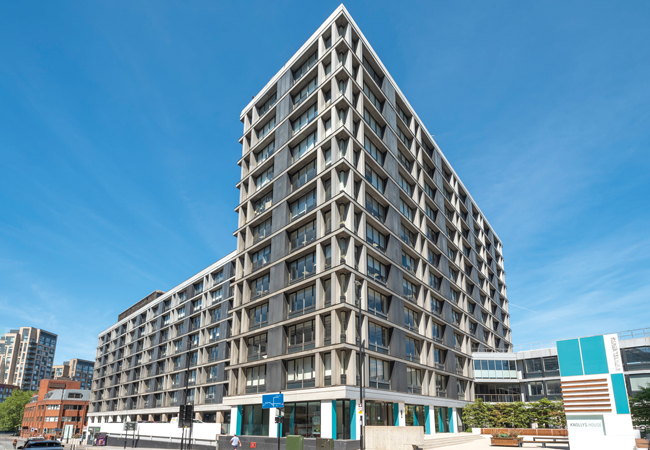
Knollys and Stephenson House
As concern grows over climate change and our ability to meet our environmental, social and governance targets, we often overlook our existing building stock. We tend to assume that improving this stock will be prohibitively expensive and disruptive.
Without attention, there is a risk that these sites will become stranded assets (buildings that the owners will no longer be allowed to sell or rent). Frequently, it is assumed that once a building management system (BMS) has been installed or upgraded, the site will run efficiently. This is usually not the case, however.
Often, these systems are not programmed correctly or are adjusted over time and rarely recalibrated as the building evolves.
As part of the solution to making sure our buildings are fit for purpose five to 10 years down the line, we need to make the building truly smart, using automated continuous control optimisations with regular seasonal recalibration via the BMS. If we do, we can reduce the carbon emissions associated with each building, typically by 20-60%.
This case study covers work done by REsustain with Feldberg Capital on Knollys and Stephenson House, a 17,600m2 (net lettable area) office building in Croydon, built in 1967.
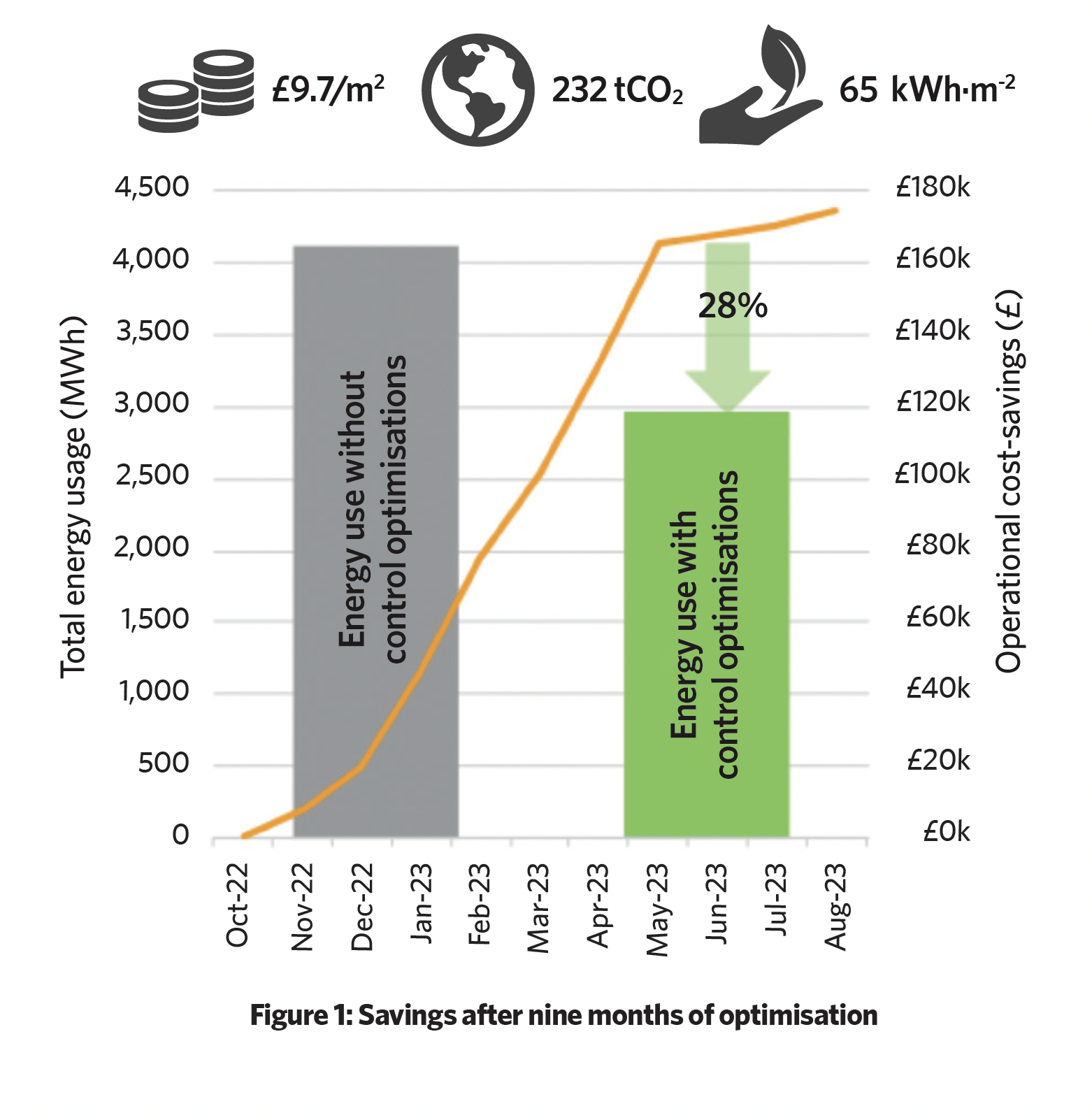
The continuous control optimisations were implemented from 1 October 2022, remotely via a gateway to the BMS. From October 2022 to July 2023, these improvements have provided 28% energy savings, avoided the need to emit 232tCO2 into the atmosphere, and saved £171,000 in operational energy costs over the nine months (see Figure 1).
The building
