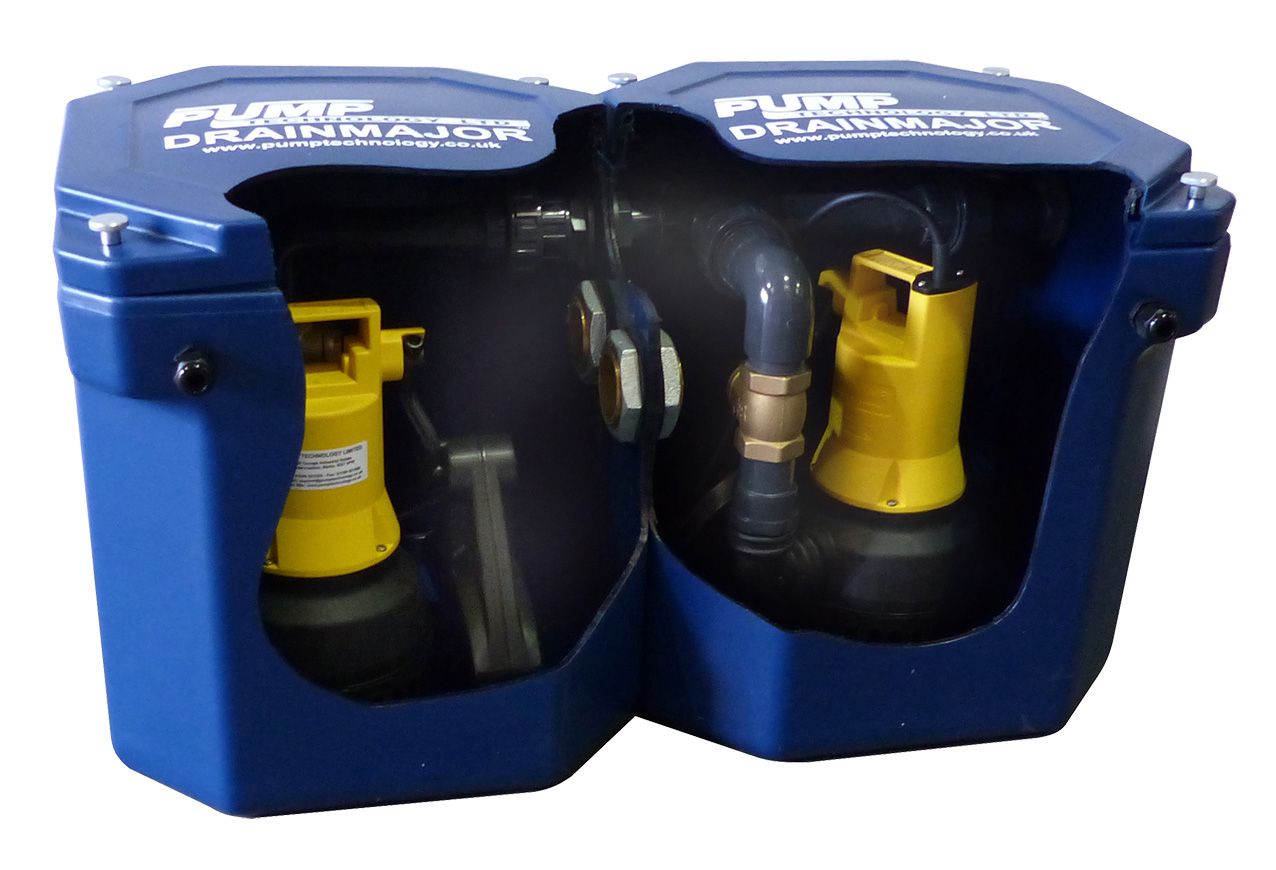
While a floor mounted wastewater pumping system is a relatively small part of a project, it requires accurate product specification to ensure reliable operation and long pump life. The consequences of a pump breakdown could be flooded floors or a blocked toilet, often in an office working environment. This can be extremely inconvenient and possibly expensive in terms of work lost and repair bills.
Pumping equipment is relatively low tech. Products from leading brands have now been developed to a level where, if specified and installed properly and correctly serviced, they should provide many years of trouble-free service.