This multitenanted building is heated and cooled using the original variable air volume reheat system that has been adjusted over the years. The chiller and cooling towers have been decommissioned, and variable refrigerant flow (VRF) systems have been installed in individual offices to cool them in the summer. The building was using approximately 215kWh/m2 (gas and electricity together) each year, which corresponds to emissions of 1,110tCO2 and an operational energy cost of around £26/m2.
A data gateway was deployed in April 2022, and has been streaming to the REsustain platform since then. To make the most of the polled values and to fully understand the building, a full-calibrated dynamic thermal model of the building was created. This includes principal HVAC specifications and control patterns. The building geometry was modelled in DesignBuilder v7 and then transferred to the EnergyPlus v9.4 calculation engine.
The internal gains were based on site visit information, and the annual pattern of occupancy, lighting and plug load in the spaces were taken from standard ASHRAE profiles for an office building. The building was assumed to be occupied for eight hours a day, five days a week, except for one floor that was known to be occupied 24 hours a day. The actual tenant-occupancy numbers were also included in the model.
The HVAC system was modelled as is and was matched to utility bills to ensure alignment between assumptions in the model and real-life operation. These details were taken from documentation obtained from site visits. The energy usage was calibrated to the utility data using the international performance measurement and verification protocol methodology, allowing for a maximum 15% error on the root mean square error, as stated in ASHRAE guideline 14-2014 (see Figure 2).