Working through the minefield of ‘choice’
However, within the pump industry there is an infinite matrix of choice. Pumps are designed with limited performance envelopes but, if operated within their design specifications, will fit the project requirements perfectly. The science, or I should say ‘art’, is matching the correct pump to the application.
This is where working with a specialist pump system distributor can really pay dividends, saving time and stress in the search for the right product for the job.
Application criteria includes
Discharge head, required flow, liquid temperature, usage – domestic or commercial, the nature of the waste pumped, available footprint, venting, single or duplex pumps and alarms. Some of these criteria will not always be black and white.
Furthermore, not all pumps are ‘equal’; different manufactures claim the same function, but subtle pump design differences result in widely varying overall performance and reliability results.
This makes pump selection for public health engineers a potential minefield.
A good example of this is McDonalds burger restaurants
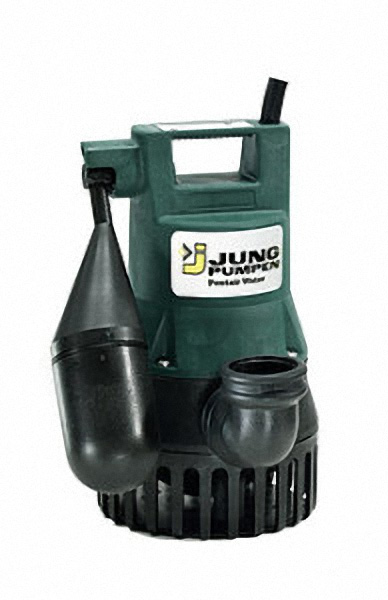
The Jung Pumpen U3K submersible pump is the ideal selection for an application requiring pumping of wastewater from a kitchen sink. However, in some McDonalds restaurants, they have changed this normally reliable pump to a Jung Pumpen U3K Spezial.
The reason is that in some kitchens, staff have taken to washing an excessive quantity of waste coffee granules and milk skin down the sink. This can often now be happening 24 hours a day, seven days a week.
Although the U3K and U3K Spezial are basically the same pump, a subtle design differential within the pump results in a significant increase in reliability for this particular application, making the correct selection extremely critical.
In this case, the design feature that makes the difference is the seal between pump and motor. The U3K uses the normally reliable, three-fold radial shaft seal ring, while the U3K Spezial is fitted with a silicon carbide, mechanical rotating shaft seal, oil chamber and shaft seal ring between it and the motor section.
If this pump was selected from the manufacture’s literature – which states that the pump is suitable for aggressive media such liquids containing salts, brackish water, condensate, silage liquor, liquid fertilizer – the uninitiated might well miss the fact that it can also handle coffee and milk, which is not mentioned.
This brings us back to the benefits that a dedicated pump expert can assist with.
At Pump Technology, we encourage public health engineers to work with our experienced application team who will be happy to provide pump specifications and general pump answers straight away.
Another example
We would also select the U3K Spezial for applications such as: janitor sink, likely to see a concentration of cleaning chemicals; hair dresser, likely to see gels and dyes; pharmaceutical fume cupboards subject to a variety of diluted chemicals.
Cost matters
However, the reason that we don’t select that pump all the time is simply because it is not always required and it comes with a cost implication of around a 20% premium.
Every aspect of a pump’s design and also that of the collecting tank has a specific purpose. Manufactures claim the same performance, but there are different results and I hope that the following design option pointers will provide a useful guide to your pump understanding.