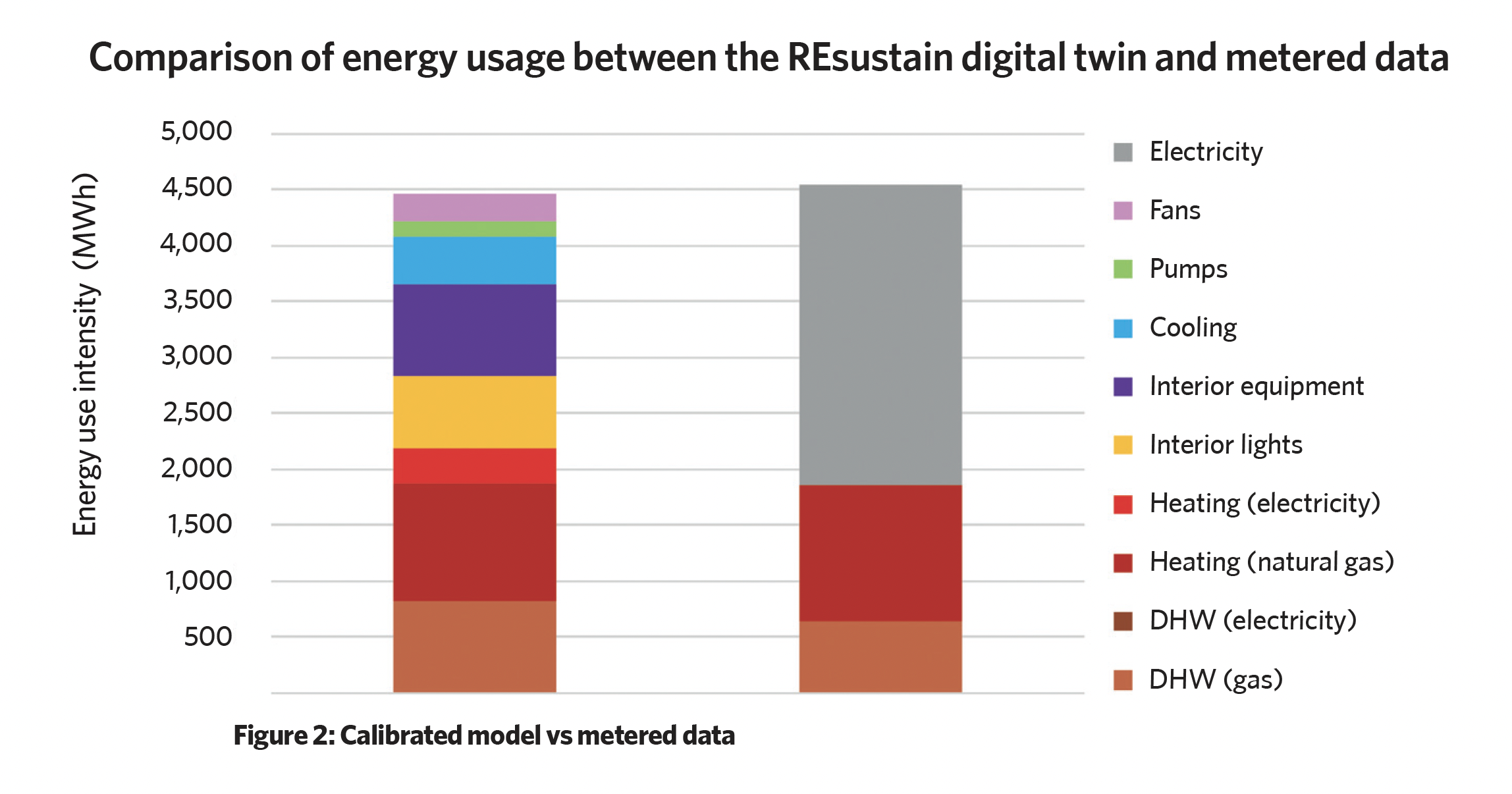
The rules engine then ran through all of the data and identified the following groups to be controlled throughout the year.
- Ventilation load to be reduced at certain times.
- Fans to have a stricter schedule to reflect operational times of the building.
- Eliminate simultaneous heating and cooling.
- Ensure the boiler plant is operating only when necessary.
The optimisations were implemented in the energy model to forecast the potential energy, carbon and cost savings. It was estimated that the building could potentially save 26% energy usage, £140,000 of annual operational cost, and reduce carbon emissions from 1,110tCO2 to 900tCO2 per year – a 210tCO2 reduction (see Figure 3).