How a floor-mounted system is configured
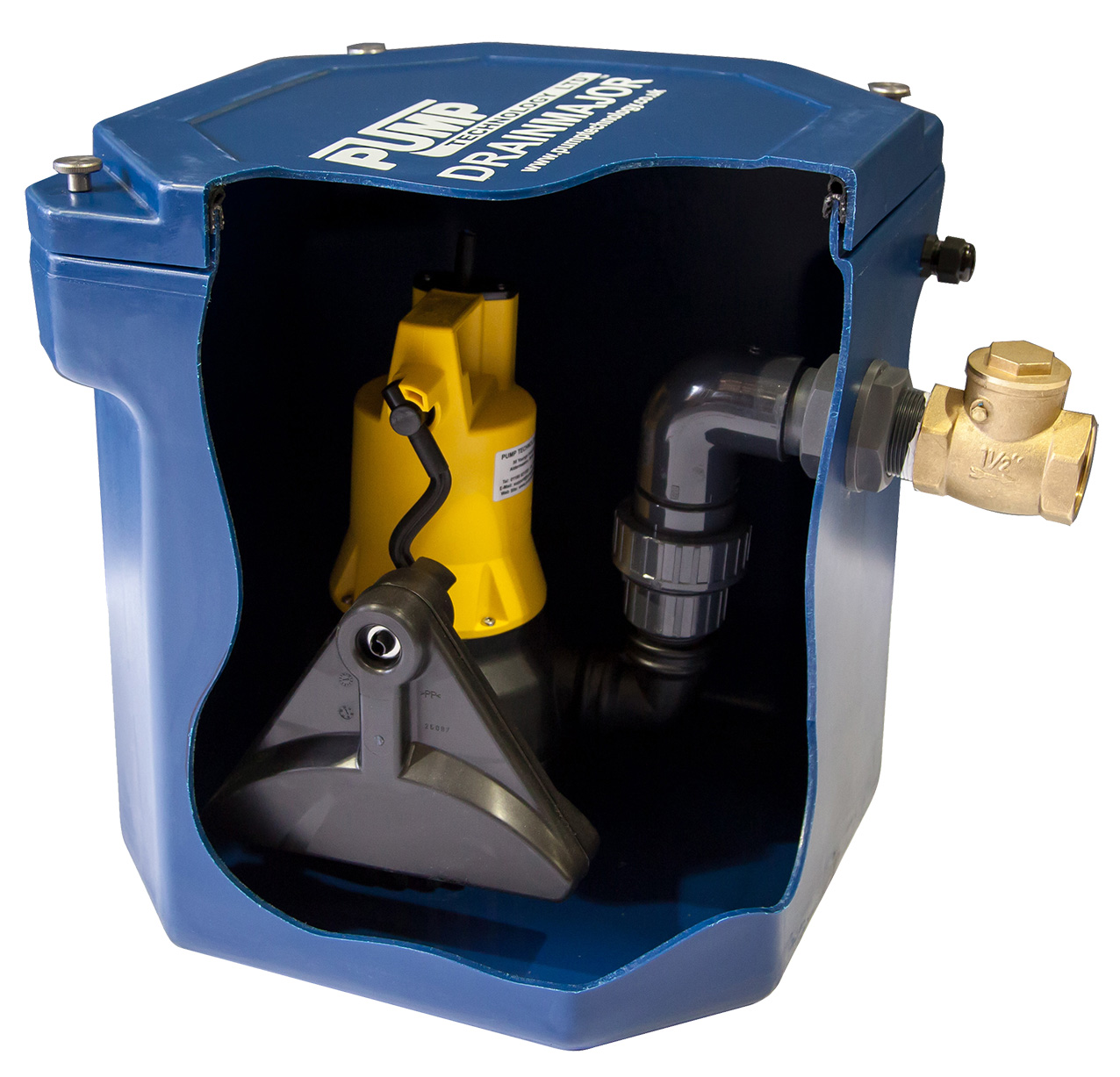
The standard configuration for a floor mounted wastewater pumping system is a submersible pump mounted within a collection tank. The pump’s operation is activated by its own dedicated level float. Two basic float design options are available. A float on a trailing cable or a float on a rigid float arm.
In situ, results can fluctuate. Each application has its own characteristics. Personally, I am a fan of the rigid float arm, it is more tolerant of variations such as turbulent inlet flow or being weighed down by foreign objects. It is also less prone to sticking within an excessively clogged tank contaminated with food debris, fats and grease, for example.
The float operation is important since accurate stop/starting of the pump improves product reliability and life. False float signals can cause multiple start/stop operation leading to burnt out motors, dry running or failure to re-start.
The Jung Pumpen range
The Jung Pumpen submersible pump range not only uses a ridged float arm, but also comes with a bigger and more buoyant low-level float. This not only enhances accurate float movement, but also reduces the volume of residual wastewater left within the collecting tank. This has the advantage of reducing potential odours and possible septicity if the system is left un-operational for a length of time in situations such as schools and office kitchens.
There is always a volume or level of liquid left in the tank, this means that the inlet to the submersible pump is covered/flooded. If this was not the case, the pump would draw air in and air lock making it unable to suck the liquid up into the impeller.
Venting the system
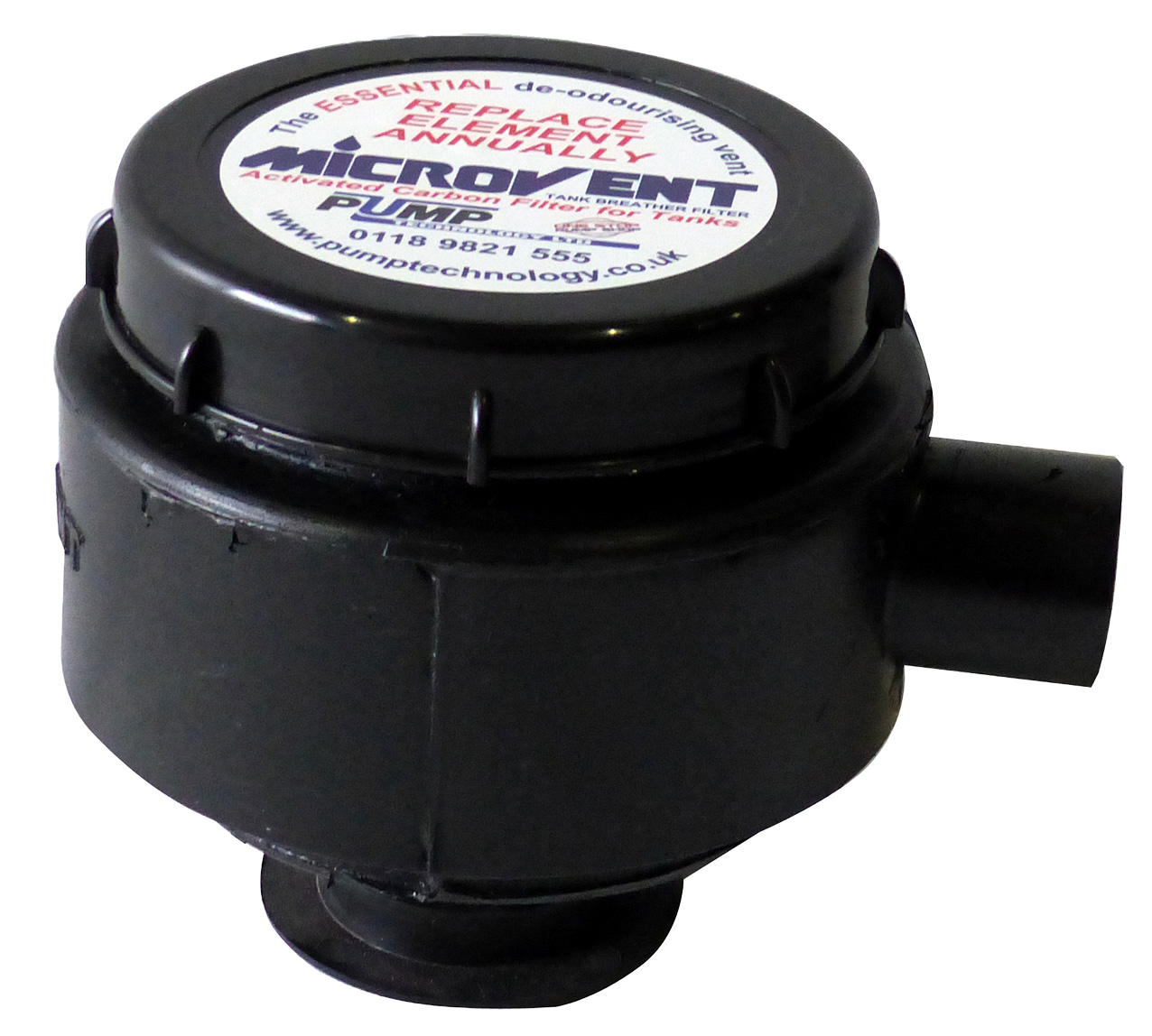
This brings us to venting a pumping system. Venting is essential to the operation of the pump and tank. The vent must allow air in and out. If not, liquid will not drain into the tank or be emptied via the pump. Ideally, all tanks should be vented to the outside of the building. Where this is not possible, a carbon filter can be used. This filter should be of adequate size and positioned as high as possible away from the tank so that it provides the best possible odour reduction and longer effective life. If the filter is mounted too close to the tank, moisture will contaminate the carbon and reduce its effectiveness and life. This can eventually result in a smart city kitchen office or social space smelling of stale waste.