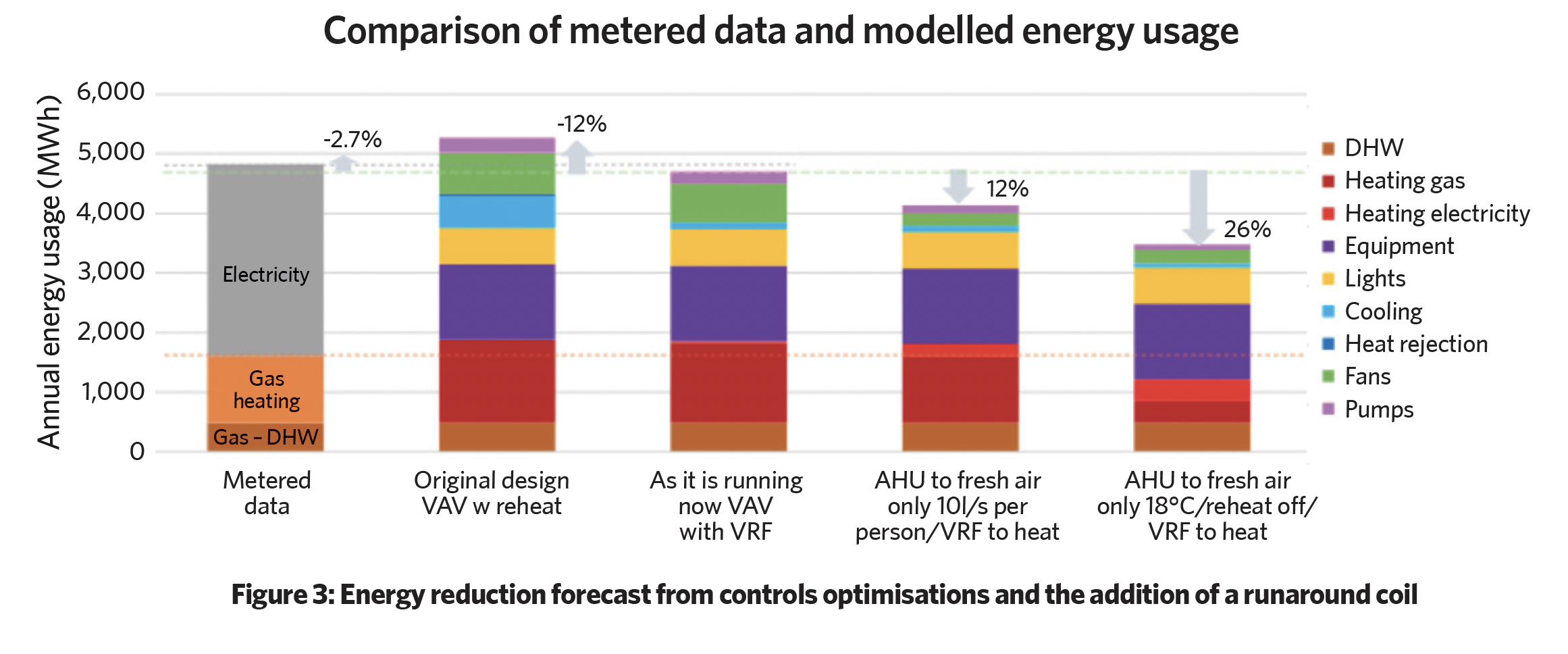
Implementation of controls optimisation
In October 2022, the implementation of the controls’ optimisation began. Because of a milder autumn, the VRFs in the office spaces were able to maintain comfortable temperatures, so the boilers remained turned off for the months of October and November. This meant that only the ventilation control strategy and fan control strategy were implemented in those months.
This was not straightforward. When trying to implement the strategy it was not possible to move the outdoor air dampers via the BMS because, as a result of their age, they were now stuck. Instead of moving the dampers, the control strategy was applied to the fan. The flowrate was reduced to 30%. It was thought that to reduce the fan to a lower flowrate could cause it to fail, so this was deemed to be the low limit.
The central boilers were turned back on in December 2022. At this point, the simultaneous heating and cooling elimination strategy was implemented. There were reheat coils in the four ducts leading from each air handling unit. The initial plan was to close these. However, it was found that the reheat coil valves had corroded, stuck at their 100% open position, so an alternative was found.
In this case, a decision was made to turn the hot water temperature setpoint down from 70oC to 60oC, with a weekly pasteurisation cycle. It was hoped that the hot water temperature could later be dropped further to 50oC. It was also suggested to the facilities manager that variable speed drives be put on the low temperature hot water pumps to allow the circuit to be more controllable. These were not added; instead, the pumps were controlled on a daily/weekly basis to reduce heating energy consumption.
To understand how much energy is being saved as a result of these optimisations, the calibrated energy model is updated monthly using BMS data, weather data, any changes relating to tenancy or retrofit, and the utility bills. Once this calibration has been verified, the control optimisations in the model are removed and the model is rerun for the previous month, then compared with reality to measure what effect the changes have had.
The optimisation of the services at Knollys and Stephenson House proves that – by making buildings smarter and constantly analysing control patterns – it is possible to make existing building stock considerably more efficient without any significant capital expenditure or the need to add any further embodied carbon into the building.
About the author
Annie Marston is chief product officer at REsustain
This article is based on a paper presented at the CIBSE Technical Symposium 2023 titled A comparison of forecast energy reduction through control optimisation in an existing building with actual data from the optimised building
The 2024 CIBSE Technical Symposium will be held on 11-12 April 2024, at Cardiff University, Welsh School of Architecture. www.cibse.org/symposium