Tank choice
Tanks come in a variety of versions with different sizes and construction materials. Some offer greater onsite pluming flexibility and ease of operator use than others.
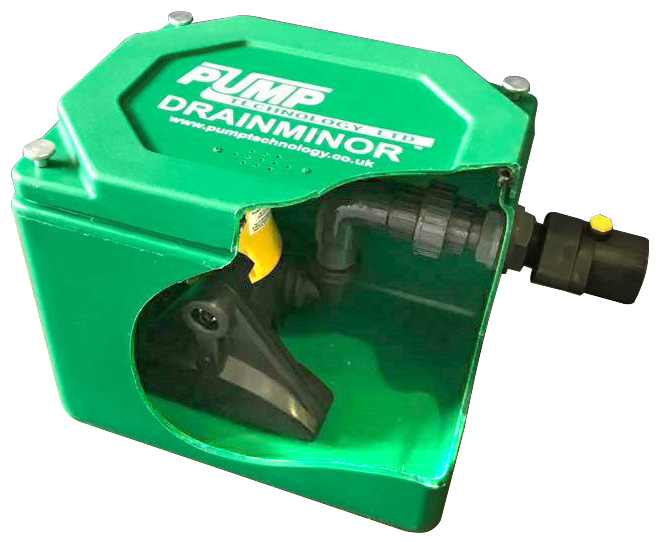
At Pump Technology, our preferred tank material is polyethylene. It is recyclable and, while I would not claim that a pumping system is environmental, it seems only right that, if possible, this factor should be taken into consideration when specifying.
This martial also has the advantageous of rigidity making it easier to cut inlet pipe or discharge pipe positions. Also, in practice, the surface finish over a GRP constructed tank is proving less likely to allow fats and grease to collect over time.
The ideal tank should also allow easy maintenance. This, ideally, means that the lid needs to be removed without the need for tools such as screwdrivers It should also feature an encapsulated lid seal, rather than more traditional flat gasket design, to facilitate regular tank inspection and simple cleaning.
Installation flexibility
Often, tanks are supplied with discharge only or with all sides blank. Some may feature predetermined punch-out inlet positions. The idea here is that the inlet pipe should follow the correct fall from the sink, or dishwasher and be the straightest route possible.
At Pump Technology, we have chosen to supply our tanks with blank sides, giving the installer the kind of flexibility that can be so important in instances such as tight, under-cupboard installations.
Hot wastewater
A further topic we should discuss is hot wastewater, from sources such as zip taps, commercial dishwashers, pasta makers and oven programmed cleaning cycles.
Standard wastewater submersible pumps rely on the liquid in the tank and the pumping flow of that liquid through the pump to maintain a working, operating temperature for the pump and its motor.
This means that the seals and materials of these standard submersible pumps is designed for a common nominal max. wastewater temperature of 40ºC, with occasional use up to 60ºC.
Zip taps left on their hot setting or pumping from commercial appliances will exceed this temperature and therefore a dedicated, designed hot wastewater submersible pump is required.
It’s fair to say that one pump alone has proved through reputation to be the ideal selection for these applications. This is the Jung Pumpen 730HES or the slightly higher pumping duty 1030HES.
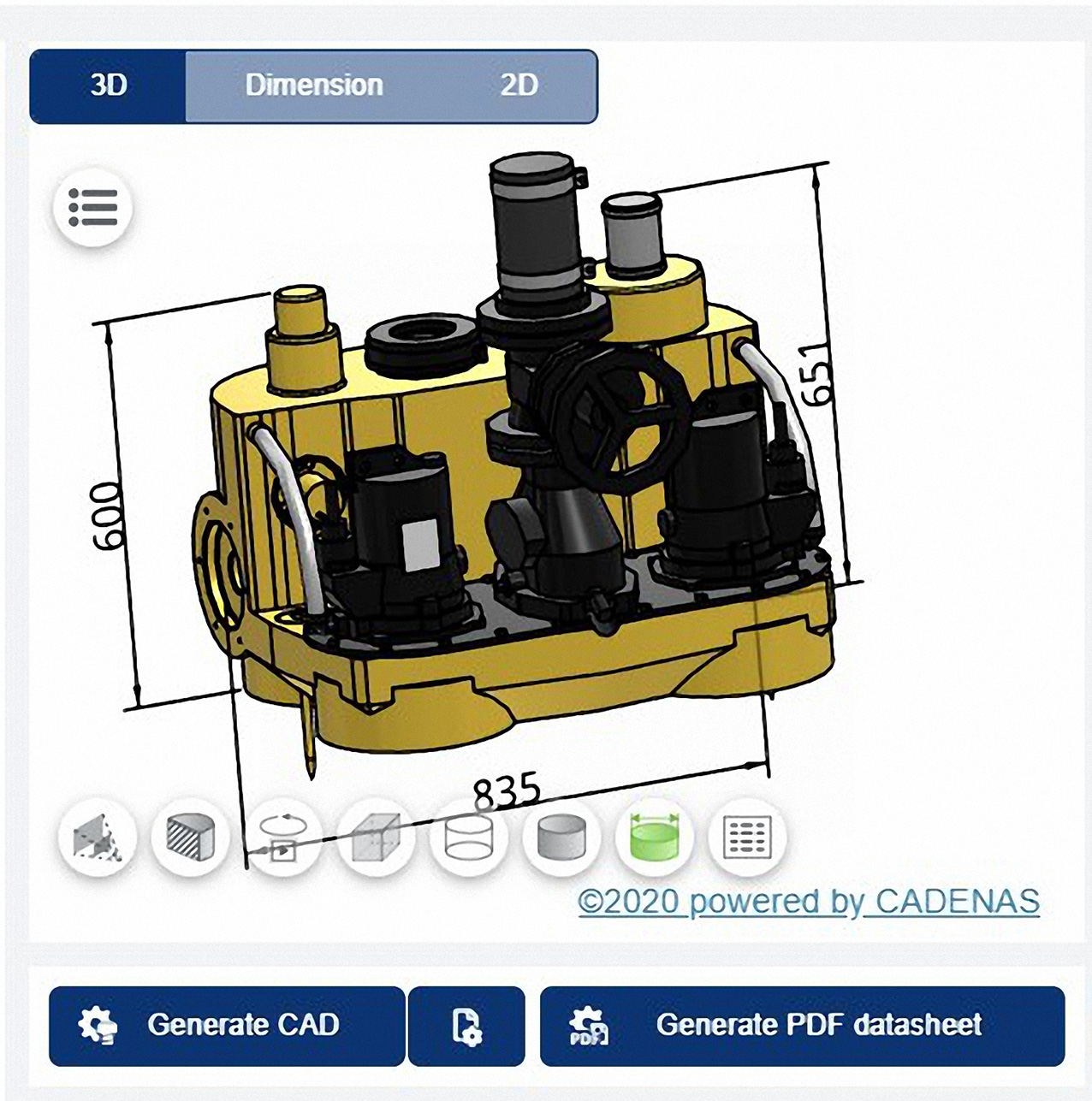
Its robust construction of grey cast Iron volute casing, stainless steel motor casing, insulated power cable for hot water power operation, terminal board lid, impeller, wear plate and strainer base made of glass-fibre reinforced plastic, allow this pump to operate reliably for continuous operation at 90ºC.
At Pump Technology, we don’t expect public health engineers to learn or understand all of the ins and outs of pump selection, and this is why we offer our service.
To ask for a pump selection or confirm your own selections, just contact our pump selection team. You can phone, email or even ask to view a product in our brand new ‘virtual showroom’. Whatever your pumping questions, we are here to assist.
- Coming mid-November 2020, our new 3D BIM library for floor-mounted wastewater and sewage pumping system, incorporating Jung Pumpen GmbH pumps.
- Pump Technology, based in Berkshire, is one of only two Jung Pumpen authorised UK distributors/stockists responsible for the specification, supply and support of Jung Pumpen equipment.